Lithium Battery Testing
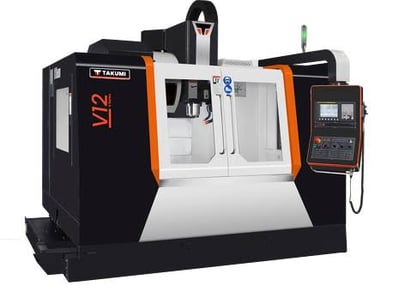
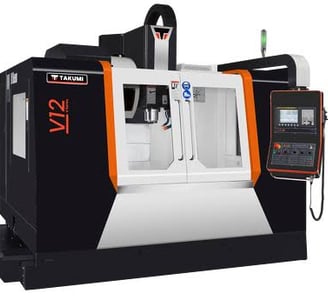
The demand for high-performance lithium-ion batteries is surging due to the rising adoption of electric vehicles, portable electronics, and renewable energy storage systems. Our company specializes in providing comprehensive solutions for lithium-ion battery manufacturing, offering a wide array of equipment and technologies for critical processes such as CAM/AAM production, electrode production, battery cell assembly, and charging/discharging inspections. With our expertise and advanced machinery, we empower manufacturers to optimize production efficiency, enhance product quality, and remain competitive in the rapidly evolving battery industry. Our commitment to innovation and excellence ensures that our clients are well-equipped to meet the growing market demands and contribute to a sustainable energy future. The global lithium-ion battery (LIB) market is currently witnessing unparalleled growth, fueled by the surging demand for electric vehicles, portable electronics, and renewable energy storage systems. To maintain a competitive edge in this dynamic environment, manufacturers need to adopt innovative technologies and enhance their production methodologies. Our company provides a diverse array of solutions that transform LIB production. We offer comprehensive turnkey solutions alongside cutting-edge production machinery tailored for battery material manufacturing, including LCO, LFP, NCM, NCA, silicon anode, and graphite anodes. Additionally, our expertise extends to advanced processes for electrode production, cell assembly, and essential charging/discharging inspection. By integrating these services, we empower manufacturers to streamline their operations and meet the growing market demands effectively.
Energy Storage Battery Aging Cabinet
The ESS Battery Module PACK Aging Cabinet is specifically designed to evaluate the aging characteristics of energy storage battery modules and packs.
Product description
1. Equipment Overview
The ESS Battery Module PACK Aging Cabinet is specifically designed to evaluate the aging characteristics of energy storage battery modules and packs. This cabinet simulates long-term use conditions by performing charge and discharge cycles to assess capacity fade, efficiency degradation, and thermal stability over time. The system is engineered for ESS applications, ensuring quality and reliability for modules and packs.
2. Key Features
Precise Aging Simulation: Conducts controlled charge/discharge cycles for aging evaluation.
High Channel Capacity: Supports simultaneous testing of multiple modules or packs.
Real-Time Monitoring: Tracks electrical and thermal parameters during aging cycles.
Data Integration: MES-compatible for centralized tracking and traceability.
Safety-Certified: Features robust safety mechanisms to handle ESS modules and packs
3. Technical Specifications
3.1 Module/PACK Compatibility
Supported Formats:
ESS Prismatic Battery Modules.
ESS Cylindrical Battery Packs.
ESS Pouch Battery Packs.
Dimensions:
Minimum: 200 × 150 × 50 mm.
Maximum: 1,500 × 1,000 × 300 mm.
Weight Capacity per Module/PACK: Up to 50 kg.
3.2 Electrical Testing Parameters
Voltage Range: 0–1,000 V.
Voltage Accuracy: ±0.05%.
Current Range: 0–300 A (customizable).
Current Accuracy: ±0.1%.
Capacity Range: 0–300 Ah per channel
3.3 Testing Modes
Charge/Discharge Profiles:
Constant Current (CC).
Constant Voltage (CV).
Constant Power (CP).
