Lithium Battery Assembly
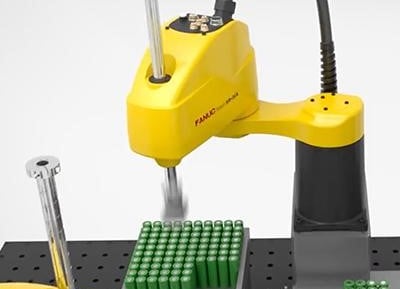
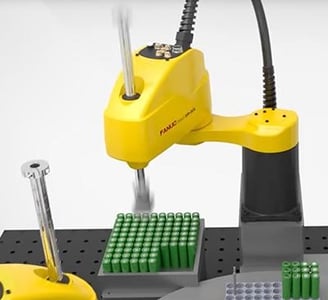
The ESS prismatic battery module pack assembly line is a cutting-edge solution designed to enhance the manufacturing process of energy storage system (ESS) prismatic battery packs. This assembly line is built for high precision and throughput, ensuring that each battery pack meets the rigorous standards of today's energy demands. With a focus on scalability and flexibility, it integrates advanced automation and robotics, allowing for streamlined operations and increased efficiency. Furthermore, the inclusion of robust quality control mechanisms ensures that every unit produced adheres to the highest quality specifications, ultimately delivering superior reliability and performance. This innovative assembly line is poised to meet the growing needs of the energy storage market, making it an essential asset for manufacturers aiming to excel in a competitive landscape. The EV cylindrical battery module pack assembly line represents a significant advancement in automated production technology, specifically tailored for the efficient assembly of cylindrical cells into battery modules and packs. This comprehensive system includes various stages such as cell sorting, grouping, module assembly, electrical interconnection, testing, and final pack assembly. Each of these stages is designed to ensure high precision and reliability, making it ideal for electric vehicle applications. The assembly line boasts flexible configurations that can adapt to diverse production needs, while also facilitating effective traceability throughout the manufacturing process. This optimization not only enhances productivity but also guarantees that the final battery packs meet stringent quality standards, thereby supporting the ever-growing demand for reliable electric vehicle power sources.
Assembly Process For Cylindrical, Square And Prismatic Batteries
General processes for every type of batteries
Electrolyte Filling (Liquid Electrolyte)
In traditional lithium-ion batteries using liquid electrolytes, the electrolyte injection process is a critical step. An opening or port is created in the battery casing to facilitate this. The liquid electrolyte, a lithium salt dissolved in a solvent, is injected into the cell through this opening. The specific electrolyte composition can vary depending on the battery design and intended application.
Venting and Degasification
After electrolyte injection in both liquid and solid-state batteries, a degasification process is often conducted to remove any remaining gas or air from the cell. This ensures that the cell is properly filled with electrolyte. Venting may also be performed to release any excess gas produced during the formation process.
Sealing the Battery
Once the battery is filled with the appropriate electrolyte and any excess gas has been vented, the next step is sealing the battery. The sealing process is critical for preventing electrolyte leakage and maintaining the integrity of the battery. The sealing methods may vary depending on the battery type (cylindrical, square, prismatic) and the manufacturer’s techniques.
Cylindrical Batteries
For cylindrical batteries, the open end of the cell is typically crimped or welded to seal it. This creates a hermetic seal, preventing the escape of electrolyte and ensuring the battery is airtight.
Square and Prismatic Batteries
Square and prismatic batteries are sealed using a combination of methods, including welding, adhesive bonding, and heat-sealing. These techniques are employed to achieve a secure seal that prevents electrolyte leakage and gas ingress.
