Roll Forming Lines
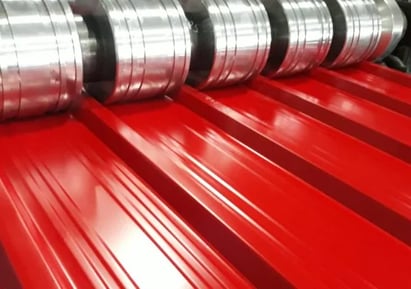
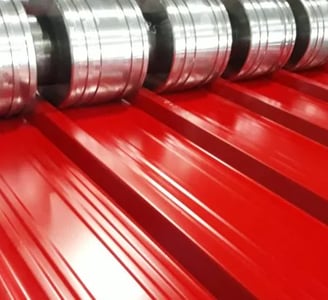
The sheet metal roll forming machine is designed for the efficient production of customized metal frames, offering precise measurements and user-friendly operation. Engineered for durability and affordability, this machine integrates PLC control equipment, ensuring high-quality output for sheet metal parts. The roll forming process is ideal for creating special shape frame panels with holes, making it a versatile solution for various construction applications. With its robust production line capabilities, the sheet metal roll forming machine serves as a vital tool for manufacturers looking to streamline their operations while maintaining accuracy in part creation. By utilizing this advanced machinery, businesses can enhance their productivity and reduce costs while delivering tailored solutions to meet their clients' needs.Our high-performance trapezoidal sheet roll forming plants from Roll Forming Technology are designed to manufacture high-quality trapezoidal sheets with virtually limitless profile geometries. Each component of our systems is constructed for maximum rigidity, enabling our customers to achieve production within the tightest tolerances. The precision engineering of our plants guarantees exceptional repetition accuracy, ensuring consistent quality in every batch. Additionally, the combination of high production speeds and short set-up times enhances overall plant efficiency, making the production process more streamlined. Equipped with state-of-the-art PLC automation and high-quality hydraulic components, our plants are optimized for performance and reliability, allowing businesses to meet their manufacturing demands effectively.
Trapezoidal Sheet Roll Forming Lines
The high-performance trapezoidal sheet roll forming plants from us Roll Forming Technology facilitate the manufacture of high-quality trapezoidal sheets. There are almost no limits with regard to the profile geometries. All components of the high-performance systems are constructed in such a way that they are highly rigid. This allows our customers to run production within the lowest tolerances. In addition, the high-precision design of our plants ensures excellent repetition accuracy. Furthermore, the high production speed in combination with short set-up times ensures optimum plant efficiency. Our plants are also equipped with the latest PLC automation and high-quality hydraulic components. This guarantees that everyday production runs smoothly in the long term.
Areas of application
Trapezoidal sheet roll forming plants from us Roll Forming Technology are available for the following applications:
Single or double-shell trapezoidal facings for roof and wall covering
Trapezoidal sheets with anti-condensation fleece
Corrugated sheets for roof and wall cladding
Depending on the layout of the plant, the following primary materials can be used:
Galvanized sheet steel with a thickness of at least 0.4 millimetres
Aluminium with a thickness of at least 0.3 millimetres
Coated and painted primary material
High-strength primary material grades
Primary materials with and without protective foil
Highlights and features
Trapezoidal sheet roll forming plants from us Roll Forming Technology come equipped with the following features right from the factory:
Coil loading
Strip preparation
Strip connection with automatic gluing machines
Roll forming section for edge and surface profiling, surface lining, surface structuring
Flying or static separation
Stacker
Packer
Get the most out of your production! We offer real distinctive features:
High precision
Excellent repetition accuracy
Very high production speed
Shortest set-up times
Optimum plant efficiency
Tailor-made customer solutions
Trapezoidal Sheet Roll Forming Lines
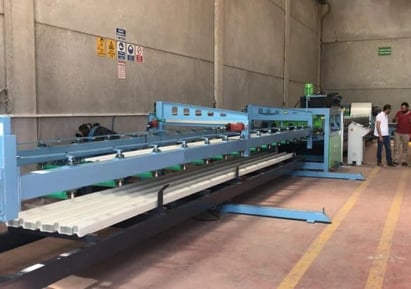
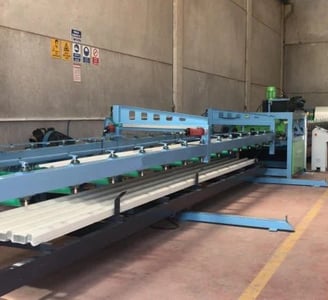
Sandwich Panel Roll Forming Lines
Roll Forming Technology provides the right machine technology for surface and edge profiling in the continuous production of high-quality sandwich composite elements with a core of polyurethane or mineral wool and metal facings. This fits perfectly into the existing plant concept of the continuous sandwich panel lines from us . We are one of only a few companies worldwide with overall system competence and can therefore offer its customers complete solutions for everything ranging from sheet metal de coiling to packaging the finished stack. A distinctive characteristic of the high-performance sandwich panel roll forming plants from us Roll Forming Technology is that they are extremely rigid. This gives our customers the security of being able to work with the lowest tolerances. The plants are highly precise and have an excellent level of repetition accuracy. The high production speed in combination with very short set-up times ensures optimum plant efficiency. State-of-the-art control technology and high-quality hydraulic components ensure that everyday production runs smoothly.