Dynamic Load Profiles.
Cycle Testing: Configurable cycles for capacity fade and efficiency evaluation.
Rest Period Simulation: Adjustable periods to
Energy Storage Battery Aging Cabinet
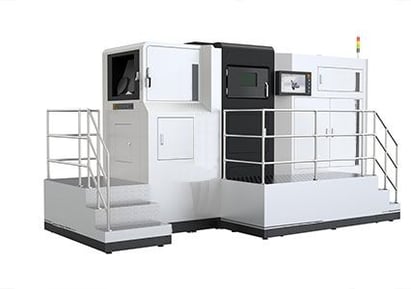
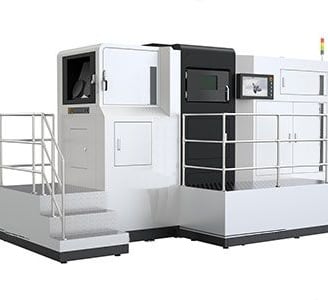
Energy Storage Battery Performance Testing
The ESS Battery Cell Performance Testing Cabinet is a high-precision system designed to evaluate the electrical and thermal performance of energy storage system (ESS) battery cells.
Product description
1. Equipment Overview
The ESS Battery Cell Performance Testing Cabinet is a high-precision system designed to evaluate the electrical and thermal performance of energy storage system (ESS) battery cells. It conducts a comprehensive analysis of capacity, efficiency, thermal behavior, and durability under varied operational conditions. The cabinet is engineered to ensure reliability and consistency for cells used in ESS applications.
2. Key Features
Comprehensive Testing: Supports multi-parameter evaluation including voltage, current, capacity, resistance, and temperature.
Wide Compatibility: Accommodates prismatic, pouch, and cylindrical battery cells.
High Precision: Accurate and repeatable testing results.
Flexible Testing Profiles: Customizable charge/discharge and stress cycle programs.
Integrated Data Management: MES and ERP compatible for real-time monitoring and traceability.
3. Technical Specifications
3.1 Cell Compatibility
Cell Types: Prismatic, cylindrical, pouch.
Cell Dimensions:
Prismatic: 50 × 20 × 70 mm to 300 × 100 × 400 mm.
Cylindrical: 18650, 21700, 4680.
Pouch: 50 × 50 mm to 300 × 500 mm.
3.2 Measurement and Testing Capabilities
Voltage Measurement:
Range: 0–5 V.
Accuracy: ±0.005 V.
Current Measurement:
Range: 0.1–300 A.
Accuracy: ±0.05%.
Capacity Testing:
Range: 0–500 Ah.
Accuracy: ±0.1%.
Internal Resistance Testing:
Range: 0.01–50 mΩ.
Accuracy: ±0.1 mΩ.
3.3 Testing Profiles
Charge/Discharge Modes:
Constant Current (CC).
Constant Voltage (CV).
Constant Power (CP).
Programmable Cycles: Up to 1,000 customizable cycles per test.
Testing Speed: Adjustable based on cell specifications and parameters
3.4 Thermal Monitoring and Control
Temperature Range: 15–80°C (adjustable).
Temperature Accuracy: ±1°C.
Thermal Chamber Integration: Optional environmental chamber for high/low-temperature performance testing.
3.5 System Capacity
Channels:
Standard: 64–128 channels (expandable).
Independent control for each channel.
Throughput: Up to 1,000 cells/day depending on configuration
3.6 Data Management
Data Logging: Real-time acquisition of voltage, current, capacity, and resistance data.
Traceability: Full history stored with unique serial numbers for each cell.
Report Generation: Automated reports with graphical and tabular analysis.
Integration: Compatible with MES/ERP systems for centralized data management
3.7 Automation and Control
HMI: Touchscreen interface for user-friendly operation.
Control System: PLC-based with real-time monitoring.
Programmable Recipes: Customizable profiles for different cell chemistries and specifications.