Assembly Process For Cylindrical, Square And Prismatic Batteries
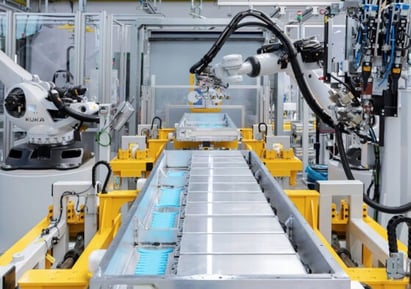
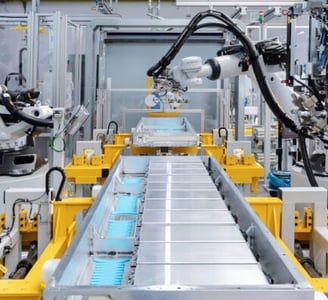
Energy Storage Battery Cell Capacity Grading
The ESS Battery Cell Capacity Grading Cabinet is a high-precision system designed for grading energy
Product description
1. Equipment Overview
The ESS Battery Cell Capacity Grading Cabinet is a high-precision system designed for grading energy storage battery cells based on their capacity, voltage, and internal resistance. This equipment is optimized for ESS applications and ensures consistent quality and performance by identifying cells with similar characteristics for balanced module and pack assembly.
2. Key Features
High Precision: Accurate measurement of cell parameters for optimal grading.
Multi-Channel Testing: Simultaneous testing of multiple cells to enhance throughput.
Flexible Compatibility: Supports various cell formats, including prismatic, pouch, and cylindrical.
Data Integration: MES-compatible for real-time data tracking and traceability.
Safety Assurance: Comprehensive safety features, including temperature monitoring and fault alarms.
3. Technical Specifications
3.1 Cell Compatibility
Cell Types: Prismatic, cylindrical, pouch.
Cell Dimensions:
Prismatic: 50 × 20 × 70 mm to 300 × 100 × 400 mm.
Cylindrical: 18650, 21700, 4680.
Pouch: 50 × 50 mm to 300 × 500 mm.
3.2 Measurement Capabilities
Voltage Measurement:
Range: 0–5 V.
Accuracy: ±0.005 V.
Current Measurement:
Range: 0.1–200 A.
Accuracy: ±0.05%.
Capacity Measurement:
Range: 0–500 Ah.
Accuracy: ±0.1%.
Internal Resistance Measurement:
Range: 0.01–50 mΩ.
Accuracy: ±0.1 mΩ.
3.3 Grading Parameters
Sorting Criteria: User-defined thresholds for capacity, voltage, and resistance.
Grading Groups: Up to 16 classification levels for precise grouping.
3.4 Testing Modes
Charge/Discharge Cycle: Programmable current profiles for realistic performance evaluation.
Constant Current (CC): Stable current for capacity grading.
Constant Voltage (CV): Stabilized voltage for cell calibration
3.5 System Capacity
Channel Count: 64–256 independent channels (expandable).
Testing Throughput: Up to 1,000 cells per day.
Cycle Time: Adjustable based on cell specifications and testing profiles
3.6 Data Management
Data Acquisition: Real-time logging of cell performance data.
Traceability: Unique serial number tracking for each cell.
Integration: MES and ERP system compatibility for centralized data management.
Reporting: Automated generation of grading reports and analysis charts.
3.7 Control System
HMI: Intuitive touchscreen interface for operation and monitoring.
PLC: Reliable control system for precise testing and safety management.
Alarm System: Visual and audible alerts for fault conditions.
3.8 Safety Features
Overcurrent Protection: Automatic shutdown for abnormal current levels.
Overvoltage Protection: Prevents damage to cells due to excessive voltage.
Thermal Monitoring: Real-time temperature monitoring with alerts.
Emergency Stop: Accessible emergency stop buttons for immediate power cutoff
3.9 Mechanical Design
Cabinet Dimensions: 2,000 × 1,200 × 1,800 mm (customizable).
Weight: Approximately 1,500 kg.
Cooling System: Integrated forced-air cooling for stable operation.
3.10 Power Requirements
Input Voltage: AC 380V ±10%, 50/60 Hz, 3-phase.
Power Consumption: ≤50 kW.
3.11 Environmental Requirements
Operating Temperature: 15–35°C.
