Batching Plant
REVOLUTIONARY WAY OF MAKING CONCRETE
The Batching Plant represents a revolutionary approach to concrete production, efficiently reducing waste through an innovative design. By storing raw materials in separate compartments, it allows for precise mixing according to a predetermined recipe, ensuring that only the necessary quantities are used. This method enables the production of various certified concrete qualities from the same load, enhancing versatility. Furthermore, production occurs directly on-site, overseen by an intuitive onboard computer that manages the weighing of cement, aggregates, and the dosage of additives and water. This streamlined process not only guarantees superior product quality but also minimizes time and costs. With its mobile, user-friendly design, the Blend plant can be efficiently operated by a single individual, making it an ideal solution for modern construction needs.
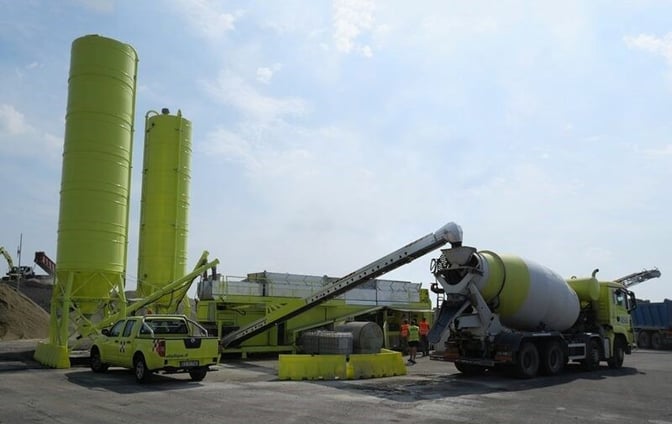
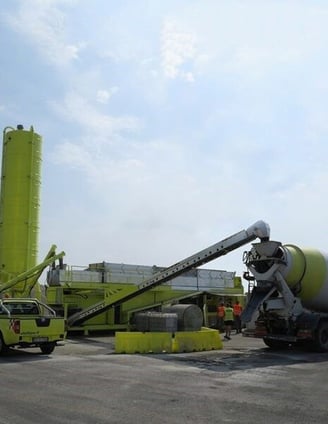
Onsite Mobile Batching Plant
CHOOSE THE MODEL MOST SUITABLE FOR YOUR NEEDS
Mobile Batching plant is the new way of thinking concrete and reducing waste. Its internal structure stocks raw materials in separate compartments, mixing, on the basis of the set recipe, only what is necessary. In this way it is possible to obtain, with the same load, different qualities of certifiable concrete. Production takes place directly on site, and is controlled by an intuitive on-board computer; the weighing of the cement, aggregates, the dosage of additives and water guarantee the quality of the product, reducing time and costs. A mobile, simple and versatile plant managed by a single operator. Blend mobile plants are available in a variety of sizes and with a wide range of optionals, to meet different production needs. Blend is a multifunctional plant that allows not only the production of concrete, but also of cementitious mixtures, sand, mortar, cold asphalt and concrete from recycled materials
Separate transport of the components:
AGGREGATES
CEMENT
WATER
ADMIXTURES
EMULSION
Our plants are independent from traditional Batching Plants.
• Mixing directly on-site.
• Raw materials are loaded into different hoppers. Materials are dosed into the single shaft ribbon mixer according to recipe and automatically controlled by the on-board computer. There is no need to wait for concrete deliveries or pay additional costs for leftover material.
• From 1 to 3 aggregates hoppers for different materials and sizes based on the model
• Automated production.
• Aggregates / cement weighing and consumption reading
On-board computer for fully automated production with simple and intuitive software.
– The electronic control unit with military grade protection on Blend plants keeps the production and concrete flow under constant control by its sensors. Different types and qualities of recipes can be stored and selected. No manual operations are necessary.
– Weighing of aggregates/cements and reading of consumptions in Kg.
– Integrated printer with paper printout and digital report of different production lots. Humidity probe for automatic water adjustment in the recipe.
• Blend mobile plants are compact, easy to lift and load.
• All MCM-series plants fit perfectly into a container.
• Easy to transport, ready to produce on site.
