Injection Moulding
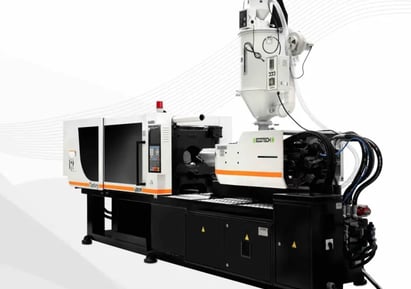
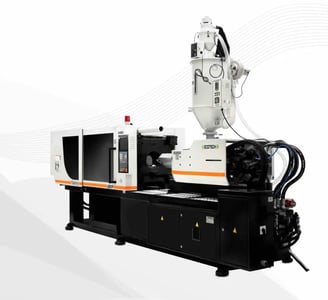
Step into the realm of precision and efficiency with our extensive range of injection molding machines, perfectly tailored for professionals in the manufacturing sector. Injection molding stands as a cornerstone of modern manufacturing, celebrated for its capability to produce high volumes of identical parts with intricate details and complex geometries. Our diverse lineup includes machines that vary in size, clamping force, and shot capacity, ensuring that you'll find the perfect fit for every project. Whether your focus is on automotive applications, consumer goods, medical devices, or any other industry demanding high-quality plastic components, we have the ideal solution to meet your production needs. Our commitment to innovation and excellence guarantees that you will achieve optimal results in your manufacturing endeavors, enhancing efficiency and precision in every process. Embrace the future of production with our state-of-the-art machines.
All Electric Medium Injection Moulding Machine
The injection and plasticising apparatus using the system, with characteristics that ensure precise reproducibility, is now powered by a servo motor. Measurements and positioning data for the injection locations are controlled in a closed loop to improve the positioning precision, achieving stable repetitions of the plasticising, measuring, and injection cycle. The line of injection units with plungers of 28 mm and 40 mm in diameters include models that emphasise speed and pressure, allowing you to choose the unit that best suits the moulded product type.
Electric Clamping Action
The servo motor drive and adoption of the mould clamping device by the original toggle link mechanism shortened the mould opening and closing cycle. The movable platen is supported by a linear guide to improve the stability of the mould orientation. The power design for these products significantly reduces power usage while contributing to quieter operation.
Operation Panel Focused on Intuition
Offering selector type switches, the control panel has been developed especially for the . The ability to move the switches in the same direction in which you want each unit to move results in a more intuitive operating experience and helps simplify moulding operations.
Excellent Plasticisation & Injection Performance
Equipped with a highly stable and highly reliable plasticisation and injection unit which contributes to accurate and highly repeatable resin injection, and a hydraulic accumulator mechanism that enables high-speed injection with dynamic responsiveness at a high level.
Original Mould Open/Close & Clamping Mechanism
Adopts both a mould open/close mechanism which realises accurate position control by an electronic system, and a mould clamping mechanism which reproduces an accurate mould clamping force by a hydraulic system. Equipped with a direct pressure mould clamping system which utilises the merits of the electro-hydraulic hybrid system to the utmost.
Total Servo Drive
Further improved energy-saving performance by the use of an electric servo motor for the hydraulic pump drive, in addition to the electric servo motor drive for the mould open/ close mechanism and ejection mechanism
Max. clamping force (kN) 980
Tie bar distance (W x L, mm) 460 x 420
Platen dimension (mm) 640 x 610
Open daylight (mm) 800
Min./ Max. die height (mm) 200 / 450
Max. weight of tool (kg) 600
Screw diameter (mm) 28 32 40
Plunger diameter (mm) 28 40
Max. injection specific pressure (MPa) 215 285 160 215
Max. injection rate by volume (cm3/s) 246 185 339 251
Max. injection stroke (mm) 160 200
Machine dimensions (L x W x H, mm) 4,240 x 1,215 x 1,748
All Electric Medium Injection Moulding Machine
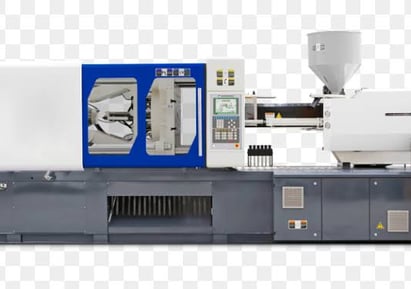
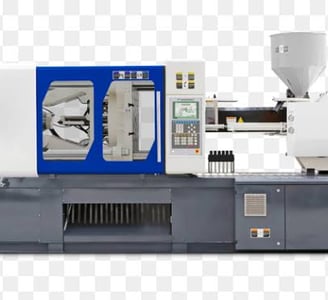
All-Electric Injection Molding Machine For High Productivity
This is a new generation molding machine that achieves a high level of labor-saving and environmental friendliness.
