Extrusion Profile
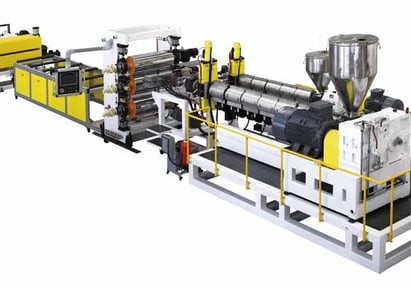
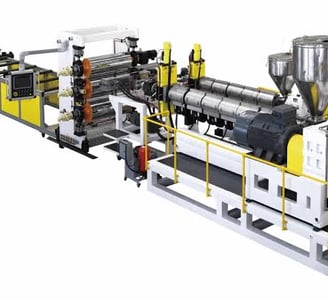
Our PE profile extrusion line is expertly designed to provide high-quality, efficient, and reliable solutions for the manufacturing of PE profiles. Equipped with the latest technology and robust components, this production line guarantees optimal performance and exceptional product quality. It excels in creating profiles suitable for a variety of applications, including construction, agriculture, and industrial settings. Whether you require profiles for piping systems, cable protection, or insulation panels, our PE profile extrusion line is tailored to meet your specific needs. Additionally, our PC/PMMA profile extrusion lines are engineered to process premium polycarbonate and polymethyl methacrylate materials, producing top-tier LED lighting profiles that enhance functionality and aesthetics.
Single Screw PVC Profile Extruder Machine
Our single screw PVC profile extruder machine is engineered to meet the highest standards of quality and efficiency, leveraging advanced cold extrusion technology.
This method ensures precise, high-quality profiles suitable for various industries, including construction and decoration.
Our PVC profile extruder exclusively uses granulated PVC materials, making it ideal for manufacturers focused on environmental sustainability.
These profiles offer exceptional durability, weather resistance, and aesthetic appeal, making them ideal for both residential and commercial use.
Construction Materials: Producing profiles for doors, windows, and protective strips for shelves and edges.
Decorative Profiles: Creating durable, impact-resistant profiles for various decorative applications.
Key Components of PVC Profile Extruder Machine Line
General (thermal) extrusion process
Main Extruder
The single screw extruder is the core of the PVC profile extruder machine line. It melts and mixes the PVC resin with additives to form a uniform melt. This type of extruder is cost-effective and suitable for producing simple profiles and basic applications.
The extrusion die shapes the molten PVC into the desired profile. It determines the profile’s dimensions and surface finish. Precise die design is crucial for producing accurate profiles with minimal defects.
Vacuum Sizing Tank
After shaping, the profile needs to be cooled to retain its shape and dimensions. The cooling system often includes water tanks where the profile is immersed to cool rapidly.
Haul-Off Machine and Cutting Machine
This machine pulls the profile through the extrusion line at a controlled speed, ensuring that the profile maintains its dimensions and consistency. The speed of the haul-off machine must be synchronized with the extrusion speed to prevent stretching or compression of the profile.
Cut the continuous profile into specific lengths and stack them for further handling. Precision cutting ensures clean edges and accurate dimensions, which are vital for the final application of the profiles.
Comparison of Cold Extrusion and Hot Extrusion Processes for PVC Profiles
Hot Extrusion (Vacuum Forming Extrusion)
Process Characteristics:
• Surface Quality: Typically results in a matte finish with potential surface defects like pull lines and shrink marks.
• Material Use: Suitable for PVC products with filler content below 30%.
• Production Efficiency: High production speed and efficiency, making it ideal for high-strength and tough profiles.
• Dimensional Precision: Profiles may have larger tolerances compared to cold extrusion.
Cold Extrusion (Cold Top/Hard Top Forming)
• Process Characteristics:
• Surface Quality: Achieves a mirror-like, high-gloss surface.
• Material Use: Capable of using high filler content materials, such as high calcium components, which reduce raw material costs.
• Production Efficiency: Lower production speed and efficiency compared to hot extrusion. Suitable for profiles requiring high surface quality.
• Dimensional Precision: Produces profiles with very tight tolerances and high precision.
Advantages & Disadvantages of Hot Extrusion (Vacuum Forming Extrusion)
• Advantages:
• High Efficiency: Fast production speeds, ideal for high-volume manufacturing.
• Good Strength and Toughness: Produces profiles with strong structural integrity.
