Vertical machining centers (VMC) and horizontal machining centers (HMC) are essential in modern manufacturing, offering advanced solutions for intricate precision machining tasks across various industries, including aerospace, automotive, and medical technology. These cutting-edge CNC machines are designed for superior speed, accuracy, and efficiency, With the capability to handle complex components, our 5-axis CNC machine solutions streamline operations and minimize the need for frequent tool changes, enhancing productivity and reducing downtime. , VMC and HMC machines enable manufacturers to achieve exceptional results while maintaining high-quality standards. As technology continues to evolve, these machining solutions remain at the forefront, transforming the landscape of advanced manufacturing

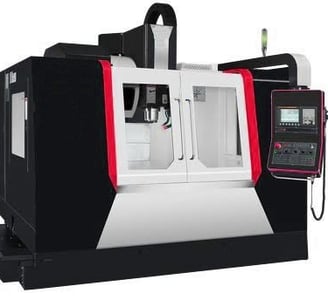
Machining Centers
Plastic machines
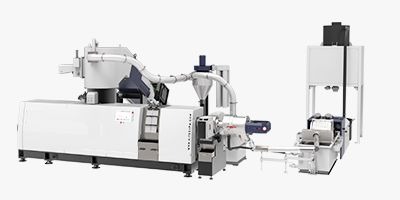
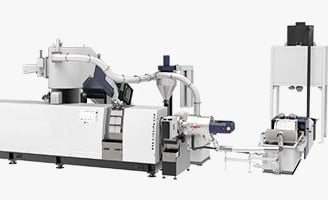
The all-electric medium injection molding machine features advanced injection and plasticizing technology powered by a state-of-the-art servo motor, ensuring precise reproducibility and efficiency in production. Designed with a minimalist elegance in mind, this compact machine is ideal for small-scale operations without compromising on quality. Additionally, the production line for PET sheets includes a twin screw extrusion system, eliminating the need for drying, which optimizes the manufacturing process. The multi-layer co-extruded sheet production line for PP and PS materials allows for versatile applications and enhances product performance. For those seeking specialized solutions, the PPR pipe extrusion machine is expertly crafted to produce polypropylene random copolymer pipes, while the nylon extrusion machine caters to specific industry needs, demonstrating a commitment to innovation in the plastic manufacturing sector
Industrial Manufacturing
In the realm of modern manufacturing, vertical machining centers (VMC) and horizontal machining centers (HMC) play a pivotal role in enhancing productivity and precision. These advanced machines are complemented by innovative technologies such as laser welding and sheet metal roll forming, designed specifically for the efficient production of customized metal frames. Furthermore, all-electric medium injection molding machines utilize cutting-edge servo motors to deliver exceptional precision in injection and plasticizing processes, ensuring consistent quality. The integration of laser cutting with various printing technologies, including inkjet, hybrid digital, flexographic, and rotogravure printing, elevates manufacturing capabilities. Additionally, rotogravure presses and selective laser sintering (SLS) with 3D metal printers push the boundaries of production techniques, allowing for intricate designs and superior efficiency in fabricating metal components.
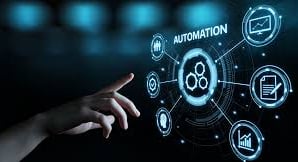
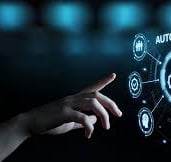
. Meanwhile, the sheet metal roll forming machine is expertly designed for the efficient production of customized metal frames, providing precise measurements and a user-friendly operating experience. Engineered to be both durable and affordable, it incorporates PLC control equipment, ensuring that the output quality of sheet metal parts meets high standards. Additionally, the sheet metal automatic production line streamlines specific tasks, enhancing productivity in metalworking operations. Together, these machines represent the future of industrial cleaning and metal formation, combining innovation with practicality for optimal results.The fiber laser cleaning machine stands out as a revolutionary solution for effectively removing surface contaminants such as rust, grease, paint, and other persistent deposits.
