Vapour Deposition Coating
Our PVD and DLC/PECVD equipment offers a comprehensive solution for various coating technologies within a single machine, specifically designed for industrial applications. This advanced system effectively enhances the durability and performance of cutting and forming tools, precision-engineered components, automotive and aerospace parts, medical devices, and other critical components. By utilizing a magnetron sputtering system, it ensures rapid deposition of functional coatings that significantly boost wear and heat resistance while reducing friction, thereby extending the lifespan of both industrial and consumer products. The equipment achieves dense, smooth coatings comparable to those produced with HIPIMS technology, but does so at an accelerated deposition rate. This flexible solution meets the diverse needs of industries striving for high-quality performance and longevity in their products.
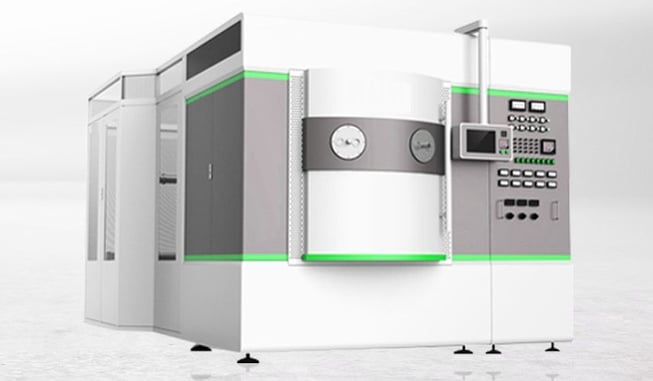
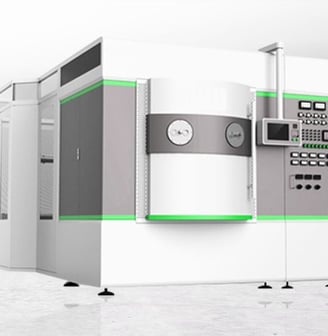
PVD Coating (Small)
Our system is a compact PVD & PECVD/DLC coating machine designed for easy operation. It offers durable color, functional coatings, and diamond-like carbon coatings.PVD coating equipment flexibilityThe small coating machine is the right-sized PVD and DLC coating system for customers who previously considered thin-film coating systems too complicated or expensive. Differentiate your product by applying the same hard, durable PVD or DLC finishes, which were previously only available to high-volume manufacturing operations, right in your facility.
The compact 6-rack design of this small PVD coating machine can deposit a wide range of durable decorative and functional PVD finishes on metal or plated parts, including some plastics. our system is suitable for both small and higher-volume applications, and many parts per batch means a low cost per part and a fast return on investment.
DLC
Diamond-like carbon coatings.
specifications
System capacity
System footprint
3.4m x 1.6m
Coating area per batch 4.79m2
Number of racks 6
Rack size 100cm x 25.4cm Ø
Coating technologies
Low-temperature cathodic arc vapor deposition
Coating processes
Physical vapor deposition (PVD)
Plasma-enhanced chemical vapor deposition (PECVD) to create diamond-like carbon (DLC) coatings
Available coatings
Pure, alloyed, or reacted zirconium, titanium, chromium, and carbon
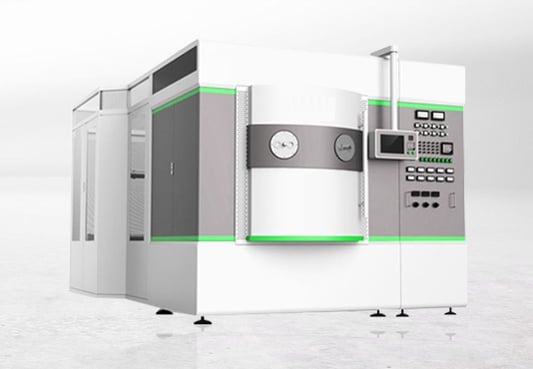
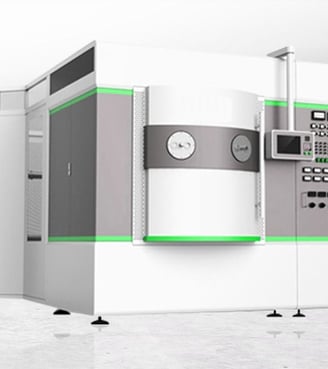
PVD Coating (Medium)
Long Span Shelving
Our PVD & DLC/PECVD equipment delivers multiple coating technologies in a single PVD coating machine for industrial applications in cutting and forming tools, precision-engineered components, automotive/aerospace parts, medical devices, and other components that require enhanced durability, lower friction, and longer product life span.• Modern turbomolecular vacuum pumps for excellent pumping performance and lower power consumption.
