Freeze Dryer
Freeze Drying Machine removes all the water from a product and nothing else. The product retains allmost all of it’s original nutrients, flavor and color, making it obvious choice for quality production. Freeze Drying Versus Traditional Drying
Dried foods have played a huge part in food preparation for centuries. Freeze Drying is still a relatively new technique for drying food, but the benefits are immediately obvious as the table below demonstrates Freeze Drying Machine ensures no loss of aroma in taste
Ice capacity upto 100 to 1000 Kgs in a 24 hour period
Chamber, Shelf Holder, Tray and Vaper Condenser – AISI 304 Heating System + Vacuum System and Refrigeration System
Effective in handling granular / large solids
Surface as well as bound moisture can be removed
Very uniform & gentle drying / cooling action.
High efficiency
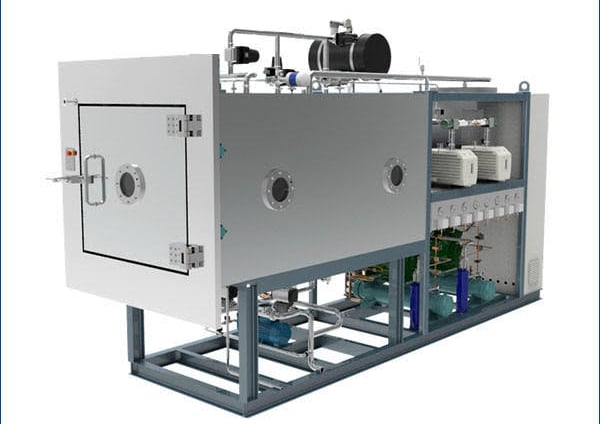
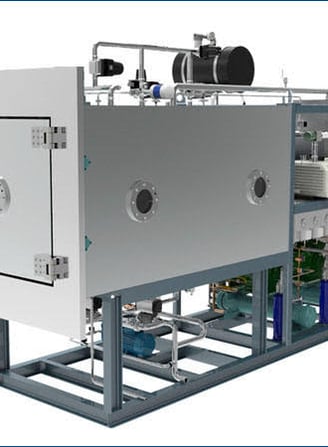
Industrial Dryer
We have customized solutions for making Industrial Driers for various applications . Our energy efficient Drier Machines using Intelligent Technology for Freeze Drying , Rotary Drying ,Fluidized Bed drying ,Vacuum Drying IR belt Dryer Systems And supply across the Global companies at competative price
Our IQF tunnel consists of two main parts - the belt section and the evaporator section. The belt section is divided into two pressure chambers, located under the perforated, modular belt. In each chamber there are fans equipped with frequency converters that enable the control of the fluidization process and the entire freezing process. The evaporator section consists of evaporators designed, calculated and manufactured by us, dedicated to various refrigerants: ammonia, freons and CO2.
A vibrating feeder installed in front of the tunnel is responsible for the continuous distribution of the product and feeds the product directly into the tunnel.
IQF tunnel is also equipped with an external 1st belt cleaning system, which allows periodic or continuous cleaning of the 1st belt during freezing - without stopping production.
This system that is used to remove frost from evaporators, using a blast of compressed air. Each evaporator has a compressed air tank to support it with air nozzles positioned to remove frost, snow and ice from between the evaporator fins. The entire system is controlled automatically by the tunnel computer. Thanks to the use of the system and the external belt cleaning system, it is possible to operate the tunnel for up to 22 hours between defrosts.
The control touch-panel is located on the door of the control cabinet and allows precise control over all components of the tunnel without the need to enter its interior.
The tunnel can also be equipped with an additional CIP (Cleaning-In-Place) system, sequential defrosting system or remote access system.
IQF tunel benefits
During designing tunnels, we always aim to obtain the highest quality frozen product. Our advanced technology allows you to freeze a wide range of products using the same tunnel - all thanks to the extensive control of the freezing process and tunnel components. We guarantee durability and reliability while reducing electricity and water consumption. Frost removal devices allow you to minimize the downtime between successive freezing cycles and to obtain maximum efficiency in relation to the size of the tunnel.
