Lithium Battery Cell
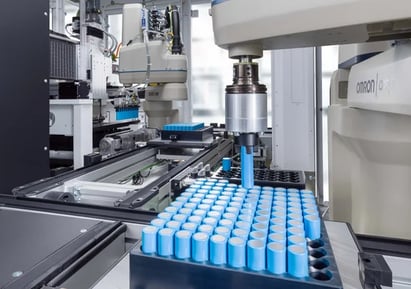
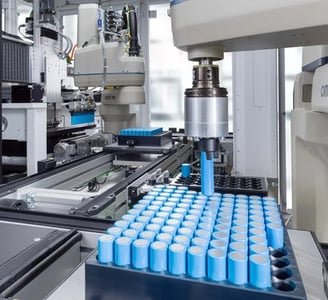
The production of electrodes is a critical part of battery cell manufacturing, involving the careful fabrication of both positive (cathodes) and negative (anodes) electrodes. This intricate process includes several essential steps: material preparation, coating, calendaring, and slitting, each demanding precise control and the use of advanced machinery to achieve high-quality results. Our company specializes in providing a comprehensive range of equipment and solutions tailored specifically for electrode production, ensuring that each stage is performed efficiently and consistently, ultimately leading to optimal electrode performance. Following electrode production, the next phase involves battery cell assembly, where electrodes, separators, and electrolytes are combined to create the functional heart of the battery. This meticulous assembly process is crucial for the overall efficiency and reliability of the final battery cell.
Mixing Systems For Electrode Production
Mixing process is to make slurry by active material, conductive material, binder and solvent, and ensure uniform distribution by accurately inputting through metering, mixing and steaming by powder supply device.
The mixing process usually consists of the following process:
Supplying powder (active material, etc) to mixer
Pre-dispersion of binder or conductive material before main mixing for mixing efficiency
Main mixing of active material, conductive material, binder, etc.
Storing the produced slurry and transferring it to the next process, the coating process
POWDER TRANSFER SYSTEMS for Electrode production
PTS (Powder Transfer System) is to transfer powder quantitively and smoothly by using air or vacuum.
PD Mixer
PD mixer has twist blades to generate big power for kneading and stirring, and have despair for high speed dispersion at the same time.
Because of efficient mixing and high volume, PD mixer is the most common mixer used in manufacturing secondary battery slurry equipment
Mixing Systems For Electrode Production
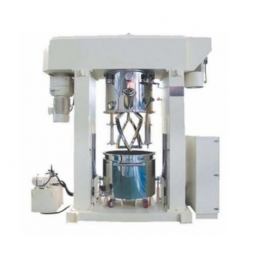
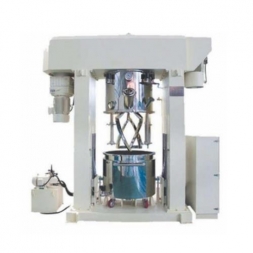
Coating Process
Coating process is a key process in battery manufacturing, and is a facility for coating and drying cathode slurry and anode slurry on metal foils such as aluminum and copper.
In many cases, slot dies are used as the coating method, but we can propose continuous coating, intermittent coating, double-sided simultaneous coating, etc. according to the customer’s electrode manufacturing process.
Coater Standard Specification
Winding Type: Auto Turret
Coating Width: Max. 1400mm (Anode), Nor. 680mm
Machine Speed: 80m/min
Coating Speed: Nor. 70m/min (18mg/cm2)
Coating Type: Slot Die
Coating Mode: Stripe & Intermittent
Coating Thickness: Nor. 200µm (One side)
Foil Feeding Type: Roll Support
Drying Zone: 1F/L 5m x 12 zones = 60m / 2F/L 5m x 12 zones = 60m
Heating source: 1. Electric heater 2. Steam 3. Hot oil
Option: Loading Density Measuring, Ceramic Coating
Delivery: 12 months (FOB)
*This specification is a standard specification, and we can make proposals according to the customer’s electrode manufacturing process.y
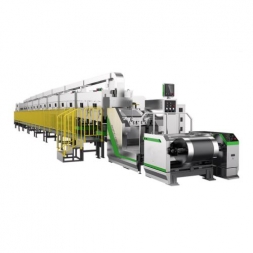
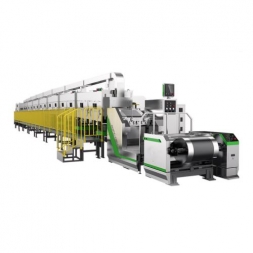
Coating Process line
Roll Pressing This equipment unwinds a thin film of aluminum foil, copper foil, etc. coated with an active material, continuously compresses it with a press roll, and winds it up. It is used to increase the filling factor of the active material applied to the thin film.