Areas of application
Sandwich panel roll forming plants from us Roll Forming Technology are available for the following applications:
· Insulation roof panels
· Insulation thermal walls
· Insulation cold storage elements
· Insulated industrial sectional doors
· Garage sectional doors (with and without finger protection)
· Sandwich fire safety elements
Depending on the layout of the plant, the following primary materials can be used:
· Galvanized sheet steel with a thickness of at least 0.4 millimetres
· Aluminium with a thickness of at least 0.3 millimetres
· Coated and painted primary material
· High-strength primary material grades
· Primary materials with and without protective foil
Highlights and features
Sandwich panel roll forming plants from us Roll Forming Technology come equipped with the following features right from the factory:
· Coil loading
· Strip preparation
· Strip connection with automatic gluing machines
· Profiling area for edge and surface profiling, surface lining, surface structuring
· Integration of punching and forming processes, for example panel embossment for sectional doors
Get the most out of your production! We offer real distinctive features:
· High precision
· Excellent repetition accuracy
· Very high production speed
· Shortest set-up times
· Optimum plant efficiency
· Tailor-made customer solutions
Sandwich Panel Roll Forming Lines
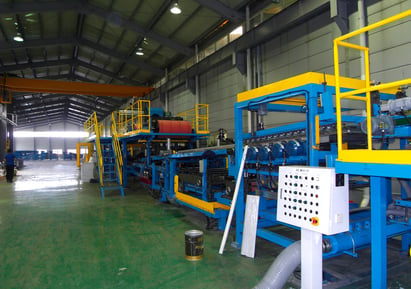
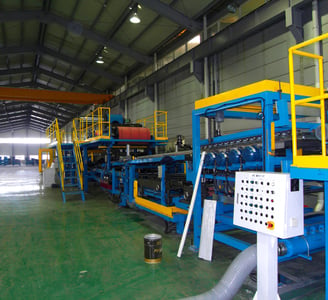
Sheet Metal Roll Forming Machine
Sheet Metal Roll Forming Machine for customized metal frame with accurate measurement and easy operating, low price and durable system, PLC control equipment for production Sheet metal parts. Sheet Metal Roll Forming Machine process solution widely used in construction
Roll forming machine for production Sheet metal parts.
Special shape frame panel with hole by Roll Forming Process
Sheet Metal Roll Forming Machine parts production line process
Un coiler straightener 2 in 1 →Servo feeder→ Guide device → Hydraulic Punch → roll forming machine →shear device (including knife)→ finished product rack
Customized metal parts production equipment machine list
2 in 1 Un coiler straightener
1, Type Manual Expansion
2, Parameter
1) Passive discharge
2) Coil weight:< 2T
3) Coil inner D.:φ450mm-φ530mm
4) Max. Width.200mm
5) Thickness .0.4-1.6mm
6) Straightener Roller :7 pcs
7) Power.1.5kw
Servo Feeder
3.1 Max. feeding width:200mm
3.2 Feeding thickess: 0.4-1.6mm
3.3 Motor , 0.85KW(Yaskawa)
Hydraulic Hole Punching System
3.1 Function:Hydraulic punch breach
3.2 Structure: set the length, automatic length measurement, automatic positioning reaches the set distance stop action , hydraulic cylinder driven punching die, stamping automatic shutdown.
3.3 Hydraulic system working pressure:16MPa
3.4 Hydraulic station:15KW( Hydraulic punch hole/shear use same station)
Main Forming machines (for panel width 36mm)
Forming Roller:14 stations,and add Rub-roll, To make sure the surface profile no scratches.
