Animal Feed Mill
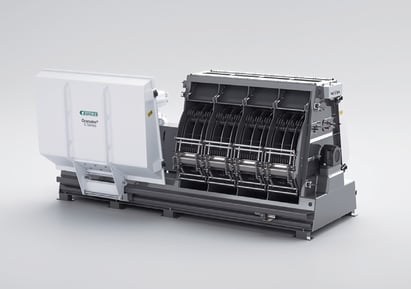
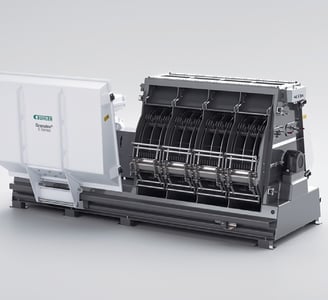
At our company, we specialize in providing innovative process solutions and consulting services designed to transform a diverse range of feed ingredients into safe, healthy, and nutritious animal feeds, whether in pellet or mash form. Our commitment to animal welfare and optimal feed conversion rates drives us to implement cutting-edge technology in our feed processing installations. Our experienced engineers ensure that you meet the most stringent hygiene standards while reducing the risk of cross-contamination. We are dedicated to supporting you in every facet of reliable animal feed production, working closely with you to keep you ahead of the competition. With our tailored solutions, you can enjoy superior quality and enhanced feed safety, ensuring that your livestock receive the best nutrition possible for their health and productivity. Our aim to be a leading global brand in the feed machinery industry, with high customer satisfaction, solution-oriented, sustainable and achievable targets to be the best, adopting a high-quality solid production and service concept, offering advanced technology machines to the market with confidence Feed Tech provides technology products and services that fully meet customer expectations, spend less energy, by making complete facilities, machinery sales, renovation, and capacity increase.
PELLET MILL
We Fully Understand How To Pellet A Wide Range Of Materials. Our Expertise Focuses Not Only On Creating Pellets In Partnership With You We Strive For A Process That Improves The Feed Conversion Rates, Nutrition And Safety Of Your Pellets.
Our extensive pellet mill portfolio covers a wide range of applications.
Die diameters: from 420mm - 1200mm
Capacities: ranging from 5 up to 80 t/h (depending on product)
Options like central lubrication system, heating mats, slippage detector, execution in and many more are available depending on the machine type.
Pellet Mill With Direct Drive Developed in close cooperation with leading feed millers, the pellet mill is different from anything else in the industry. A specially designed direct drive system powers the production of feed pellets with an unprecedented level of efficiency. The result is an output of up to 80 metric tons per hour. Due to its compact design it is also easier to use and maintain than anything comparable in the market.
Pellet Mill With V-Belt Motor. Our pellet presses from series have been used successfully for generations. Characterized by low maintenance requirements and a durable design they deliver high pellet quality and enable a flexible operation when product recipes change frequently in your process.
Pellet Mill With 2 V-Belt Motors Shouldered.
This design version covers another state-of-the-art compacting technology. Thanks to the power transmission via shouldered motors those pellet mills require less footprint and run with reduced circumferential die speed
Benefits:
– Sturdy construction
– Easy to maintain
– Stable, reliable production
– Reduced footprint
This modular system combines modern conditioning and hygienization technology, which can be adapted to your pelleting process. High feed hygiene, reduction of start-up time and productivity increase are just some of the many advantages.
1 Feeder.
The feeder ensures optimal product dispensing from the pellet mill surge hopper to the conditioner.
2 Conditioner & Mix
The conditioner enables the heating of compound feed particles to temperatures of up to 95 °C. In addition to steam, up to two additional liquids can be added. Thanks to the optimised design of the mixing tools, residue quantities are consi- derably reduced.
Compared to the conventional conditioner the conditioner comes in a more sophisticated design with additional temperature sensor and intelligent control unit to achieve a reduction of start-up time.
3. Retentioner.
The system can be supplemented with retentioner for increased hygiene requirements. This allows retention times of 30 up to 360 seconds. It has best machinery hygiene properties thanks to the optimised design of the screw segments and the large service door.
4 Opti flow.
The Opti flow system ensures continuous product input and protects the pellet mill from current peaks and fluctuations. This reduces the risk of roller slippage, increases pelleting performance and extends the service life of the entire pellet mill.