Humidity: ≤70% RH (non-condensing).
Cleanliness: Dust-free environment recommended for optimal performance.
4. Applications
Energy Storage Systems (ESS): Cell grading for large-scale battery storage applications.
Renewable Energy: Grading cells for solar and wind power storage solutions.
Electric Vehicles (EV): Pre-assembly quality assurance for high-capacity cells
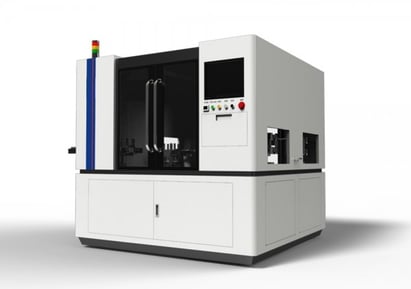
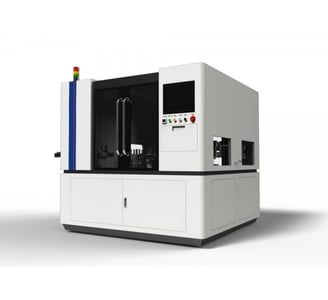
Energy Storage Battery Cell Capacity Grading
Cylindrical Battery Module PACK Assembly Line
The EV Cylindrical Battery Module PACK Assembly Line is a fully automated production system designed for efficient assembly of cylindrical cells into battery modules and packs.
Product description
1. Equipment Overview
The EV Cylindrical Battery Module PACK Assembly Line is a fully automated production system designed for efficient assembly of cylindrical cells into battery modules and packs. It incorporates cell sorting, grouping, module assembly, electrical interconnection, testing, and PACK assembly to ensure high precision, traceability, and reliability. This line is optimized for EV applications with flexible configurations and integrated quality assurance systems.
2. Key Features
High Throughput: Fully automated line ensures consistent production efficiency.
Flexibility: Supports various cylindrical cell sizes (e.g., 18650, 21700, 4680).
Precision Welding: Advanced laser welding for interconnect reliability.
Quality Assurance: Inline testing and inspection at multiple stages.
Smart Integration: MES system compatibility for real-time data and process control.
3. Technical Specifications
3.1 Cell Sorting and Grouping
Sorting Accuracy:
Voltage: ±0.01 V.
Capacity: ±0.1 Ah.
Internal Resistance: ±0.1 mΩ.
Sorting Capacity: Up to 1,200 cells/hour.
Grouping Strategy: Automatic grouping by voltage, capacity, and resistance for balanced modules.
3.2 Module Assembly
Cell Arrangement: Supports various configurations, including parallel and series arrangements.
Fixture Accuracy: ±0.2 mm alignment for cylindrical cells.
Adhesive Application: Automated dispensing of thermal adhesive for structural integrity and heat dissipation.
Cycle Time: ≤40 seconds/module.
3.3 Electrical Interconnection
Connection Method:
Laser welding for busbar connections.
Optional ultrasonic welding for tab-to-tab connections.
Welding Precision: ±0.1 mm.
Busbar Material: Nickel or copper with optional conductive coatings.
Conductivity: ≤0.2 mΩ per connection.
3.4 PACK Assembly
PACK Design:
Customizable configurations for EV applications (e.g., 8s1p, 16s2p, etc.).
Casing Assembly: Automatic alignment and fastening of PACK enclosures.
Thermal Management Integration:
Liquid cooling plates or air-cooling channels added during assembly.
3.5 Integrated Testing and Inspection
Inline Testing:
Voltage, current, and internal resistance measurement.
Welding strength verification.