Single Calendar (Auto Turret)
Pressing Unit
Roll Press Standard Specification
Calendar Thickness Quality : ± <2um
Winding Type: Auto Turret
Calendaring Width: Nor. 680mm, Max. 1400mm (Anode)
Machine Speed: Max. 110m/min
Calendaring Speed: Max.100m/min, Nor. 80m/min
Calendaring Gap Control: 1. Screw Servo, 2. Hydraulic Servo
Calendaring Main Roll: Hot oil heat source
Calendaring Pressure: Max. 6Ton/cm, Nor. 4Ton/cm
Option:
1. Auto Thickness Gauge (Auto Feed Back System)
2. Force Elongation
3. IHU
*This specification is a standard specification, and we can make proposals according to the customer’s electrode manufacturing process.
Roll Pressing
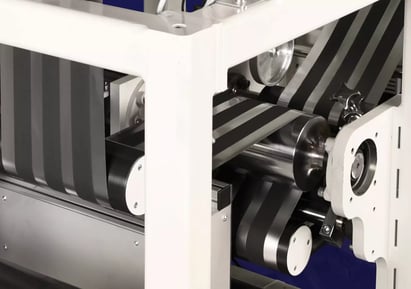
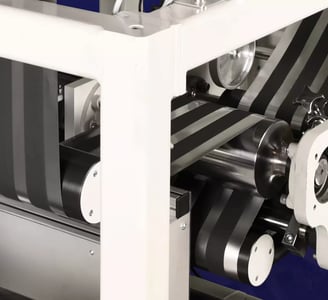
Slitting
Charge and discharge equipment is one of the most important processes in lithium-ion battery manufacturing to determine the quality of lithium-ion batteries by repeatedly charging and discharging them at a specified current, voltage, and temperature. Charge and discharge testing is one of the most important processes in lithium-ion battery manufacturing. High-precision charge/discharge inspection, excellent safety, and energy saving are required at the same time. We manufacture advanced charge/discharge testing equipment based on our unique electrical control technology, and have sold many of these products to users in Japan and overseas. In addition to our existing power supply line up, we develop power supplies to meet required specifications, and can handle everything from testing equipment to mass production machines.
Slitter
The slitter for LIB unwinds a roll of metal foil or an electrode plate, continuously cuts (slits) it to an arbitrary width, and rewinds it into a roll. We can also propose waste material collection equipment after slitting.
Slitter Standard Specification
Slitting Knife: Gang + Shear
Slitting Width: Max. 1400mm
Slitting Lane: Max. 2 ~ 11 lanes
Slitting Speed: Max. 100m/min, Nor. 70m.min
Option: Visual Inspection System
Cylindrical Type (Auto Turret)
Integration: Calendar + SlittingC
Slitting
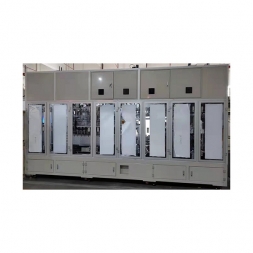
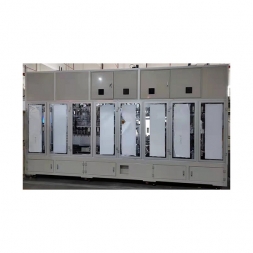
Winding Machines for Cylindrical Batteries
This machine is for the cylindrical battery manufacturing equipment. After the equipment is used for positive and negative film unwinding and rectification, the positive/negative tab is ultrasonically welded and glued. After the electrode is inserted into the film, it is wound into a cylindrical battery cell together with the separator. After cutting/ attaching protective tape/ hot hole and measuring/ the short circuit checked, it is finally sent out by the conveyor belt.