ON-SITE MIXING, REDUCED TRANSPORTDOSAGE OF MATERIALS, ZERO WASTE
MOBILITY AND FLEXIBILITY
NOISE REDUCTION
EURO 6 DIESEL (BIFUEL), METHANE OR ELECTRIC
LOW WATER CONSUMPTION WASHING
ECOLOGICAL AND RECYCLABLE MACHINE COMPONENTS
MIXING OF RECYCLED MATERIALS
INDUSTRY 4.0 AND OTHER INCENTIVES
THE PLANTS THAT REDUCE CONSUMPTION
EFFICIENCY AND QUALITY WITHOUT COMPROMISE
REDUCTION OF EMISSIONS AND CONSUMPTIONS
REAL MOBILITY, MORE FLEXIBILITY
.
MCM15 MCM25 MCM50 MCM50
Aggregates 3.5 m3 5 m3 10 m3 12 m3
Cement 1.1 m3 2.3 m3 3.2 m3 3.2 m3
Water 550 lt .500 /3.000 lt (opt.) 2.000/4.000 (opt.) 2.000/4.000 (opt.)
Emulsion 300 lt (opt.) 300 lt (opt.) 600 lt (opt.) 600 lt (opt.)
Admixtures 3×42 lt (opt.) 3×42 lt (opt.) 3×42 lt (opt.) 3×42 lt (opt.)
Output ≤35 m3/h ≤50 m3/h ≤50 m3/h ≤50 m3/h
Power* 27 Kw PTO 44 Kw PTO 44 Kw PTO 44 Kw PTO
Empty weight 1.690 Kg 1.370 Kg 2.870 Kg 2.550 Kg 3.650 Kg 3.250 Kg 3.750 Kg 3.370 Kg
Dimensions 3.570 x 2.000 x 1.450 mm 4.317 x 2.250 x 1.994 mm 5.650 x 2.250 x 2.276 mm 6.150 x 2.250 x 2.276 mm
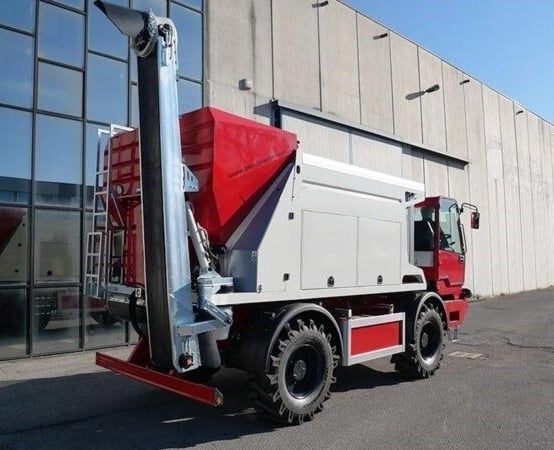
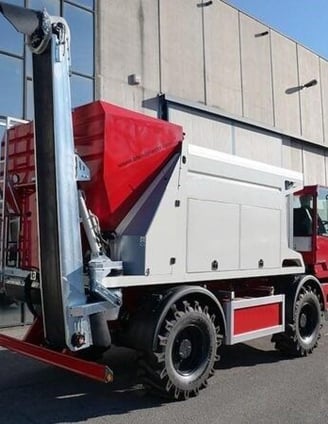
Automatic Batching Plant (Mobile)
It is the versatile plant par excellence with high production capacity, ease of transport from one work site to another and with no additional mounting operations required. The plant has total hydraulic and electrical autonomy. Each type of aggregate is transferred from the hoppers to the main conveyor belt, to the twin shaft mixer, by means of variable speed extractor belts. Aggregate Dosing is by negative weighing. Dosing of cement and additives is also by negative weighing, to give greater accuracy and reliability and dosing of water, emulsion and other additives is electronically controlled by electronic flow meters connected the onboard PLC. GPS and remote control systems allow you to have complete management information regarding production and stock levels at all times.
Unique Features
Plant can be easily transported: weights and dimensions allow it to fit in on conventional transport vehicles (No exceptional transport required).
Self-loading, no crane is needed.
The positioning is quick: it can be done in an hour and it does not require special installations or concrete foundations.
MATERIALS DATA
PRODUCTION REPORT
RECIPES MANAGEMENT
AGGREGATES MATERIALS MANAGEMENT
ASSISTANCE ON REQUEST
DIRECT MACHINE – TECHNICIAN CONNECTION
REMOTE / PANEL MIRRORING
DIRECT ACCESS TO MACHINE PARAMETERS
MONITORING SYSTEM
A system that allows remote machine management in a simple and intuitive way.
REMOTE ASSISTANCE
A remote assistance service for activities that can be performed remotely by the Blend specialist technician.
AUTOMATION
Automated production.
Aggregates / cement weighing and consumption reading.
Remote control from the client’s head office and by Blend technicians, to guarantee immediate assistance.