High-Pot Testing:
Cylindrical Battery Module PACK Assembly Line
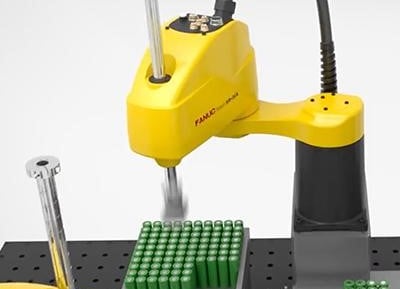
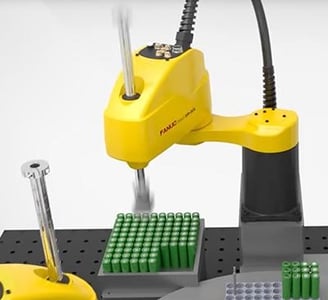
Prismatic Battery Module PACK Assembly Line
The ESS Prismatic Battery Module PACK Assembly Line is engineered to deliver high-precision, high-throughput manufacturing of energy storage system (ESS) prismatic battery packs.
Product description
1. Technical Introduction: ESS Prismatic Battery Module PACK Assembly Line
The ESS Prismatic Battery Module PACK Assembly Line is engineered to deliver high-precision, high-throughput manufacturing of energy storage system (ESS) prismatic battery packs. Designed for scalability, flexibility, and optimal performance, the line incorporates advanced automation, robotics, and integrated quality control mechanisms to meet the stringent requirements of modern ESS applications, which demand superior reliability, safety, and efficiency.
2. Process Flow and Technical Overview:
2.1 Thermal Interface Material (TIM) Insertion
Process: Automated dispensing systems insert a consistent layer of TIM at the bottom of the prismatic battery box.
Technical Detail:
The TIM is precisely dispensed to ensure uniform thickness and full coverage, ensuring optimal heat dissipation between the prismatic cells and the battery housing. This is critical for maintaining battery performance and longevity under load conditions.
2.2 Module Insertion and Alignment
Process: High-precision handling systems load prismatic battery modules into the battery box, ensuring proper orientation and mechanical alignment.
Technical Detail: Automated feeders, combined with vision systems, ensure that each module is aligned to within ±0.1mm accuracy to avoid misalignment issues during assembly. The modules are secured within the box using automated pressing mechanisms to ensure even distribution of mechanical forces.
2.3 Glue Application for Top Cover Assembly
Process: Precision glue dispensers apply an even layer of adhesive to the top of the battery box for secure attachment of the top cover.
Technical Detail: The glue dispensing system is calibrated for precise volume control, applying the correct adhesive amount for a uniform bond. This system is integrated with a real-time vision inspection system to verify glue pattern and volume consistency, ensuring a strong bond that adheres to industry standards.
2.4 Top Cover Mounting
Process: The top cover of the battery box is mounted automatically using robotic arms, followed by fastening using high-torque screwdrivers.
Technical Detail: Robotic arms (such as KUKA models) are programmed to handle the top cover, aligning it precisely with the battery box using vision-guided systems. Fastening is performed with torque-controlled screwdrivers to ensure consistent sealing pressure and to prevent over-tightening or under-tightening, which could compromise pack integrity.
2.5 End-of-Line (EOL) Testing
Process: Once the module is assembled, it undergoes a series of automated tests at the EOL station.
Technical Detail: The EOL testing station is equipped with electrical testing units that check key parameters such as voltage, capacity, impedance, and thermal behavior. Advanced diagnostic equipment performs high-voltage insulation resistance tests, overcharge/discharge simulations, and short-circuit fault injections to ensure that each module adheres to strict performance and safety standards. These tests ensure compliance with UL, IEC, and other international safety certifications.
2.6 Labelling and Custom Branding
Process: The final step involves labelling the completed battery pack with customer-specific branding and serial numbers.
Technical Detail: A fully automated labelling system uses high-precision printers and robotic placement arms to apply labels accurately and securely. The label includes critical information, such as battery specifications, date codes, and safety warnings, as required for traceability and compliance purposes.