3.8 Safety Features
Overcurrent Protection: Automatic shutdown in case of abnormal current.
Overvoltage Protection: Stops testing if voltage exceeds safe thresholds.
Temperature Alarms: Alerts for overheating or deviations from set ranges.
Emergency Stop: Accessible buttons for immediate operation termination.
3.9 Mechanical Design
Dimensions: 2,000 × 1,200 × 1,800 mm (customizable).
Weight: Approximately 1,800 kg.
Cooling System: Integrated air circulation for stable operation.
3.10 Power Requirements
Input Voltage: AC 380V ±10%, 50/60 Hz, 3-phase.
Power Consumption: ≤60 kW
3.11 Environmental Requirements
Operating Temperature: 15–35°C.
Humidity: ≤70% RH (non-condensing).
Cleanliness: Dust-free environment recommended for optimal performance.
4. Applications
Energy Storage Systems (ESS): Performance testing for cells used in large-scale storage systems.
Renewable Energy Storage: Validation of cells for solar and wind power systems.
Electric Vehicles (EV): Supplemental performance evaluation for ESS-grade cells.y
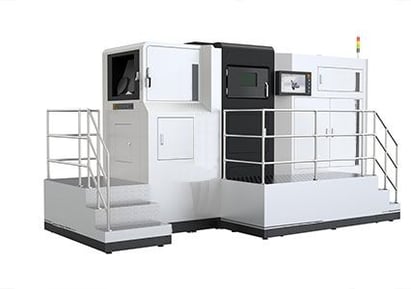
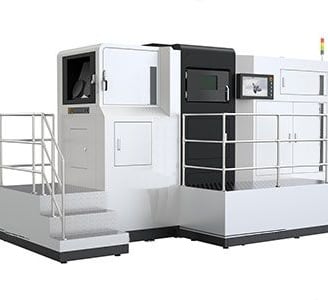
Energy Storage Battery Performance Testing
ESS Battery PACK End-of-Line (EOL) Testing System
The ESS Battery Module PACK End-of-Line (EOL) Testing System is a comprehensive solution for validating the final quality and performance of energy storage system (ESS) battery modules and PACKs.
The ESS Battery Module PACK End-of-Line (EOL) Testing System is a comprehensive solution for validating the final quality and performance of energy storage system (ESS) battery modules and PACKs. Designed to simulate real-world operational scenarios, this system ensures each module or PACK meets stringent industry standards before deployment. The system supports high-accuracy testing, data analysis, and efficient testing workflows for large-scale production environments.
1. Equipment Overview
The ESS Battery Module PACK End-of-Line (EOL) Testing System is a comprehensive solution for validating the final quality and performance of energy storage system (ESS) battery modules and PACKs. Designed to simulate real-world operational scenarios, this system ensures each module or PACK meets stringent industry standards before deployment. The system supports high-accuracy testing, data analysis, and efficient testing workflows for large-scale production environments.
3. Technical Specifications
3.1 Module/PACK Compatibility
Supported Formats: Prismatic, pouch, and cylindrical module/PACK configurations.
Size Range:
Minimum: 300 × 200 × 50 mm.
Maximum: 1,500 × 1,000 × 300 mm.
Weight Capacity: Up to 200 kg per module/PACK.
3.2 Electrical Testing Parameters
Voltage Testing:
Range: 0–1,000 V.
Accuracy: ±0.05%.
Current Testing:
Range: 0–500 A.
Accuracy: ±0.1%.
Capacity Testing:
Range: 0–1,000 Ah.
Accuracy: ±0.1%.
Internal Resistance Testing:
Range: 0.01–50 mΩ.
Accuracy: ±0.05 mΩ.
3.3 Functional Testing
Key Parameters Evaluated:
Overvoltage/undervoltage protection.
Overcurrent/short-circuit protection.
Temperature monitoring performance.
SOC (State of Charge) and SOH (State of Health) accuracy.
