The trend of bringing SLA 3D printing in-house has been driven by several key factors. First, the cost of high-quality SLA printers has decreased significantly, making them more accessible to a wider range of businesses. Additionally, the printers themselves have become more reliable and user-friendly, allowing for smoother integration into existing workflows. Advancements in printing materials have also expanded the range of possible applications, attracting professionals from engineering, manufacturing, and healthcare. By establishing their own resin 3D printing capabilities, organizations can enjoy numerous benefits, including reduced costs and shortened lead times for both internal projects and customer demands. This technology not only enhances operational efficiency but also fosters innovation, enabling businesses to bring their ideas to life more rapidly and effectively.
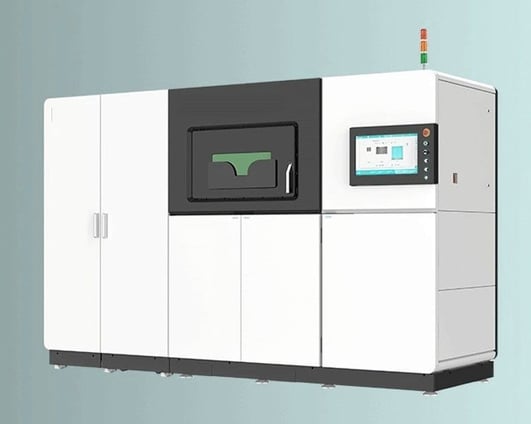
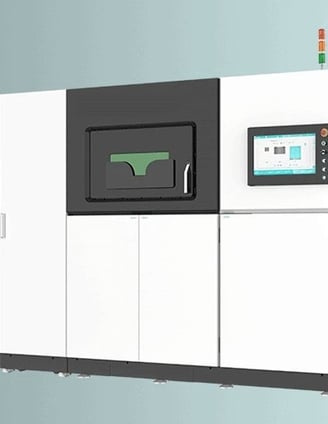
3D Stereo Lithographic Printer
3D SLA Printer ( Large)
Fully-integrated Factory Solution for Direct Digital Production
Leading Throughput
The combination of speed and accuracy complemented by a light-based UV curing process that takes minutes vs. hours with heat-based curing processes, yields the world’s fastest additive manufacturing throughput and time-to-part. Recent data highlights Production part print speeds up to 65 mm/hour, and prototyping speeds of up to 100 mm/hour, and part accuracy and Six Sigma repeatability cross all materials.
A customizable, fully-integrated solution for direct 3D production
PRINTER HARDWARE
Build Volume (xyz) 124.8 x 70.2 x 346 mm (4.9 x 2.8 x 13.6 in)
Throughput Up to 1 print job per minute
(part geometry dependent)
Resolution 1920 x 1080 pixel
Pixel Pitch 65 microns (0.0025 in) (390.8 effective PPI)
Wavelength 405 nm
Operating Environment
Temperature
Humidity (RH)
24/7 operation design
18-28 ºC (64-82 ºF)
20-80%
Electrical 208/120 Vac, 3-phase Y, 60 Hz; 60A (max)
Compressed Air 90 psi min, 2 cfm, dry air
Dimensions (WxDxH)
Control Cell crated
Control Cell uncrated
4-Print Engine Cell crated
4-Print Engine Cell uncrated
116.8 x 121.9 x 233.7 cm (46 x 48 x 92 in)
76.2 x 132 x 210.8 cm (30 x 52 x 83 in)
116.8 x 121.9 x 233.7 cm (46 x 48 x 92 in)
88.9 x 91.4 x 210.8 cm (35 x 36 x 83 in)
Weight
Control Cell crated / uncrated
4-Print Engine Cell crated /
uncrated
430.9 kg (950 lbs) / 363 kg (800 lbs)
408.2 kg (900 lbs) / 340 kg (750 lbs)
MATERIALS
Build Materials See material selector guide and individual
material datasheets for specifications on
available materials.