Main Parameters and Functions
Electrode automatic roll change
Separator automatic roll change
Segmented tension automatic Control
Ultrasonic welding system
Dust removal system
Hi-pot testing function
Three-axis automatic winding
Positive and negative electrode tape device
Double station cutting, high speed stability
Edge positioning correction control
Cell hot hole
Winding Machines for Prismatic Batteries
The equipment is mainly used for the winding of the prismatic battery cell, the coil material is supplied to the electrode and the separator, and the positive and negative electrode sheets and the diaphragm are wound to complete the cell bare core. Three-station operation: one station into the film winding, two stations for finishing glue, three stations for unloading. Automatic test for short circuit, weighing, and defective product rejection.
Main Functions
Dust removal system
Segmented tension
Automatic control
PC control
Positive electrode cutting and taping device
CCD overhang detection
Battery shape detection
Hi-pot test function
Electrode automatic roll change
Separator automatic roll change
3 axles automatic roll change.
Winding Machines
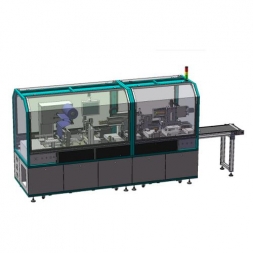
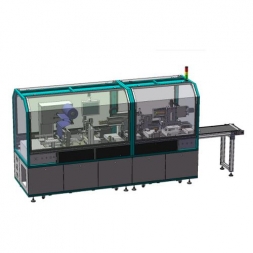
Stacking Machine
The equipment is used for Z-shaped lamination of positive and negative electrode sheets of lithium ion battery cells, U-shaped glue sticking on cells, short-circuit testing, cell blanking and other functions.
Flow of Electrode Stacking
Electrode Preparation:
Before stacking, individual electrode layers are prepared. This involves coating or depositing active materials onto current collectors, which could be conductive substrates like metal foils. These active materials are chosen based on the type of electrochemical device and the desired electrochemical reactions.
Separator Integration:
Separators, which are typically ion-conductive membranes or materials, are often placed between adjacent electrode layers. Separators prevent electrical short circuits between electrodes while allowing ions to pass through. In solid-state devices like solid oxide fuel cells (SOFCs), separators could be solid electrolytes.
Electrode Stacking:
Once the electrodes and separators are prepared, they are stacked in a specific order to form a layered structure. The order of stacking depends on the type of device and the intended electrochemical reactions. For example, in a lithium-ion battery, the typical order could be: cathode – separator – anode.
Electrode Alignment:
Proper alignment of electrodes and separators is crucial to ensure optimal electrochemical performance. Misalignment could lead to uneven distribution of reactants, reduced efficiency, or even short circuits.
Sealing:
In devices that require containment of reactants and products, the stacked layers are often sealed around the edges to prevent leakage. This sealing process ensures that the electrochemical reactions occur within the designated areas
Stacking Machine
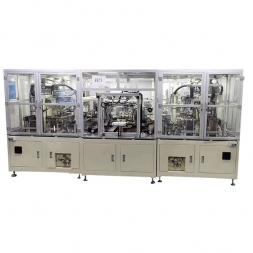
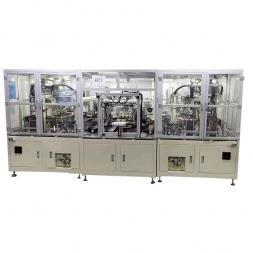
Vacuum Roll to Roll Drying System
Suitable for drying cathode/anode electrodes
Features for Vacuum Roll to Roll (R to R) drying system
Energy Saving
By adopting a continuous process, our product eliminates the need for cooling down at each stage of a batch process. This significantly minimizes energy loss, leading to considerable energy savings and the development of more environmentally friendly processes.
Uniform Heating
R to R drying is a continuous process where the electrode material is coated onto a flexible substrate in a continuous web format. Compared to conventional roll drying, R to R processing provides uniform product quality.
Reduced Drying Time
R to R drying is designed for high-throughput production, making it suitable for large-scale manufacturing. It allows for the efficient processing of electrode materials in large volumes. Compared to conventional roll drying, R to R processing significantly reduces processing time. (12hr→0.6hr).
