Extrusion Sheet
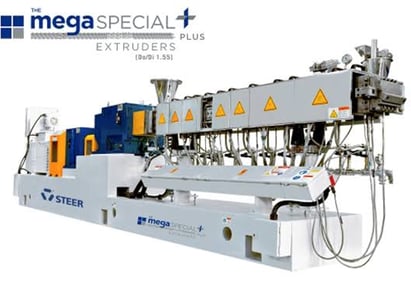
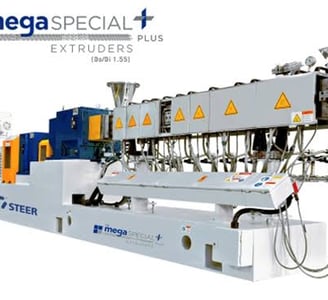
The PET/PLA environmental sheet extrusion line is a cutting-edge solution designed for the production of both PET and PLA sheets, significantly minimizing energy consumption during pre-crystallization and drying processes. This versatile line is particularly well-suited for the fabrication of biodegradable PLA materials and starch-based degradable products, aligning with eco-friendly manufacturing practices. The system comprises essential components including a flat twin extruder, a screen changer, a metering pump, a mold, three rollers, a cooling bracket, as well as traction and winding mechanisms. Notably, the extruder utilizes an innovative co-rotating flat double design, which enhances efficiency while ensuring low energy usage, thereby making it a sustainable choice for industries focused on reducing their environmental footprint. This technology promotes the production of secondary materials, reflecting a commitment to sustainability and resource conservation.
The multi-component feeding device offers precise control over the proportions of new and recycled materials, as well as color masterbatch, ensuring that the produced sheets are perfectly suited for applications in blister printing and packaging. Incorporating a Siemens electrical system, the machine provides user-friendly operation, high automation levels, and significant cost savings. Additionally, the barrel features a double vacuum exhaust system, effectively removing water vapor for optimal production quality. The extruder is equipped with a melt metering pump that guarantees quantitative and stable output, alongside a closed-loop automatic control system for pressure and speed settings. Overall, the entire machine utilizes PLC control to enable seamless automation of parameter adjustments, data calculations, and feedback analysis, enhancing efficiency and performance throughout the production process.
PET Sheet Production Line
Developed by our company has a compact structure, ensuring efficiency and space-saving benefits. With a large and stable output, this production line is capable of meeting high demands while maintaining consistency in quality. The technical specifications are carefully designed to ensure optimal performance, providing a reliable and efficient production process. One of the key features of this production line is its high level of automation, which reduces the need for manual intervention and ensures precision in the manufacturing process. This automation not only improves productivity but also enhances the overall quality of the PET sheet produced. Furthermore, our production line is designed to produce sheets using 100% recycled PET materials.
This sustainable approach not only reduces waste but also contributes to environmental conservation efforts. The PET sheets produced can be thermoformed to create a variety of packaging products, showcasing their versatility and adaptability. These PET sheets have excellent gas barrier properties, making them ideal for packaging applications where preserving freshness is crucial. Additionally, the sheets are free from other additives, ensuring purity and hygiene in the packaging process. With good toughness and ductility, these sheets can withstand handling and transportation without compromising their integrity. Moreover, the PET sheets exhibit excellent recycling performance, further enhancing their sustainability and eco-friendly credentials. Overall, our PET sheet production line offers a comprehensive solution for producing high-quality sheets with outstanding properties, catering to various packaging needs effectively and efficiently.
PET sheet is a versatile material that finds applications in various industries such as medicine, food, electrical appliances, toys, and printing. In the medical field, PET sheets are commonly used for packaging pharmaceutical products due to their excellent barrier properties that protect the contents from moisture, oxygen, and other contaminants. In the food industry, PET sheets are used for packaging fresh produce, snacks, and beverages as they are safe for food contact and resistant to grease and oil. Moreover, PET sheets are also widely utilized in the manufacturing of electrical appliances and toys due to their durability and flexibility. In the printing industry, PET sheets are often used for creating labels, posters, and other promotional materials due to their smooth surface and excellent printability. Overall, the versatility and benefits of PET sheets make them an essential material in various industries.