Discover more
-On-board computer for fully automated production with simple and intuitive software.
-The electronic control unit with military grade protection on Blend plants keeps the production and concrete flow under constant control by its sensors. Different types and qualities of recipes can be stored and selected. No manual operations are necessary.
-Weighing of aggregates/cements and reading of consumptions in Kg.
-Integrated printer with paper printout and digital report of different production lots. Humidity probe for automatic water adjustment in the recipe.
–Remote control for production managemen
The design offers 2, 3 or 4 hoppers to satisfy different needs: from the quantity of storage to the type of aggregates.
The loading of materials requires neither ramps nor civil works.
The material is loaded onto a tipper truck or a truck mixer by means of a height-adjustable conveyor belt.
HIGH EFFICIENCY TWIN SHAFT PADDLE MIXER
Discover more
-The continuous twin shaft mixer has been designed to be compact, easy to clean and maintain.
-It can be hydraulically extracted from the machine and comfortably positioned for cleaning & maintenance.
-The paddles are in Hardox and easy to replace.
-The production reaches up to 120 m3/h depending on the material recipe used.
mescolatore
HIGH QUALITY MIXING
TECHNICAL FEATURES
Aggregates 2 3 4 5
Hoppers capacity 9/11 m3 9/11 m3 14/15 m3 9/11 m3
Power diesel /electric 90 kW diesel /electric 100 kW diesel /electric 100 kW diesel /electric 100 kW
Dimensions ~10.500 x 2.530 x 3.100 mm ~13.500 x 2.530 x 3.100 mm ~24.120 x 2.530 x 3.550 mm ~21.100 x 2.530 x 3.550 mm
Weight ~18.000 kg ~21.000 kg ~40.000 kg ~34.000 kg
MIXER
Type Twin shaft paddle mixer Twin shaft paddle mixer Twin shaft paddle mixer Twin shaft paddle mixer
Power 30 kW 30 kW 30 kW 30 kW
Engine Hydraulic Hydraulic Hydraulic Hydraulic
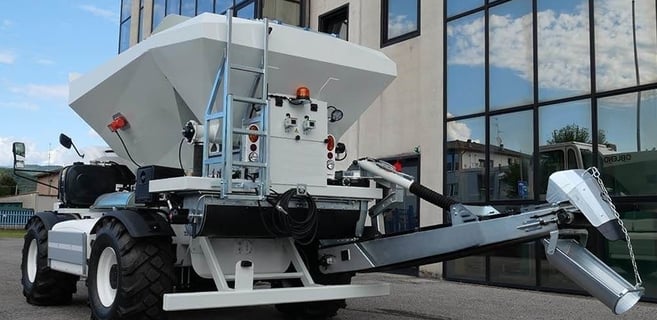
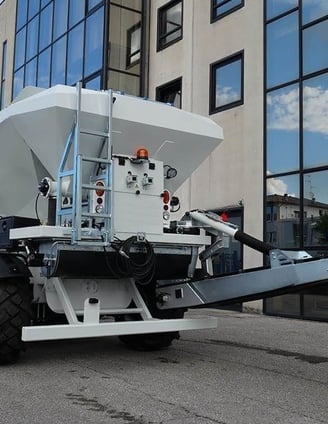
Automatic Batching Plant (Medium)
It is the versatile plant par excellence with high production capacity, ease of transport from one work site to another and with no additional mounting operations required. The plant has total hydraulic and electrical autonomy. Each type of aggregate is transferred from the hoppers to the main conveyor belt, to the twin shaft mixer, by means of variable speed extractor belts. Aggregate Dosing is by negative weighing. Dosing of cement and additives is also by negative weighing, to give greater accuracy and reliability and dosing of water, emulsion and other additives is electronically controlled by electronic flow meters connected the onboard PLC. GPS and remote control systems allow you to have complete management information regarding production and stock levels at all times.
Unique Features
Plant can be easily transported: weights and dimensions allow it to fit in on conventional transport vehicles (No exceptional transport required).
Self-loading, no crane is needed.
The positioning is quick: it can be done in an hour and it does not require special installations or concrete foundations.
MATERIALS DATA
PRODUCTION REPORT
RECIPES MANAGEMENT
AGGREGATES MATERIALS MANAGEMENT
ASSISTANCE ON REQUEST
DIRECT MACHINE – TECHNICIAN CONNECTION
REMOTE / PANEL MIRRORING
DIRECT ACCESS TO MACHINE PARAMETERS
MONITORING SYSTEM
A system that allows remote machine management in a simple and intuitive way.