Cost Efficiency
R to R processes are cost-efficient for large-scale production due to minimal downtime and reduced manual intervention. They are highly automated, streamlining production.
Space Saving
The vertical arrangement of the heaters reduce the installation space to 1/10 compared to the horizontal arrangement.
Lead time reduction
By adopting a gate valve mechanism, the lead time for product replacement is greatly reduced.
Conventional roll drying in batch process compared with Vacuum Roll to Roll drying system
Batch vacuum drying system requires a lot of factory space compared with R to R system.
Differences between batch vacuum heating systems
Heat treatment
The biggest difference between the batch type roll drying process and our R to R drying system is how we can treat uniform heating to the electrodes. Companies that manufacture electrodes where they have drying process in the production line, they usually face a problem called “Spring back Effect”. This is caused when there are temperature differences between the inner part and the outer part of the electrode roll, which then causes the cathode/anode materials to “Spring back” even though they are pressed in the previous processes.
Energy Saving
Since the conventional vacuum heating systems uses nitrogen (N2) to make a “vacuum” atmosphere, the operational cost is significantly high. Also, the structure of the R to R drying system has a significantly smaller chamber than the conventional systems, power consumption is also dramatically lower. It is estimated have approx. 50% lower power consumption and 100% less nitrogen (not necessary) compared to conventional systems which also has a large impact to CO2 emission!
Vacuum Roll to Roll Drying System
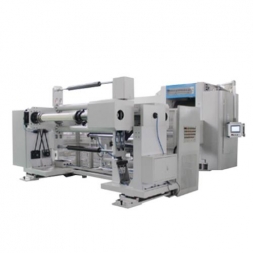
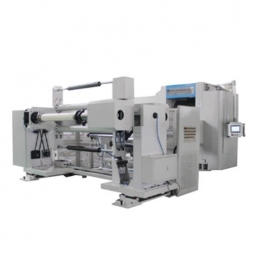
Assembly Process For Cylindrical, Square And Prismatic Batteries
General processes for every type of batteries
Electrolyte Filling (Liquid Electrolyte)
In traditional lithium-ion batteries using liquid electrolytes, the electrolyte injection process is a critical step. An opening or port is created in the battery casing to facilitate this. The liquid electrolyte, a lithium salt dissolved in a solvent, is injected into the cell through this opening. The specific electrolyte composition can vary depending on the battery design and intended application.
Venting and Degasification
After electrolyte injection in both liquid and solid-state batteries, a degasification process is often conducted to remove any remaining gas or air from the cell. This ensures that the cell is properly filled with electrolyte. Venting may also be performed to release any excess gas produced during the formation process.
Sealing the Battery
Once the battery is filled with the appropriate electrolyte and any excess gas has been vented, the next step is sealing the battery. The sealing process is critical for preventing electrolyte leakage and maintaining the integrity of the battery. The sealing methods may vary depending on the battery type (cylindrical, square, prismatic) and the manufacturer’s techniques.
Cylindrical Batteries
For cylindrical batteries, the open end of the cell is typically crimped or welded to seal it. This creates a hermetic seal, preventing the escape of electrolyte and ensuring the battery is airtight.
Square and Prismatic Batteries
Square and prismatic batteries are sealed using a combination of methods, including welding, adhesive bonding, and heat-sealing. These techniques are employed to achieve a secure seal that prevents electrolyte leakage and gas ingress.
Assembly process for cylindrical batteries
Assembly process for square batteries
Assembly process for prismatic batteries
Assembly process differs depending on the shape of the battery (cylindrical, square, prismatic). We can propose various machines used in the processes above according to customer requirements.
Assembly Process For Cylindrical, Square And Prismatic Batteries
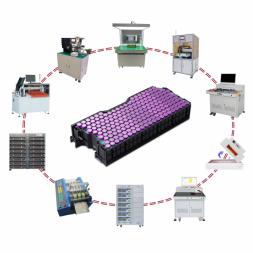
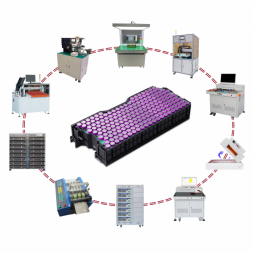