Textiles & Wood
. It helps Uniform heating through entire thickness of the various materials. Energy efficient and Eco- friendly than conventional drying methods. The products are made with state of the art technology with very low maintenance compared to conventional heating equipments. Various products / materials and packaging can be heated / treated in single unit which means less capital investment. Due to immediate heating there is no need of warm up time; So you can meet Rapid pay-back time with No pigment or dye contamination you get Improved quality of the end product.ndustrial Microwave Fabric Drying improves product quality, reduces costs, and increases drying speeds for textiles, fabrics, and nonwovens. Microwave technology, fabrics that require heating or drying benefit from pre-drying, post-drying or complete drying with retrofitted or standalone systems. Our heating and drying systems may retrofit onto existing conventional infrastructure as pre- or post-dryers to increase production speeds. microwave has several designs of commercialized industrial microwave fabric drying systems for knits, towels, yarn, rope, carpet, and other nonwovens.
industrial microwave fabric drying system for a leading producer of woven fiberglass fabric. The system needed to dry one-half ounce per square yard to four and one-half ounces per square yard fabric after saturation through a size bath to a final moisture content of less than 0.2%.
The system also needed to eliminate fabric damage typically generated from the latent heat of conventional drying during the numerous stops and starts in the process. accomplished these objectives, while also increasing process speeds and installing the system on a balcony with limited headroom.
915 MHz Planar Drying System oriented vertically in eight linear feet of headroom and two and one-half feet in the machine direction on an overhead platform. The system doubled drying speeds. It also eliminated off quality since there was no latent heat generated by the microwave energy during stops and starts.
Overall, textiles applications benefit from the excellent color drying and adhesive setting properties of microwave power. Also, as a process that involves drying as well, microwave treatment has an added benefit.
Common Product Applications
Fabrics, textiles, and non-woven products that are typically dried with microwave systems include
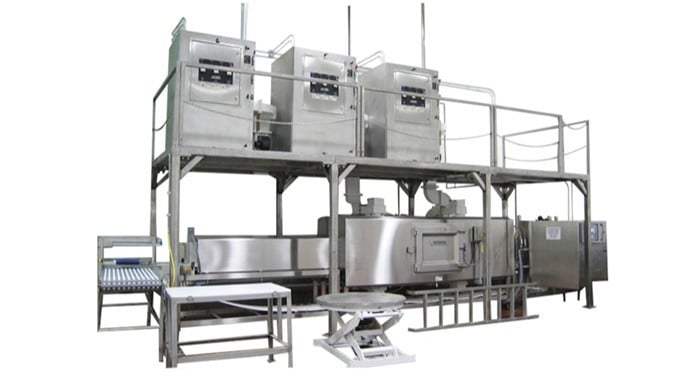
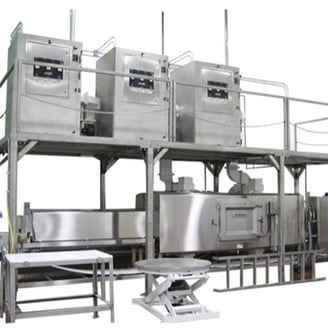
Microwave Textile Drying
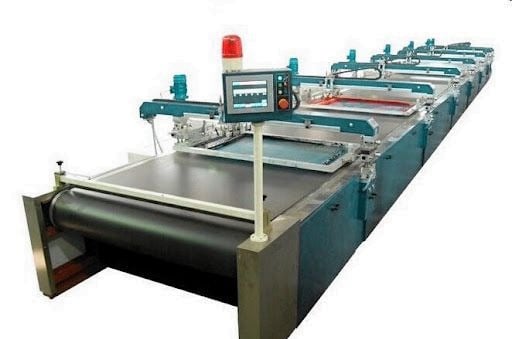
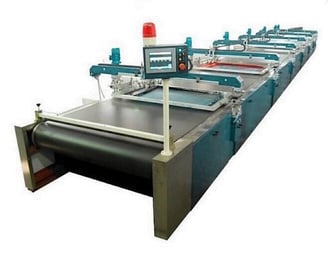
The Fastest Flatbed In The Market
Our Printer Provides High-Performance Printing And Friendly Machine Operation. The Extra Line Control And Driving System Allows For Top-Down Access To All The Main Functions Through One 15-Inch Tft Touch Screen And Two 6-Inch Touch Screens At The Entry And Exit Of The Printer. With The Printing Pressure Applied On The Screen Is Simple And Precise, Assuring High-Quality Results With All The Repeats – But With No Need For Any Additional Equipment. The Desired Features Of Hand Printing Are Available Because Of The Innovative Pressure/Speed Adjustment System. Lifting-Up Speed, Lifting Height, And Delays Can Be Adjusted For Each Stroke, Satisfying The Needs Of Any Printing Application.
