Lithium Battery Manufacturing
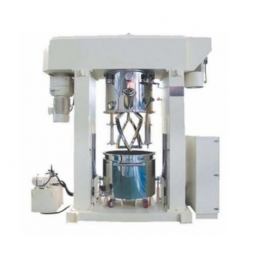
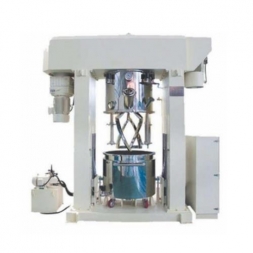
The demand for high-performance lithium-ion batteries is surging due to the rising adoption of electric vehicles, portable electronics, and renewable energy storage systems. Our company specializes in providing comprehensive solutions for lithium-ion battery manufacturing, offering a wide array of equipment and technologies for critical processes such as CAM/AAM production, electrode production, battery cell assembly, and charging/discharging inspections. With our expertise and advanced machinery, we empower manufacturers to optimize production efficiency, enhance product quality, and remain competitive in the rapidly evolving battery industry. Our commitment to innovation and excellence ensures that our clients are well-equipped to meet the growing market demands and contribute to a sustainable energy future.The global lithium-ion battery (LIB) market is currently witnessing unparalleled growth, fueled by the surging demand for electric vehicles, portable electronics, and renewable energy storage systems. To maintain a competitive edge in this dynamic environment, manufacturers need to adopt innovative technologies and enhance their production methodologies. Our company provides a diverse array of solutions that transform LIB production. We offer comprehensive turnkey solutions alongside cutting-edge production machinery tailored for battery material manufacturing, including LCO, LFP, NCM, NCA, silicon anode, and graphite anodes. Additionally, our expertise extends to advanced processes for electrode production, cell assembly, and essential charging/discharging inspection. By integrating these services, we empower manufacturers to streamline their operations and meet the growing market demands effectively.
Rotary Kiln for drying lithium hydroxide , coating process for cathode active material A rotary kiln is a cylindrical, inclined, and rotating device used for a variety of processes, including heating, calcination, drying, and more. It’s essentially a large, industrial-scale furnace with a rotating drum. The rotation is usually slow and continuous, allowing materials to be processed evenly as they move through the kiln. In battery material production, a rotary kiln is often utilized for the drying lithium hydroxide and coating for cathode active materials. Rotary kilns can essentially be designed in two different types: a batch type and a continuous type. In our experience, the majority of customers producing battery materials prefer the continuous type to take advantage of the throughput (kg/h) for mass production. Various heating methods exist, but due to the recent trends in ESG, most customers opt for heaters powered by electrical resistance. We recommend utilizing electrical heaters powered by renewable energy for global sustainability. Special Features Of Rotary Kiln For Lithium Precursors And Cathode Active Materials
Seal material Considering the recent production process for any precursors or most cathode active materials, the drying process is one of the most crucial steps in the entire production line. One of the critical aspects of rotary kilns for battery materials applications is gas tightness and tube material. Gas tightness is crucial because, in some cases, rotary kilns are utilized for coating cathode active materials using a special gas atmosphere. In such instances, gas leakages and oxygen concentration must be minimized. Our rotary kiln features a special seal structure designed to secure the gas atmosphere and minimize gas leakage, achieved by using a special carbon material for the seals.
Tube material Regarding the tube material, we offer several options based on the customer’s request. One major concern we address is lithium corrosion, which typically results from a chemical reaction between chromium in the tube material and lithium in the battery material. We mitigate this issue by employing a special pure nickel tube that has undergone rigorous testing by major global players in the battery materials industry.