3. Automation, Robotics, and Quality Control Systems:
Robotic Arms and Automated Handling Systems:
The line utilizes a series of KUKA robotic arms, equipped with advanced vision systems and end-of-arm tooling (EOAT), for tasks including module handling, glue application, top cover assembly, and pack transfer. The robotic arms are configured for high payload capacity, speed, and flexibility, with precision repeatability of ±0.05mm to ensure optimal alignment and assembly.
Vision Inspection and Error Detection:
Integrated vision systems, such as high-resolution cameras and laser sensors, continuously monitor every step of the assembly process. These systems perform real-time quality inspections, verifying module placement, adhesive application, alignment, and torque settings. Any deviations from the predefined tolerances trigger automatic alerts and corrections to maintain production quality.
Conveyor Systems and Centralized Control:
The assembly line employs high-speed conveyor systems with modular design for flexible line configuration. A centralized PLC-based control system manages the entire process, ensuring synchronized operation between various stations. Real-time data monitoring and analytics allow for predictive maintenance, minimizing downtime and improving operational efficiency.
4. Technical Advantages:
High Precision and Repeatability:
The use of robotics, vision-guided systems, and automated handling ensures that each module and pack assembly is executed with consistent precision, meeting tolerances of up to ±0.1mm in alignment and ±0.5% in component placement.
Throughput and Scalability:
The assembly line is designed for high throughput, capable of producing thousands of ESS prismatic battery packs per day. The modular design allows easy scalability for different production volumes, accommodating both small-batch and mass production needs.
Advanced Safety and Compliance:
The entire line is built with safety protocols aligned with international standards (e.g., ISO 26262, IEC 61508). This includes automated safety stops, emergency shutoff systems, and real-time monitoring of electrical, mechanical, and environmental parameters to safeguard against potential hazards during the assembly process.
Flexibility for Custom Configurations:
The line is highly adaptable, capable of handling multiple prismatic battery sizes and configurations. Whether dealing with different voltages (e.g., 12V, 48V) or customized pack designs, the system can be reconfigured rapidly with minimal downtime.
Cost Efficiency and Reduced Labour Dependency:
With a fully automated workflow, labour costs are reduced, and the risk of human error is minimized, ensuring optimal performance and cost-effective production.
5. Conclusion:
The ESS Prismatic Battery Module PACK Assembly Line represents the next generation of automation in energy storage system manufacturing. By integrating advanced robotics, automated quality control, and high-precision assembly techniques, it offers manufacturers a robust, scalable solution for producing high-quality prismatic battery packs with reduced cycle times, enhanced safety, and compliance with international standards. This assembly line supports the growing demand for reliable, efficient energy storage solutions across a variety of industries, including renewable energy, electric vehicles, and grid stabilization
Prismatic Battery Module PACK Assembly Line
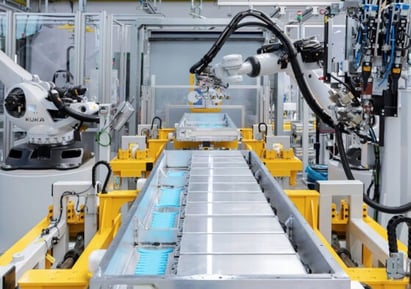
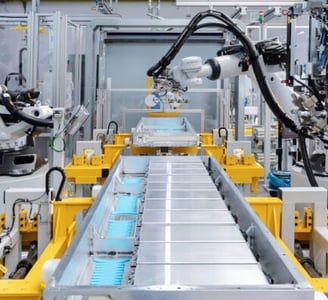
EV Blade Battery CTP Automatic Welding Line
Automatically feeds blade cells into the line and ensures precise alignment for welding.
Product description
1. Equipment Overview
The EV Blade Battery CTP (Cell-to-Pack) Automatic Welding Line is a cutting-edge automated solution tailored for the direct assembly of blade battery cells into robust packs without intermediate modules. This line combines high-precision handling, advanced laser welding, and quality inspection systems to ensure efficient, high-throughput production while meeting the demanding safety and performance requirements of EV batteries.