It is equipped with a new controller that has dramatically improved functions from the conventional series, and it is possible to realize a smart factory by improving operability and visibility and connecting with a production control system. It has become. The medium and large class of the series greatly contributes to productivity improvement by combining the mechanical performance and high-performance controller, which have significantly shortened the dry cycle and mold setup time from the conventional series. Furthermore, in order to evolve the popular high-precision core back, we have improved the die plate parallelism maintenance performance, making it a machine that can meet the back pressure accuracy requirements
Takes over powerful filling performance in high speed and high pressure range and achieves steady molding by smooth movement.
Friction-free drive
・Suppresses slide resistance to the utmost limit and contributes to precise and steady molding by stable injection characteristic.
・Smoothes leading response of injection and improves charging stability.
・Reduces variation among molding machines.
Control accuracy improvement in injection pressure and back pressure
- Absorbs inherent characteristic of pressure detector by linearize correction control, to lose machine difference to the utmost limit. This improves control accuracy of injection pressure and back pressure and achieves one up steady molding.
Ultra-high speed and high-pressure injection specification
・ Achieves ultra high-response injection by a combination of newly developed low inertia /high response servomotor and direct drive mechanism
Dynamic acceleration/deceleration control (Patent pending)
・ Adopts acceleration/deceleration control to reduce shock at mold opening/closing.
・ Enables maximum accelerate from an arbitrary position achieving high speed cycle molding.
High response ejection
・Sharp movement shortens ejection time.
. Grease-less tie rod
・Grease-less tie rods eliminates grease adhesion onto mold or product and maintains clean environment.
・ Standard rust proofing on the hopper inlet prevents mixing of rust or refuse into product.
SFC (high-speed mold open/close) specification (option)
・ Shortens dry cycle time further and achieves molding at higher speed cycle.
Streamlines inputs and maximizes output
Injection unit
Injection unit for stable plasticization and filling
• Friction-free drive that minimizes sliding resistance
• Noise-resistant digital load cell that improves pressure detection accuracy
• Linearization compensation that eliminates variation between machines
• High output motor that enables industry's top pressure holding capacity
High-performance screw for uniform plasticization of materials
• Screw design for high quality molded products
standard screw has a sub-flight for
separating the solid channel from the melt channel, and
transferring the molten resin, thereby eliminating break-up.
Precise charging for stable filling volume
• Check ring is mechanically closed by dedicated screw tip assembly and screw reverse rotation
• Dramatic improvement in molding stability
Automatic setting based on guideline setting values and advanced mold protection functions.
• The low pressure clamping force and mold closing limit position are automatically calculated and set
• Enables fine adjustments from automatic setting values to increase the mold protection effects
Clamp unit
Shorten the cycle time without changing the molding conditions
• Enabling shorter cycle times without impact on the quality while maintaining the same molding conditions as before
All-Electric Injection Molding Machine For High Productivity
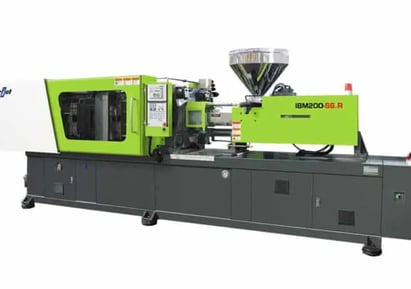
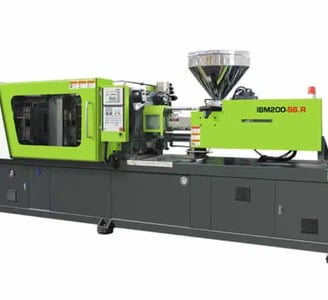
Toggle Small Injection Moulding
Toggle Small Injection Moulding Machine adheres to the design concept of minimalist elegance; every line, detail, and piece is born for performance optimization With the capacity of 50 - 150 ton toggle injection machine adopts a new generation of servo power systems that save 30% to 80% of energy compared with traditional hydraulic systems. Ultra-high response speed, short cycle time, and widened the moulding process.