• Extruder: Parallel twin screw extruder has high output, good plasticizing, vacuum exhaust improves product quality, and can process a variety of plastics.
• Screen exchanger: Our company uses the column type screen changer, which is an important filter equipment, the equipment is simple in structure, easy to operate, and effectively improve the production efficiency. It is characterized by the use of a large area of the filter screen, which can effectively filter out more impurities and particles.
• Gear pump: The melt metering pump made of heat -resistant alloy steel is characterized by maintaining a constant flow unrelated to the discharge pressure to ensure the stable pressure and flow of solution.
• Mold: It is made of heat-resistant alloy steel with a highly active throttling device, so that the material flow is evenly distributed in the die.
• Haul off unit: The cooling roller uses a large diameter, low temperature, S-shaped discharge, which increases the forced cooling area and shortens the length of the production line. The traction adopts the traction of rubber and steel rollers, which not only ensures the friction required for traction but also ensures the quality of the sheet surface.
• Double station winding: Two torque motors are used as the power, and the inflating shaft is a scroll, respectively for winding.
• Sheet width: ≤1500mm,thickness:0.2-1.5mm
Parameter
Type of extrusion line single screw sheet PET extrusion line twin screw venting PET sheet extrusion line PET sheet planetary multi-screw exhaust extrusion line
Method of dealing material Crystallization and drying Free from crystallization and drying Free from crystallization and drying
Extrusion type Mono extruded or co-extruded
Finished Product Single layer, double-layer or multi-layer PET sheet
Raw material PET vergin ,flake and crushed material
Net width 600mm-1220mm and more
Thickness range 0.15mm-2mm and more
Capacity 200kg/h-1200kg/h and more
Application Food and fruit packing,Medical supplies packaging,cosmetics packaging,electronic products,decoration and conservation of buildings and more
Application
Because of its excellent physical properties and chemical stability, PET sheet, processed using the cutting-edge PET Sheet Extrusion Line, is widely used in packaging, electronics, construction, and other fields. In the packaging industry, our PET sheet, produced with the PET Sheet Extrusion Line, offers high transparency and flatness, ensuring impeccable packaging material appearance. Its outstanding physical properties, thanks to the advanced extrusion process, guarantee the durability and protection of packaging materials, making it ideal for food packaging, medical supplies packaging, cosmetic packaging, and more. In the electronics industry, PET sheets, manufactured with precision using our PET Sheet Extrusion Line, play a pivotal role in the production of electronic products like screens and solar panels. Their high transparency and flatness, achieved through cutting-edge extrusion technology, ensure optimal display quality and light transmission for electronic products. In the construction industry, PET sheets, crafted with expertise on our PET Sheet Extrusion Line, find application in decorating and safeguarding buildings, including glass curtain walls and sound insulation walls, offering both functionality and aesthetics
PET Sheet Production Line
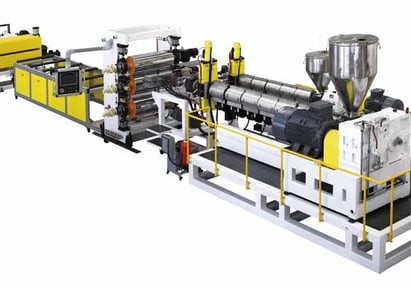
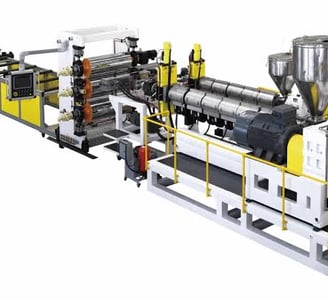
Twin Screw Dryer-Free Vented PET Sheet Extrusion Line
1.At present, various exhaust extruders are evacuated after the polymer is melted. Multiple exhaust ports can be set according to the needs, which can always reduce the water content and small molecular components to the desired level. This kind of design is suitable for processing those materials that are not sensitive to water (such as PS, ABS, etc.), but it is not ideal for PET.