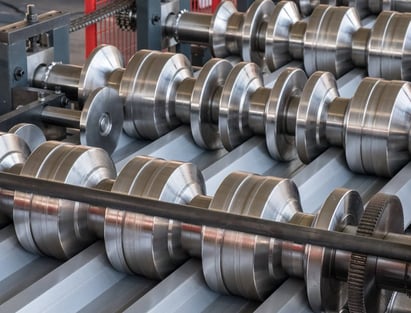
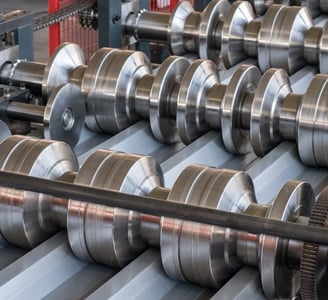
Metal Machinery
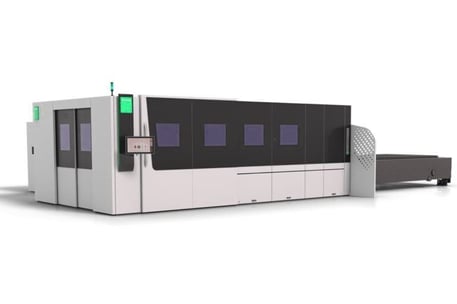

The fiber laser welding machine ingeniously merges the convenience of a mini welding device with the robust functionalities of a full-sized model. This advanced equipment delivers precision while maintaining strength and quality, making it an ideal choice for various industrial applications. Equipped with a pulsed laser, it boasts fast welding speeds, high efficiency, and a minimal heat-affected zone, ensuring strong welding joints even at high melting temperatures. Additionally, the fiber laser cutting system offers excellent value for its price, making it a popular choice among industry professionals. . This combination of power and portability makes it a reliable tool for any modern fabrication process.
Laser Machines
Our PVD and DLC/PECVD equipment offers a comprehensive solution for various coating technologies within a single machine, specifically designed for industrial applications. This advanced system effectively enhances the durability and performance of cutting and forming tools, precision-engineered components, automotive and aerospace parts, medical devices, and other critical components. By utilizing a magnetron sputtering system, it ensures rapid deposition of functional coatings that significantly boost wear and heat resistance while reducing friction, thereby extending the lifespan of both industrial and consumer products. The equipment achieves dense, smooth coatings comparable to those produced with HIPIMS technology, but does so at an accelerated deposition rate.
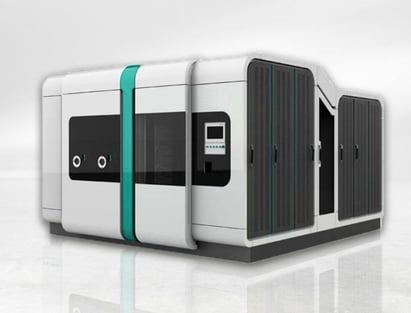
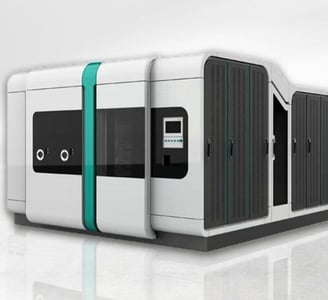
PVD Coating
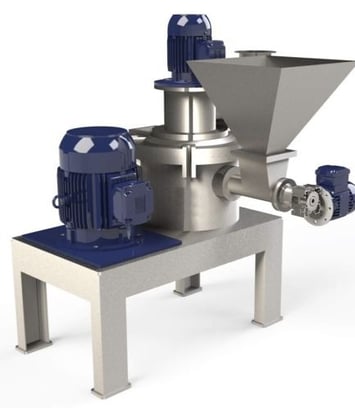
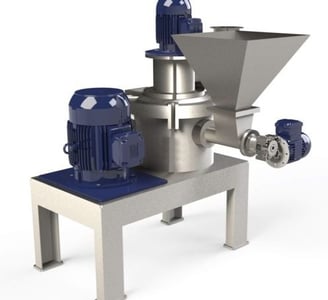
Powder processing and particle size reduction are essential processes in numerous industries, transforming raw materials into finely powdered forms with defined attributes like particle size, shape, and surface characteristics. These attributes significantly impact the performance and quality of final products. The process begins with feeding the raw material into specialized processing equipment, where it undergoes comminution. During this stage, various techniques such as milling, grinding, and micronization are employed to achieve the desired particle size. Once the raw material is sufficiently reduced, classification follows, where the powder is sorted into different size fractions through methods like sieving and air classification.