REMOTE ASSISTANCE
A remote assistance service for activities that can be performed remotely by the Blend specialist technician.
AUTOMATION
Automated production.
Aggregates / cement weighing and consumption reading.
Remote control from the client’s head office and by Blend technicians, to guarantee immediate assistance.
Discover more
-On-board computer for fully automated production with simple and intuitive software.
-The electronic control unit with military grade protection on Blend plants keeps the production and concrete flow under constant control by its sensors. Different types and qualities of recipes can be stored and selected. No manual operations are necessary.
-Weighing of aggregates/cements and reading of consumptions in Kg.
-Integrated printer with paper printout and digital report of different production lots. Humidity probe for automatic water adjustment in the recipe.
–Remote control for production managemen
The design offers 2, 3 or 4 hoppers to satisfy different needs: from the quantity of storage to the type of aggregates.
The loading of materials requires neither ramps nor civil works.
The material is loaded onto a tipper truck or a truck mixer by means of a height-adjustable conveyor belt.
HIGH EFFICIENCY TWIN SHAFT PADDLE MIXER
Discover more
-The continuous twin shaft mixer has been designed to be compact, easy to clean and maintain.
-It can be hydraulically extracted from the machine and comfortably positioned for cleaning & maintenance.
-The paddles are in Hardox and easy to replace.
-The production reaches up to 120 m3/h depending on the material recipe used.
mescolatore
HIGH QUALITY MIXING
TECHNICAL FEATURES
Aggregates 2 3 4 5
Hoppers capacity 9/11 m3 9/11 m3 14/15 m3 9/11 m3
Power diesel /electric 90 kW diesel /electric 100 kW diesel /electric 100 kW diesel /electric 100 kW
Dimensions ~10.500 x 2.530 x 3.100 mm ~13.500 x 2.530 x 3.100 mm ~24.120 x 2.530 x 3.550 mm ~21.100 x 2.530 x 3.550 mm
Weight ~18.000 kg ~21.000 kg ~40.000 kg ~34.000 kg
MIXER
Type Twin shaft paddle mixer Twin shaft paddle mixer Twin shaft paddle mixer Twin shaft paddle mixer
Power 30 kW 30 kW 30 kW 30 kW
Engine Hydraulic Hydraulic Hydraulic Hydraulic
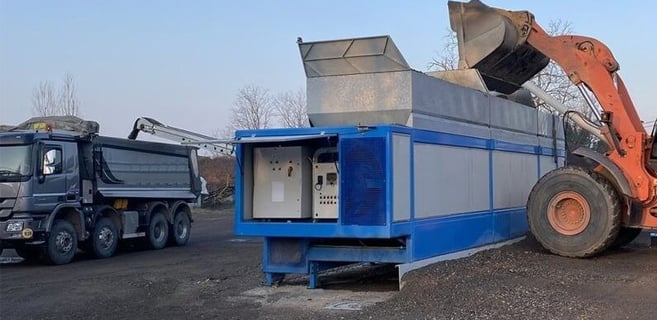
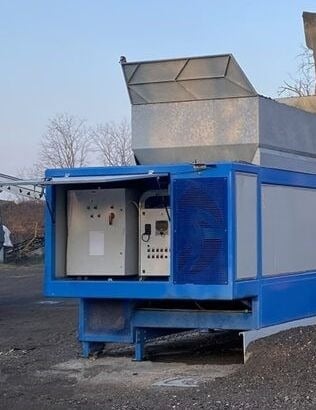
Automatic Batching Plant (Large)
The new generation of concrete mixing plants from revolutionize the production of concrete by enabling economical production. The modular design of our series offers a wide range of options that can be flexibly adapted to the customer's needs. This flexibility enables the quick and uncomplicated realization of both stationary and mobile concrete mixing plants.
Fast assembly and availability
Quick assembly
Installation of the mixing plants is extremely quick and cost-effective thanks to their folding concept and the integrated technology container with pre-cabling ex works.
series requires no foundation work - concrete production is possible after 9 days under the right conditions.
For the stationary series, only a level base plate or simple foundation strips are required - concrete production is possible after 15 days if the right conditions are met.
Mixing plants can be delivered within a few weeks, which enables efficient project planning.
The modules are delivered to the construction site as complete transport units. Thanks to transport optimization, special transports are no longer necessary for almost all system variants.
Mixing plants can be delivered within a few weeks, which enables efficient project planning.