Because water has a severe degradation effect on the PET melt, the PET exhaust extruder must have solid exhaust capability. As much water vapor as possible is drawn out of the barrel before the PET is melted, which is significantly different from the conventional design concept of exhaust extruder.
2.The PET melt exhaust must complete in the shortest possible time. Considering that the PET melt is most hydrolyzed in the first 5 minutes, the exhaust operation should not exceed 1 minute.
The longer the exhaust time of conventional materials, the better the exhaust effect, but this does not apply to PET.
3.While taking into account the output, the solid section of the PET exhaust extruder should be as long as possible. The screw groove should be as shallow as possible, which is conducive to the uniform heating of the PET slice and makes more water evaporate from the slice.
4.Under the premise of no feeding, the screw groove of the melt exhaust section should be as shallow as possible to reduce the diffusion path of bubbles in the melt.
At the same time, the viscosity of the PET melt is relatively small, and the bubbles located in it are easier to diffuse, which provides the possibility of rapid de volatilization in a short time.
5.The melting section and melt conveying area of the screw are designed with flexible threads to provide gentle shear for PET melting and giving, realize low-temperature extrusion, and avoid thermal degradation of PET.
According to the above design principles of PET exhaust extruder, independently developed the PET single-screw exhaust extruder, which is dedicated to PET drying-free processing. The production test achieves the expected effect: the final sheet viscosity is reduced between 0.03 -0.05 dl/g, and the output can reach 500kg/h. Furthermore, compared with the conventional dry sheet production line, the electricity cost is reduced by 35%-50% on the original basis.
Performance & Advantages
develops the parallel twin screw extrusion line for PET sheet, this line equipped with degassing system, and no need drying and crystallizing unit. The extrusion line has the properties of low energy consumption, a simple production process, and easy maintenance. The segmented screw structure can reduce the viscosity loss of PET resin, the symmetrical and thin-wall calendar roller heighten the cooling effect and improve the capacity and sheet quality. Multi components dosing feeder can control the percentage of virgin material, recycling material, and master batch precisely, the sheet is widely used for the thermoforming packaging industry.
Technical Parameter
Model
Main motor power(kw)
Products thickness(mm)
Extruder model
Max extrusion Capacity(kg/h)
Multi layer
75&36/40-1000
0.15-1.5
132/15
500
Single layer
75/40-1000
0.15-1.5
321
450
Highly-efficient
95&65/44-1500
0.15-1.5
250/75
800-1000
Twin Screw Dryer-Free Vented PET Sheet Extrusion Line
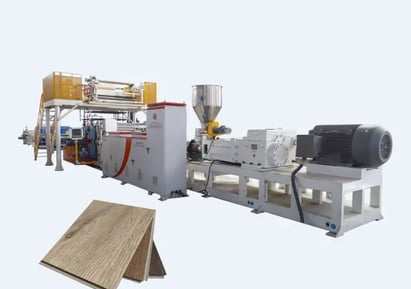
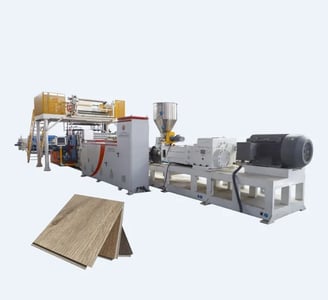
PP, PS Multi-Layer Co-Extruded Sheet Production Line
PP, PS multi-layer co-extruded sheet production line using multiple extruder extrusion technology to produce multi-layer PP, PS and other sheets, to meet the needs of different uses of sheet, widely used in thermoforming, printing, hardware packaging and so on. Single screw sheet extruder adopts new screw structure, feed stability, melt mixing evenly, to ensure low melting temperature and high output, extruder adopts motor and reducer direct transmission, improve transmission efficiency, reduce speed fluctuations, improve extrusion stability. Equipped with melt metering pump, precision multi-layer distributor, using flow ratio and blade clearance ratio double adjustment technology, more uniform stratification. The machine adopts PLC control to realize automatic control of parameter setting, data calculation, feedback, alarm and other functions. The width of the sheet produced in this production line is 600-1220mm, the thickness range is 0.15-3mm, and the output is 200-1000kg/h, and there are differences in the output of different models.