Powder Processing
Our modern silos are transforming traditional storage methods by utilizing premium materials and state-of-the-art technologies. Equipped with features such as temperature detection systems, aeration capabilities, and sweep augers, these silos ensure optimal storage conditions for various grains. The innovative combo milling system operates by vacuuming grain into the initial milling body, which then transfers it to a second milling body for the production of fine flour. Additionally, the inclusion of fan blades enhances the vacuuming process, allowing for a seamless and efficient milling operation. Designed with precision, the pneumatic roller mill and its extensive array of milling machinery provide superior performance, catering to the high demands of today's milling industry. Through this advanced approach, we set new standards in storage and milling, making them more effective and reliable than ever before.
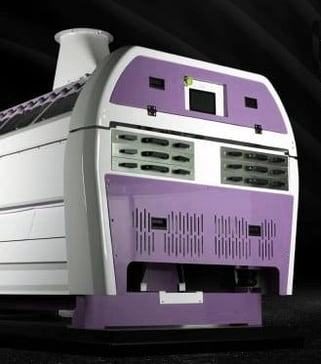
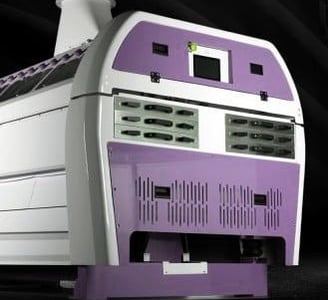
Food &Grain Processing
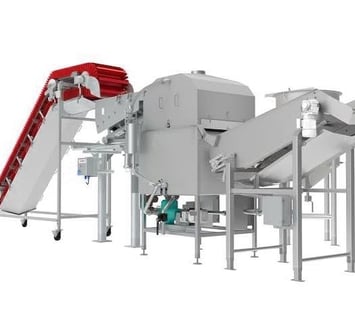
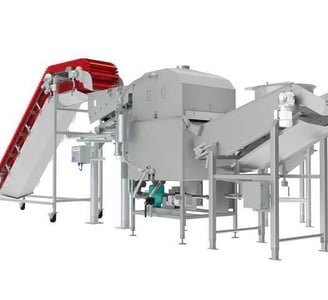
At our animal feed mill, we prioritize conversion rates by implementing cutting-edge technology in our feed processing installations. As a leading brand in the feed machinery industry, we specialize in aqua feed production, where achieving the perfect formulation for both food and ornamental fish is essential. A crucial aspect of this process is using a gentle processing method, particularly through extrusion, which cooks and shapes the feed while maintaining its nutritional integrity. This extrusion process not only affects the final product's texture and digestibility but also enhances its overall quality. Additionally, both the pretreatment and post-treatment steps are vital in optimizing the feed, ensuring that our offerings meet the highest standards for fish nutrition. Our commitment to innovation and quality continues to drive us forward in the competitive feed market
Animal Feed Processing
Industrial dryers play a crucial role in a variety of applications, particularly in the food processing sector. Our freeze dryers are specifically designed for this industry, ensuring optimal preservation of food products. Additionally, we offer tunnel IQF industrial ovens, which create high temperatures for heat treating parts, conditioning metals, and curing metal coatings. To cater to diverse requirements, our range of industrial microwave drying equipment is expertly crafted to meet your unique drying needs. With extensive experience in drying materials such as food products, pharmaceuticals, and chemicals, we leverage advanced technology to achieve precision and efficiency in the drying process. This not only enhances the quality of the end products but also contributes to significant savings in time and energy.