The modules are delivered to the construction site as complete transport units. Thanks to transport optimization, special transports are no longer necessary for almost all system variants.
High energy efficiency
A significant innovation in modern mixing plants is the smoothing of power peaks. This is achieved through the use of frequency inverters and their parameterization, which intelligently start up and control all of the mixing system's drives. This not only significantly reduces connection costs to the power grid, but also noticeably reduces wear thanks to the smooth starting and stopping of the drives.
High energy efficiency
A significant innovation in modern mixing plants is the smoothing of power peaks. This is achieved through the use of frequency inverters and their parameterization, which intelligently start up and control all of the mixing system's drives. This not only significantly reduces connection costs to the power grid, but also noticeably reduces wear thanks to the smooth starting and stopping of the drives.
Mixer variety
Depending on customer requirements and application, different mixing systems can be installed in the same basic system. its own twin-shaft or ring-pan mixers for the highest demands. Output rates of 100 to 210 m³ of compacted fresh concrete per hour are possible.
Faster cleaning
Cleanliness and convenience reach a new level with the new cleaning solutions from us. cleaning solutions offer various options for efficient cleaning of the systems, saving up to 80 % time and 70 % water.
Generous space conditions
All accessible areas of the entire mixing plant are generously designed and offer sufficient space as well as very good access for maintenance and cleaning. Tools, spare parts or equipment can be stored at any time without compromising the working areas. All applicable standards for ergonomics and safety are complied with.
-Bolted for installation on site, mounted on concrete foundations
- One advantage is that no welding work is necessary
- Simple foundation or floor slab
Type 2.5 3.0 3.5 4.0 4.5
Theoretical output in compacted fresh concrete1 105 m³/h 125 m³/h 135*/139**m³/h 150*/154**m³/h 175*/250**m³/h
Theoretical output in compacted fresh concrete
with LiPerformance*** 115 m³/h 132 m³/h 148*/152**m³/h 165*/170**m³/h 193*/275**m³/h
Mixer size 2.5 m³
3.0 m³
3.5 m³
4.0 m³
4.5 m³
pan mixer ✓ – – – –
Twin-shaft mixer ✓ ✓ ✓ ✓ ✓
Max. Storage volume aggregates mobile in-line silo2 140-500 m³ 140-500 m³ 140-500 m³ 140-500 m³ 140-500 m³
Max. Storage volume of aggregates tower silo3 400-600 m³ 400-600 m³ 400-600 m³ 400-600 m³ 400-600 m³
Max. Number of cement silos 6 6 6 6 6
Vertical feeder elevator ✓ ✓ ✓ – –
Feeding belt ✓ ✓ ✓ ✓ ✓
Concrete foundations ✓ ✓ ✓ ✓ ✓
Steel foundations ✓ ✓ ✓ ✓ ✓
control system ✓ ✓ ✓ ✓ ✓
1 Mixing time 30 seconds
2 4-6 chambers
3 4-8 chambers
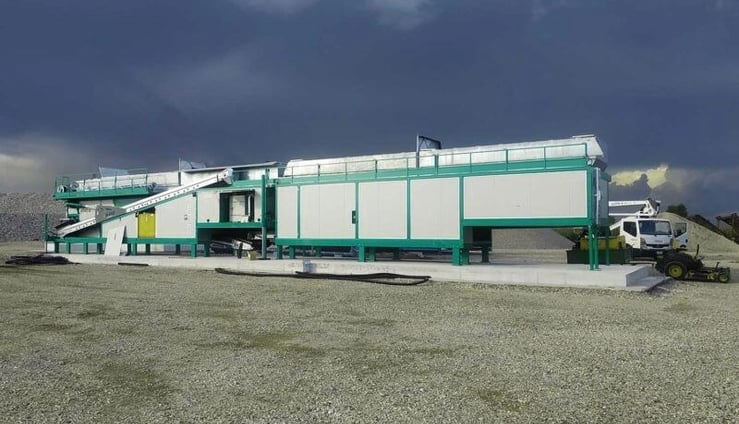
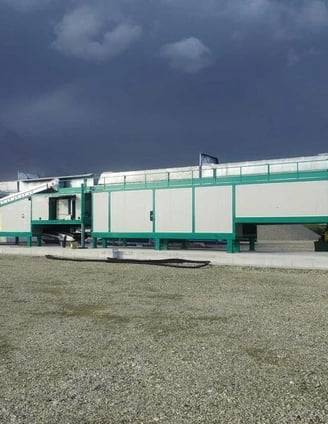