5 Pellet Mill And Line Control.
Combine thermal pre-treatment with pellet mill to create a high performance complete system. In order to utilize the complete performance capability of the pellet line, we recommend to connect it to
PELLET MILL
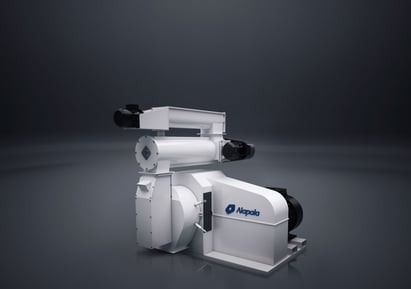
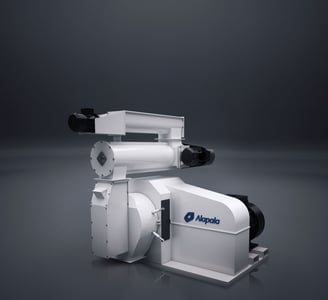
POWDER GRINDING MILLS
With our versatile grinding portfolio, consisting of horizontal and vertical hammer mills as well as roller mills, we can cover all of your size reduction needs. We can bring you solutions for pre- and post-grinding, coarse and fine grinding, as well as for creating crumbles of various sizes.
Vertical hammer mill.
With its vertical grinding shaft, our Vertical grinding and pre-grinding hammer mill can deliver up to 25% energy savings. A smaller footprint, change-over and sanitation benefits make it ideal for animal feed, grain/oil milling and biomass industries.
Horizontal hammer mill.
Our horizontal hammer mill is a high efficiency grinder for size reduction in various feed & food processing industries. Generally applied for dry materials with a bulk density of
0.2-0.8kg/dm3, it convinces through high production flexibility and minimal downtime.
Impact Mill
This hammer mill provides industry leading throughput capacities on a wide range of friable and fibrous products with exceptionally uniform particle size distribution from coarse to fine applications.
Cracking mill..
The high performance cracking mill is for optimal processing of oilseeds and various applications in the feed milling industry, providing ease of maintenance, full automation control as well as highest throughput rates.
It is available in a modular design with up to 3 roll pairs, 2 different roll lengths and diameters
Features
From 5 to 35 tons/hours capacities
Two directions of rotations
Rotor has been balanced under maximum working speed
Particle size up to 60 mm. edge length
Bulk density 0.2 to 0.8 kg/dm3
Electro pneumatically controlled pivoted deflection plate
Low noise 90-93 dba under nominal load
Easily changeable screens within one minute by quick span lock
Interlock preventing opening of doors (when motor is running)
Two bearing suspension
Hammers and rods hardened for long life
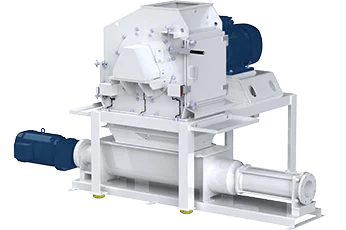
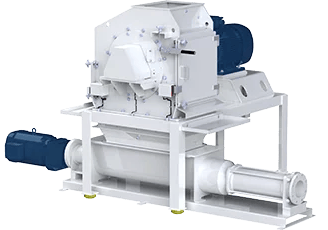
Powder Grinding
PELLET CRUMBLER.
This grinder is applied for crumbling feed pellets and for size reduction applications in multistage grinding systems in various industries. The modular concept allows a combination of up to 3 crushing stages in one crumbler with optional automatic roll gap adjustment system.
Generally for very young poultry, small pellets should be reduced smaller parts as called crumbs 5 or 6 mm. diameter pellets reduced by means of two or four crumbling rolls, also that provide a nutritionally balanced diet. Also the crumbler are used commonly in cattle feed and sheep feed industry today
Features
Roll adjustment assembly with overload protection device
Each roller is driven seperately by means of electric motor
Heavy hardened and fluted longitudinally press rollers
Rolls are mounted in heavy duty self-aligning bearings
Installed in a sturdy steel housing
Pneumatically operated by-pass flap
Low noise level
Capacity up to 30 tons per hour
Seperately driven dosing and supply feeder distributes pellets
PELLET CRUMBLER.
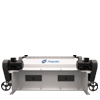
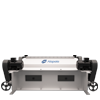
COOLING
Ready for handling and storage.
The cooling of your hot pellets is essential for further handling and proper storage. Our extensive portfolio of counter current coolers offers you an efficient, hygienic and homogeneous cooling process. Different discharge systems ensure gentle handling with minimal fines tailored to your product.
Conical discharge.
The conical screen bottom creates a uniform product layer and therefore an even air distribution across the cooler which results in a very homogeneous cooling. Due to the angle of the cone the pellets move gentle to the outlet leaving almost no product residues behind.
Flatbed discharge.
Compared to the conical discharge, the flatbed coolers take up less space in terms of construction height. The rotating rack distributes the product layer evenly and the discharge systems are designed the way that the pellets stay intact with minimal pellet breakage or fines.
