Pallet Rack
Industrial racking is another popular storage solution used across industries, especially in warehouses and large distribution centers to optimize the storage space. They are deeper and stacked higher than shelves. It is designed in such a way that makes it possible to access products using forklifts or automated mechanized devices. Industrial racking is made of durable, high-strength materials, like stainless steel. Owing to the desirable properties of the material, it can withstand the weight of heavy products.Pallet racking may require material handling equipment, such as forklifts or mechanized devices to lift and move heavy materials. This is not the case with industrial shelving.
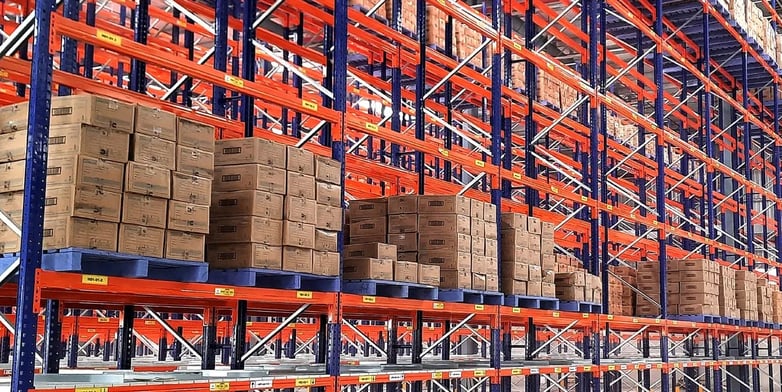
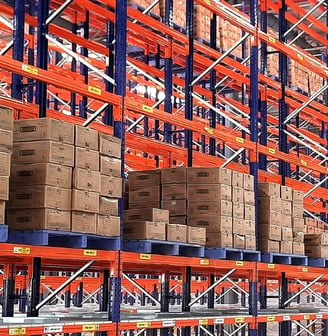
Selective Pallet Racking
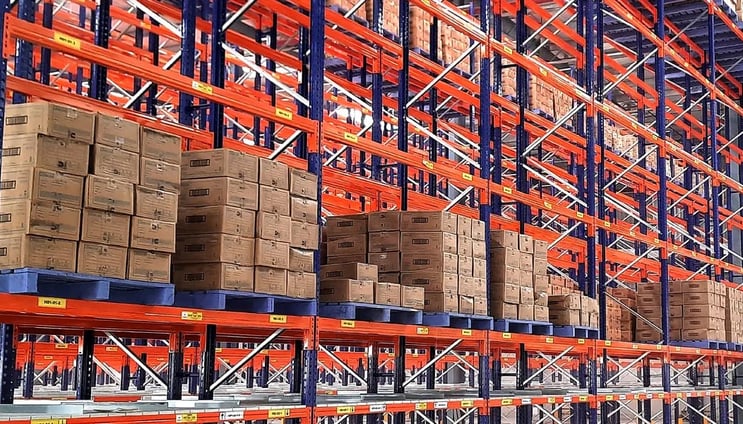

Selective pallet racking is the most universal storage system thanks to its versatility. Its distribution in the warehouse creates a series of interior aisles, enabling direct, individual access to all pallets. This setup is ideal when working with a wide array of SKUs.
Our racks are manufactured in accordance with the highest quality pallet racking standards and are equipped with several safety features. An extensive range of uprights, beams, shelving and supports allow for the design of installations tailored to the most demanding needs.
Advantages of selective pallet racking
Direct access to each pallet: all pallets are accessible from the working aisle.
Safety locking system this mechanism prevents the accidental displacement of the beam, enhancing the overall safety of the racking.
Easy implementation: the structures are assembled quickly and have a low maintenance cost.
Versatile: these racks adapt to the height of the facility and to multiple load types (from pallets and containers of different weights and sizes to boxes, drums and reels).
Configurable and scalable: the height of the storage levels is adjustable and can be modified to reconfigure the storage system. Moreover, the racking can be expanded easily by adding bays and height levels.
Suitable for picking: operators can perform picking tasks at floor level (or on the lowest parts of the racking). They can also pick items from higher locations using order pickers.