Highlights
Wide Range Of Fabrics
Suitable For Any Kind Of Fabric From Woven, Knitted, Elastic, And Synthetic, To Cotton And Silk.
Machine Entry
Fabric Feeding, Using Built-In Devices, Allows For Constant Control Of Fabric Width, Tension, And Type Of Fabric. The Dynaplast System Synchronizes The Blanket Advancement With The Entry Speed To Reduce Fabric Tension, Making It Ideal For Knitted Fabric.
Simple Operation
Easy And Simple Man/Machine Operation Using Touch Screens And Touchpad. The Control Panel, Placed On The Operating Side Of Each Printing Unit, Provides Functions Such As Printing Speed, Printing Mode, Printing Pressure, And More.
Precise Blanket Movement
Printing Blanket Movement Is Driven By Brushless Motors And Is Controlled In A Closed Loop For Precise Control. The Printing Pressure Applied On The Screen Is Easily
And Perfectly Achieved, Even With Big Repeats. Thanks To Our Latest Innovations, Great Printing Evenness Is Achieved With All The Repeats And With No Need For Any Additional Equipment.
The Peculiar Features Of Hand Printing Are Available Because Of The Innovative Pressure/Speed
Adjustment System. Lifting-Up Speed, Lifting Height, And Delays Can Be
Adjusted For Each Stroke, Satisfying The Needs Of Any Printing Application. Additionally, All Of The The Printing Parameters Can Be Easily Saved And Reproduced Thanks To The Top-Down Interfaces.
Machine Entry
The Fabric Feeding Uses Built-In Devices To Keep All
Desired Variables Constant And Controlled, Like:
• Fabric Width
• Fabric Tension
• Kind Of Fabric
System Synchronizes The Discontinuous Blanket Advancement With The Entry Speed By Providing
Constant Speed At The Introduction Of Fabric. This Reduces The Fabric Tension And Is Particularly Suitable For
Knitted Fabric. System Can Be Heated, Which Allows You To Glue The Fabric Onto The Printing Blanket In Caseof Thermoplastic Adhesives. Suitable For Any Kind Of Fabric: Woven, Knitted, Elastic, And Synthetic, From Cotton To Silk
• Bridge Printing Units Equipped With Rubber Squeegees
• Weft Wise Printing Movement
• Pneumatically Adjustable Squeegee Pressure
• Easy And Simple Operation With Touch Screens Andtouch Pad
• High Flexibility
• Blanket Movement Control In A Closed Loop
• Highly Reliable And Efficient Electronics
• High-Quality Printing Blanket Driven By Brushless Motors
Control Panel
The Control Panel, Placed On The Operating Side Of Each Printing Unit, Has The Following Functions:
• Printing Speed: From 1 To 9, Independently Adjustable For Each Direction
• Printing Mode: From 1 To 9, Squeegees Or Flood Stroke
• Printing Pressure: From 1 To 9, Independently Adjustable For Each Direction
• Intermediate Delays Between The Squeegee Passages
• Adjustable Lifting Height To Enable Printing Blanket Advancement
• Adjustable And Self-Learning Squeegee Stroke
• Test Of A Printing Cycle With The Selected Parameters (Cycle Test)
• Unlocking Device For Printing Unit’s Movement Along The Printing Table
15” Main Touch Screen With Colors Touch Screen For Adjustment And Drive Of Printing Heads
Technical Data
Models 1800 , 3200, 3400 mm
Useful Printing Table 6-60 M
Number Of Installable Colors From Four To Max 24
Repeat Fractioning Optional
Squeegee Pass Weft Wise
Squeegee System Bridge, Extraline
Printing Unit Set Up Independent Per Each Printing Unit
Advancement At Adjustable Speed
Screen Lifting Up At Individually Adjustable Height And Speed
Flat Screens Serigraphic With Four Hook-Up Devices
Operating Side Right Or Left (Upon Request)
Color Feeding Manual Or Automatic (Optional)
Printing Table Height 32 In (80 Cm) From The Ground
Flatbed Textile Printer
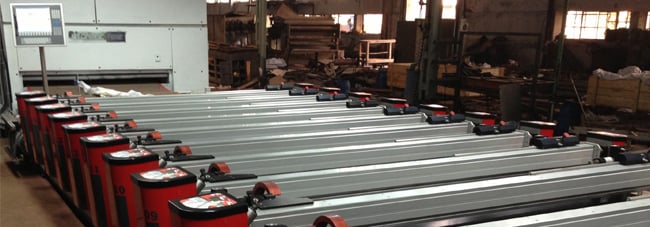
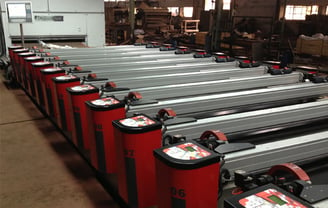
In Rotary Screen Printing, Several Factors Influence The Quality Of Your Printing Results, Such As The Printing Paste And The Screens You Use. The Price You Pay Is Of Course Also Related To These Factors. There Is Good News About That. Introduced A Way To Reduce Process Costs And Improve Product Quality, Without Having To Change The Process Itself. This Will Increase Your Competitiveness In The Printing Business.