Cathode Anode Drying Pre Calcination
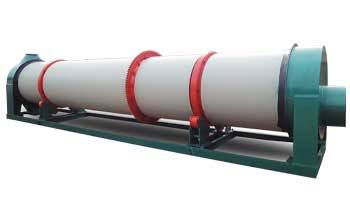
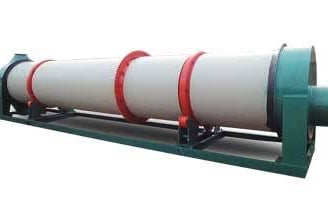
Milling process in Cathode/Anode Material Production
Importance of Milling in Battery Material Production
In the production of battery cathode active materials (e.g., NCM, LFP) and anode materials(e.g., silicon anode), milling plays a pivotal role in achieving optimal electrochemical performance. Milling is a fundamental step in battery material production and lithium processing, influencing particle size, distribution, and reactivity. Employing specialized milling equipment like roll mills, jet mills, and classifier mills ensures the desired material characteristics are achieved for various battery cathode and anode materials, as well as lithium compounds.
For high-quality milling equipment designed for battery material production, explore our range of roll mills, jet mills, and classifier mills to elevate your materials to the next level of performance and efficiency
· Particle Size Control:
Milling allows precise control over particle sizes, ensuring uniformity and enhancing electrode performance. Smaller particle sizes translate to larger surface areas, facilitating faster ion diffusion and better electrochemical reactions.
· Homogeneous Distribution:
Milling ensures even distribution of active materials, conductive additives, and binders. This homogeneity enhances electrode integrity, promotes efficient charge transfer, and reduces internal resistance.
· Reactivity Enhancement:
Finely milled particles exhibit increased reactivity due to greater exposed surface area. This enhances charge and discharge rates, leading to improved battery power and performance.
Milling Equipment
· Roll Mills:
Roll mills are versatile and commonly used for particle size reduction in battery material production. They consist of two rotating rollers that crush and grind materials, producing finely milled powders. Roll mills are suitable for a range of materials, including NCM and LFP cathode materials after calcination.
· Beads Mills (Wet Mill):
Also known as wet mills or bead milling equipment, beads mills are used in the production of battery materials, particularly in the processing of electrode materials.
Bead mills are capable of finely grinding and reducing the particle size of electrode materials, which is crucial for improving the performance of batteries. Smaller particle sizes provide a larger surface area, which can enhance the material’s electrochemical reactivity. These are commonly used for materials that are required to reach a particle size below 1 microns. For example, LFP and silicon anode materials, specifically speaking with battery materials.
· Jet Mills:
Jet mills utilize high-speed jets of air or gas to pulverize materials into fine particles. They are suitable for fragile or heat-sensitive materials like lithium hydroxide and lithium carbonate. Jet mills provide precise particle size control without the need for mechanical contact.
Classifier Mills:
Classifier mills combine milling and classification processes. They’re suitable for producing narrow particle size distributions. These mills are ideal for materials like silicon anode, where controlling particle size and distribution is crucial. Milling is a fundamental step in battery material production and lithium processing, influencing particle size, distribution, and reactivity. Employing specialized milling equipment like roll mills, jet mills, and classifier mills ensures the desired material characteristics are achieved for various battery cathode and anode materials, as well as lithium compounds .For high-quality milling equipment designed for battery material production, explore our range of roll mills, jet mills, and classifier mills to elevate your materials to the next level of performance and efficiency
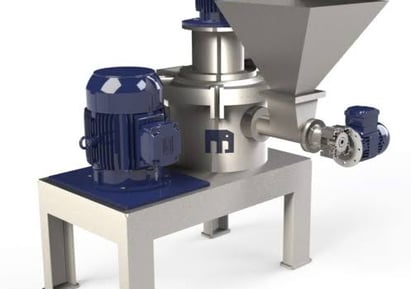
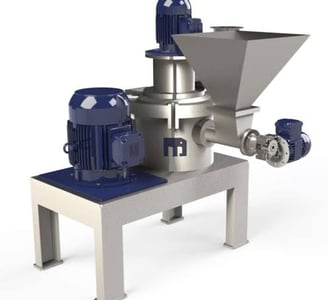
Cathode Anode Milling
MIXING process of Cathode & Anode materials
The best solution for mixing, dispersing, coating Functions Mixing
The mixing process holds immense significance in the production of battery cathode active materials and anode materials. It ensures uniformity, homogeneity, and optimal characteristics in the materials, which are essential for achieving superior battery performance.