2. Key Processes and Modules
2.1 Automatic Blade Cell Feeding and Positioning Station
Function: Automatically feeds blade cells into the line and ensures precise alignment for welding.
Specifications:
Cell Size Range: Length 400–1,200 mm, Width 80–150 mm, Thickness 10–40 mm.
Positioning Accuracy: ±0.2 mm.
Cycle Time: ≤8 seconds per cell.
2.2 Cell-to-Bus bar Laser Welding Station
Function: Performs high-precision laser welding to connect blade cell terminals to the busbar.
Specifications:
Welding Power: 600–1,500 W ( Fiber laser).
Welding Accuracy: ±0.05 mm.
Cycle Time: ≤5 seconds per weld.
Real-Time Monitoring: Inline monitoring system for weld quality with defect detection.
2.3 Thermal Management System Installation Station
Function: Installs cooling plates and applies thermal interface materials (TIM) to ensure efficient heat dissipation.
Specifications:
TIM Application Accuracy: ±0.1 mm.
Cooling Plate Compatibility: Liquid or air-cooling systems.
Cycle Time: ≤20 seconds per assembly.
2.4 Structural Bonding and Frame Assembly Station
Function: Bonds and assembles the structural frame around the blade cells for mechanical stability.
Specifications:
Adhesive Type: Epoxy or UV-curable adhesive.
Bonding Accuracy: ±0.2 mm.
Frame Material: Aluminum or composite material.
2.5 High-Voltage Bus bar and Connector Welding Station
Function: Welds high-voltage connectors and bus bars to create electrical paths between cells and the pack.
Specifications:
Welding Type: Laser or ultrasonic.
Welding Accuracy: ±0.05 mm.
Voltage Handling Capacity: Up to 1,000V DC.
Cycle Time: ≤10 seconds per connection.
2.6 PACK Assembly and Sealing Station
Function: Assembles multiple blade modules into the pack housing and seals it to protect against environmental factors.
Specifications:
Sealant Material: Silicone or polymer gaskets.
Assembly Accuracy: ±0.3 mm.
Cycle Time: ≤3 minutes per PACK.
2.7 Electrical and Safety Testing Station
Function: Conducts comprehensive testing for electrical performance, insulation, and leakage.
Specifications:
Test Parameters: Voltage, resistance, insulation, short circuit, and leakage current.
Helium Leak Detection: Sensitivity ≤1x10⁻⁶ Pa·m³/s.
Testing Speed: ≤2 minutes per PACK.
2.8 Final Visual Inspection and Quality Assurance Station
Function: Automated inspection of weld quality, assembly alignment, and surface defects.
Specifications:
Vision System Resolution: 8 MP industrial cameras.
Inspection Speed: ≤1 minute per PACK.
AI Algorithm Accuracy: ±0.05 mm for defect detection.
3. Production Line Specifications
Overall Dimensions:
Length: 85,000 mm.
Width: 12,000 mm.
Height: 4,000 mm.
Weight: Approximately 55,000 kg.
Production Capacity: 12–15 PACKs/hour.
Automation Level: Fully automated with robotic handling and AI-powered monitoring.
4. Vision and Quality Control Systems
Defect Detection: AI-driven system for weld and assembly defect detection.
Data Logging: Centralized database for traceability and production analytics.
Inspection Accuracy: ±0.05 mm for weld and surface defects.
5. Control and Interface
Control System: Distributed PLC and HMI for centralized operation.
HMI Features:
17-inch touchscreen with multilingual support.
Real-time monitoring and diagnostics.
IoT Integration: Remote access for predictive maintenance and data analysis.
6. Safety Features
Enclosure Design: Fully enclosed with interlocks for safety.
Emergency Stops: Strategically placed along the line.
Laser Safety: Class 1 certified enclosures with auto shutdown on fault detection.
Electrical Protection: Surge and overcurrent protection systems.
7. Electrical Specifications
Power Supply: AC 380V ±10%, 50/60 Hz, 3-phase.
Maximum Power Consumption: 320 kW.
