Warehouse
Modern warehouse automation began with the integration of conveyor belt systems. In the time since those innovations, conveyors have played a major role in facilitating the efficient, accurate automation of warehouse operations across applications and industries International regulations for a safe work environment. We can build them according to special requirements or with several options such as a Hydraulic cushion / ejector Broadly speaking, warehouse automation refers to the use of robots and other technologies to enhance production, improve efficiency, streamline operations, cut costs, and provide additional benefits to a warehouse environment. In general, automation in warehousing focuses on increasing productivity in the most cost-effective and efficient ways possible with the right systems. The rapid adoption of automation in warehouses is largely due to a number of persistent trends in the industry. When we consider the future of warehousing, some of the forces driving automation trends include:
Increasing demand for fulfillment and expedient distribution
Ongoing labor shortages
Growth-limiting supply chain issues
Investing in automation solutions can help warehouses effectively address these challenges in a scalable way.
Warehouse Technology
Adopting automated warehouse technology can look very different depending on the facility, its needs, and its restrictions. Warehouses may consider integrating solutions such as:
Automated conveyor systems
Collaborative robots
Internet of Things (IoT)
Inventory management systems
Fleet management systems
Predictive and proactive maintenance systems
Combining process and physical automation solutions often provides the best results, though available space, budget, and technicians may limit potential integrations.
On the other hand, physical automation primarily refers to the integration of robots and other robotics in warehousing operations. Physical automation may include the use of technologies such as:
Goods-to-Person (GTP) fulfillment systems
Automatic Guided Vehicles (AGVs)
Autonomous Mobile Robots (AMRs)
Automated sortation systems
Automated storage and retrieval systems
Pick-to-light systems
All of these automation integrations are used to improve efficiency, worker safety, and overall productivity in warehouses.
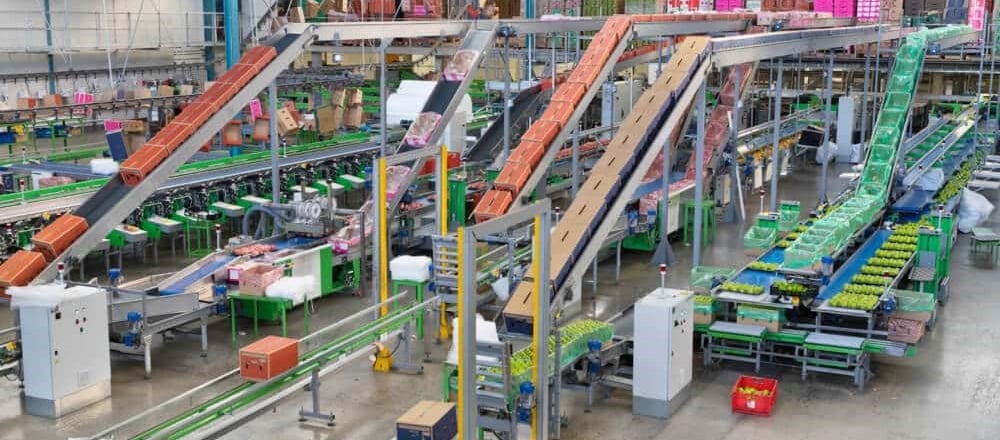
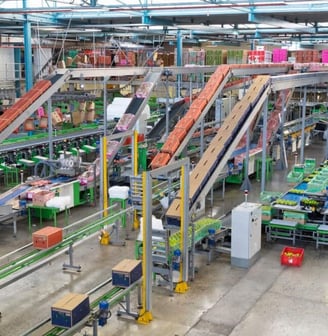
Warehouse Conveyor Automation
Flexible chain Conveyor
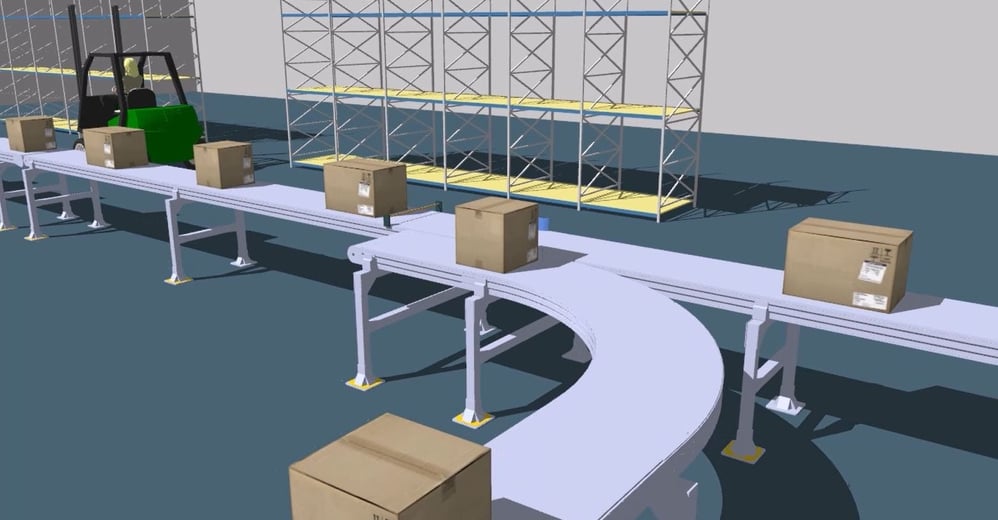
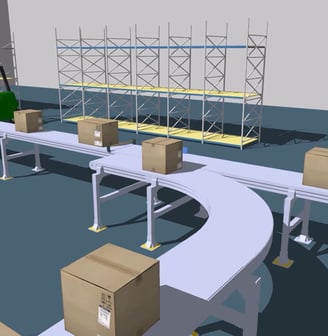
Tailored to Your Needs
We specialize in engineering custom conveying systems for our clients, tailoring the systems to the limitations of your space as well as your specific applications. Our approach is the same regardless of whether you’re in need of a single conveyor for packaging medical devices or a complete system for manufacturing, assembling, packaging, and labeling.