Dispersing
Dispersing is a critical step in the production of battery cathode active materials (CAM) and anode active materials (AAM). It involves uniformly distributing additives, binders, and other components within the active material mix.
Coating
Coating is a crucial process in battery material production, involving the application of thin, uniform layers onto the active material particles. It enhances electrode stability, interface integrity, and can be tailored to meet specific battery requirements, contributing to longer-lasting, higher-performing batteries.
Material Examples
CAM (Cathode Active Materials)
Lithium cobaltite(LiCoO2)
Lithium nickelate(LiNiO2)
Lithium manganate(LiMn2O4)
Lithium iron phosphate(LiFeO4)
NCA
NCM (Ni, Mn, Co)
AAM (Anode Active Materials)
Graphite + Pitch
Silicon Oxide + Pitch
Lithium Titanate (LTO)
In our extensive experience, we have successfully handled a diverse range of battery materials, including cathode active materials like NCM and LFP, anode materials such as silicon anode. This breadth of expertise empowers us to deliver tailored solutions that meet the intricate demands of battery material production.
Electrolyte Coating for Solid-state batteries
Solid-state batteries rely on the interface between the cathode active material and the solid electrolyte for ion conduction. Coating the cathode active material with a thin, protective layer stabilizes this interface, preventing undesirable reactions and improving overall battery performance.
In the realm of solid-state battery technology, electrode coatings for cathode active materials play a pivotal role. By stabilizing interfaces, reducing resistance, enhancing cyclability, minimizing side.
MIXING process of Cathode & Anode materials
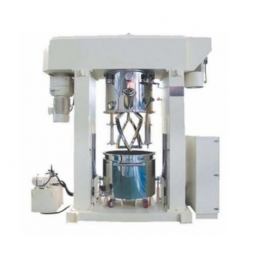
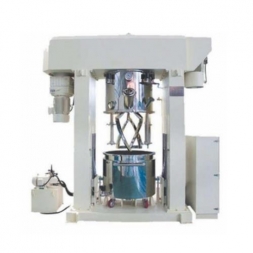
Roller Hearth Kiln Solutions for Battery Material Calcination
Roller Hearth Kiln (RHK) is a continuous firing furnace which transports products using ceramic rollers. RHK provides outstanding temperature uniformity, cleanliness and heat efficiency.
Uniform Temperature Distribution: RHK’s roller transportation method makes radiant heating from all direction possible
Clean Atmosphere: RHK materials are composed of ceramics which helps maintain a clean atmosphere
Energy Saving and Space Saving: The combination of uniform heating and high speed firing allow for high efficiency production with energy and space savings
Roller Hearth Kiln (RHK):
We have experienced many projects globally for Lithium ion battery cathode and anode active materials:
From R&D scale to pilot scale and mass production scale
Uniform temperature distribution
High throughput by utilizing special rollers
Best insulation material selection to fit customers’ application
Gas flow control
High speed continuous firing
Temperature : up to 1,620℃
All ceramic materials used inside the firing chamber – No metal contamination
Tailor made design for your materials and factory layout
Fully automated sagger handling system (option)
R&D scale batch kiln (RHK-Simulator)
Roller Hearth Kiln is best solution for Lithium-ion battery materials
We can offer automated sagger handling systems for your production. The Lithium-ion battery market requires large amount of cathode and anode production. Our sagger handling system can cover high volume production rates with optimized footprints.
