Horizontal Turning Machine
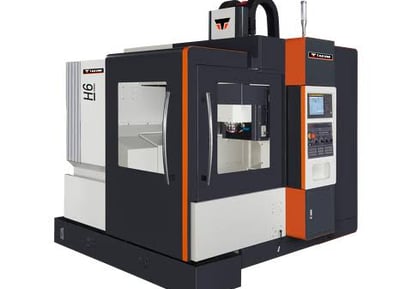
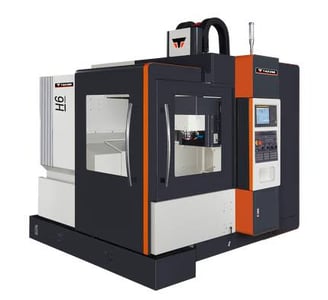
In today's heavy engineering industries, the demand for high-end solutions is paramount, particularly in sectors like earth moving, automobile manufacturing, agriculture, and construction. To meet these needs, innovative machinery has been developed featuring integrated guide-ways that provide enhanced accuracy and superior vibration damping characteristics. This precision is further complemented by the design of the spindle, turret, and tailstock axes, which are aligned parallel to one another, allowing for higher cutting depths. Such advancements not only improve operational efficiency but also ensure the reliability and effectiveness of the machinery used in these critical applications, ultimately pushing the boundaries of what's possible in heavy engineering. Our turning machine solutions are designed to address the varied needs of contemporary industrial applications. These machines feature advanced capabilities that enhance turning processes, allowing for precise contouring, threading, and surface finishing. The horizontal turning machines boast a single-piece inclined bed combined with a saddle, ensuring stability and accuracy through heavy-duty LM guideways and high-precision ball screws. Standard with a servo turret, our latest technology for turning mill centers provides increased rigidity and efficiency. With the spindle, turret, and tailstock axes aligned in parallel, these machines allow for greater depth of cut, making them ideal for both high-volume production and intricate machining tasks.
Our turning machine solutions are crafted to meet the diverse demands of modern industrial applications. Equipped with advanced features that optimize turning processes, these turning machines enable precise contouring, threading, and surface finishing. Horizontal turning machines are made with single-piece inclined bed cum saddle. They are built with heavy-duty LM guide ways for rigidity and precise ball screws for higher accuracy. The Servo turret is provided as standard and it is the newest technology for turning mill center for more rigid solutions.
Spindle, turret, and tail stock axes are parallel to each other. It enables higher depth of cut.
Mono block construction of bed cum saddle with an inclined angle of 45 deg for Helix and (30 + 45) deg for with Y – axis
Highest bar capacity 65 | 75 | 90
Base mount type servo turret of 12 stations
All 12 stations can be used for live tool applications
Swivel operator panel for operator easiness
Lesser loading height from the floor and lesser distance from the door for clamping heavy components
Basic TPM features
2 & 4 jaw self-centering chuck
Collet chuck
Hollow cylinder
Pneumatic operated Auto door
Chip conveyor with chip bin
Door safety limit switch
Bar feeder
Part catcher
Steady rest
Tool probe
Work probe
Automation solutions
Tooled-up solutions
LM guide-ways for all axis – Class H
High Precision ball screws- Class C3
Belt-driven spindle
AC servo drives for spindle & axis
Linear & circular interpolation
Laser calibration & Ball bar tested
Rigid taping
12-station hydraulic turret
Tool display
Rigid tap retraction push button
3 jaw self-centering chuck
Solid rotary cylinder
Tail-stock with programable quill
Coolant tank with chip tray
Machine lamp
Operations indication lamp-3 color
AC unit for electrical cabinet
Centralised lubrication system
Specifications Unit
Capacity:
Swing over bed mm 550 550
Swing over carriage (Y at zero position) mm 280 280
Admit between center distance mm 620 620
Standard turning diameter (Y at zero position) mm 240 240
Max component dia at Y+50 position mm 140 140
Maximum turning Dia (Disc-80mm length) 280 280
Interference-free turning dia(Tool collision dia with adjacent tool pocket) mm 224 224
Max turning length between Tail-stock & Head-stock centre mm 500 485
Max turning length from chuck hard jaw face to tallstock centre mm 410 395
Work holding & tool holding:
Standard chuck size mm 250 250
Bar capacity mm 65 74
Turret indexing mechanism type Servo Servo
Turret center height 100 100
Turning Tool Shank size (B x W) mm 25 25 25 25
No of tools No.s 12 12
Boring tool holder dia mm 40 40
Spindle:
Spindle nose type A2-6 A2-8
Spindle bore mm 76 86
Number of bearing front/ rear No.s 3/ 2 3/ 2
Spindle bearing front/ rear mm 110/ 100 120/ 100
Spindle speed rpm 3200 3000
Live tool speed rpm 4000 4000
No of live tool stations No.s 12 12
Live tool spindle power kW 4.5 (Fanuc) | 5.6 (Siemens) 4.5 (Fanuc) | 5.6 (Siemens)
Control system-Fanuc/ Siemens
Spindie motor power continues/ intermittent rating kW Fanuc – 11/ 15 | Siemens 11/ 16.5 Fanuc – 11/ 15 | Siemens 11/ 16.5
Full power range rpm Fanuc – 1000 – 1750 | Siemens 750 – 2400 Fanuc – 1000 – 1750 | Siemens 750 – 2400
Traverse
Cross slide movement (X axis) mm 200 (+140/ -60) 200 (+140/ -60)
Longitudinal movement (Y axis) mm +/- 50 +/- 50
Longitudinal movement (Z axis) mm 525 525
Rapid traverse (X axis) m/min 20 20
Rapid traverse (Y axis) m/min 12 12
Rapid traverse (Z axis) m/min 20 20
Cutting feed rate m/min 0 – 10 0 – 10
Tailstock
Quill diameter mm 80 80
Quill traverse mm 100 100
Base traverse mm 400 400
Quill taper type MT – 4 MT – 4
Quill thrust force-Max at 15 bar kgf 300 300
Fluid system
Coolant tank capacity ltr 160 160
Coolant pump capacity lpm 200 200
Lubrication tank capacity (servo 68) ltr 2.7 2.7
Hydraulic tank capacity (Servo 68) ltr 40 40
Hydraulic pump capacity lmp 20 20
Hydraulic system pressure bar 35 35
Accuracy as per ISO 230-2
Positioning X/Z mm 0.01 0.01
Positioning – C axis arc sec +/- 36 +/- 36
Repeatability – X/Z mm 0.007 0.007
Machine installations:
Machine dimension W x D X H mm 3100 1850 2100 3100 1850 2100
Total connected load kVA 35 35
Machine Weight kg 4500 4600
High Precision Horizontal Turning Machine
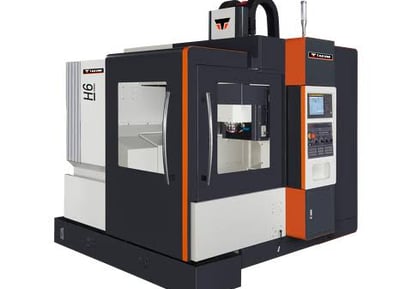
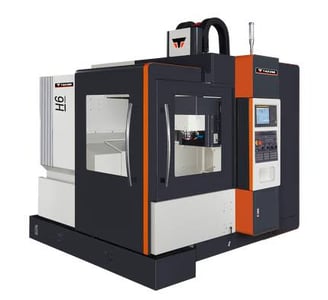
Our turning machine solutions are crafted to meet the diverse demands of modern industrial applications. Equipped with advanced features that optimize turning processes, these turning machines enable precise contouring, threading, and surface finishing.Horizontal turning machines
To meet the requirement of heavy engineering industries for High-end solutions such as Earth Moving, Automobile, Agriculture, Construction Etc.. Built with integrated guide-ways and ensure greater accuracy & vibration damping characteristics.
Wide variety of Mill-Turn Centers with turning lengths 1000, 1500, 2000, 3000, 4000, and 4500 mm in 2 center heights and several configurations.
Built on the PL600 platform with same bed, headstock, tailstock, and Z and X axes, so all special features specified in PL600U are applicable here
Spindle C axis position feedback is by hollow shaft encoder.
In case of a large spindle bore 180 – 230 mm, the feedback is by normal encoder with timing pulleys and belt
Hydraulic power pack with float level switch
Single piece cast iron bed
Integral hardened and ground guide ways
In built geared head stock
High rigidity Hydraulic clamping turret
Servo live tool turret (Optional)
C-Axis and Live tools (Optional)
Easy accessibility to turret to tool chang
Optional higher power Fanuc 30/37 or Siemens 28/34 kW
Optional spindle nose A2-15 with larger front bearings for chucks of 630 mm dia.
CNC systems from Fanuc and Siemens on request
Machine color as per customer requirement
Special turret disc suitable for tool shanks of 40 ht x 32 width and up to 110 mm overhang for crankshaft journal turning application
Specifications Unit
Max Swing diameter mm 720
Max Turning diameter & Chuck mm 630
Max Turning diameter over carriage mm 500
Max turning length mm 1000 (1500) (2000)(3000)(4000)
Spindle motor power kW 22/ 26 (30/ 37)
Turret mm Servo Live turret
Live tool Spindle power kW 5.5
Machine dimensions (WxDxH) mm 4200 x 2750 x 2800
Machine weight kg ~8500
Heavy Duty Horizontal Turning Machine
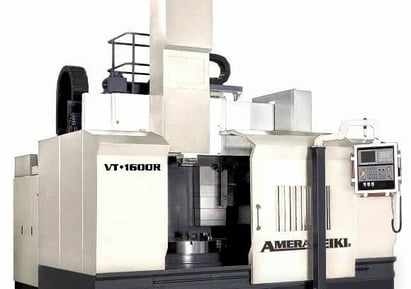
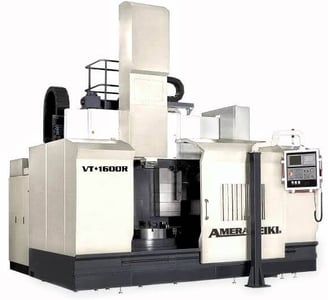