We Developed Eco Specifically To Be Both Economically And Technologically Advantageous. The Most Important Adjustment? This Screen Allows More Control On The Print Process And Paste Deposition Than Standard 125mesh Screens. It Brings Other Interesting Features Like A Random Adjustment Of The Holes And Superior Stability Customers Worldwide Are Printing Woven And Knitted Fabrics, Wide And Narrow Width, For Household And Fashion With Great Satisfaction And Profitability.
The New Printing Units Highlight The Typical Features And Advantages That, Top-Quality Printing Machines:
• Closed Bearing Printing Heads
• Multi-Repeat Printing Heads (From 25 In/640 Mm To 40 In/1018 Mm, No Tools Needed)
• Totally Sealed And Lubricated Printing Heads (No Maintenance Required)
• Step Less Adjustment Of Printing Height According To Fabric Thickness
• Step Less Adjustment Of Printing Width (Any Screen Cutting Length Accepted)
• Individual Screen Drive With One Or Two Brushless Servomotors In Closed Loop
• Uniflux Linear Magnetic System
• Easy And Simple Machine Operation, With Touch Screen Interfaces
• High Reliability-Efficiency Electronics.
Closed-Bearing Print Heads
• High Precision And Accuracy
• Self-Aligning Screen Holders
• Evenness In Screen Tension
• Perfect Driving Of The Screen
• No Risk Of Damaging The Screens, No
Mechanical Wearing
• Totally Sealed And Lubricated Print Heads
(No Maintenance Required)
• Easy Screen Installation (With One Operator Only)
• Optimum Control/Access To The Printing, Even With Big Repeats, Thanks To The Large Distance Between The Print Heads
Uniflux Linear Magnetic System
• Perfect Evenness And Uniformity, Even With Widewidth Fabrics
• No Center-Right, Center-Left Effect
• High Flexibility
• Digital Printing Pressure Stepless Adjustment, From Ultra-Low To Very High Pressure
• High Efficiency And Very Low Energy Consumption
• No Pole-To-Pole Overpressure (Typical In Multi-Beammagnet Systems)
Multi-Repeat Print Heads
Totally Pneumatic And Electronically Controlled Between 25 In/640 Mm And 40 In/1018 Mm, And No Tools Are Needed To Change The Repeat. The Operator Sets The Repeat Value On The Main Touch Screen, And All The Print Heads Raise Up So The Screens Can Be Easily Installed On The Machine Without Any Extra Mechanical Parts To Save Time.
Individual Screen Drive
Easy And Friendly Machine Operations, High Efficiency And Low Consumption
All The Electronic Components Are The Most Updated And Highest Performing Available On The Market: The Standard Of
(Plc, Motion Controls, Inverters, Control Panels, And Touch Screens).
The Interfaces Are Simple To Understand And Easy To Use:
• One Touch Screen At The Front Of The Machine
• One Touch Screen On Each Printing Unit (Optionally Available On Both Sides)
• One Main Control Board With A 15ʺ Tft Touch Screen
• One Touch Screen At The Exit Of The Dryer
The Printing And Design Parameters Can Be Easily Adjusted, Saved, And Automatically Reproduced. High Reliability And Very Low Energy Consumption Energy Consumption Is Becoming More And More Important In An Industrial Budget. Which Has Always Been Concerned About Environmental Issues, Has Equipped Its Rotary Printing Machines With Inverters On The Dust And Lint Removal Device, On The Blanket Washing, On The Dryer Fans, And On The Dryer Exhaustion To Guarantee A 25% Savings On Energy Consumption.