Material Packaging 9 kg click-in cartridges for automated
replenishment; 2 per printer quad
SOFTWARE AND NETWORK
System Interface Ethernet, USB host
Native File Format PXL native via 3D Sprint
3D Sprint® Software Easy build job set-up, submission and job
queue management; Automatic part placement
and build optimization tools; Part nesting
capability; part editing tools; Automatic support
generation; Job statistics
3D Connect™ Software
Capable
3D Connect Service provides a secure cloudbased connection to 3D Systems service teams
for proactive and preventative support.
Client Hardware
Recommendation
• 3 GHz multiple core processor (2 GHz Intel® or
AMD® processor mini) with 8 GB RAM or more
(4 GB mini)
• OpenGL 3.2 and GLSL 1.50 support (OpenGL
2.1 and GLSL 1.20 mini), 1 GB video RAM or
more, 1280 x 1024
(1280 x 960 mini) screen resolution or higher
• SSD or 10,000 RPM hard disk drive (minimum
requirement of 7 GB of available hard-disk
space, additional 3 GB free disk space for
cache)
• Google Chrome or Internet Explorer 11
(Internet Explorer 9 mini)
• Other: 3 button mouse with scroll, keyboard,
Microsoft .NET Framework 4.6.1 installed with
application
Client Operating System Windows® 7 and newer (64-bit OS)
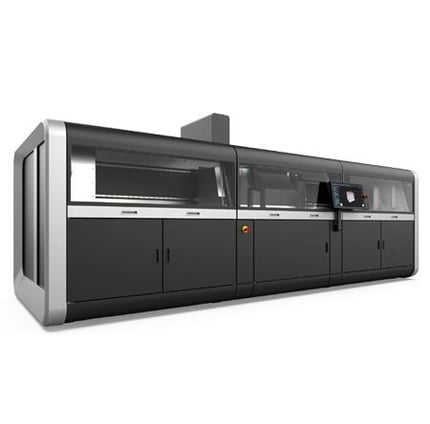
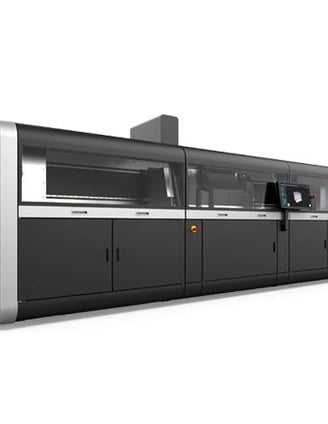
3D FDM Printer
Extrusion printing, sometimes referred to fused filament fabrication (FFF) or fused granulate fabrication (FGM), starts when a thermoplastic feedstock—such as plastic filament or pellets—is forced through a heated nozzle, melting the material and depositing it on a print surface. Either the nozzle, the print bed, or a combination of the two are moved on a gantry in XYZ space, enabling the gradual creation of an object from the bottom up, layer by layer.
Extrusion
The thermoplastics used in extrusion printing are available in a wide range of formulations from commodity plastics like PLA, ABS, PETG, ASA, polycarbonate and nylon to aerospace and high-performance polymers for healthcare such as PEEK and PPSU. Elastomers and carbon-reinforced or glass-filled materials are also available. The open market for extrusion printing materials is expansive, but not every material is printable on every machine. The feedstock format, filaments or pellets, is a primary consideration, as well as maximum nozzle, bed and chamber temperatures.
a person's hand scooping up black, plastic pellets
Pellets
Thermoplastic pellets are the most affordable 3D printing feedstock available. Pellets also enable high speed printing with larger nozzles, making them the preferred feedstock for large-format extrusion additive manufacturing. Pellet printing also allows the use of highly flexible elastomers as well as high-percentage carbon and glass-filled plastics that are difficult or impossible to print with filament.
a roll of filament material
Filament
Most extrusion-based 3D printers use thermoplastic filament feedstock due to its convenience and availability from various suppliers. Filament is supplied on spools, making it easy to handle and store. Filament is the preferred choice for highly detailed parts and when a clean surface finish is essential.
