Extrusion Pipe
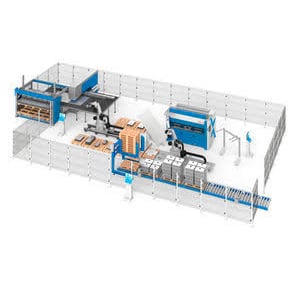
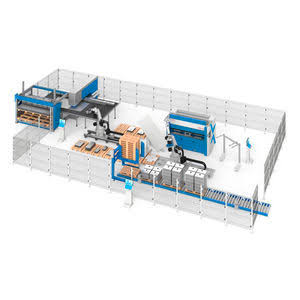
Introducing our cutting-edge tube extrusion machine, meticulously engineered to produce high-quality single-lumen PVC flexible tubes. With a minimum diameter of 1.6mm, these versatile tubes are ideal for various applications in the medical and industrial sectors, including specialized components for lighters. Our state-of-the-art equipment is designed to accommodate a wide range of materials, ensuring exceptional performance and quality tailored to your production requirements. Whether you need to extrude PVC soft hoses, PP/PE dip tubes, or PA tubing, our advanced machinery delivers precise and efficient solutions. We take pride in providing the perfect match for your specific needs, helping you achieve excellence in every aspect of your production process.
PPR Pipe Extrusion Machine
A PPR pipe extrusion machine is specialized equipment used for producing Polypropylene Random Copolymer (PP-R) pipes. These pipes are highly valued for their durability, resistance to high temperatures and pressure, and use in plumbing and heating systems.
Our machines can produce single-layer, double-layer, and even fiber-glass reinforced PPR pipes. Below is a detailed overview of each component of the PPR pipe extrusion machine, highlighting their functions and importance in the production process.
Applications:
• Plumbing Systems
• Heating Systems
• Industrial Piping
Key Components of PPR Pipe Extrusion Machine Line
If there is a need for multiple layers or enhancements, the line will be configured to increase accordingly.
Main Extruder
The main extruder of PPR pipe extrusion machine melts and homogenizes the PP-R pellets. It consists of a barrel, screw, and heaters. The rotating screw, driven by a powerful motor, pushes the pellets through the barrel, where they are gradually melted by the heat.
There are two versions, one with normal thermostat meter controlled heating. The other one is PLC system.
Vacuum Sizing Tank
Function: The vacuum sizing tank stabilizes the shape of the molten PP-R pipe by using a vacuum to pull it against the sizing sleeve. This process ensures that the pipe retains its correct dimensions as it cools and solidifies.
Details:
• Cooling System: Equipped with an efficient cooling system to rapidly solidify the pipe.
• Adjustable Spray Angle: Allows for precise control of the cooling process, enhancing dimensional stability
Cooling Tank
Function: The cooling tank further cools the pipe to ensure its structural integrity and dimensional accuracy. It usually follows the vacuum sizing tank in the production line.
Details:
• Length: Typically designed in segments to provide adequate cooling.
• Cooling Method: Uses water sprays or baths to evenly cool the pipe, preventing warping and ensuring uniform thickness
Haul-Off Unit
Function: The haul-off unit pulls the pipe through the extrusion line at a consistent speed, which is crucial for maintaining uniform diameter and wall thickness.
Details:
• Caterpillar Tracks: Multiple tracks driven by independent motors ensure smooth and even pulling.
• Speed Control: Precisely adjustable to match the extrusion speed and ensure product consistency
Cutter
Function: The cutter precisely cuts the extruded pipes to the required lengths. This unit is designed to make clean, accurate cuts without damaging the pipes.
Details:
• Type: Non-dust or planetary cutters are commonly used for their precision and efficiency.
• Operation: Often equipped with servo motors for enhanced control and adaptability to different pipe sizes
Common Pain Points and Solutions of PPR Pipe Extrusion Machine Line
Difficulty in Producing Multi-Layer and Reinforced Pipes
Producing complex multi-layer or fiber-glass reinforced pipes can be challenging with standard extrusion equipment.
Solutions
Our PPR extrusion machine is equipped with co-extrusion capabilities, allowing for the production of single-layer, double-layer, and reinforced pipes with precise control over each layer's properties
Compliance with Industry Standards
Ensuring the produced pipes meet various international standards such as ISO 15874 can be complex and requires specific configurations.
Solutions
Our PPR extrusion machines are customizable to meet different standards, ensuring compliance with ISO 15874 and other industry requirements. This includes precise control over dimensions and material properties
Consistency and Quality Control
Inconsistent product quality can lead to customer dissatisfaction and increased returns.
Solutions
Our PPR pipe extrusion machines feature advanced PLC control systems that ensure consistent extrusion parameters, and effective cooling and calibration processes that result in high-quality finished products
PPR Pipe Extrusion Machine
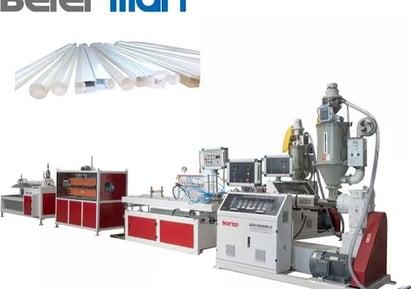
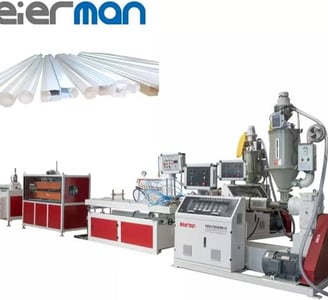
Nylon Tube Extrusion
A nylon extrusion machine, specifically designed for producing PA12 brake line tubing, is essential for manufacturing high-quality, durable, and reliable tubing used in automotive braking systems.