Blade Squeegee 180 Cm, Repeat 640
Squeegee Blade Isoform Print Height 1800, Repeat 640. Each Situation Requires A Diverse Setup With Available Adjustments Of The Printing Squeegee System/Color/Cylinder The Squeegee Isoform Can Be Used For Any Type Of Printing On Any Article. The Operations Of Introduction/Extraction Is Facilitated By The Swivel Releasing Completely In The Introduction Section. With No Operator Required, In 10‑12 Minutes, It Is Possible To Wash And Dry All The Screens, Pumps, Color Pipes, And The Blanket On The Machine. The Length And Amount Of Washing And Drying Cycles Can Be Determined By The Operator (And Then Saved And Automatically Reproduced).
After The Washing/Drying Cycles, The Machine Is Ready To Re-Start Printing Without Any Extra Time To Register The Screens. Conceived Mainly For The Colorways, The Wol Washes So Fast And Well That It Is Typically Used For Printing New Designs, Too.
Technical Data
Models 1800mm 2400mm 3200 Mm
Number Of Colors Up To 24
Speed Up To 90 M/Minute
Print Heads Closed Bearing, Self-Aligning, Lubricated
Multi-Repeat Print Heads From 640 To 1018 Mm , Stepless Adjustment,
Electronically Controlled
Screen Drive With One Or Two Brushless Motors
Printing Width Stepless Adjustment
Squeegee System With Uniflux Linear Magnetic System
Operating And Color Side Right Or Left
Gluing System Water Soluble Glue As Well As Thermoplast
Blanket Washing System Two Variable Speed Brushes, Four Rubber Squeegees (The Last One Adjustable)
Interfaces Touch Screens On Each Printing Unit, Touch Screens At The Entry/Exit Of The Machine, One Control Board With A 15ʺ Tft Touch Screen; All With Colors
Electrical Cabinet Conditioned
Rotary Screen Printing Machine
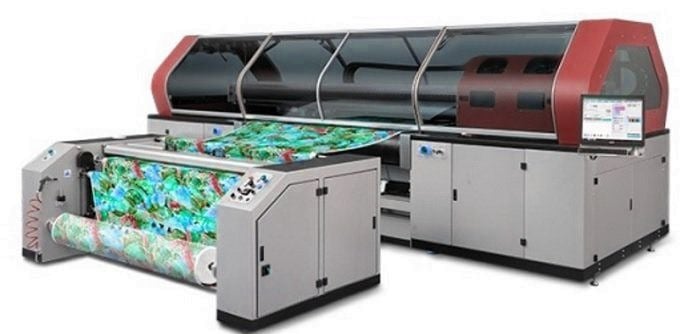
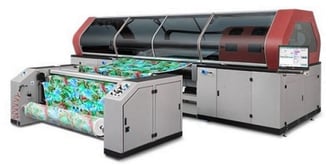
High Speed, High-Quality Digital Textile Printer
Digital Fabric Printing Machine, Which Fantastically Incorporates The Latest Technology And Efficient Engineering To Meet The Ever-Growing Demands Of The Textile Business. As A Digital Textile Printing Consultant, This High-Speed Fabric Printing Machine That Is Compatible To Work With All Types Of Inks Like Reactive, Acid, Disperse, And Pigment. This Industrial Textile Printer Weaves Magic On A Variety Of Fabrics, Ranging From 0.1 Mm To 30 Mm Including Cotton, Polyester, Silk, Viscose, Wool, Nylon, Acetate, Or Any Other Blended Fabric. This High-Speed Digital Textile Printing Machine From Indian Textile Printing Leaders,
It Is The Best Printing Solution For Businesses With An Intent To Invest In Sustainable And Performance-Oriented Digital Textile Printing Solutions. Offers A Clean Future For The Environment. Ink With Binder Offers Greener Solution By Way Of Eliminating Process In Digital Textile Printing. Polymerization At 160-Degree After Printing Provides Excellent Color Fastness And Print Quality With Exceptional Production Capacity
Our Latest Digital Fabric Printer Is A Great Combination Of High Speed And High Quality. It Is The Best Printing Solutions For Businesses That Want To Experiment With Different Patterns Like Checks, Stripes, Geometric Designs On Fabrics And Make Them Appealing Without Compromising The Quality.