Our portfolio of coolers contains various types and sizes and covers capacities ranging from 7 - 60 t/h.
Pellet coolers are consist of three sections
Rotary valve | Exhaust hood | Cooling column | Discharge grid system | Collecting hoper
Pellet coolers reduce the temperature very quickly and reduce the moisture level from 18 % to ambient moisture level to 10-12 % avoid moulding for proper storage and handling.
Features
Side walls with one transparent inspection door
Level control sensors
Collecting hoper
Rotary valve with electric motor
Exhaust hood
Pellet spreader
Unloading mechanism consisting of one electro pneumatıcally adjustable, one stationary and one
Electro pneumatically driven sliding grid discharge system
Single deck or double deck design
.
Pellet Cooler
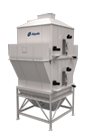
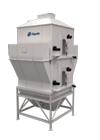
COATING
Upgrading your feed pellets.
Coating & post pelleting applications.
Coating your feed pellets with fats and oils, colorants and flavourings, vitamins or enzymes enables you to offer your products in a higher quality grade at higher values. Our coating and post pelleting application solutions can add this capability to your line. Micro dosing allows to store all ingredients in bulk and it will automatically add the required amount of ingredients needed in the mix.
Uniform coating through high-precision control.
The coating drum enables you to simultaneously coat and thus upgrade your products with up to three different liquids – with a liquids addition rate of max. 8 percent of the product throughput. Design versions of mild steel or high-grade stainless steel for throughputs up to 30 t/h offer you a wide range of choices.
Micro dosing ingredients such as drugs, vitamins and trace minerals with ease and pin point accuracy
Features
Heavy-duty mild steel frame
The rotating drum with scale system is enclosed for dust control
All contact parts with ingredients of the machinery are AISI304 stainless steel
Flexible spouting from the micro hopper to the drum
Clean and dust-free environment
Micro scale accuracy is a +/- of 0.02 lbs. (9.07 grams.)
Micro hopper speed control
Hopper lids are designed to swing or lift open for filling
COATING
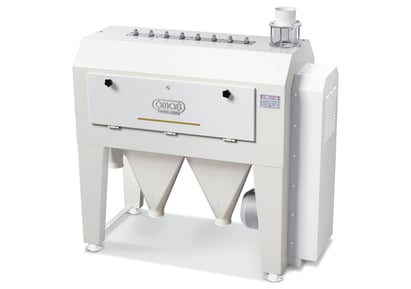
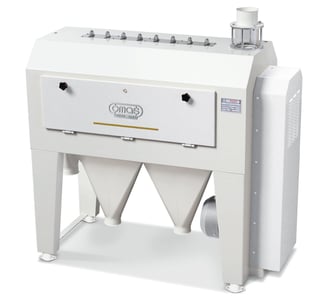
Full Colour Optical Sorter
Brand new full colour optical sorter has arrived. Offering the ultimate solution in optical sorting, it is sure to full fill your sorting needs.
Features
· Full Colour Cameras: The machine is equipped with Japan’s latest full colour cameras which allow the sorter to match the eye’s ability to see true colour. Even the smallest colour differences are identified and rejected.
· Near Infrared (NIR) Camera: The NIR camera detects inorganic foreign material such as stones, plastic, glass and other items that have a similar colour to the accept product. Impurities such as glass, plastic and stones which have the same colour as the accept material cannot always be detected by a full colour camera. Featuring both NIR Glass high technology camera and RGB full colour cameras the NIRAMI has the ability to detect and remove foreign materials.
· Shape Recognition: Shape recognition technology enables the machine to sort the material by shape (such as broken or adhered) which conventional colour sorters could not achieve
· Advance Software: The 12 inch touch screen is designed for easy use. The user- friendly interface with simple Icons and images provides
intuitive operation of the machine. The advanced software evaluates
the product application and automatically creates the sensitivity accurate defect removal.
Full Colour Optical Sorter
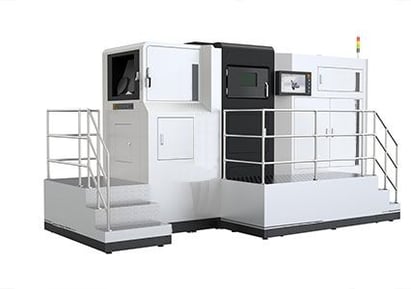
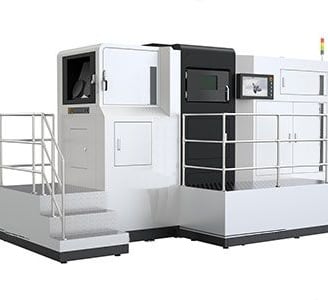