Grinding Mill
Grinding Mill
Stikine Systems designs and manufactures size reduction and powder processing solutions for the . Food , Chemical, Pharmaceutical, Mineral, Cosmetic And Plastic Industries.
We Are One Of The World’s Market Leaders In Wet And Dry Powder Processing Technology With Innovative Material Processing Solutions, We Enable Our Customers To Create Exciting Products For A Sustainable World Offering An Extensive Range Of Products From Laboratory To Production Sized Machines And Complete Plants. A Large Number Of Wet And Dry Grinding Systems Are Available For Different Grinding Tasks Even Down To The Nanometer Range For Low Or High-Viscosity Products For A Multitude Of Applications
Impact Mills
The Impact Mills Series Are Modular Design Provides Full Flexibility In Operating And Retrofitting The Units With All Available Individual Grinding Elements And Sieve Inserts. Depending On The Product, Minimum Grain Sizes Of Below 5 µm Are Achievable. For The Broad Variety Of Applications For These Impact Mills, We Are Developing Ever New Customized Layouts For Generating Optimal Production Results. Our Aggregates’ Drives Comply With Latest Energy Efficiency Standards.
Impact Mills Series For GMP Applications And Heavy Duty Industrial Use Are Being Advanced By Us Since Decades. The Units Are Employed As Pin Mills In Tailored Rotor And Stator Layouts, Turbo Mills With Variable Sieve Inserts, Beater Mills With Grinding Rings And Sieve Inserts As Well As Fluted Disc Mills With Variable Grinding Gap.
The Material, Shape And Size Of The Grinding Elements Can Be Customised To Fit Requirements. The Pressure Surge-Proof And Explosion-Proof Housing Is Designed To Prevent Deposits. Easy Access To The Grinding Chamber Means That The Machines Can Be Cleaned Quickly And With Very Little Effort.
Advantages of our fine impact mills:
Easy to clean
Long service life
Prevents deposit accumulation
Sharply defined upper particle size limitation
Energy efficient
Tools easily interchanged
Tool variety (grinding pins, plate beaters, beater discs)
APPLICATIONS OF Fine impact mills:
There are also no limits to the areas of application for fine impact mills. The mills and systems are used for chemical raw materials, minerals, food, medical products or colourants and plastics. The optimum combination of drive, machine type, tool and system concept can be used to create a powder that perfectly meets any requirements.
Protein shifting
Oily and greasy products
(Powdered) sugar
Cereals
Soya
Maize
Lactose
Plastics (polymers & rubber)
Pigments
Silicone resins
Waxes
Solid acids, salts & minerals
Calcium carbonate
Flowers, leaves & teas
Tobacco
Cryogenic grinding
Fertilisers
Impact Mill
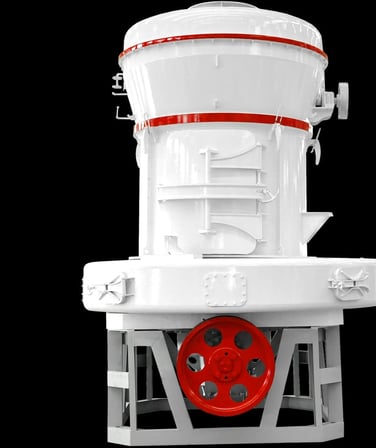
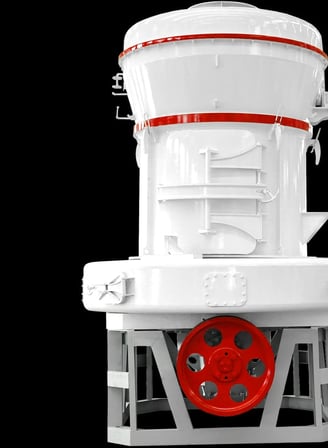
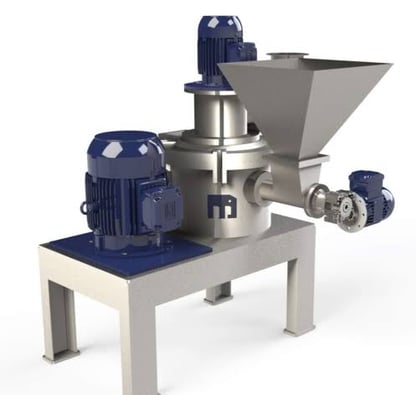
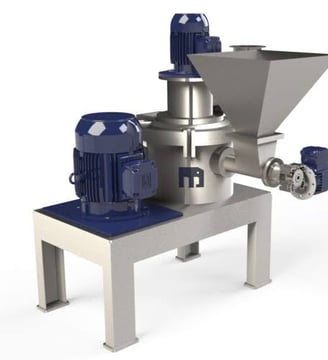
Air Classifying Mill
The Air Classifying Mill is ideal for grinding heat sensitive and extremely cohesive material efficiently. It grinds, classifies and conveys in one step. Due to the volume of air passing through, the temperature in the grinding chamber is generally lower than that in other types of fine grinding equipment. This condition offers a primary advantage in the processing of materials with low melting points.