Electric pre plasticizing technology is a technical method in which the traditional hydraulic motor is replaced with a “large torque servo motor + gearbox drive system” to drive the screw to rotate and melt the plastic material.
The injection unit features a reciprocating screw, with injection capacities from 268g to 4400g (PS) across the range. servo hydraulic injection moulding machines are equipped as standard with:
• Multi touch Controller
• Smart Flex clamping unit with generous tie bar spacing to accommodate larger moulds
• Moving platen that rides on linear bearings for excellent platen parallelism and reduced energy consumption
• Long ejector strokes
• Robust in-line swinging injection unit with quick release barrel
• Highly efficient servo motor driven gear pump system
MAIN CHARACTERISTICS
• New “Flat Clamp Mechanism” for optimum contact pressure
• High Precision Metering Control with “Pre Pack”
• 3 methods of V-P changeover
• Low Particle Emission below Class 10,000
• Higher Platen Dynamic
• More Compact Footprint
FLAT CLAMP
• Reduced Toggle Bush Loading
• Prolonged Mould Life
• Reduced clamp force requirement
HIGH DYNAMIC TOGGLE
• Faster Open/Close Speeds
• High Sensitivity Mould Protection
• Automatic Force Adjustment
PRISMATIC LINEAR PLATEN GUIDES
• Optimal Platen Guidance
• Energy Efficiency
• Clean Environment
CLEAN OPERATION
• Reduced Particle Emission
• Centralised grease lubrication
• Cleanroom 10,000
PRE-PACK
• Consistent Volume and Melt Density
• Stabilises Check Valve Response
• Auto adapt for batch inconsistencies
• Auto adapt for regrind
EG INJECTION UNITS
• Reduced Heat-Up Time
• Shorter Plasticising Times
• Improved Moulding Stability
COMPACT FOOTPRINT
• Upto 15% smaller footprint than previous series
• More machines per given area
• Higher factory output
MULTI-TOUCH CONTROLLER
New controller for smart factory
• Improved controllability by adopting EtherCAT (high-speed field network).
• It is easy to connect with devices that are expected to play an active role in smart factories in the future, such as web cameras, QR scanners, and RFID (IC cards, etc.) devices.
Improved controllability with digital servo commands
• Digitalization of servo control eliminates disturbance components such as electrical noise, enabling more accurate control.
User-friendly screen design
• A universal design is adopted to reduce the burden on the operator (colors with good visibility and large font size).
Improved screen operability
• It is possible to switch the upper and lower screens and scroll the history display and graph display.
Touch panel resistant to water and dust
• Even if the touch panel part is covered with water due to problems such as mould water pipe trouble, it will not break down easily.
Toggle Small Injection Moulding
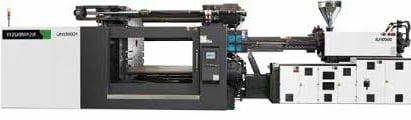
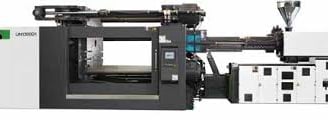
Toggle Medium Injection Moulding
Toggle Medium Injection Moulding Machine adheres to the design concept of minimalist elegance; every line, detail, and piece is born for performance optimization With the capacity of 50 - 150 ton toggle injection machine adopts a new generation of servo power systems that save 30% to 80% of energy compared with traditional hydraulic systems. Ultra-high response speed, short cycle time, and widened the moulding process.
Electric pre plasticizing technology is a technical method in which the traditional hydraulic motor is replaced with a “large torque servo motor + gearbox drive system” to drive the screw to rotate and melt the plastic material.
