Process Mixers
Mixer And Dispersers
Mixers Encompasses Batch As Well As Continuous Type Mixers For A Wide Range Of Applications. We Offer Planetary Mixer High Intensive Mixers Conical Screw Mixers For Homogenizing Free Flowing Powders As Well As Pastes. In Addition We Offer Shear Mixers For Cohesive Powders, Slurries And Pastes. Mixing Processes And Mixer Designs Are Determined By The Nature Of The Materials To Be Mixed. We Developed A Wide Range Of Mixing Technologies To Meet Customer Requirements For Powder, Paste, Slurry And Liquid Applications. Depending On The Characteristics Of The Products, You Will Need To Select Different Types Of Mixing Technologies.
Planetary Mixer
Planetary Mixing And Kneading Machines Operate According To The Planetary System. They Are Used For Thixotropic And High-Viscosity Products.
Temperature-Sensitive Products Can Be Mixed Gently With This System. Even Powdered And Very Light Components Can Be Dispersed Quickly In Liquids, Achieving An Optimum Fineness And Distribution. To Empty The Mixing Vessels Supplies Container Press Outs.
Features :
· The Mixing And Kneading Machines Operate According To The Planetary System
· The Mixing Elements Rotate On A Central Axis In A Fixed Tank, With Each Element Simultaneously Rotating On Its Own Axis As Well
· The Double Rotary Motion Of The Mixing Elements Covers The Entire Mixing Zone And Guarantees Optimal Dispersion
· The Revolving Wall/Floor Scrapers Support The Mixing/Kneading Process While Also Providing For Good Heat Transfer To The Tank Wall
· Processing Of Products With Very High Viscosities
· Homogeneous Mixing Of A Wide Variety Of Components
· Extremely Short Mixing Times For Very High-Quality Results
· Product-Specific Mixing And Dispersing Elements
· Easy-To-Clean Design
· Direct Measurement Of Product Temperature Via Rotating Thermo-sensor
· Variable Speed And Independent Dispersion Drive
· Vacuum-Tight And Explosion Proof Models
From laboratory-scale to large production-scale machines
Easily exchangeable mixing tools
Planetary Mixer
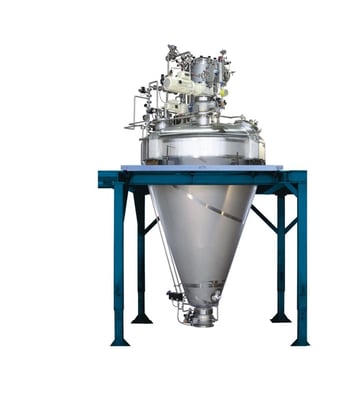
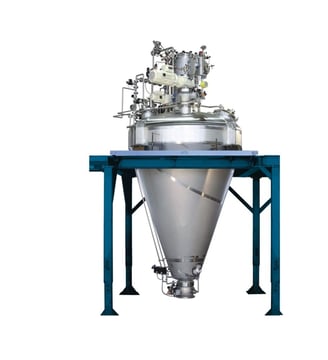
Conical Screw Mixer
Conical Screw Mixer is a batch mixer specially designed for segregative, free-flowing powders and pastes. The Conical Screw Mixers is famous for its low-intensity mixing and is a pioneer in mixing technology. It especially suited to delicate products and processes where very accurate results are required and is synonymous with gentle mixing of large volumes of up to 100,000 liters. The basic design consists of a cylindrical screw located at the vessel wall that conveys product from the bottom of the conical vessel to the product surface. The screw is attached to an arm which rotates around the perimeter of the vessel causing convective mixing and shear. The particles at the surface opposite the screw accelerate downward in a mass flow by gravity as the diameter of the vessel decreases. The three actions result in a unique three dimensional mixing action.
Advantages:
Cantilevered Screw design (no bottom support)
Belt drive systems available for sanitary applications – no lubrication inside the vessel
Clean in place designs CIP/SIP
Designed for chemical, pharmaceutical, mineral & food
Applications:
Mixing and homogenization of powders, pastes and slurries
Granulation or agglomeration of powders
Addition or injection of liquids into dry powders
Reaction under vacuum or pressure conditions
Heating and cooling of powders
De-aeration or densification of powders
Homogenization of particle size and color
Conical Screw Mixer
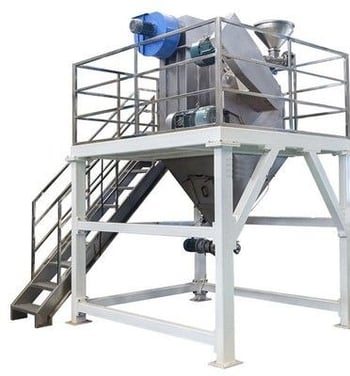
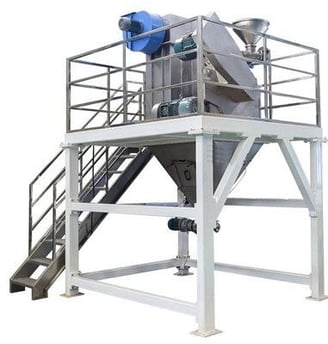
High Intensity Mixer
High Intensity Mixer can produce solid-solid composite materials in a dry process without the use of a binder by only applying mechanical force. It is also a multi-functional processing unit for precision mixing, particle surface modification and shape enhancement.