We’ll provide recommendations for products that suit your space and specialized needs so that you can maximize your productivity as seamlessly as possible. Flexible conveyors are a customizable solution designed for tight spaces while still offering the flexibility to grow along with your needs. This series of material handling and industrial equipment can handle twists, multiple curves, inclines and declines on a single conveyor. conveyors can also move products as small as 3 inches in diameter.The Flexible line is our most versatile and innovative series, suited for a range of applications from assembly and accumulation to transfers and packaging. Easy to configure (and reconfigure), Flexible conveyors are ideal for the manufacturing of medical devices, making it easy for you to adjust and adapt your process as demand changes.
The Flexible Series are especially useful for additional applications, including:
Part handling
Tight spaces
Assembly automation
Machine conveyance
Elevation changes
Buffering
Complex configurations
Long lengths
Curves, jogs, inclines, and declines
Pallet Conveyor
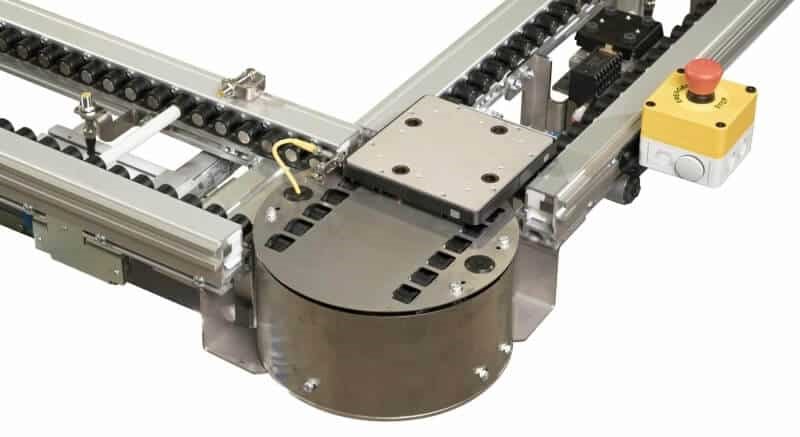
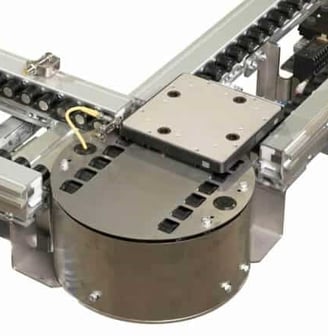
Pallet conveyors handle and transport large, heavy or unwieldy loads. Often positioned low to the ground for better control, products are moved by belt, slats, rollers or chain. Like traditional conveyors, powered or unpowered pallet conveyor solutions offer seamless integration with ancillary pallet handling equipment like robotic palletizers and depalletizers, turn tables, stretch wrappers, transfers, unit load ASRS, pallet dispensers and more.
Pallet accumulation conveyors help to prevent product damage, prolonging equipment lifespan.
Features & Benefits
Improve warehouse flow and decrease traffic
Minimize labor load handling
Gentle handling – reduce product damage / precision and positioning
Improve system throughput, safety and ergonomics
Free up fork truck equipment for other tasks
Pallet Conveyor Technologies
Various pallet conveyor technologies, configurations and customizations are available to meet your specific needs and processes. As an independent integrator, our brand-agnostic approach, allows our engineers to leverage the best available technologies for your project
Accumulation Pallet Conveyors
There are several different designs of pallet accumulation conveyor. However, all designs allow for zero pressure accumulation of products. Pallet accumulation technology includes photo eye controlled networked AC and DC motor controlled zoned accumulation.