Control Voltage: 24V DC for auxiliary systems.
8. Cooling System
Type: Centralized water cooling for welding and power systems.
Cooling Capacity: 150 kW.
Flow Rate: 40–60 L/min.
9. Environmental Requirements
Operating Conditions:
Temperature: 15–30°C.
Humidity: ≤60% RH (non-condensing).
Noise Level: ≤75 dB during operation.
Installation Space: Minimum clearance of 2,000 mm around the line.
EV Blade Battery CTP Automatic Welding Line
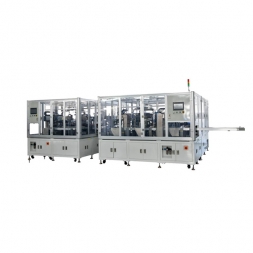
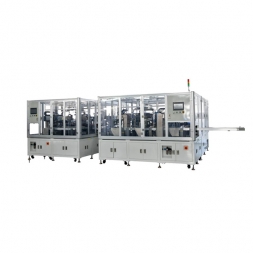
Battery Laser Welding
Precise welding of top caps onto battery cases, ensuring airtight sealing and electrical connectivity for prismatic and pouch batteries.
Product description
1. Equipment Overview
Equipment Name: Battery Top Cap Welding Equipment
Application: Precise welding of top caps onto battery cases, ensuring airtight sealing and electrical connectivity for prismatic and pouch batteries.
2. Mechanical Specifications
Equipment Dimensions:
Length: 1500 mm xWidth: 1200 mmx Height: 2100 mm
Frame Material: High-strength steel frame with powder coating for durability.
Worktable Material: Anodized aluminum with anti-static and wear-resistant surface.
Motion System: Precision servo-driven X-Y-Z axes with linear guide rails.
3. Welding Specifications
Welding Technology:
Laser Welding (standard).
Laser Type: Fiber laser, 1064 nm wavelength.
Laser Power: 500–3000 W (adjustable).
Welding Speed: 150mm/s (process-dependent).
Welding Spot Size: 0.1–0.5 mm (configurable).
Welding Accuracy: ±0.03 mm.
Material Compatibility:
Top Cap Materials: Aluminum, nickel, and copper.
Battery Case Materials: Aluminum and stainless steel.
4. Vision and Alignment System
Alignment Accuracy: ±0.02 mm.
Camera Specifications:
Resolution: 5 MP industrial-grade CCD camera.
Field of View: Adjustable for varying cap sizes.
Lighting System: Adjustable LED illumination for enhanced visibility.
Inspection Features:
Pre-weld alignment and cap placement verification.
Post-weld inspection for seam integrity and defects.
5. Control and Interface
Control System: Welding control card based with integrated HM
19-inch display with vital user interface.
Multi-language support (English, Chinese, others).
Programmable Parameters:
Laser power, duration, and focus.
Welding patterns and sequences.
Recipe storage for various battery models.
Data Logging:
Internal Capacity: 1 TB SSD for process history.
Export Formats: CSV and PDF via USB, Ethernet, or Wi-Fi.
6. Electrical Specifications
Power Supply: AC 220V ± 10%, 50/60 Hz.
Maximum Power Consumption: 18 kW.
Control Voltage: 24V DC for auxiliary systems.
7. Safety Features
Emergency Stop: Emergency stop buttons on all accessible panels.
Overload Protection: Real-time monitoring of force and welding power.
Laser Safety: Fully enclosed Class 1 laser operation with interlock systems.
Protective Barriers: Transparent enclosure with safety interlocks for operator protection.
Error Detection: Audible and visual alarms for misalignment, overheating, or defective welds.
.9. Cooling System
Type: Water-cooled laser module with independent chiller.
Flow Rate: 10–15 L/min.