PA12 is favoured for its excellent mechanical properties, including high strength, flexibility, and resistance to heat and chemicals.
Below is a detailed overview of each component of the nylon extrusion machine line, highlighting their functions and importance in the production process.
• Automotive Brake Systems
• Hydraulic Systems
• Industrial Piping
Key Features of Our Nylon Extrusion Machine
The nylon extrusion machine line can proceed to either cutting or winding according to customer requirements after the haul-off machine.
Main Extruder
Function: The main extruder melts and homogenizes the PA12 pellets. It consists of a barrel, screw, and heaters. The rotating screw, driven by a powerful motor, pushes the pellets through the barrel, where they are gradually melted by the heat.
Details:
• Screw Design: Optimized for high output and efficient plasticization, ensuring the PA12 material is evenly melted and mixed.
• Temperature Control: Advanced temperature control systems maintain precise heat levels to ensure uniform melting, preventing degradation of the material and maintaining its properties.
• Energy Efficiency: The extruder is designed to minimize energy consumption while maximizing performance, reducing operational costs
Vacuum Cooling Water Tank
Function: The vacuum cooling water tank stabilizes the shape of the molten PA12 tubing by using a vacuum to pull it against the sizing sleeve. This process ensures that the tubing retains its correct dimensions as it cools and solidifies.
Details:
• Cooling System: Equipped with an efficient cooling system that rapidly solidifies the tubing, maintaining its precise dimensions.
• Adjustable Spray Angle: Allows for precise control of the cooling process, enhancing the stability and uniformity of the tubing.
Haul-Off Unit
Function: The haul-off machine pulls the tubing through the extrusion line at a consistent speed, which is crucial for maintaining uniform diameter and wall thickness.
Details:
• Flat Belts: Multiple flat belts driven by independent motors ensure smooth and even pulling, preventing deformation.
• Speed Control: Precisely adjustable to match the extrusion speed and ensure consistent product quality.
Nylon Tube Extrusion
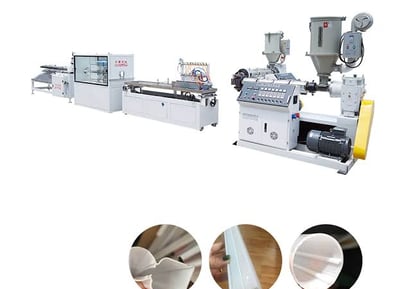
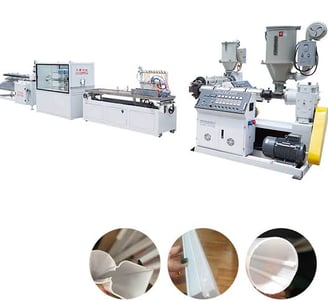
PVC tube extruders
Industry-leading PVC tube extruders are designed for stability, precision, and exceptional value. Our production equipment engineered explicitly for manufacturing single-chamber tubes from PVC or TPU materials.
These versatile tubes find applications across diverse sectors, including medical, industrial, and more, providing reliable solutions for various needs.
With precision capabilities reaching as low as 1.6mm in diameter
Key Features of Our PVC Extrusion Machines
Main Extruder
The main extruder in our PVC tubing extrusion line is a single screw extruder designed for processing PVC granulated material. This extruder is engineered to ensure consistent melt quality and optimal material flow, which is crucial for producing high-quality PVC tubing.
Water Cooling Tank
After extrusion, the hot PVC tubing is passed through a water cooling tank. This stage is critical for solidifying the tubing and maintaining its dimensional accuracy.
Combined Haul-Off and Servo Cutter
Our extrusion line includes a combined haul-off and servo cutter mounted on the same platform.
This integrated system ensures the tubing is pulled through the line at a consistent speed and cut to precise lengths without generating debris.
We offer the most cost-effective dip tube extruder machine. The production equipment is tailored for manufacturing dip tubes from PP or PE materials.
Our extruders are perfect for creating tubes compatible with pump or spray dispensers, ensuring seamless integration into various packaging bottles.
Alongside our dip tube extruders, we offer accompanying foam gasket production equipment, enhancing your production capabilities and ensuring a perfect fit for your packaging needs.
• Hygiene Products(perfume, hair-care, skincare, etc.)
• Pharmaceutical Products(sun protection, etc.)
• Industrial Products (cleansers, etc.)
PVC tube extruders
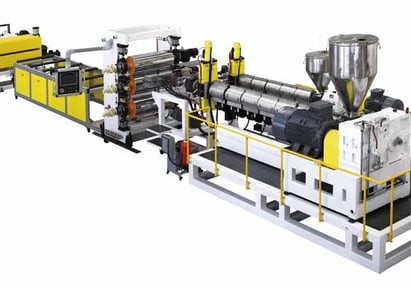
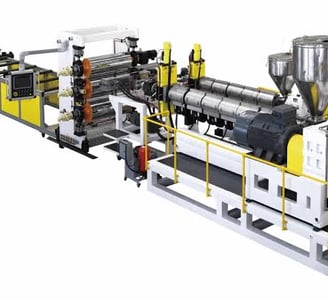