It Separate Fine Powder Due To The Desired Final Fineness Or Other Product Characteristic.
The Best Results And Yields Are Achieved Regardless Of Whether You Are Separating Coarse Fractions (Grit) Or Classifying Fines (De-dusting). The Limitless Adjustment Of The Classifier Wheel Separates The Particle Sizes. The Optimized Classifier Wheel Design Guarantees That Very High Finesses Can Be Achieved With Only One Classifier Wheel, Even With High Throughputs.
The User Friendly Machine Housing Allows The Machine To Be Thoroughly Cleaned, Fast, When Product Or Batches Are Changed. Vortex free fines outlet with expansion chamber to reduce circumferential speed and wear as well as product build up in the outlet Classifier wheel with exchangeable, simultaneously rotating immersion tube to achieve highest finesses, unlimited adjustment
Gap between classifier wheel and fines outlet rinsed by gas for highest possible prevention of oversize particles in the fine fraction. Classifier shaft seal rinsed by compressed gas to protect the bearings Conically shaped bottom, with vertical coarse particle outlet Bearing of the classifier shaft is permanently grease sealed or oil lubricated for hot gas applications Extremely sharp separation due to optimized classifier wheel design
Highest finesses and maximum throughput achievable with just one classifier wheel Even product load on the classifier wheel through rotationally symmetrical design of the machine Hinged classifier head provides very good access for fast, easy cleaning and maintenance
Design & Options:
Available with 5 HP to 100 HP
Process up to 4,000 lbs /hour down to D90 < 20 µm
Grinds, Classifies and Conveys in one step
Designed for sticky, fatty and heat sensitive materials
Easy to Clean and Operate
Stainless Stain construction available
Designed for processing heat sensitive materials
Suitable for Chemical, Food, Plastics & Cosmetic Application
Finesses from d97 10 µm to d97 250 µm (based on limestone)
Air classifier with vertical shaft
Air Classifying Mill
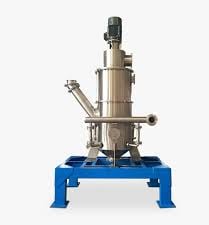
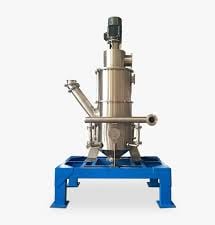
The Innovative Air Jet Mill Is Capable Of Fine Grinding All Kinds Of Dry Products With Virtually No Contamination.
Through this specialized milling concept, product grinding is Fully Automatic. Gas jets alone create the grinding energy. No tool wear occurs!
An integrated dynamic air classifier in the housing can be infinitely adjusted to the desired fineness. This guarantees exact adjustment of the grinding parameters and reproducible product quality.
Even the hardest of products poses no problem for this machine. In addition, extremely temperature sensitive products such as wax can be processed under continuous operation.
The energy efficiency of this technology. The result is a completely new grinding method.
Until now air jet milling, due to its energy consumption, was only cost efficient when applied to high value products. Now many other materials can be economically processed in our fluidized bed jet mills.