Explore Extrusion Materials
Explore our full catalog of pellet and filament extrusion materials for prototypes, production tooling, end-use production parts, and medical applications.
Learn More About our Extrusion 3D Printers
3d Systems’ growing line of extrusion (EXT) 3D printers are reliable, high-performance machines designed for professional and industrial use. Functional parts printed on EXT machines can be found in factories, vehicles, art galleries, hospitals and even human bodies.
Pellet Specifications
•
BUILD VOLUME
Pellet
Print 1070mm X x 1070mm Y x 1118mm Z (42”x42”x44”)
Cut 1041mm X x 990mm Y x 990mm Z (41" x 39" x 39")
Print 1070mm X x 1070mm Y x 1219mm Z (42”x42”x48”)
Cut N/A
TOOLHEAD CONFIGURATIONS
One Toolhead (Standard) Pellet Extruder
Two Toolheads Dual Pellet Extruders, Pellet + Filament Extruder, Pellet Extruder + Spindle
Three Toolheads Pellet Extruder + Filament Extruder + Spindle, Dual Pellet Extruders + Spindle
One Toolhead (Standard) Pellet Extruder
Two Toolheads Pellet Extruder + Filament Extruder
Three Toolheads Pellet Extruder + Dual Filament Extruders
TEMPERATURES
Pellet Extruder 400°C
Filament Extruder 400°C
Bed 140°C
Enclosure 80°C
SPINDLE FEATURES
Speed 18,000 RPM (1.5HP)
Tool Size Up to 1/4" diameter, 4" length
Tool Calibration 3-axis sensor configuration
•
EXTRUSION CAPABILITIES
Pellet Nozzle Diameters 0.6 mm - 9.0 mm
Pellet Layer Heights 0.4 mm - 6.0 mm
Pellet Extruder Throughput .45kg - 13.6kg* (1lb - 30lbs*) per hour
Filament Nozzle Diameters 0.4 mm - 1.2 mm
Filament Layer Heights 0.15 mm - 1.0 mm
Filament Throughput <.45kg - .9kg (<1lb - 2lbs) per hour
*Max flow rate with 9 mm nozzle
CONTROL SYSTEM
Motion Controller CNC Controller
Drives Servos on all axes
Print Speeds Up to .5m/sec
Slicing Software Simplify3D
SYSTEM REQUIREMENTS
Power Input 208V Three Phase 60A
Machine Weight 2041kg (4500lbs)
Machine Footprint 2.4m x 2.1m x 2.6m (8' x 7' x 8.6')
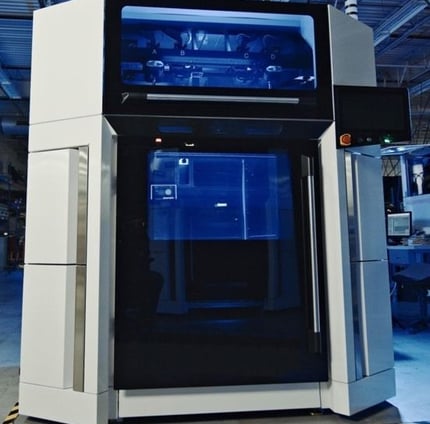
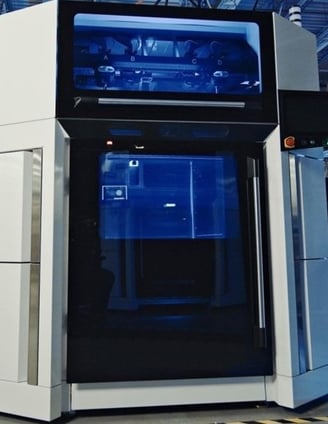
3D Wax Printer
Tool-less production of 100% wax casting patterns
Unmatched Turnaround Time
Save weeks on wax pattern production with tool-less MultiJet Printing and accelerate time-to-market. IC enables a digital workflow with direct wax pattern printing, increasing productivity and enabling fast time-to-part for premium service delivery to customers. With fast wax pattern production, short cycle times capability and 24/7 operation, you can rely on the output and improved casting room efficiency.