• Advanced cathodic arc, sputtering, bias, and ion source power supplies to improve coating quality and system reliability
• The compact system footprint is 2.1m x 4.8m and all components are on one skid for easier transport and a faster, streamlined installation.
• Straightforward maintenance with dual chamber doors, easy-to-remove deposition shields, and quick access to all sources for target changes.
• The most recent version of our simple-to-use VaporTech coating system software interface
Specifications
System capacity
Coating area per rack 80 cm x 25.4 cm ø (6 rack option)
Number of rack positions 6 standard (up to 12 optional)
Chamber coating zone 80 cm x 88 cm ø
System footprint 2.1 m x 4.8 m
Coating technologies
Low-temperature cathodic arc vapor deposition
Magnetron sputtering
Plasma-enhanced chemical vapor deposition (PECVD) to create diamond-like carbon (DLC) coatings
Plasma nitriding
Available coatings
Pure, alloyed, or reacted zirconium, titanium, chromium, aluminum, carbon, and other metals.
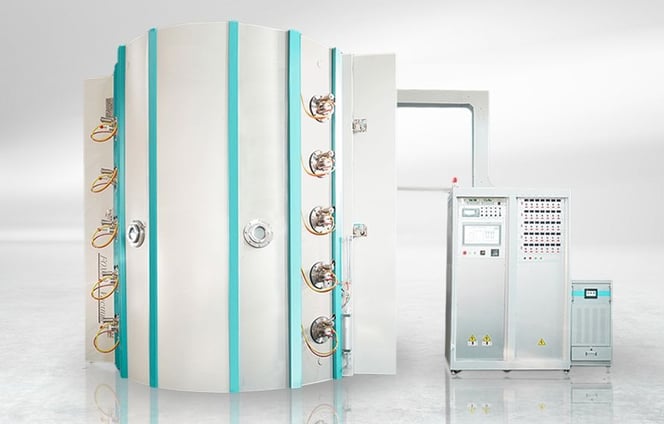
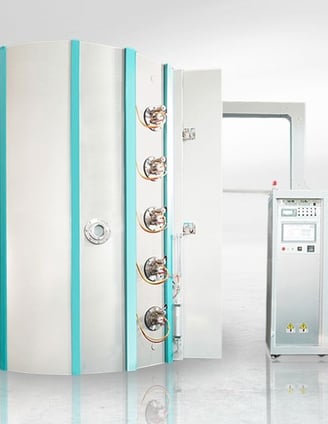
PVD Coating Large
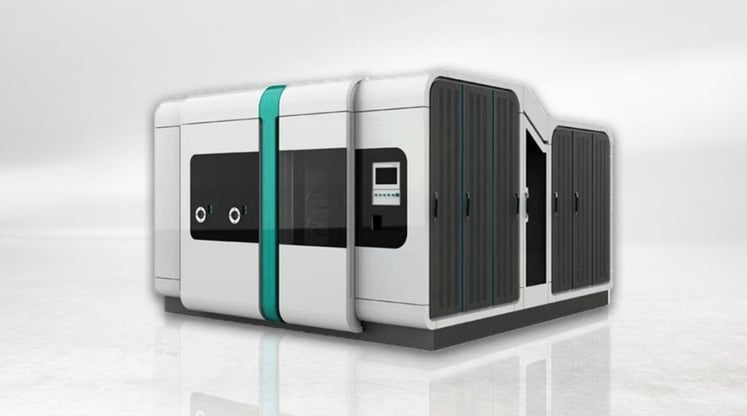
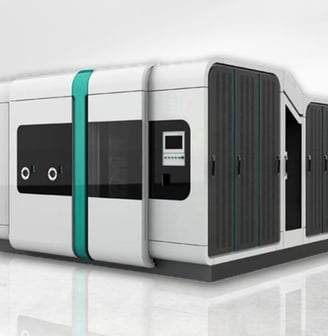
our largest PVD and PECVD/DLC coating system delivering our largest chamber and high throughput for large operationsour highest-capacity coating machine for large-scale operationsPVD coating machine is a large PVD and DLC/PECVD coating system for high throughput or larger parts up to 122 cm (48 in).