Features:
Designed for Mixing, Composing, Surface Treatment, And Spheronisation Of Chemicals, Minerals, Cosmetic & Pharmaceuticals
Available from 0.5 liters to 300 liters systems
Equipped with water-cooled jacket for even operating temperature control
Options for hard-facing and ceramic lined components
Ideal for producing heat sensitive, sticky, and abrasive materials
Easy to dismantle for inspection, maintenance, and cleaning
Suitable for processing nano-size materials
Typical Applications:
Energy Storage – Improve packing density and sintering ability for secondary batteries. Improve capability of fuel cells.
Copy & Photos – Improve flow of Toner, surface modification of carrier particles.
Pigments – Improve colour tone by high dispersion.
Chemicals – Design functional resin ( nano - filler + resin etc), high performance catalysts.
Cosmetics – Control refraction, improve flow by surface modification.
Architecture – High resistance to environment, high temperature resistance and high intensity material, gradient functional composite.
Environment – Improve of catalytic performance, effective high temperature treatment and high stability to environment.
Pharmaceutical – Particle design for Drug Delivery System (control solubility, high dissolution), improve colour tone.
High Intensity Mixer
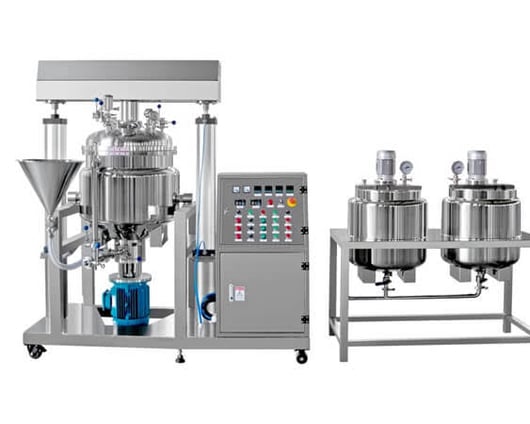
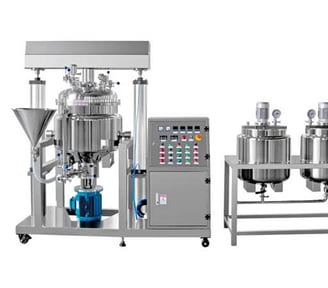
Mid Shear
Mid-Shear Mixer Capable Of Ultra-Short Cycle Times With Up To 8 Times More Transport Volume Than Conventional Ribbon Screw Mixers. The, Also Known As Ribbon Screw Blender, Also Has A Wider Range Of Operation Using Tip Speeds From 0.4 M/S To 6.0 M/S.
This multi-functional mixer combines gentle mixing and mid to low shear in the one compact machine. It’s ideal for the addition of liquids and creates a homogenous mixture without using lump breakers. The ribbon screw mixer is an energy-efficient mixer that reduces energy costs and saves on mixing time.
mixer technology enhanced for up to 8 times faster mixing
Combining gentle and mid low shear mixing in one machine
Addition of liquids creating a homogenous mixture without needing lump breakers
Coating powders with powders
Fast mixing of powders, pastes and slurries
Fast and full discharge with bottom outlet
Energy-efficient mixing
Mid Shear Mixture
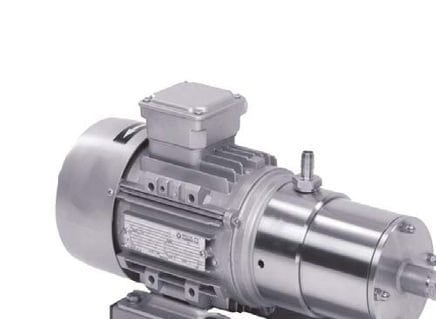
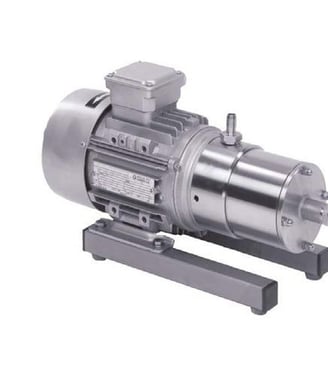
Inline Disperser
For the best possible wetting and dispersion of the powdered solids in liquid, the pressure differences created by the pumping and centrifugal action of the rotor are utilized. Air contained in the powder expands in the negative pressure of the suction area and the powder enters the liquid, which is pressed into the core of the powder structure in the positive pressure area of the rotor.
Powders wetted in this way can be finely dispersed with considerably less energy input. As a result, products that do not require further grinding can be manufactured with permanently reproducible quality.
Products that require further homogenization in a rotor/stator or further grinding in an agitator bead mill can be processed with optimized parameters, such as higher throughput or smaller grinding media. Here, the consistent quality of the pre dispersion has a positive effect on the reproducibility of the grinding result.