Side Panel:T.18mm ,A3 steel Heavy duty 。
Rolling speeding: 2-8 m/min。
Roller material:#45,overall quenching, hardness HRC56-62 ℃.
Motor power:5.5KW。
Main Roller :¢65mm,45 #。
Equipment base: 45 # H type using welded steel plate.
Transmission: chain drive.
Security: across the board with emergency stop buttons, easy to handle emergencies, to ensure that equipment and operator safety. And other gear in the chain and the staff could easily lead to injury transmission section covered with protective cover, to ensure the safety of workers.
Flat Collect Rack
Electrical control system
The entire line imported PLC control, LCD touch screen, man-machine interface. People interact with the PLC. Operator setting the program to run automatically (programmable control) and control process monitoring, production line operator control and modify the control parameters, and real-time monitoring the equipment status & parameters and fault indication. Workpiece length digital setting, adjustable length can be adjustable as well. Real-time monitoring of equipment operating status and fault indication.
Operation manual / automatic two styles. With manual and automatic switching function: In the manual mode, can be stand-alone operation, easy maintenance; In automatic mode, carry out full production run, in order to start; across the board with emergency stop buttons, easy to handle emergencies, to ensure that equipment and operating personnel Safety.
Machinery main components of the brand:
PLC control system: Siemens
Inverter: Taiwan
Encoder: Omron
Touch screen: Siemens
Devices completed door industry production line
No. Machine name QTY REMARK
1 Un coiler straightener 1
2 Servo Feeder 1
3 Hydraulic machine 1 With mould
4 Guide device 1
5 Forming machine 1
6 Hydraulic machine 1 With mould (2 sets)
7 Follow Shear 1 Including knife
8 Collect rack 1
9 Control system 1
Metal parts production machine accessories
No. Name manufacturer
1 Motor & Reducer Domestic
2 The main key bearing Domestic
3 Inverter
4 PLC Systems Siemens
5 Low-voltage electrical Schneider
6 Encoder Omron
7 touch screen Siemens
8 Hydraulic system Domestic
Product Features
Guarantee of Quality
Guarantee Door Industry roll forming line design accordance with clients required drawing, machine is brand new. Specification and performance as stipulated in drawing and operation with good smooth. Formed metal parts can be fix well with installation parts.
Door Metal Panel Production Equipment Advantage
1, Rack shelf production line for producing light storage shelves, medium storage shelves, heavy storage shelves.
2, PLC control system, automatically and easy handle.
3, Good quality roller with quench process, hardness reach HRC58-62 ℃.
4,Tracking cutting system with Cr12 Cutting blade.
Model and Meaning
Equipment For Production Door Industry Metal Parts.
Door industry metal panel fabrication machine manufacturer fully providing technology supports both within and after the warranty period, The machine is the special forming equipment for producing door industry. Door frame panel roll forming machine adopts the cold forming, cold punching, automatic stack, industrial automation controlling system and precision machining technology, therefore is can run full automatically, including un coiler straightener, feeder, roll forming, cutting and stacking. Supply door using metal parts testing raw materials with good quality, quick delivery and reasonable price
Technical Parameters
Steel door panel roll forming machine for door industry construction
Technical parameters
No. ITEM PARAMETER REMARK
1 MATERIAL Type Cold-rolled strip steel, galvanized sheet
T.(mm) 0.8-1.2mm
Material strength G300 MPA
2 Forming speed (m/min) 3-8m Including hole
3 Forming main power (KW) 5.5KW
4 Hydraulic power (KW) 15KW
5 Total Power 20.5 KW
6 Voltage AC380V,50Hz,3Phase Customized
Sheet Metal Roll Forming Machine
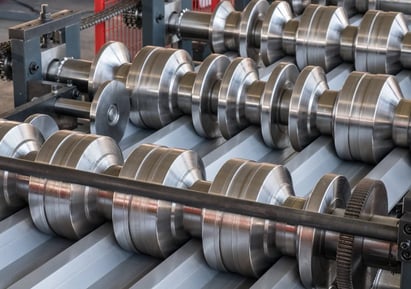
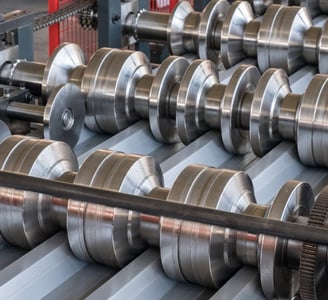