Pallet Shuttle
Our system maximizes warehouse and manufacturing floor space, allowing for a significant increase in pallet storage capacity. By strategically minimizing aisle widths and leveraging vertical space, the Pallet Shuttle system ensures optimal use of every square foot. Optimized Space Utilization
Pallet Shuttle systems provide high density storage of bulk stored items. These systems provide better storage density than legacy Drive-in and Push Back system
For operations that need high density storage with a low SKU count and high volume lot in and lot out storage, Systems can greatly improve overall storage capacity and reduce redundant forklift usage. Operators move the Shuttles from lane to lane and level to level for Semi-Automated deep lane storage. Maximize Bulk Storage and Reduce Redundant Manual Forklift Bulk Stack Labour
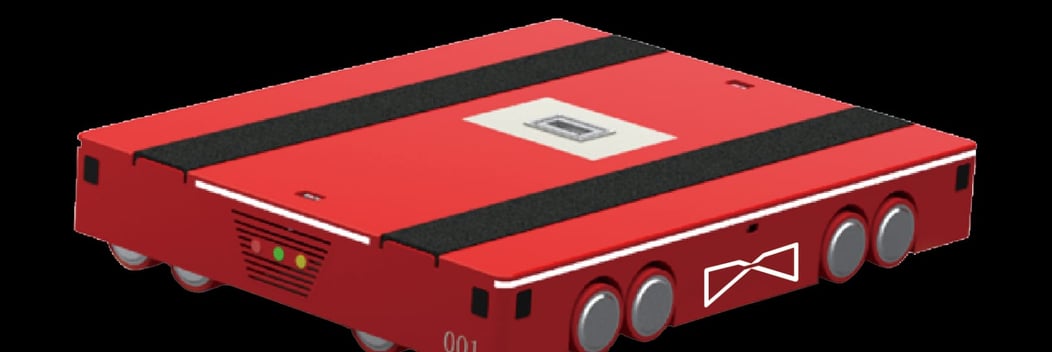
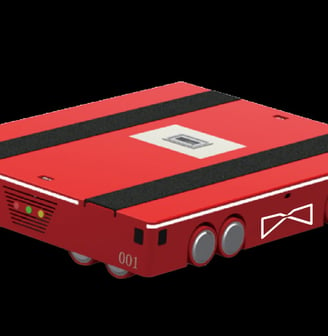
Speed and accuracy are critical in high-demand environments. The automated shuttle effortlessly transports pallets to their designated location, reducing manual handling and streamlining the entire storage and retrieval process. This precision not only boosts productivity but also minimizes the risk of inventory damage
Adaptability to fluctuating inventory levels and diverse product types stand at the core of our system’s design. It seamlessly scales to meet growing operational demands, ensuring that your investment today continues to yield returns well into the future.
The evolution of high-density pallet storage systems: greater capacity, speed and throughput
The Pallet Shuttle is a semi-automated high-density storage system in which a shuttle with an electric motor runs along rails within the storage channels to load and unload pallets. The process is controlled by an operator, who places the shuttle in the racking using a forklift and controls it via a tablet.
Compared to other high-density solutions, e.g., drive-in racking, the shuttle rack system increases storage capacity, goods-in/goods-out flows and the number of products to be stored. The system is also available in a fully automated version, which features either stacker cranes or transfer cars.
Advantages of the Pallet Shuttle system
Time savings and productivity gains: the shuttle executes orders speedily, and the forklift operates in the aisle without entering the racking. This shortens loading/unloading times and raises the number of cycles/hour.
Space savings: storage channels can exceed 60 m in depth, while clearances between levels are minimal, increasing storage capacity.
Cost savings: the optimal use of space reduces the system’s footprint, thus keeping down land costs. And in cold storage warehouses, this means less surface area to be cooled, resulting in lower energy consumption.
Multiple SKUs: grouping SKUs by channels as opposed to complete lanes allows for greater product diversity in the storage system.
Compatible with LIFO and FIFO: the system can operate in line with the LIFO (last in, first out) or FIFO (first in, first out) inventory management strategies.
Easy to use: all system functions are activated from the control tablet, which is equipped with an intuitive user interface.
Safety: as the forklifts do not operate inside the racking, the metal structure remains free from damage, and the risk of accidents is minimized.
Pallet Shuttle system applications
For companies that need high-density storage and maximum throughput
The Pallet Shuttle is the perfect storage solution for boosting productivity in warehouses looking to considerably increase storage capacity while facilitating and streamlining loading and unloading operations.
Facilities with many pallets per SKU
The Pallet Shuttle is ideal when managing a large number of pallets per SKU. Each channel can hold a different SKU.
Warehouses with massive inbound/outbound flows
The system notably speeds up pallet storage and retrieval for businesses with a fast-paced turnover of very homogeneous goods.
Cold stores
Thanks to space optimisation, the volume to be cooled is reduced, resulting in significant savings in energy costs.