Parameter
Type of extrusion line single screw venting or not PP/PS sheet extrusion line twin screw venting PP/PS sheet extrusion line
Extrusion type Mono extruded or co-extruded
Finished Product Single layer, double-layer or multi-layer PET sheet
Raw material PP/PS vergin ,flake and crushed material
Net width 600mm-1220mm and more
Thickness range 0.15mm-2mm and more
Capacity 200kg/h-1200kg/h and more
Application Food and fruit packing,Stationery pieces,Printing, hardware packing,electronic tray,flocking,clothing,decorative pieces,high barrier packing and more
Type of extrusion line PP/PS single-extruder extrusion line PP/PS double-extruder Co-extrusion line PP/PS multi-extruder co-extrusion multi-layer sheet extrusion line
Can produce single layer sheet Can produce double-layer or three-layer sheet Can produce multi-layer sheet, which usually has 5 layers, 7 layers or 9 layers
Type of extruder Single screw extruder or parallel twin screw extruder
Width of Products 600mm-1220mm
Thickness of Products 0.15mm-3mm
Output 200kg/h-1000kg/h
Application
Developed PP, PS sheet production line, for the production of multi-layer composite environmental protection sheet, the material is mainly used for blister molding all kinds of food containers and packaging, such as: tray, noodle bowl, lunch box, cake box, fruit plate and so on. The equipment can effectively use the proportion of stone powder, not only reduce the raw material cost of sheet, but also improve the degradability of sheet and ensure the comprehensive physical properties and subsequent processability of sheet.
PP, PS Multi-Layer Co-Extruded Sheet Production Line
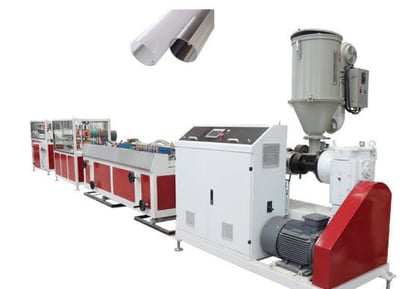
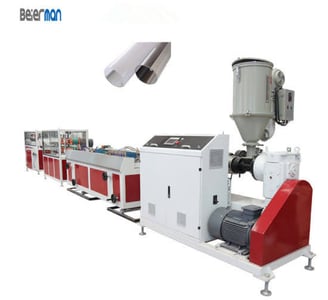
c
PET Stretch Film Extrusion Line equipment is mainly composed of: extruder, die, casting, longitudinal stretching, transverse stretching, automatic winding, control system. Relying on the advanced overall design of company.
PET stretch film extrusion line Product Flows
Extruder —- Screen changer —– Melt pump —– T-die —— Calender —– Cooling bracket —– Haul-off—- Winder
Feature of PET stretch film
Plastic Extruder– According to the requirements of the application field for the special properties of the film, the film not only has the excellent physical and mechanical properties of polyester film, but also has excellent optical properties, good transparency, low haze, high gloss, heat Good stability, low thermal shrinkage, smooth surface, good peel ability, light aging resistance, etc., and OPET thin mould also has the characteristics of high unidirectional tensile strength and unidirectional orientation, which is suitable for special fields. Polyester film shrink film is a new type of packaging material, which is easy to recycle, tasteless, and has good mechanical properties, especially in line with environmental protection requirements.