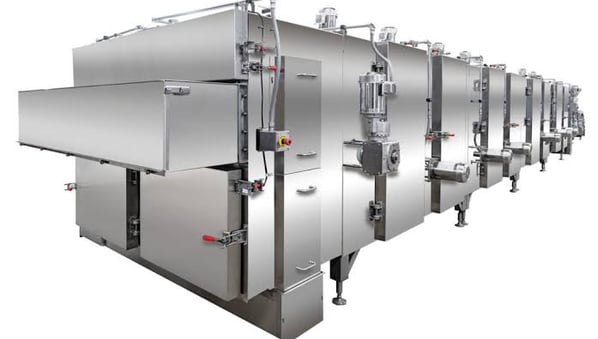
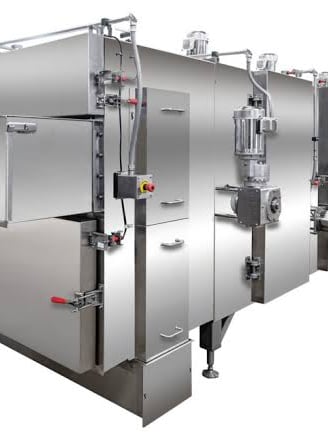
TUNNEL IQF

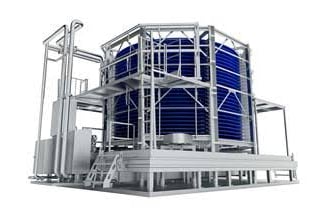
Jet Dryer
Jet Tube Dryer technology as to make the heat exchange between the product and the hot air quickly and uniformly by jetting out the hot air at a very high speed onto the product from the tip of vertical long tube which are placed regularly in the Conveyor .
This Jet-Tube Technology realizes an excellent and unparalleled heat exchange, and enables a heat processing in a much shorter time. This dryer uses hot air at high speed. A centrifugal fan that sends the air to a series of circular section nozzles, arranged diagonally in relation to the feed, obtaining a semi-closed-circuit ventilation system. high air speed, the dryer is ideal for quick drying of the colors. It’s possible to inserted infrared lamps to use the radiation action in addition to the action of percussion air.
Advantages
Can be install infrared lamps at different wavelengths spaced out with the blades for a mixed irradiation and hot air action. Air speed adjustable by both damper and
The hood allows an optimal heat exchange allowing the homogeneous drying on the whole
Energy saving through air recirculating system and VFD
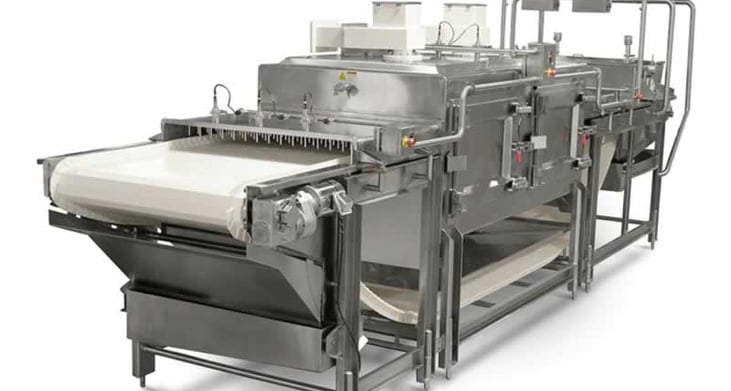
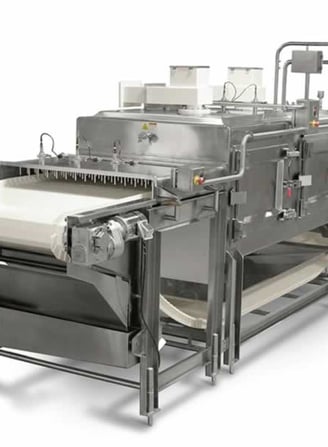
Rotary Dryer
Rotary dryers are one of the most common types of industrial dryer, utilised for large quantities of material with particles of size 10 mm or larger. Typical rotary dryer consist of cylindrical shell made of steel plates slightly inclined (1O to 5O) to horizontal to assist the transportation of the wet material fed for the processing, shell is typically 0.3-5 m in diameter, 5-90 m in length and rotating at 1-5.
Rotary dryer shell tube acts as body to transfer the wet feedstock and number of steam heated tubes are placed symmetrically around the perimeter and rotate with it. Wet material is fed into the upper end of dryer and the material travels through it by virtue of rotation and slope of the shell and dried product is picked as the lower end.
The feed rate, speed of rotation of shell, the volume of heated air or gases, and their temperature are so regulated such that by the time material reaches to discharge point of rotary dryer it’s accurately dried.
Rotary Dryers are flexible in processing virtually any bulk solid material, rotary dryers have made their way into an abundance of industries around the globe.
Working Principle of Rotary Dryers
When rotary Dryer is operating, it shall be in direct contact with heated gas. The dryer consists of a large rotating cylindrical tube. In order to convey the material through the underside of dryer, the dryer should be slanted slightly to ensure that the discharge end is lower than the end of material feed .
Material shall be dried to enter the dryer. When the dryer is rotating, a series of internal fins will lift the material by lining the inner wall of the dryer. When the material reaches certain height to roll the fins back, it will be fell back to the bottom of the dryer, then passing through the hot gas stream as it falls.