Insulation resistance and dielectric strength.
Cycle Testing: Supports multiple charge/discharge cycles to simulate long-term operation.
3.4 System Capacity
Parallel Channels: 8–32 channels (configurable).
Testing Throughput: Up to 20 modules or PACKs per batch (depending on size and configuration).
3.5 Data Management
Real-Time Monitoring: Tracks voltage, current, resistance, and thermal behavior during tests.
Traceability: Unique ID tracking for each module/PACK.
Data Logging: High-resolution data storage for performance analysis and fault diagnosis.
Reporting: Automated generation of customizable test reports.
Integration: Compatible with MES/ERP systems for centralized monitoring and analysis.
3.6 Control System
HMI: 12-inch touchscreen for user-friendly operation.
Software: Advanced testing software with customizable profiles and real-time monitoring.
Communication Protocols: CAN, RS485, RS232, and Ethernet for interfacing with BMS.
3.7 Safety Features
Electrical Protection: Overcurrent, overvoltage, and short-circuit protections.
Thermal Monitoring: Alerts for overheating or thermal deviations.
Emergency Shutdown: Physical and software-activated emergency stop functions.
Fire Suppression: Optional fire suppression system for high-capacity modules/PACKs.
3.8 Mechanical Design
Dimensions: 2,500 × 1,500 × 2,200 mm (customizable).
Weight: Approximately 3,000 kg.
Cabinet Structure: Modular design for efficient testing and maintenance.
Cooling System: Integrated forced-air cooling or optional liquid cooling for high-capacity tests.
3.9 Power Requirements
Input Voltage: AC 380V ±10%, 50/60 Hz, 3-phase.
Power Consumption: ≤120 kW.
3.10 Environmental Requirements
Operating Temperature: 15–35°C.
Humidity: ≤70% RH (non-condensing).
Environment: Clean and dust-free area recommended for optimal operation.
4. Applications
Energy Storage Systems (ESS): Final validation for battery modules and PACKs used in grid stabilization and renewable energy storage.
Commercial and Industrial ESS: Ensures compliance with quality standards for large-scale deployments.
Renewable Energy Integration: Tests modules and PACKs designed for solar and wind energy storage systems..
ESS Battery PACK End-of-Line (EOL) Testing System
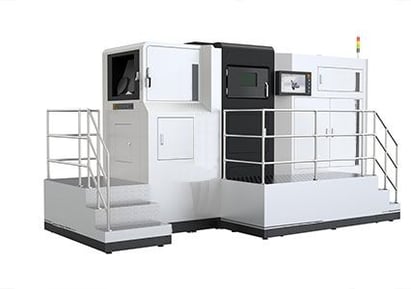
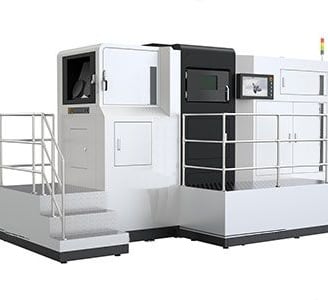
ESS Battery Module PACK BMS Testing System
The ESS Battery Module PACK BMS Testing System is designed to evaluate the functionality, performance, and reliability of Battery Management Systems (BMS) used in energy storage system (ESS) modules and packs.
Product description
1. Equipment Overview
The ESS Battery Module PACK BMS Testing System is designed to evaluate the functionality, performance, and reliability of Battery Management Systems (BMS) used in energy storage system (ESS) modules and packs. It ensures proper communication, safety, and efficiency of the BMS, which is crucial for maintaining battery health and preventing malfunctions in ESS applications.
2. Key Features
Comprehensive BMS Testing: Verifies communication, protection mechanisms, balancing performance, and more.
Protocol Compatibility: Supports common BMS communication protocols such as CAN, RS485, RS232, and Ethernet.
Customizable Testing Profiles: Tailored to ESS application needs and BMS specifications.