Features of PET Stretch Film Extrusion Line Equipment
The preheating roll, stretching roll, annealing roll and cooling roll of China GWELL PET Stretch Film Extrusion Line are all driven by servo motors, and the speed control precision is higher.
The spacing of the stretching rollers is adjustable, which can achieve “zero spacing” stretching and reduce the necking effect.
Single-point and double-point stretching are optional, and the stretching ratio is continuously adjustable.
Applicable to PET/PP/PE/PA and other materials, the stretching ratio is in the range of 1-10 times, various stretching forms, multi-point stretching structure, and the line speed can reach 200m/min.
Oil/electric heating optional: oil heating temperature is uniform, while electric heating can obtain higher process temperature.
The side plate is provided with a labyrinth film guiding groove, which is convenient for manual film guiding.
Aluminium alloy integral side plate frame, light weight, high strength, corrosion resistance and long service life.
GWELL as a plastic extruder manufacturer high-performance PLC with 12-inch touch screen, high control precision and easy operation. The two-point stretching process can greatly improve film properties, such as film barrier properties, stiffness, flatness, tensile strength, and porosity.
Feature of PET stretch film extrusion line
· Single screw or twin-screw extruder structure can be used to produce cast films with single-layer, double-layer, or three-layer co-extrusion structure.
· Plastic Extruder Supplier – We adopts a specially designed extrusion process according to the particularity of PET materials or the characteristics of modified PET materials, after dehumidification and drying-automatic metering and feeding-extruder plasticization-T-type casting die-processing produce high-quality products.
· Forming and setting device-automatic post-measuring system-preheating stretching and setting device-surface treatment device-edge trimming and edge material treatment device-automatic winding device or films with special orientation properties, which can be used in various fields.
· PET Stretch Film Extrusion Line specially designed longitudinal stretching roller.
· The power transmission and control system adopts international famous brands.
· The control system adopts precise PLC program control.
· High wire drawing precision, fast speed and stable operation of the whole machine.
PET Stretch Film Extrusion Line Product Advantages
· Easy to operate, long life and energy saving
· Stable and reasonable extrusion
· High-quality T-die with excellent film uniformity and stability
· Enhanced cooling system
· (using a primary cooling roll with a diameter of 720 mm and a secondary cooling roll with a diameter of 370 mm)
· PET Stretch Film Extrusion Line advanced swing (swing) system
· The highest winding speed in the same type of stretch film machine (up to 200 m/min)
· High production capacity: up to 350 kgs/h at film thickness of 23 microns and 150 m/min
· Optional automatic thickness gauge
· Excellent stretch film roll quality, suitable for manual rolls and stretch rolls
Parameter
Type of extrusion line
single screw PET film extrusion line
twin screw PET film sheet extrusion line
Method of dealing material
Crystallization and drying
Free from crystallization and drying
Extrusion type
Mono extruded or co-extruded
Finished Product
Single layer, double-layer or multi-layer PET sheet
Raw material
PET vergin ,flake and crushed material
Net width
1000mm-1500mm and more
Thickness range
0.02-0.1mm and more
Capacity
200kg/h-500kg/h and more
Application
Medical packing, Electronic components packing, Food packing and more
Application
Tinplate composite film: after compounding with tinplate, it can be used as a variety of food and beverage packaging;
Packaging of electronic components: it can be made into anti-static packaging bags to package and shield sensitive electronic components, circuit boards, communication equipment and electronic products;
Pharmaceutical packaging: mainly used for pharmaceutical tablet packaging;
PET Stretch Film Extrusion Line
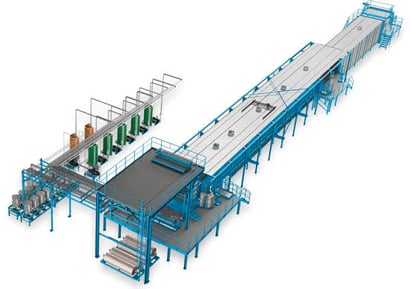
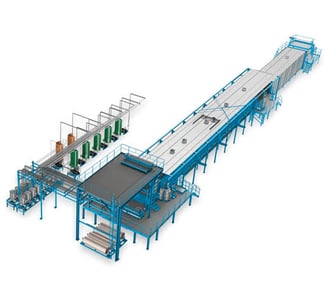
PVC Rigid Sheet Extrusion Line
PVC Rigid Sheet Extrusion Line and PVC Soft Sheet Extrusion Line, adopts conical twin-screw extruder according to the characteristics of transparent PVC material, combined with the hopper, screen changer, melt pump enables the product to achieve highly transparent product, and the product will not turn to be hardened in the cold temperature of 30 degrees below zero. Auxiliary design based on the principle of the multi-function production line, in the case of no need to make any changes to the equipment, can produce different patterns of PVC rigid sheet.