Cooling Power: 3.5 kW.
as
Battery Laser Welding
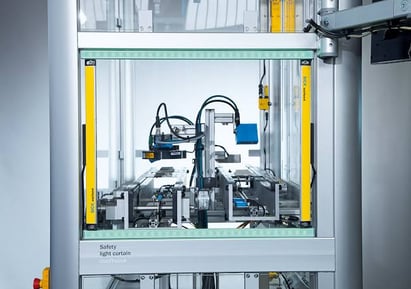
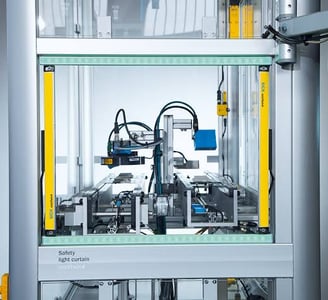
Energy Storage Battery Cell Capacity Grading
The ESS Battery Cell Capacity Grading Cabinet is a high-precision system designed for grading energy
Product description
1. Equipment Overview
The ESS Battery Cell Capacity Grading Cabinet is a high-precision system designed for grading energy storage battery cells based on their capacity, voltage, and internal resistance. This equipment is optimized for ESS applications and ensures consistent quality and performance by identifying cells with similar characteristics for balanced module and pack assembly.
2. Key Features
High Precision: Accurate measurement of cell parameters for optimal grading.
Multi-Channel Testing: Simultaneous testing of multiple cells to enhance throughput.
Flexible Compatibility: Supports various cell formats, including prismatic, pouch, and cylindrical.
Data Integration: MES-compatible for real-time data tracking and traceability.
Safety Assurance: Comprehensive safety features, including temperature monitoring and fault alarms.
3. Technical Specifications
3.1 Cell Compatibility
Cell Types: Prismatic, cylindrical, pouch.
Cell Dimensions:
Prismatic: 50 × 20 × 70 mm to 300 × 100 × 400 mm.
Cylindrical: 18650, 21700, 4680.
Pouch: 50 × 50 mm to 300 × 500 mm.
3.2 Measurement Capabilities
Voltage Measurement:
Range: 0–5 V.
Accuracy: ±0.005 V.
Current Measurement:
Range: 0.1–200 A.
Accuracy: ±0.05%.
Capacity Measurement:
Range: 0–500 Ah.
Accuracy: ±0.1%.
Internal Resistance Measurement:
Range: 0.01–50 mΩ.
Accuracy: ±0.1 mΩ.
3.3 Grading Parameters
Sorting Criteria: User-defined thresholds for capacity, voltage, and resistance.
Grading Groups: Up to 16 classification levels for precise grouping.
3.4 Testing Modes
Charge/Discharge Cycle: Programmable current profiles for realistic performance evaluation.
Constant Current (CC): Stable current for capacity grading.
Constant Voltage (CV): Stabilized voltage for cell calibration
3.5 System Capacity
Channel Count: 64–256 independent channels (expandable).
Testing Throughput: Up to 1,000 cells per day.
Cycle Time: Adjustable based on cell specifications and testing profiles
3.6 Data Management
Data Acquisition: Real-time logging of cell performance data.
Traceability: Unique serial number tracking for each cell.
Integration: MES and ERP system compatibility for centralized data management.
Reporting: Automated generation of grading reports and analysis charts.
3.7 Control System
HMI: Intuitive touchscreen interface for operation and monitoring.
PLC: Reliable control system for precise testing and safety management.
Alarm System: Visual and audible alerts for fault conditions.
Energy Storage Battery Cell Capacity Grading
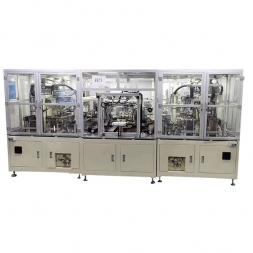
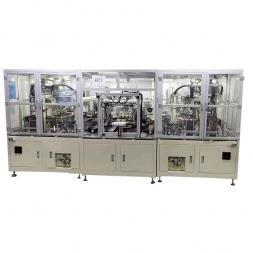