Racking inspection: as a manufacturer of industrial pallet racking, We offers an annual mandatory racking inspection service. Inspections are conducted by a highly qualified specialised technical team.
Drive-in Racking
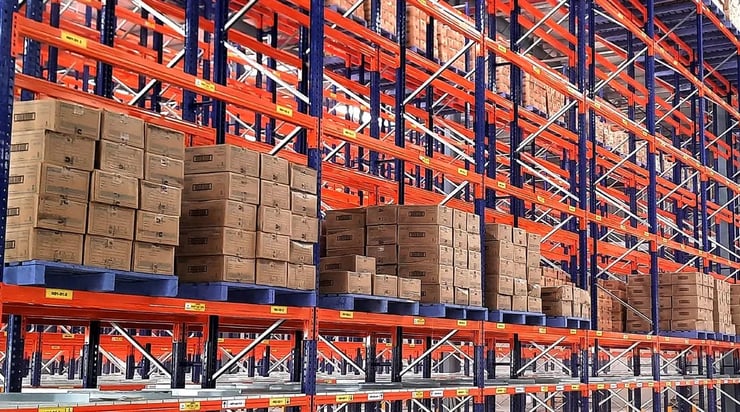

Drive-in/drive-through racking system: perfect for warehouses with homogeneous goods and a large number of pallets per SKU
Drive-in racking is the simplest and most affordable high-density storage method. It is comprised of multiple racks with a series of lanes accessed by forklifts to deposit or retrieve pallets. Compared to conventional pallet racking, this solution notably increases storage capacity.
These racks can have two configurations: drive-in (pallets are loaded and unloaded from the same working aisle) or drive-through (pallets are loaded through the front aisle and unloaded through the rear aisle).
Advantages of a drive-in/drive-through racking system
Maximum utilisation of space: it makes excellent use of both the available surface area and height, thus increasing storage capacity compared to conventional pallet racking.
Simple and economical: it’s the simplest high-density storage system and requires the lowest investment.
Configurable: the depth and height of this racking can be adapted to the needs of each customer and to the characteristics of the goods handled.
One or two aisles: this solution can be used with just one aisle (loading and unloading from the front) or with two (loading in the front, unloading from the back).
Guiding elements: drive-in racks incorporate accessories that facilitate forklift movements and correct pallet positioning.
Energy savings: the smaller footprint reduces the surface area to be cooled in cold storage and freezer warehouses.
Easy inventory management: each lane stores a single SKU, streamlining stock control.
Different pallet types: this racking can accommodate pallets of varying weights and dimensions...
Mobile Racking
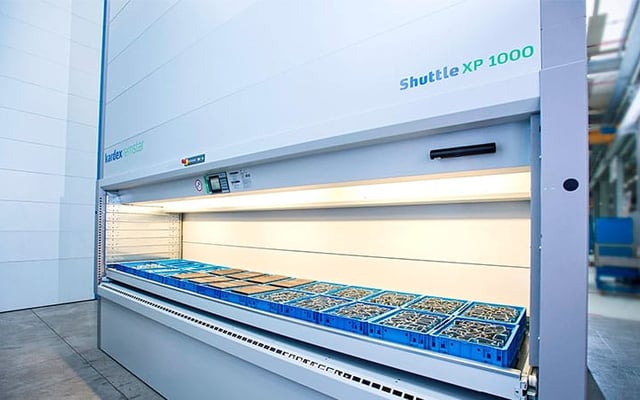
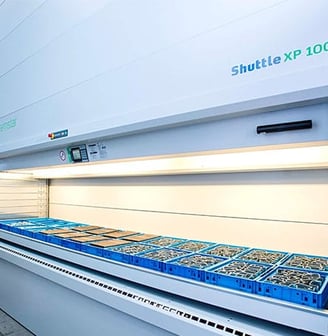
Mobile racking is a high-density storage solution that considerably increases storage capacity while maintaining direct access to each pallet. The racks are mounted on motorised mobile bases that move laterally along rails.
mobile storage racks optimise the volume occupied by the storage system. That is, the racking units come together or separate in a completely controlled way, opening only the working aisle required at any given time.