• Cost-Effective for Low Filler Content: Best suited for profiles with filler content below 30%.
• Disadvantages:
• Higher Mold Costs: More expensive due to the need for complex molds.
• Surface Quality: Matte finish with potential for surface defects, such as pull lines and shrink marks.
• Larger Tolerances: Dimensional precision may not be as high as cold extrusion.
• High Equipment Requirements: Requires high-quality extruder configuration and PVC formulation.
Advantages & Disadvantages of Cold Extrusion (Cold Top/Hard Top Forming)
Advantages:
• High Surface Quality: Produces profiles with a glossy, mirror-like finish.
• Dimensional Precision: Achieves tight tolerances, making profiles fit precisely with CAD designs.
• Lower Raw Material Costs: Can use high filler content, reducing overall material costs.
Disadvantages:
• Lower Production Efficiency: Slower production speeds compared to hot extrusion.
• Reduced Strength and Toughness: Profiles may be less tough and strong due to high filler content.
• Handling and Surface Protection: Requires protective measures such as coatings or bags to prevent surface damage during handling and transportation
Single Screw PVC Profile Extruder Machine
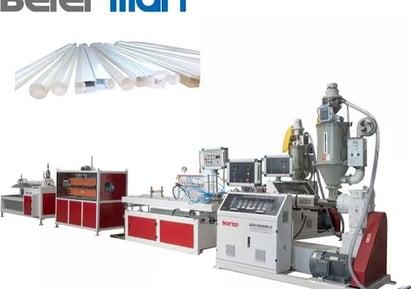
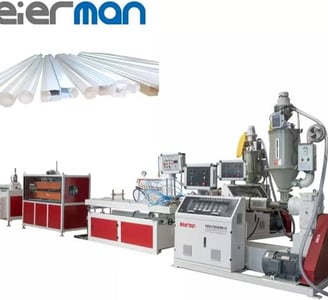
LED Lighting PC Profiles Extrusion Line
Our PC/PMMA profile extrusion lines are designed to process high-quality Polycarbonate (PC) and Polymethyl Methacrylate (PMMA) materials, creating superior LED lighting profiles such as diffusers and tubes. These profiles come in various finishes and are essential for modern LED lighting solutions.
They come in various configurations and sizes, such as flat, tubular, semi-circular, and irregular. Some have beam angles, often called optical lenses, and some do not. The colors are transparent, translucent, and milky white. Depending on the application, some are rigid, and some are flexible.
Including glossy, two-color co-extruded, frosted, sandblasted, wide diffusion, semi-circular, and so on.
• LED lighting covers or lampshade
• Outdoor and architectural lighting solutions
• Decorative lighting profiles
Extruded hosts are our most mature products. The unique screw and barrel for the PC material of the extruder are made of high-strength nitrided alloy steel (38CrMoALA) or high-strength quenched alloy steel (9Cr18MoV). We have especially designed the Gravimetric Dosing Controller system for rigid profiles
Co-extrusion is a process required for the production of two-color lamps, lampshades, etc. Our co-extrusion equipment can be controlled by PLC system together with the host machine and haul-off to achieve precise extrusion production results
The subsequent production steps are hauling and cutting. We can laminate the surface of the product after the production of PC lamps and lanterns according to the customer’s demand, in order to protect the PC lamps and lanterns from wear and tear.
LED Lighting PC Profiles Extrusion Line
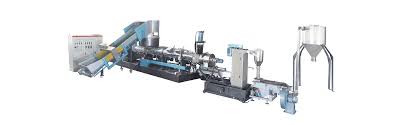
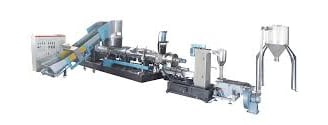
PE Profile Extrusion Line
Our PE profile extrusion line is engineered to deliver high-quality, efficient, and reliable solutions for manufacturing PE profiles. With cutting-edge technology and robust components, our production line ensures optimal performance and superior product quality.
Whether you need profiles for construction, agriculture, or industrial applications, our PE profile extrusion line is designed to meet your needs.
• Ideal for piping systems, cable protection, and insulation panels.
• Used in liners, wear strips, and guides
Main Extruder
The single screw extruder is the core of the PP,PE profile extruder machine line. It melts and mixes the PVC resin with additives to form a uniform melt. This type of extruder is cost-effective and suitable for producing simple profiles and basic applications.