Technology Highlights
High speed: The loading time and plastic product moulding time are effectively shortened;
Energy saving: Under the same production conditions, it can save power by 15%-30%, and water by 50%;
Environmental protection: Low noise, no hydraulic oil pollution
Servo-motor driven gear pump system, using the very latest technology from renowned component suppliers The benefits of this system are many and offer a much greater overall efficiency, the most important of which are:
• Improved process control reduces reject levels
• Lower power consumption results in a lower cooling requirement
• Much less noise for a better working environment
• Longer oil life, longer lasting hydraulic components and reduced maintenance
These performance enhancements combine to produce a more profitable moulding process for the owner. This arrangement, coupled with special energy optimising software from, provides the user with excellent energy efficiency, reduced power consumption, and a more profitable manufacturing process.
CLAMPING UNIT
• 5-point double toggle clamp
• SPI platen configuration
• Chrome plated tie bars
• Linear bearings for moving platen guidance and support
• Powered mould height control
• Automatic central lubrication system by means of electric pump
• Three‐stage mould closing speed profile
• Three‐stage mould opening speed profile
• Moving platen pre‐feed
• Mould closing and opening stages governed through closed loop with proportional control valve
• Digital reading of moving platen position displayed on the operator interface
• Mould thickness and clamping force self‐adjustment
• Digital control and reading of cross‐head position on the operator interface
• Digital reading of clamping force displayed on the operator interface
• Two‐stage ejection speed profile
• Ejection force control
• Digital reading of ejector position displayed on the operator interface
• Repeated ejection with stroke and speed control
• Ejector proportional speed control, with overlapped movement at opening, Ejector return signal
• Freely-programmable multiple core pulling control
BASE
• Lowered base to optimise combined use of a robot
• Optional raised base to allow part drop
• Sound insulated motor‐pump assembly housings
• Anti-vibration mounting pad holes
• Lubricating oil recovery trough
Toggle Medium Injection Moulding
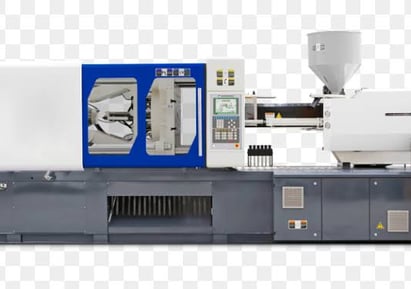
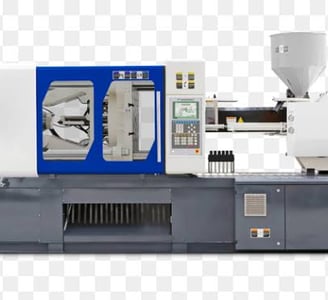
TWO PLATEN HYBRID TECHNOLOGY
Powerful • Efficient • Compact
New Design
The latest generation of the compact series of two-platen moulding machines demonstrates a smaller footprint than the previous series.
Features such as the European designed tie-bar locking system (clamp nut), with precision engineered annular mating surfaces, allow for higher loading and increased machine durability and service life.
The unique and patented tie-bar design and specification allows for accidental high overloads, with reduced risk of breaking and long tie-bar service life
Additional Features
Pure two platen design with an extended opening stroke.
Option of high-speed platen movement by servo motor and ball screw for shorter dry cycle times.
Moving platen supported by highly rigid and robust sliding pedestal system can accommodate heavier moulds.
The synchronisation of all tie bar-locking units provides uniform loading, which helps extend the moulds useful life.
The design allows for less moving components and also fewer lubrication points, which saves on cost and maintenance.
Each injection moulding machine comes with the latest generation controllers.