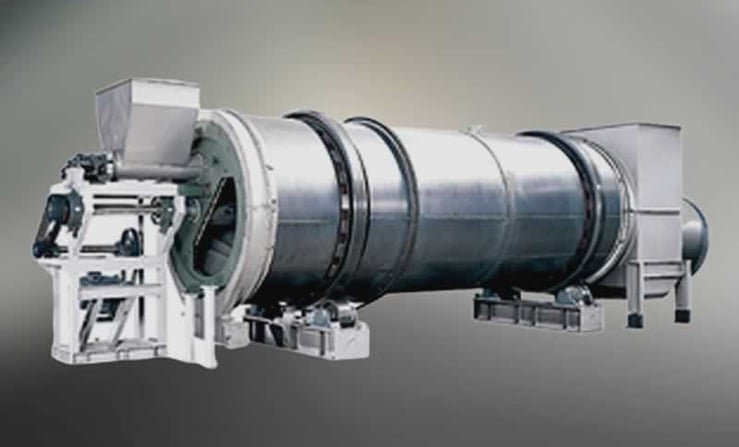
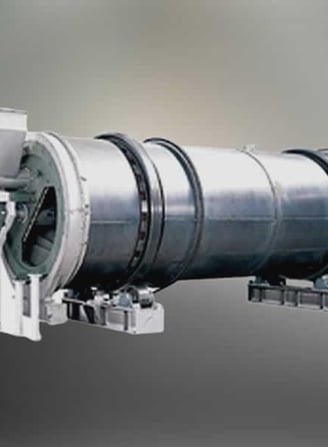
IR Belt Dryer
We are Belt Dryers Manufacturers for last decades with expertise to provide customized drying solutions to Food and Other Agro Processing Industries.
A Belt dryer / Belt cooler is a device designed for the particularly gentle thermal treatment of product. The wet product is continuously and evenly applied through an infeed chamber onto a perforated belt. The belt, predominantly in horizontal position, carries the product through the drying area which is divided into several sections. In these cells drying gas flows through or over the wet product and dries it. Each cell can be equipped with a ventilating fan and a heat exchanger.
This modular design allows the drying and cooling temperatures to be controlled separately in the different sections.
Belt dryers / Belt coolers are designed in modular system. Each Belt Dryer consists of infeed hopper, conveyor belt and discharge end. Different kinds of dryers are possible to construct, e.g.
Single – Belt dryer
Multi – Belt Dryer
Multi-stage Belt Dryer
Multi-level Belt dryer

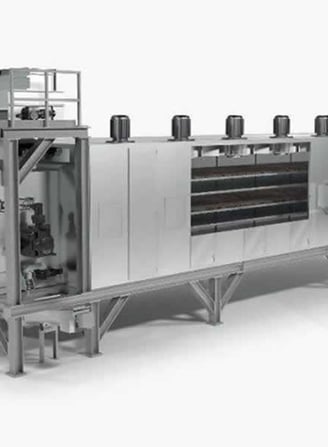
Fluidized Bed Dryer
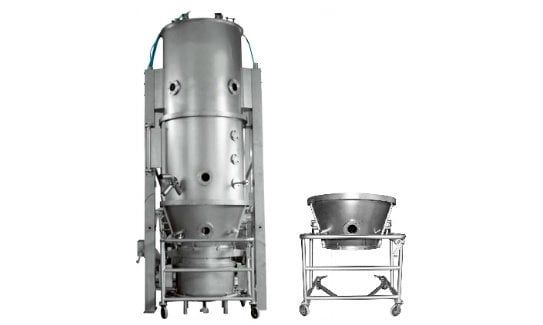
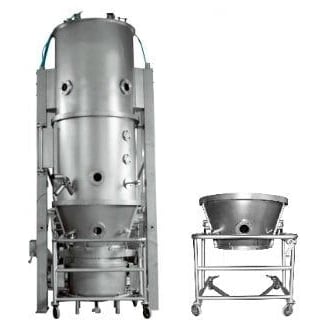
Fluidized bed system, the high velocity air (30~50m/sec) jetted out from many long tubes placed above the product bed on the conveyor creates a buffer zone, floats the product on the conveyor and stirs (fluidization). This realizes a maximum heat transfer /heat exchange.
The contact surface with the processing air of individual grains, pellets or parted products separated and fluidized is much bigger and the processing time is drastically reduced. As the air is uniformly jetted from all Jet-Tubes placed regularly, a heat processing with an extremely high uniformity is realized.Fluidized bed is achieved by passing a gas stream from the bottom of a bed of particulate solids. At low velocity of gas the bed stays in static condition, and the particles lay on a gas distributor plate. The fluidizing gas passes through the distributor and it is uniformly distributed across the bed.
The gas velocity is increased such that to achieve the fluidization of bed, gas velocity at which the bed achieves the fluidization is known as minimum fluidization velocity.
A Fluidised bed dryer operates at gas velocity higher than the minimum fluidization velocity of material under processing.
This increase in the gas velocity result in suspension of particles under processing in air, this appears as the boiling of solidparticles of material under processing.