Gravity Pallet Conveyors
Non-powered pallet conveyor solutions, gravity roller pallet conveyors move pallets manually along a track featuring a series of rollers laid in succession within the conveyor frame. The rollers help keep the pallet in motion by reducing friction between the rollers and the pallet itself.
Pallet Transfers & Turntables
Pop-up chain and roller transfers are used to divert heavy unit loads at right angles by lifting and gently transferring them. The transfer remains inactive when product needs to pass through a junction. Powered turntables with chain-driven rollers ensure that loads can be reoriented when material flow lines intersect or change direction.
High-Speed Pallet Transfer Cars
Transfer cars handle distribution, supply, and order picking functions at conveyor line heads or between conveyor lines and palletizing stations. Transfer cars are frequently used to distribute empty pallets in a large, multi-line palletizing system, as well as combine the full pallet discharges of the palletizing system into a common stretch wrapper.
Robotic Conveyor
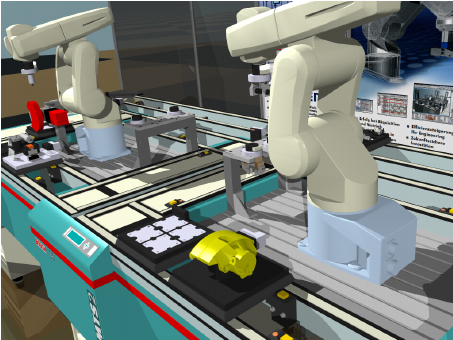
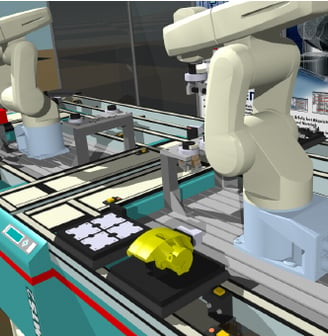
Robotic and conveyor manufacturers are making it easier than ever to integrate their systems. This is bringing a higher level of automation and efficiency to much of the packaging industry. If you’re applications makes sense for robotics, it may be the path toward advancing your company past the competition. Conveyor Systems for Robotic Automation· The integration between robotics and conveyors in recent years has brought a much higher level of automation to a variety of packaging applications. The two components work hand-in-hand to deliver a more streamlined, efficient operation with more accuracy and a strong return-on-investment.
we feel this collaborative effort is only going to get stronger within packaging as robotics become easier to program and more cost-effective to operate. Take a look in any modern-day processing or packaging facility, and you’ll see automation is the prime driver behind the way products are being produced. There’s no better time to embrace the integration of robotics and conveyors· Just as technology in robotics continues to evolve, conveyors are keeping pace as well. Robotic applications often require product to be in an exact location, in the exact position, and at the exact time on the conveyor. But to do that successfully requires a conveyor system that’s efficient, reliable and engineered to work in conjunction with robotics. Not every conveyor can do that.Servo-driven precision-move conveyors deliver accurate alignment of time and distance that provide indexing repeatability of +/- .040”, all at a rate of 100 indexes per minute.
Additionally, pallet system conveyors have become a popular choice for many automation-focused applications that require exact movements and positioning of parts, as they can be setup or programmed to start and stop at specific intervals to sync up with robotic interaction or other processes.
These types of conveyors dominate in automotive component manufacturing, as well as other industries including packaging, medical devices, electrical and electronics, and product testing/inspection that call for automated and manual assembly or handling of products.
Pallet system conveyors are available in multiple styles such as dual belt configurations powered by common drives, and flexible plastic chain belt designs. These conveyors come with lifting modules and can be used to interface with robots, change product orientation, or rotate product 90° or 180°.
Conveyor systems for robotic automation systems include all types of conveyors that are used to move/transfer raw materials, work in process and finished goods products in/out of work cells. Typical types of conveyors include roller conveyors and belt type conveyors that are often controlled by a master PLC, or the robot. Conveyors are used to control part flow in a manufacturing operation. More specialized conveyor components include pallet transfers and turntables. For example, robot palletizing cells require a conveyor of some sort to move products into a palletizing station and then out of the cell for fork truck pickup.
Decrease Manufacturing Downtime
An automated assembly system needs no downtime, besides some routine maintenance.
Minimize Errors
A robotic assembly cell removes the potential of “human error."
High Speed & Performance
Robotic assembly cells only perform precise movements and need no breaks for food and rest.
Adhesive Dispensing
Automated Assembly Systems
Case Packing
Collaborative Robots
Conveyor Systems
Injection Molding
Inspection & Vision Systems
Machine Tending
Material Handling
Palletizing & Depalletizing
Picking & Packaging
Pre-Engineered Welding Cell
Robotic Welding Systems