. The injection unit features a reciprocating screw with electric screw rotation, with injection capacities Machines feature a highly modular design with low base for excellent accessibility. BIPOWER two platen injection moulding machines are equipped as standard with:
• Fully digital control
• Robust design for proven, reliable performance
• Clamping unit with generous tie bar spacing and clamping pistons on the moving platen for excellent reliability and faster dry cycle times
• Long ejector strokes
• Robust twin cylinder injection unit
• Electric screw drive for energy savings, and overlapping movements for faster cycle times
• Powerful, user-friendly user interface with full range of control parameters
• Compact two platen clamping unit with high rigidity and minimal deflection
• Moving platen mounted ‘hydroblock’ tie bar locking system and clamping pistons
• Chrome plated tie bars
• SPI platen configuration
• Moving platen with extended support shoes
• Moving platen linear and lateral guidance system
• Automatic mould thickness control
• Automatic central lubrication system by means of electric pump
• Three‐stage mould closing speed profile
• Three‐stage mould opening speed profile
• Moving platen pre‐feed
• Mould closing and opening stages governed through closed loop with proportional control valve
• Digital reading of moving platen position displayed on operator interface
• Mould thickness and clamping force self‐adjustment
• Digital reading of clamping force displayed on operator interface
• Two‐stage ejection speed profile
• Ejection force control
• Digital reading of ejector position displayed on operator interface
• Ejector proportional speed control, with overlapped movement at opening
• Repeated ejection with stroke and speed control
• Ejector return signal
INJECTION UNIT
• Twin cylinder injection unit
• Electric motor for screw controlled by vector inverter
• Closed loop motor speed control
• Injection unit sliding on linear bearings
• Swivelling injection unit for easy plasticising screw removal and cleaning
• Quick barrel change system
• Bimetallic barrel
• General purpose screw profile, suitable for most types of thermoplastic materials, special screw profiles on demand
• Injection unit driven by two cylinders to assure perfect nozzle centring
• Ceramic heater bands
• Alarm threshold for set temperature range
• Injection speed and pressure profiles
• Switch to holding pressure triggered by screw position, hydraulic pressure or time
• Digital reading of screw position displayed on operator interface
• Adjustable screw rotation speed profile
• Screw rotation delay
• Adjustable back‐pressure profile
• Digital reading of back‐pressure displayed on operator interface
• Decompression before and after screw recovery
• Intrusion moulding program
• Auto purge program
• Stainless steel hopper
HYDRAULIC SYSTEM
• Variable delivery pump with closed loop proportional flow and pressure control
• Digital reading of hydraulic circuit pressure displayed on operator interface
• Proportional control valve for moving platen movement
• Monitoring of oil level, temperature and oil filter efficiency
• Oil temperature control system
• Automatic cooling water shut-off valve
• Oil preheating program
• Off-line circuit for oil filtering and cooling
• Oil cooling with platen heat exchanger
• Tank window to ease cleaning
• Optical and electrical oil level gauge
ELECTRICAL SYSTEM
• Enclosure for electric components with IP55 protection
• Electric motors with thermal protection
• Interlocked main switch to prevent electrical cabinet from being opened when press is energised
• Overload cut outs for motor‐pump units and dosing motor
• Fuses and static relays for control of plasticising cylinder temperatures
• Vector inverter for screw rotation
• Fan for air circulation in electrical cabinet
• LED indicators on solenoid valves
• Fully labelled electrical circuits
COOLING CIRCUIT (Optional)
• Flow meter with adjustable independent circuits with water temperature and flow rate indication (One circuit is used for throat cooling with the remaining circuits available for mould cooling)
BASE
• Lowered base to optimise combined use of a robot
• Sound insulated motor‐pump compartment
• Anti-vibration mounting pad holes
• Lubricating oil recovery trough
SAFETY DEVICES
• Constructed in compliance with essential requirements of Machinery Directive 2006/42/CE and subsequent amendments
• All models CE certified by a European certification organisation
• Safety devices comply to European Standard EN 201 and ANSI/SPI B151.1-2007
• Safeguarding system at front of moulds with double interlocking device and hydraulic safety device
• Safeguarding system at rear of moulds with double interlocking device and shutdown of motor‐pump units
• Monitoring of correct operation of hydraulic and electric safety devices
• Interlocked nozzle purge guard
TWO PLATEN HYBRID TECHNOLOGY
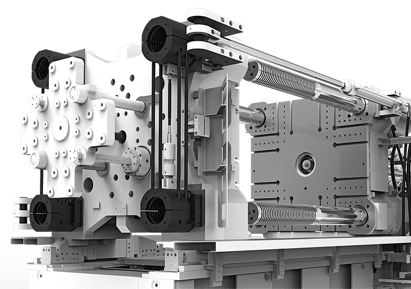
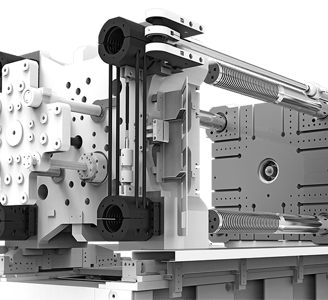
All Electric Small Injection Moulding Machine
Injection Moulding Machines
Step into the realm of precision and efficiency with our comprehensive selection of Injection Moulding Machines. Tailored for professionals in the manufacturing sector, our collection is designed to meet a broad spectrum of production requirements.