The PVC sheet is one of the largest plastic products in the world. It is cheap and widely used. The polyvinyl chloride resin is white or light yellow powder. Different additives can be added according to different uses, and PVC plastics can exhibit different physical and mechanical properties. Adding an appropriate amount of plasticizer to polyvinyl chloride resin can make a variety of hard, soft and transparent products.
Plastic Extruder manufacturer ,PVC rigid sheet is also called decorative film, adhesive film, used in building materials, packaging, medicine and many other industries. The building materials industry accounts for the largest proportion, at 60%, followed by the packaging industry, and several other small-scale application industries.
PVC rigid sheet has the characteristics of flame retardant self-extinguishing, high quality, high transparency, good surface gloss, less crystal point, small water pattern, strong impact resistance, and easy moulding, and is widely used in various tools, toys, Blister, folding box, packaging, etc. in electronics, food, medicine, clothing and other industries.
PVC Rigid Sheet Extrusion Line
Advantages
• The PVC Rigid Sheet Extrusion Line has a “one-click acceleration” function, which allows the equipment to achieve low-speed adjustment and high-speed production, and greatly reduces the waste of raw materials caused by the machine adjustment process;
• Intelligent advanced control system, rapid network transmission speed, greatly reduce the transmission error of information, and make the PVC Rigid Sheet Extrusion Line more stable in speed, pressure and material conveying;
• The winding part of the PVC Rigid Sheet Extrusion Line adopts servo control, which is more accurate, and has the function of speed synchronization with the whole machine, which makes the winding more convenient and simple, and safer;
• Through centralized control, PVC Rigid Sheet Extrusion Line can browse all the information of the equipment on one screen, such as current, pressure, speed, temperature, vacuum pressure, etc., making the operation easier;
• PVC Rigid Sheet Extrusion Line adopts international Siemens variable frequency servo control and Ethernet conduction technology control to achieve high efficiency, high precision, high stability and high safety. Quickly locate errors in the event of equipment failure and enable remote maintenance, channel level diagnostics and error analysis via HMI, greatly reducing commissioning and production downtime. The highly digital system makes debugging easier and more convenient to maintain;
• complete after-sales service system, from equipment installation and commissioning to the production and manufacture of high-quality products, and provides lifelong technical support so that customers have no worries.
PVC Rigid Sheet Extrusion Line Process Flows
PVC rigid sheet machine —- Screen changer —- Melt pump —- T-die —- Calender —- Cooling bracket —- Haul-off —-Winder
Feature
1. Screw with a special mixing function and high plasticizing capacity design.
2.The screen changer can filter the no-need material, and the melt pump can provide
stable pressure to reach the objective of uniform thickness.
3.hanger die head adopts a special BM design to make plate thickness adjustment more accurate.
4.temperature control ±1C can accurately control the plasticizing process and product thickness and flatness.
5.A three-roll calendar adopts a 45-degree tilt type, which can be raised or lowered freely.
6.plate thickness control adopts screw adjustment and press wheel two-way adjustment to control plate thickness.