Our unique centrally mounted cathodic arc deposition source ensures you get consistency and maximum control over coating uniformity and properties. Lower temperatures enable you to coat various materials such as steel, brass, zinc, or prepared plastic, giving products made of multiple materials a common finish and appearance
• Our high-energy process that significantly improves coating structure, hardness, and wear resistance compared to traditional sputtering systems.
• High deposition rates shorten coating times for functional applications.
• Multiple coating sources further increase deposition rates or deposit composite materials.
• This compact system is easy for smaller manufacturers to use and maintain.
• The perfect performance machine for zirconium, titanium, chromium, or DLC coatings.
specifications
capacity
System footprint
4.3m x 3.6m
Coating area per batch 12.44 m2
Number of racks 16
Rack size 45cm x 20.3cm Ø
Size
Height 150 in. (3.8m)
Width 141 in. (3.6m)
Depth 170 in. (4.3m)*
Coating technologies
Low-temperature cathodic arc vapor deposition
Coating processes
Physical vapor deposition (PVD)
Plasma-enhanced chemical vapor deposition (PECVD) to create diamond-like carbon (DLC) coatings
Available coatings
Pure, alloyed, or reacted zirconium, titanium, chromium, and carbon
.
.,
Optic Lens vacuum Coating
Optic Lens vacuum Coating
Capacity:up to 305 lenses/batch Ø 70 mm with ringless full dome
Supports multiple lens coating process applications: Anti-Reflective and/or mirror coating on organic and mineral eyeglass lenses via thermal evaporation process (PVD).
Deposition of multiple coating process features in one single run.
Larger Meissner trap shortens times to start the deposition, increases process repeatability, and throughput.
Powerful & fast diffusion pump system
Electron beam gun - highly flexible for selection & exchange of coating process (mirrors, AR, colors).
Simplified electron-beam emitter for easier maintenance & increased lens coating reliability.
Ion beam assisted deposition for best layer adhesion on various substrates.
Special gradient & planetary substrate holders (available upon request).
Processes
for clear AR & Sun lens coating
Top coating - Hydrophobic, Super Hydrophobic & Super Hydro/Oleophobic
AR coating - Premium, Performance
Mirror coating -
vacuum box coater can be customized to meet your product, process and production requirements.
Perfectly matched ophthalmic lens coating processes, consumables, and box coaters guarantee best coating performance.
Tech Specs
6-sector dome lens capacity
Ø 65 mm up to 270 lenses/batch Ø 70 mm up to 246 lenses/batch
3-sector dome ringless lens capacity
Ø 70 mm up to 276 lenses/batch
Ringless full dome lens capacity:
Ø 70 mm 305 lenses/batch
Planetary cylinders lens capacity:
Available upon request
Lens material:
All organic materials and mineral glass
Dimensions (wxdxh):
2384 x 3295 x 2765 mm / 94 x 130 x 109 inches
Weight:
3900 kg / 8598 lb
Ophthalmic coating solutions for higher
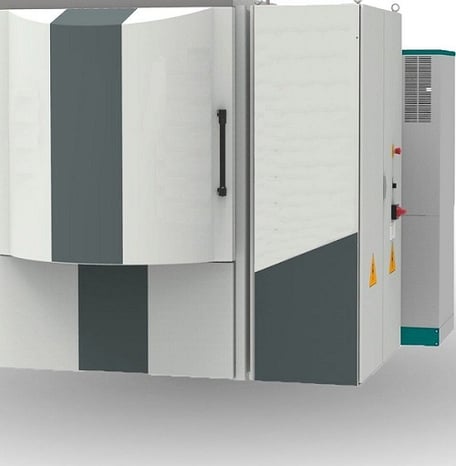
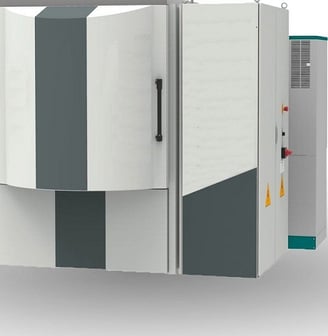