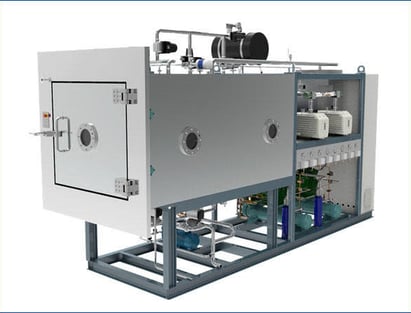
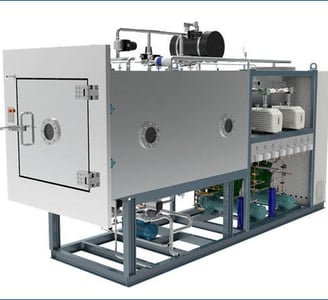
Oven Dryer
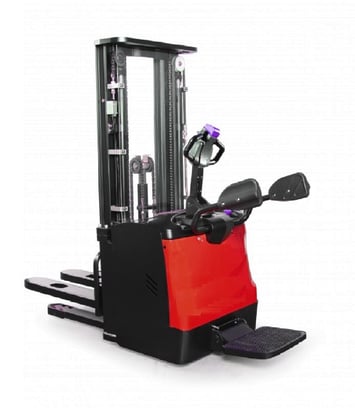
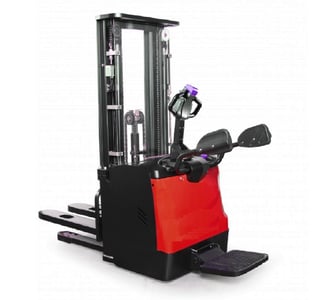
At our company, we provide an extensive range of material handling equipment tailored to suit your specific requirements. Whether you're looking for compact solutions or larger, heavy-duty autonomous robots, we have the ideal option for your application. Our offerings cover various processes, including pick and place, dispensing, palletizing, packaging, part transfer, machine tending, and assembly. We are a leading system integrator, capable of delivering solutions at any scale, from user-friendly standalone systems to fully integrated solutions that automate the entire material handling workflow. By incorporating our robotic handling solutions, you can maximize productivity, enhance throughput, and streamline operations, ensuring efficiency from the beginning to the end of your production line.
Material Handling
At the forefront of polyurethane processing, we position ourselves as the market leader in both continuous and batch PU flexible foam machinery. Our latest generation of slab stock lines adeptly transforms PU raw materials into high-quality molded foam components specifically designed for vehicles. Each year, our advanced molded foam systems technology facilitates the production of parts that cater to various applications, including seats and headrests. Furthermore, our continuous PU sandwich panel production line represents a cutting-edge solution for high-efficiency manufacturing, meeting the increasing demands of the industry. In addition, our innovations in polyurethane (PU) for fiber-reinforced composite production lines offer a revolutionary approach to producing lightweight composites that not only excel in resilience but also meet stringent performance standards. This comprehensive approach underscores our commitment to delivering advanced solutions and maintaining our leadership in the market.
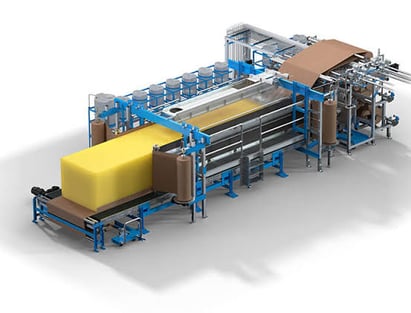
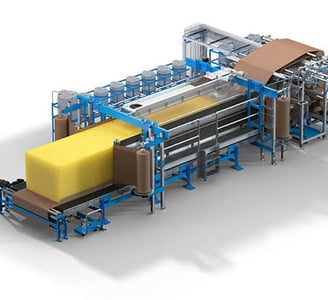
PU Foam Production line
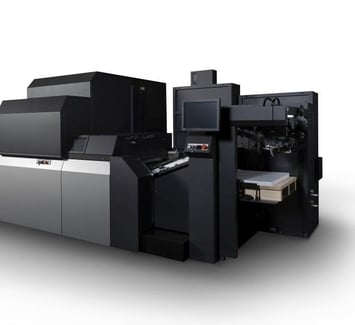
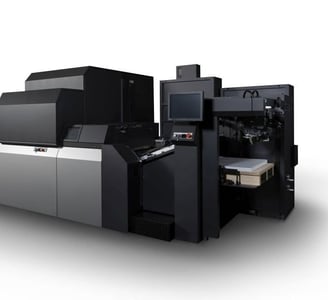
We integrates various printing technologies, from inkjet to hybrid digital, flexographic, and rotogravure printing. The rotogravure presses enhance production capabilities by employing Selective Laser Sintering SLS 3D Metal Printer ,SLA Polymer 3D Printer , DMLS 3D Metal Printer are sophisticated technique where a powerful laser fuses powdered materials layer by layer. This method enables large build sizes and compatibility with robust materials, making it ideal for developing functional prototypes and intricate end-use components. The durability and heat and chemical resistance of SLS further bolster its relevance in the production landscape, showcasing the growing trend of in-house SLA 3D printing driven by industrial demands..