7.The main models of the PVC rigid sheet extrusion line produced include conical twin-screw 80mm extruder and 92mm extruder. The capacity of the 80 models can reach 350kg/h and the capacity of the 92 models can reach 600kg/h.
Parameter
Type of extrusion line Transparent PVC rigid sheet/plate extrusion line
Extruder type Conical twin-screw extruder 65/132, 80/156, 92/188
Raw material PVC powder
Net Width 600mm-1500mm and more
Thickness range 0.2mm-3mm and more
Capacity 200kg/h-1200kg/h and more
Application Medical packaging, Electronics packaging of products, Spare parts, Toys, Gifts, Cosmetics and etc.
Application
PVC rigid sheet extrusion line is flexible in processing, transparent, environmentally friendly.
Feature of application: can be used in cold and heat insulation, save energy, windproof, soundproof, table pad, daylighting, industrial dumping, safety warning, protect the surface, these applications used in refrigeration, foodstuff, printing, weaving, electrics, instrument, medicine, storage. It has a good effect on insulation for electricity and harmful light.
General Application: Food, Medicine, Electronics packaging of products, Spare parts, Toys, Gifts, Cosmetics, and other products, And the production of various stationery, Shoe samples, Billboards, Magnetic cards, and etc.
PVC Rigid Sheet Extrusion Line
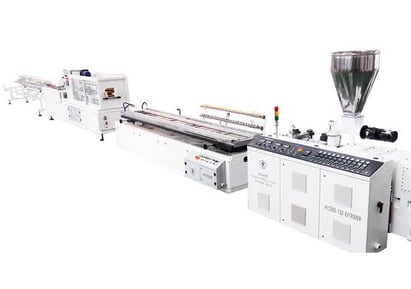
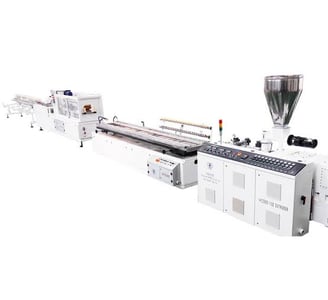
PE Breathable Film Extrusion Line
Plastic Extruder manufacturer, PE ventilated film extrusion line is composed of: raw material automatic feeding system, twin-screw extruder mixing host, screw pump, extrusion molding system, stretch forming system, cooling and winding system.
PE breathable film extrusion production line can continuously complete the processes of raw material transportation, mixing, dispersion, casting extrusion, stretching and shaping, and winding.
PE breathable film extrusion line Advantages
1. Plastic Extruder manufacturer, PE breathable film extrusion line is a continuous production process with high production efficiency. The complete production process from raw materials to breathable films is completed at one time.
2. The automatic raw material supply system completes the storage and transportation of each raw material, and feeds it into the twin-screw extruder accurately in proportion. High degree of automation, no dust pollution and other environmental protection issues in the production process.
3. The twin-screw mixing extruder adopts a high-torque transmission box and has high production efficiency. The gap between the barrel and the screw is small, and the dimensional accuracy is high. The inorganic filler is dispersed and distributed evenly in PE resin, so that the micro pores in the film are small and evenly distributed.
4. The extrusion moulding system adopts precise moulds and rollers, and the cast film is stable in width and uniform in thickness.
5. The stretching and setting system consists of a heating device, a stretching device and a cooling device, which is stable in operation and uniform in tensile ratio.
PE breathable film is a new type of material in the world. It has the characteristics of breathability and no leakage and is widely used in many fields of life: sanitary napkins, diapers, medical surgical gowns and breathing paper in the construction industry, and other packaging products.
The breathable film contains a large proportion (50~ 60%) of ultra-fine density inorganic filler. After being treated by casting and stretching processes, countless micro pores are formed and evenly distributed. The micro pores have a pore size of 0.1 to 10 microns and form a passage through which gas passes, and at the same time only permeates gas without leaking liquid.