Time Breakeven Graph
Save weeks on wax pattern production with the ProJet MJP 2500 IC
At a Fraction of Tooling Costs
Have hundreds of your small to medium-size patterns in hand more quickly and less expensively compared to the time and cost to build and run a traditional injection tool. If design changes are needed, the benefits just compound. leverages existing investment casting processes and equipment. Expect fast amortization and high returns on investment with this unique industrial wax pattern 3D printing solution.
Total Pattern Cost Graph
Have hundreds of patterns in hand at a fraction of tooling costs
Ultimate Design Freedom
With digital design, you can produce wax patterns for parts that take advantage of topology optimization, lightweighting, and part consolidation. frees you to produce multiples of a complex part geometry or simultaneously make design variants, all while delivering better performing, more cost-effective components in a fraction of the time of traditional alternatives.
Casting Bracket
Deliver better performing, more cost-effective components with topology optimization and part consolidation.
Best Casting Reliability
Cast 100% wax material emulates the melt and burn-out characteristics of standard casting waxes. This RealWax 3D printing material drops seamlessly into existing wax casting processes. MultiJet Printed patterns hold tight tolerances, ideal for complex precision metal components manufacturing with reduced or no finishing work.
High fidelity and repeatability
Smooth surfaces
Sharp edges
Extreme fine details
Cast RealWax material drops seamlessly into existing wax casting processes
Optimized Resources
Streamline your file-to-pattern workflow with the advanced 3D Sprint® software capabilities for preparing and managing the additive manufacturing process, unattended high-speed printing and a defined and controlled post-process methodology. MultiJet Printing ease-of-use and dependable process ensure reliable performance, yield, and results.
End-to-end software solution for MultiJet Printing workflows
Manufacturing Agility
MultiJet Printing provides more flexibility and versatility to develop your business with an efficient solution for wax patterns production. Create, iterate, produce and refine as required with just-in-time pattern production.
The Digital Foundry with Invest Cast
Industrial Casting
Cutting weeks off your investment casting production with tool-less 3D printed casting patterns
Wax Casting Patterns in Hours
Ideal for customized metal components, bridge manufacturing, and low volume production, produces hundreds of 100% wax casting patterns at a fraction of the cost and time of traditional wax pattern production. Delivering design freedom, quality and repeatability, RealWax patterns drop seamlessly into existing foundry investment casting processes.
Benefits
Tech Specs
Low to mid-volume production
Bridge manufacturing
Instant design validation with multiple version testing
Customized metal components
Parts consolidation into higher performing units with no assembly labor/costs
Higher part complexity not achieved through traditional molding
Topology optimization and lightweighting
Rapid metal casting prototyping
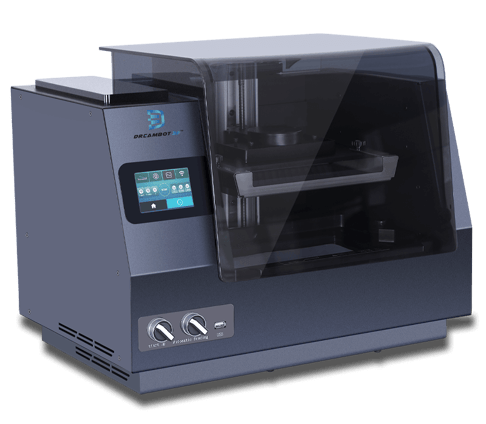
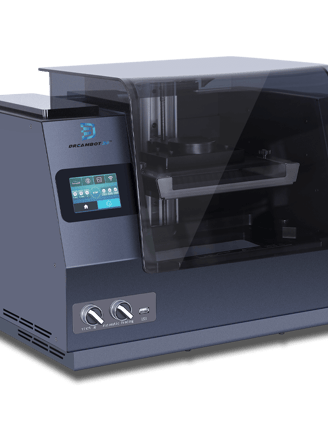