High Accuracy and Speed: Precise simulation of real-world operating conditions.
Integrated Data Management: Facilitates seamless data collection, analysis, and reporting.
3. Technical Specifications
3.1 BMS Communication Testing
Supported Protocols:
CAN 2.0A/2.0B, CAN FD.
RS485, RS232.
Ethernet TCP/IP.
Communication Speed:
CAN: Up to 1 Mbps.
Ethernet: Up to 1 Gbps.
Addressable Nodes: Up to 256 nodes.
3.2 Electrical Testing Parameters
Voltage Simulation:
Range: 0–1,000 V.
Accuracy: ±0.05%.
Current Simulation:
Range: 0–300 A.
Accuracy: ±0.1%.
Cell Balancing Testing:
Range: 0–500 mA.
Accuracy: ±0.05%.
Thermal Simulation:
Temperature Range: -20°C to 80°C (optional).
3.3 Functional Testing
Key Functions Verified:
Overvoltage/undervoltage protection.
Overcurrent/short-circuit protection.
Temperature monitoring and control.
SOC (State of Charge) and SOH (State of Health) algorithms.
Fault diagnosis and alert mechanisms.
Cycle Testing:
Simulates real-world charge and discharge cycles to validate performance.
3.4 System Capacity
Parallel Channels:
Standard: 16–64 channels (expandable).
Independent operation for each channel.
Maximum Packs Tested Simultaneously: Up to 50 (depending on configuration).
3.5 Data Management
Data Logging: Real-time recording of voltage, current, temperature, and communication logs.
Traceability: Unique ID tracking for each BMS module.
Reporting: Automated generation of detailed test reports.
Integration: MES/ERP-compatible for centralized data management.
3.6 Control System
HMI: 10.1-inch touchscreen for intuitive operation.
Control Platform: PLC/PC-based for reliable control and automation.
Customizable Test Profiles: Preloaded and user-defined profiles for various ESS applications.
3.7 Safety Features
Electrical Protections: Overcurrent, overvoltage, and short-circuit protections.
Thermal Monitoring: Integrated sensors to detect and alert temperature anomalies.
Emergency Shutdown: Accessible buttons to terminate testing immediately.
Isolation Design: Ensures safety between channels during testing.
3.8 Mechanical Design
Dimensions: 2,000 × 1,200 × 2,000 mm (customizable).
Weight: Approximately 2,000 kg.
Cabinet Structure: Modular design for ease of operation and maintenance.
Cooling System: Forced-air or liquid cooling for stable operation.
3.9 Power Requirements
Input Voltage: AC 380V ±10%, 50/60 Hz, 3-phase.
Power Consumption: ≤50 kW.
3.10 Environmental Requirements
Operating Temperature: 15–35°C.
Humidity: ≤70% RH (non-condensing).
Clean Environment: Dust-free and vibration-free area recommended
4. Applications
Energy Storage Systems (ESS): Ensures optimal performance of BMS for grid-scale storage.
Renewable Energy Storage: Validates BMS for solar and wind power integration.
Industrial and Commercial ESS: Supports testing for BMS in large-scale projects.
ESS Battery Module PACK BMS Testing System
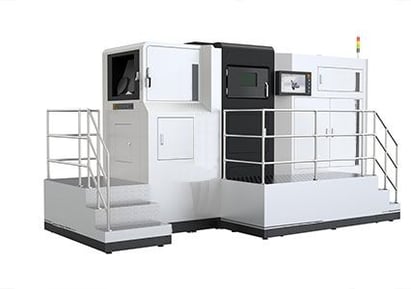
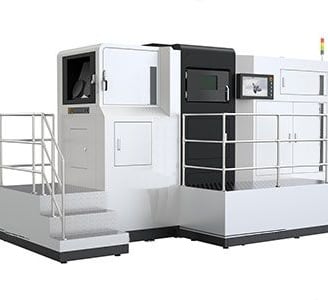