Industrial Printers
We offer a range of industrial compressor When purchasing an industrial air compressor, several crucial parameters should be taken into account to ensure optimal performance. First and foremost, consider the horsepower and kilowatt (kW) ratings of the compressor, as these dictate its power output and suitability for industrial tasks. Among the various types, scroll, reciprocating, and rotary screw compressors are popular due to their reliability and efficiency. Their sleek designs enhance safety and ease of handling, making them convenient for users. Additionally, these compressors are known for delivering superior performance, making them powerful enough for both commercial and industrial applications. Energy efficiency is another significant factor, as these units consume less power while maintaining efficacy. Furthermore, their maintenance is straightforward and cost-effective, which is an essential consideration for any business looking to minimize operational costs while maximizing productivity
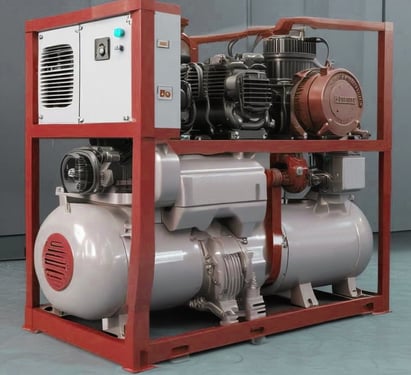
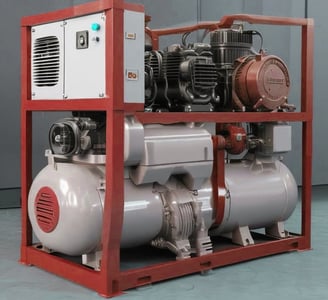
Air Compressor
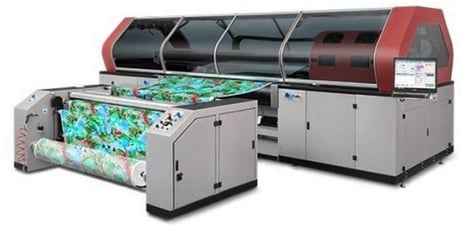
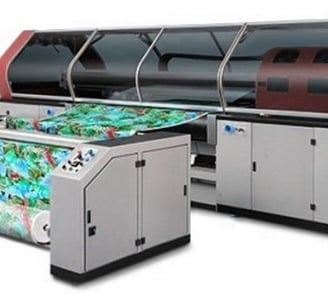
We integrates various printing technologies, from inkjet to hybrid digital, flexographic, and rotogravure printing. The rotogravure presses enhance production capabilities by employing Selective Laser Sintering SLS 3D Metal Printer ,SLA Polymer 3D Printer , DMLS 3D Metal Printer are sophisticated technique where a powerful laser fuses powdered materials layer by layer. This method enables large build sizes and compatibility with robust materials, making it ideal for developing functional prototypes and intricate end-use components. The durability and heat and chemical resistance of SLS further bolster its relevance in the production landscape, showcasing the growing trend of in-house SLA 3D printing driven by industrial demands..