Advantages
· Minimal heating of product
· Minimal input of shear forces
· De aeration of the product after addition of powder
· Time savings through efficient and effective dispersion of powder
· High degree of availability
· dispersing Solids in Liquids
Standard Version
The Inline Disperser Is Unique On The Market. In The Standard Version, Dispersion Is Not Based On The Conventional Rotor-Stator Principle, In Which High Shear Forces And A High Energy Input Are Used To Disperse Powder In Liquid. In This Version, The Dispersing Principle It Does Not Use A Stator Through Which The Product Flows And No Narrow Shear Gaps Between The Rotating And Stationary Parts.
The Pressure Differences Created By The Pumping And Centrifugal Effect Of The Rotor Are Used To Achieve The Best Possible Wetting And Dispersion Of The Powdered Solids In Liquid
Advantages :
· Minimal Product Heating
· Lowest Input Of Shear Forces
· De Aeration Of The Product After The Solid Intake
· Insensitive To Small Foreign Objects
· High Availability Application Fields:
· Shear-Sensitive Products
· Temperature-Sensitive Products
ROTOR-STATOR VERSION
For products that require dispersion with more energy, the can also be equipped with a classic rotor-stator version. The dispersion principle is the same as in the standard version. Vacuum expansion of the contained air and wetting by overpressure also takes place here. However, the stator, through which the product flows, introduces significantly higher shear forces into the product.
The result is higher shear forces in the product for de agglomeration of powders that are difficult to disperse.
Advantages:
More intensive dispersion of agglomerates that are difficult to disperse
Shorter dispersion time
Application Fields:
Solids that are difficult to disperse
Shear-insensitive products
Experience the advantages of our Epsilon Inline Disperser:
Dispersion Quality
Consistently reproducible product quality
Best wetting of the solid surface
Gentle processing of sensitive formulation components
Handling & Cleaning
Process free of manual influences
Quick and easy to clean, good accessibility
No adhesion of powder dust in the process tank
Dust & Emission Free
Closed process housing
Separate feeding of solid and liquid
Loss-free incorporation of solids
Process Reliability
Automatic mode eliminates operator error
Tolerant to smaller foreign objects, generally, no machine downtime
Explosion-proof version
Inline Disperser
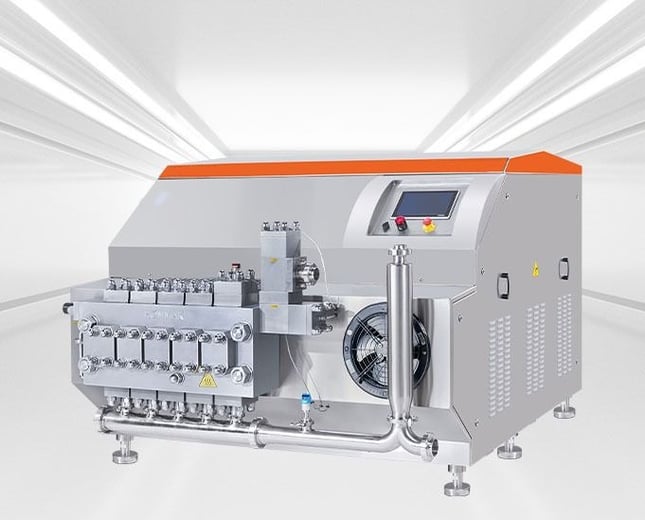
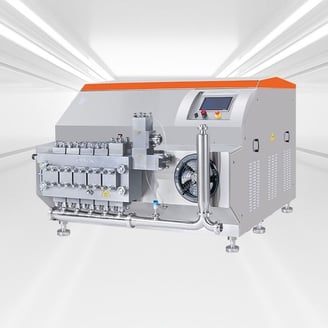
Homogenizers
The design of the homogenizer determines the quality of your dispersions.
Only with optimum utilization of the shear energy can the required particle/droplet sizes and size distributions be achieved. In addition to economy, efficiency is paramount when selecting a homogenizer. And of course, a universal application for your various products must be possible.
Our particular focus is on the development of an optimal tooth geometry, on the dispersion tooth, as well as on the design of the entire homogenizing system, in order to produce both the highest shear rates / shear energies and thus to ensure the finest droplets / particles. In addition, all homogenizers are CIP-capable.
The homogenizers ensure high flow rates, especially in the upper vacuum range. With the homogenizer we meet all the demands of the market.
A variety of options and versions makes the following possible for you:
· Homogenization
· Dispersing
· Suction of different phases directly into the area of the homogenizer (e.g. hot-cold)
· Dilution of either sulphate in a continuous process
· Induction of powders
· Dosed feeding of liquid phases at the same time and much more
Homogenizer
Rotor/ stator inline homogenizer
Stationary design
Rotor circumferential speed up to 31 m/s
Installation in the tank bottom
Installation in existing tanks via special flange
BASE
Stationary, horizontal design for external connection to existing tank or for
continuous operation
Rotor peripheral speed up to 31 m/s
MOBILE
Rotor/stator homogenizer
Mobile, horizontal design for external connection to existing tank or for
continuous operations
Rotor peripheral speed up to 31 m/s
Homogenizer