Advantages of mobile racking
Increased storage capacity: movable storage racks provide 80 to 120% more storage capacity compared to conventional pallet racking.
Direct access: this is the only high-density storage system allowing direct access to all stock stored.
Cold storage energy savings: by making better use of space, the volume of air to be cooled is smaller, reducing energy consumption.
Suitable for picking: with the multi-aisle operating mode, up to 3 aisles can be opened simultaneously (instead of just one) to perform picking.
Versatility: mobile racking can be adapted to store non-palletised loads, such as coils, pipes and profiles.
Scalable: the system adjusts to the growth of the warehouse. It can be expanded by adding additional mobile racking units.
Safety and durability: the robust structure is equipped with numerous safety devices to protect operators and goods.
High load capacity: each mobile base can move over 600 tonnes.
Mobile pallet racking applications
Ideal for high-density storage and direct access to each pallet
The mobile pallet racking system is perfect for companies requiring unrestricted access to all pallets stored and looking to make the most of their available surface area.
Facilities with multiple SKUs
Mobile racking is ideal for warehouses with a wide variety of medium-to-low-turnover SKUs.
Pallet Flow Racking
Pallet flow racking
Pallet flow racking consists of high-density storage structures formed by slightly sloped channels with rollers that enable pallets to slide into place. Palletised loads are inserted in the highest part of the channel and move by gravity to the opposite end, where they are ready to be removed.
There are no intermediate aisles in a flow rack system, which increases storage capacity. In addition, the flow through racking can work in line with the FIFO (first in, first out) strategy, facilitating efficient inventory management.
Advantages of pallet flow racking
Maximum utilisation of surface area: pallet flow racking is a high-density storage solution that significantly increases a warehouse’s capacity.
Flawless product turnover: its compatibility with the FIFO method fosters excellent inventory control.
Time savings: having all SKUs available in a single working aisle makes it easy to locate any product, reducing forklift manoeuvring time and speeding up pallet removal.
Separation of loading and unloading: pallet storage and retrieval are performed from separate aisles. This eliminates interference and enables forklifts to work without interruptions.
Multiple SKUs: although each channel houses a single SKU, these can vary between the different channels.
Better energy consumption: implementation of this system in facilities run at low temperatures reduces energy consumption since the volume to be cooled is smaller.
Safety and reliability: the different elements that make up pallet flow racks are designed to ensure risk-free operation for operators and goods.
“
Pallet flow racking system applications
Ideal solution for multiple industry and distribution sectors
Pallet flow rack systems are perfect for companies that need to make the most of their available storage space and streamline goods handling operations for efficient, error-free inventory turnover.
Large-scale storage of high-turnover SKUs
The pallet flow rack is ideal for housing many unit loads per SKU.
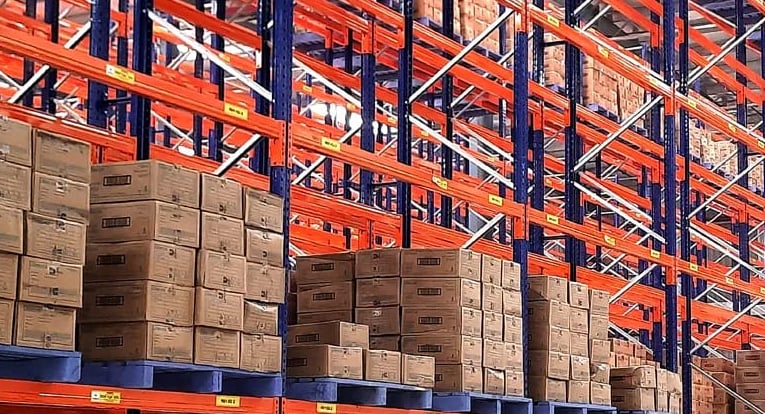
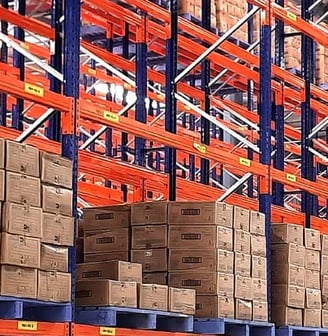