The extrusion die shapes the molten PP,PE into the desired profile. It determines the profile’s dimensions and surface finish. Precise die design is crucial for producing accurate profiles with minimal defects
Vacuum Sizing Tank
After shaping, the profile needs to be cooled to retain its shape and dimensions. The cooling system often includes water tanks where the profile is immersed to cool rapidly.
Haul-Off Machine and Cutting Machine
This machine pulls the profile through the extrusion line at a controlled speed, ensuring that the profile maintains its dimensions and consistency. The speed of the haul-off machine must be synchronized with the extrusion speed to prevent stretching or compression of the profile.
Cut the continuous profile into specific lengths and stack them for further handling. Precision cutting ensures clean edges and accurate dimensions, which are vital for the final application of the profiles.
PE Profile Extrusion Line
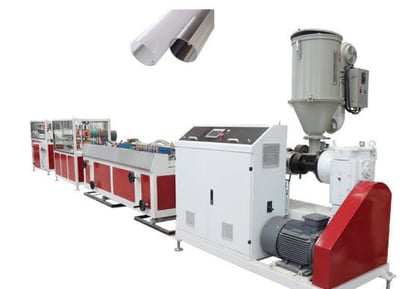
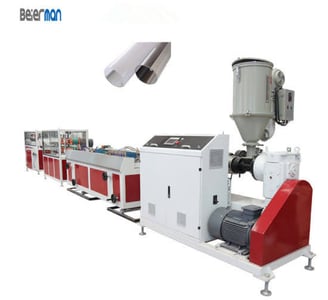
Plastic Profile Extrusion Machine
Our plastic profile extrusion machines are designed to meet the highest standards in quality and efficiency, catering to a wide range of industries including crafts, electronics, machine parts, construction materials, and decorations. Whether you need robust PVC, PE/PP profiles for construction and decorative purposes or high-clarity PC profiles for LED lighting, our extruders provide the perfect solution for your production needs.
Types of Plastic Profiles Extrusion Machines We Produce
Plastic profiles are extruded plastic products with non-circular cross-sections, used extensively in various industries. These profiles include:
• PVC Cold/Hard Extrusion: Producing profiles with a glossy surface, high precision, and widths up to 450mm.
• Plastic Extrusion Profiles: Available in PVC, ABS, PP, PE, PC, and PMMA, suitable for diverse applications.
• PC Acrylic Lampshades: High clarity and impact-resistant profiles for lighting.
• PVC Strips/Plastic Strips: Durable and versatile for multiple uses.
• Protective Corners: Impact-resistant profiles for safety and protection.
• Anti-Collision Handrails/Wall Panels: Durable and aesthetic profiles for building interiors.
By choosing our plastic profile extrusion machines, you ensure high production efficiency, consistent quality, and versatility for your specific application needs. Contact us today to learn more about how our solutions can enhance your manufacturing capabilities.
• Main Extruders: Designed for efficient processing of PVC, PE, and PC,PMMA granules.
• Vacuum Sizing Tanks: Ensure precise dimensional accuracy and cooling.
• Cooling Water Tanks: Maintain proper temperature control to stabilize the pipe.
• Haul-Off Units: Provide consistent pulling force to avoid pipe deformation.
• Cutting Machines: Equipped with precise cutting mechanisms for clean and accurate cuts.
• Storage Systems: Efficiently handle and store the finished pipes.
Profile Specification:
According to the drawings provided by the customer
Key Features:
• Consistency and Accuracy: Our molds are designed to maintain consistent profile dimensions, ensuring every piece meets exact specifications.
• Extrusion Technology: Our rigid extrusion equipment features gravimetric dosing controllers, ensuring precise material feed and reduced waste.s.
Plastic Profile Extrusion Machine
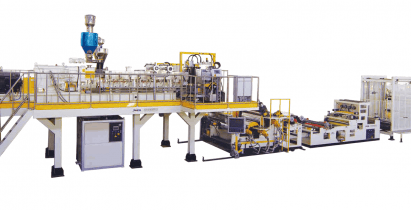
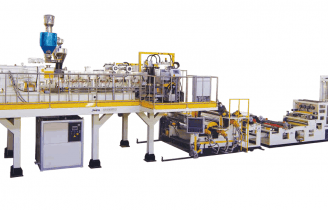