Our Experiences
Lithium-ion battery cathode materials (All types of cathode active materials; LCO, NCM, NCA, LFP, etc)
Lithium-ion battery anode materials (All types of anode materials; Carbon, Silicon Anode, LTO)
Electrolyte materials for solid state battery
Ceramic materials; Alumina, Zirconia and others
Solid Oxide Fuel Cells
MLCC
Roller Hearth Kiln For Battery Material Calcination
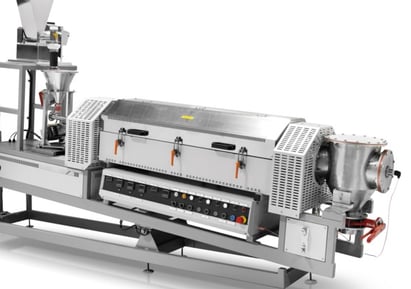
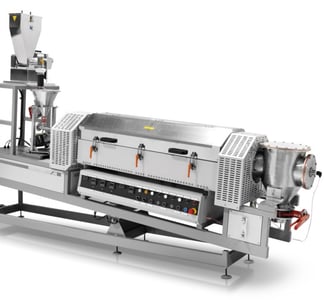
Electromagnetic Separator We are global leader in manufacturing magnetic separators, we bring extensive experience to the international delivery of this equipment. Our expertise primarily lies in cathode and anode active material production for lithium-ion batteries, providing us with insights into the latest trends in battery raw material production.The machine featured here is primarily utilized for active material production and is not commonly employed in battery recycling (yet!).Clients who have installed or are considering the installation of this machine in their main production lines understand the critical importance of eliminating metal contaminations from battery raw materials. We have observed that customers who neglect the removal of metal contaminations often find themselves at a disadvantage in the highly competitive battery material market. Of course, the necessity depends on the type of battery material being produced. However, if your production line lacks processes for removing metal contaminations, now might be the opportune moment to consider acquiring and enhancing your raw material quality. Metal contaminations can detrimentally impact battery performance and efficiency. Metallic impurities can disrupt chemical reactions within the battery, resulting in reduced capacity, diminished energy output, and a shorter lifespan. Furthermore, metal contaminations pose significant safety risks. Metallic impurities can induce internal short circuits, leading to thermal runaway, overheating, and potentially causing battery fires or explosions, as witnessed in accidents over the past few years. The removal of these contaminants minimizes the likelihood of such hazardous incidents, thereby enhancing the safety of battery operation. Electromagnetic Features Able to remove stainless steel particles From R&D scale to mass production scale available
Several types of magnetic screens available depending on customer requirement
Magnetic force up to 19,000 GAUSS
Due to the significantly high magnetic force, we can even eliminate stainless steel particles from your raw materials, potentially arising from the abrasion of other equipment. We also understand materials prohibited for battery material application and we have a specific design for it.
Our experiences
Cathode active materials: NCM, NCA, LFP, LCO etc.
Anode active materials: Silicon based anode, graphite (synthetic/natural), carbon based anode etc.
Precursors, raw materials (lithium)
Carbon additives
Slurry of active materials
We strongly recommend implementing a process to eliminate metal contaminations in your production line. We usually offer a test in Japan where customers can assess the processing of their raw materials and observe the removal of metal contaminations by a test machine.
Electromagnetic Separator
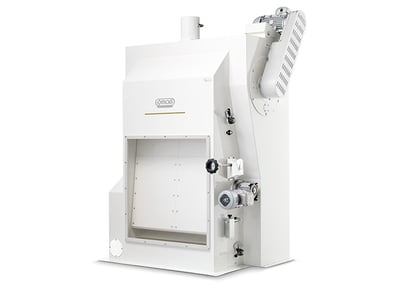
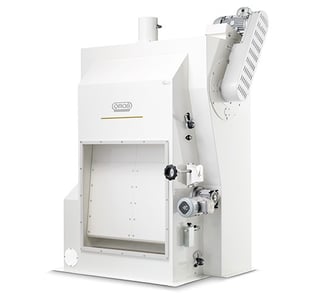