Injection moulding is a cornerstone in modern manufacturing, renowned for its ability to produce high volumes of identical parts with intricate details and complex geometries. Our lineup features machines that vary in size, clamping force, and shot capacity, ensuring a perfect fit for every project, whether you're involved in automotive, consumer goods, medical devices, or any other industry requiring high-quality plastic parts.
Our commitment to quality means every machine offers reliability, durability, and user-friendly operation, backed by the latest in technological advancements. From desktop units for small-scale production for high-volume output, find the ideal solution to enhance your manufacturing process.
Electric machines
Performance-orientated and compact at the same time: this is what companies appreciate about the electric injection moulding machines, which enable them to work with greater speed and precision.
Precise
High-quality servo motors and direct-acting powertrains guarantee quick, simultaneous machine movements and outstanding reproducibility.
Energy efficient
A toggle-type clamping unit and highly efficient servo-electric drives in a slim line design ensure optimum utilisation of energy and space.
Low emission
Closed, liquid-cooled drives and spindle systems work quietly and prevent dust pollution and air turbulence – also ideal for clean production environments.
With all the strengths of the ALL-Electric version of an already established injection moulding machine.
Engineered with the innovative CCS (Centre Clamping Structure) that eliminates platen deformation, tall-electric injection moulding machine providing advantages over traditional toggle designs. Forward-thinking and dedication to R&D are the fundamental principles that have helped to revolutionise the injection moulding machine industry.
Advantages of All-Electric Injection Moulding Machine
· Energy Saving – As there is no requirement for a hydraulic system and its associated water-cooled heat exchanger, this further reduces the required power consumption.
· Productive – Synchronous machine movement (overlap) helps achieve a shorter cycle time.
· Precise – down to 0.01mm incremental position control accuracy ensures product quality.
· Clean – No hydraulic oil for clamp movement or need to lubricate the moving platen helps keep a clean production environment.
· Quiet – Low noise levels create a more comfortable working environment.
Centre Clamping Structure (CCS), which functions using the latest servo motor technology and a ball screw mechanism. In conjunction with the linear guided platen, this allows for continuous high-speed precision throughout the machines lifetime.
A lubrication-free moving platen system provides the clean production environment that is demanded by certain industries.
Encapsulated Ball Screw Structure
The encapsulated ball screw design reduces the requirement of a clean working environment, as it offers protection against dust ingression, which could lead to premature screw wear.
The lubrication bath also removes frictional heat generated during normal operation. This increases the lifetime of the ball screw and reduces long term maintenance costs.
Plasticising System
The design of our plasticising units is of German origin, providing efficiency levels that are more than 20% above those of typical domestic design.
Max. clamping force (kN) 294 (392 optional)
Tie bar distance (W x L, mm) 310 x 310
Platen dimension (mm) 440 x 440
Open daylight (mm) 550
Min./ Max. die height (mm) 150 / 360
Max. weight of tool (kg) 200
Screw diameter (mm) 14 16 24
Plunger diameter (mm) 12 16 22
Max. injection specific pressure (MPa) 288 262 260
Max. injection volume (cm3) 4.5 14 27
Max. injection rate by volume (cm3/s) 57 101 190
Max. injection stroke (mm) 40 70
Machine dimensions (L x W x H, mm) 3,150
All Electric Small Injection Moulding Machine
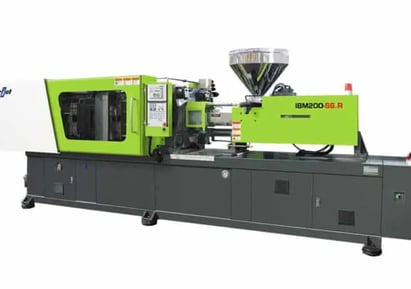
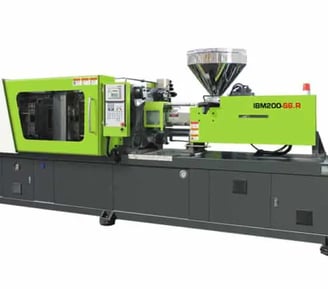