PE breathable film extrusion line Process Flows
Extruder —- Screen changer —– Melt pump —– T-die —— Calender —– Thickness Scanner —-Cooling Bracket —-Cutting Knife —- Haul-off —-Winder
PE breathable membrane is a new type of breathable and impermeable material in the world. Its main component is polyethylene. To be precise, it is a polymer material synthesized from polyethylene. Because of its soft skin affinity, high tensile strength, and good moisture permeability, it is widely used in various fields of life, such as women’s sanitary napkins, pad bottom film, baby diapers, diapers, etc. At the same time, PE breathable film is also the most important material for mask medical packaging.
PE breathable membrane is also called breathing membrane. At present, PE breathable membrane is basically used in diapers (including baby and adult diapers), sanitary napkins, and Mommy napkins, with an air permeability of about 2000-2500.
PE breathable membrane features:
1. Good air permeability
It can pass through gas but not water, so it can not only effectively isolate water, but also discharge heat and moisture. It can be used as waterproof material with moisture resistance.
2. Skin-friendly and soft
PE breathable film has an excellent hand feel, and the product is soft and comfortable. Compared with an ordinary non breathable membrane, it is not easy to cause eczema and other red ass problems on baby’s delicate skin.
3. Excellent tensile and extensibility
It can appropriately improve the air convection in the user’s small environment and is conducive to skin breathing.
4. Green environmental protection
Due to the characteristics of its raw materials, PE breathable membrane is a new environmental protection material without damaging the environment.
5. Good chemical resistance, not easy to corrosion
Principle of PE breathable membrane:
Plastic Extruder manufacturer. The PE breathable film it produces is made of LDPE/LLDPE polyethylene resin carrier and about 50% of special calcium carbonate blended, extruded, and directionally stretched according to a certain proportion.
As polyethylene resin is a thermoplastic material, it can be stretched and crystallized under certain conditions. During stretching, the interface between polymer and calcium carbonate particles peels, and interconnected winding pores or channels are formed around calcium carbonate particles. It is these pores and channels that give the air permeability (wet) function of the film, so as to communicate the environment on both sides of the film.
Parameter
Extruder Type Single screw extruder Single screw extruder Single screw extruder Single screw extruder
Raw material LDPE, LLDPE
Net width 1500mm 2200mm 2800mm 3200mm
Thickness range 0.02mm-1mm
weight of product 15-50g/m2
output 200kg/h 400kg/h 550kg/h 650kg/h
Line speed 200m/min
Application
1. Daily necessities: raincoat, suit coat, eye mask, all kinds of the tablecloth, shower cap, shower curtain, water bag, tablecloth, etc.
2. Sanitary products: diapers, sanitary napkins, medical-surgical clothes, special medical packaging, and food packaging.
3. Packaging supplies: computer, air conditioner, electrical dust cover, car cover, cosmetics flexible packaging, shopping bags, gift bags, folders, and archives.
4. Packaging bags: fashion packaging, cosmetic bags, high-grade stationery, shoulder hugging saliva, wardrobe, fishing bags, handbags, bags, and other product applications.
PE Breathable Film Extrusion Line
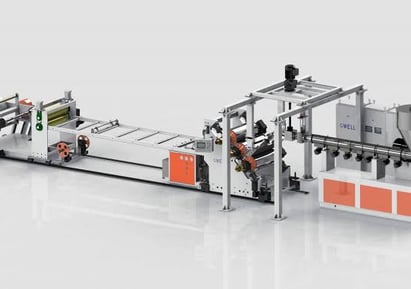
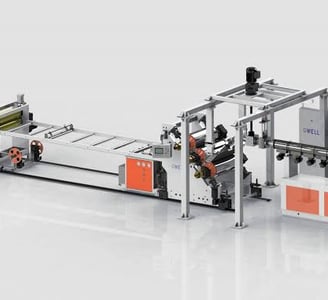