The Machine Delivers Magnificent Prints Using Original Inks Available In The Configuration Of 8 Colors Options And Is Equipped With 32 Industrial Grade Print Heads.
Digital Fabric Printing Machine Addresses Various Market Segments Such As Fashion Apparels (Women’s, Men’s, And Kids Clothing), Home Furnishings (Curtains, Bedsheets, Sofa Covers), Etc. This Digital Fabric Printing Machine Is Used To Print Shirts, Skirts, Scarves, And Sarees. Prints On Cotton, Viscose, Polyester, Polyamide, Silk, And Wool And Is Suited For The Production Of High-Quality Products As Well As Home Decoration Fabrics.
Printing Technology Drop-on-demand , Piezo Electric Inkjet
No. of Print Heads 8 KY 8 KY
Print Heads Type Industrial Grade Jetting Assemblies
Resolution Upto 1200 DPI
Height Adjustment upto 20mm
CleaningMethod Pressure Purge and Wiping
Wetting Control Piezoelectric Actuations
Inks Types Reactive/Disperse/Pigment/Acid
No of colors 8 8
Supply 10 Ltr, Bulk ink Supply System with inline degassing
Digital Textile Printer
We manufacture and specialized microwave systems for laminated veneer lumber , in addition to other wood products. Microwave heating has several uses in the production of various wood products and related materials.
For processes involving heating or drying, in which there are many, microwave energy increasingly acts as a substitute for more traditional ovens fired by oil or gas. Our industrial microwave systems are widely used in lumber processing.
Systems are often used in stand-alone heating and drying applications. However, we also see success with pre-heating materials prior to entering a conventional dryer. This also helps raise product moisture to its evaporative temperature. In addition, post-drying materials after a conventional dryer optimze the uniformity of final moisture content.
Microwave Technology for Wood Products: Benefits and Advantages
Industrial microwave wood drying systems and technology has several advantages over contentional dryers.
• Increasing production throughputs
• Rapid and uniform volumetric heating
• Much faster and more efficient than using kilns
• Preheating product to evaporative temperature
• Removing water from products with relatively low moisture content
• Environmentally friendly with no dangerous emissions or other hazards
• Products with less deformities as caused by overheating with other technology
Common Applications
While there are several different types of wood products, the most common applications involving microwaves include:
• Wood
• Timber
• Plywood
• Wood chips
• Engineered wood
• Laminated veneer lumber (LVL)
For other bonding and drying applications of this nature, system will likely suit the requirement.
In addition to these standard systems, we also offer modularized units. Both the ridged waveguide and wide applicators can heat and dry products with a width up to about 120 inches or 3000 mm. Since Industrial Microwave Systemscan offer three different types of planar applicators, it may provide a better solution than other multimode designs.
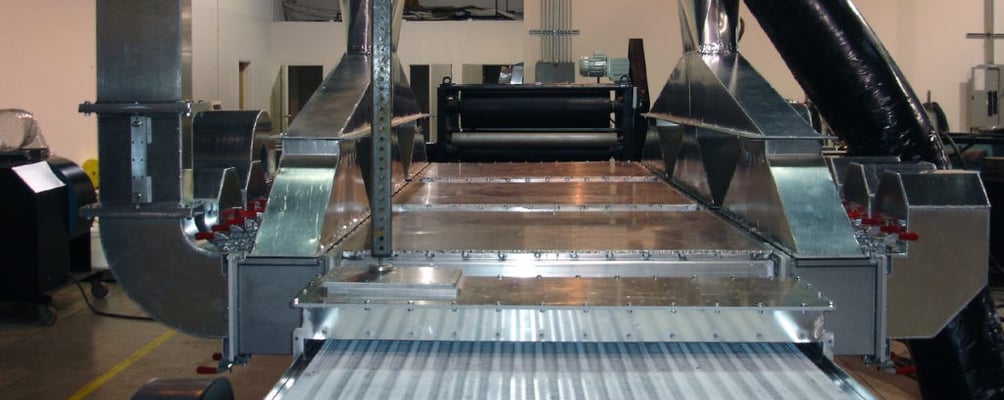
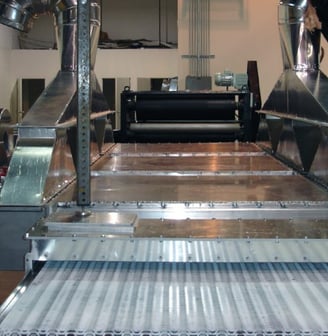