Economy is only one of the distinguishing features of our new System. Process optimization through the adaptation of grinding conditions provides energy savings of up to 30 % compared to the conventional operation of air jet mills. Products that in the past could only be economically processed in mechanical mills, can now be micronized even more economically
Features
· Finesses From D97 < 2 µm To D97 70 µm (Based On Limestone)
· Air Jet Mill For The Ultra-Fine Grinding Of Soft To Hard Materials In A Fluid Bed
· Exactly Defined Maximum Particle Size Through Integrated Dynamic Air Classifier
· Vortex Free Fines Outlet With Expansion Chamber To Reduce Circumferential Speed And Wear As Well As Build up Of Residues
· Classifier Wheel With Exchangeable, Simultaneously Rotating Immersion Tube To Achieve Highest Finesses Unlimited Adjustment
· Gap Between Classifier Wheel And Fines Outlet Rinsed By Gas For Highest Possible Prevention Of Coarse Grains
· Classifier Shaft Seal Rinsed By Compressed Gas To Protect The Bearings
· Entirely Automatic Grinding - No Tool Wear - No Contamination
· Warming Of Product Prevented By Grinding With Cooled Gas (20°C), Therefore Applicable For Extremely Temperature Sensitive Materials
· Significantly Lower Compressor Capacity As Opposed To Comparable Jet Mills
· Highest Finesses And Maximum Throughput Achievable With Just One Classifier Wheel
· Hinged Classifier Head Provides Good Access For Fast And Easy Cleaning And Maintenance
· Reproducible Results
· Optional Designs Available: Pressure Shock Resistant, Gas Tight, inert
Fluidized Bed Jet Mill
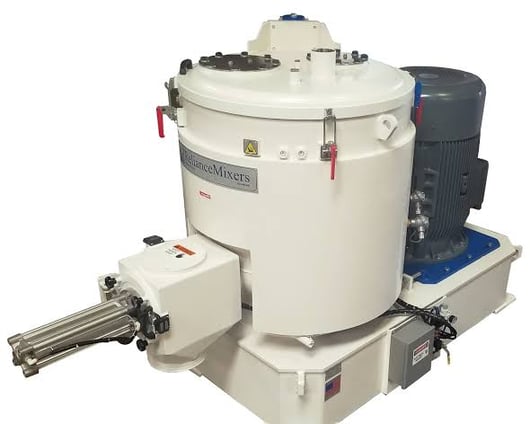
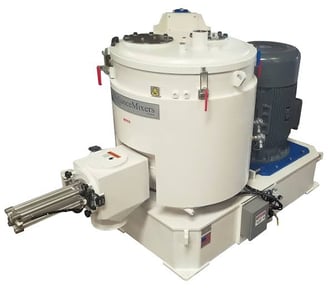
Universal Milling System is a compact, high speed impact mill capable of coarse granulation or fine size reduction with interchangeable rotor configurations. The Universal mill is the next step in the evolution of the Hammer & Screen Mill by providing the same grind as the classic hammer mill while adding the flexibility of a pin disc, knife rotor or attrition plates. The Diverse Selection Of Grinding Tools Allows The Mill To Be Used Universally Depending On The Application And Area Of Operation. This Of Course Also Applies Later On, When Circumstances Such As Product Characteristics Or Requirements Have Changed, The Grinding Tools Can Be Changed As Well. Materials enter from the feed hopper, guided by a screw or direct gravity, ensuring a consistent flow without overloading the mill. As the material meets the rotor's rotation, it gets drawn centrally, then flung outward by centrifugal force. During its outward trajectory, the material is finely ground between the rotor and stator, thanks to their unique interplay of impact and shearing actions. After passing the stator screen, the milled product is collected. The grinding fineness varies based on the product, rotor type, stator screen, feed rate, air intake, and rotor speed
. Features:
· Capable Of Fine Grinding To D97 < 35 Micron
· Lab & Production Models Available With 1 HP To 40 HP
· Capacity Ranges From 5 Grams/Batch Up To 3,000 Lb/Hr
· Suitable For Pharmaceutical, Food, Plastics & Chemical ApplicationsEnergy Efficient & Economical To Operate
· Rotor Impact Mill With Exchangeable Grinding Tools For The Grinding Of Soft To Medium Hard Materials ( Mohs 3 – 3.5)
· Grinding Takes Place In A Vertical Rotor/Stator-System In Numerous Variations:
· Wing Beater Mill Blast Mill Pin Mill (Single Rotating)
· One-Piece Machine Housing With Screwed On Inlet Cover For Very Good Access As Well As Fast, Easy Cleaning And Maintenance
· Fineness Set By Adjustment Of The Rotational Speed And Tool Selection
Flexible
· Suitable For Small Batches
· Compact Design
· Designed For Milling Soft To Medium-Hard Materials
· Fabricated Stainless Steel Construction
· Variable Speed Rotor Drive
· Cantilevered Design For Easy Cleaning & Rotor Changes
· Cryogenic Operation Available
· Available With Pin Rotor, Hammer & Screen, Knives Or Attrition Plate Configurations
· Isolator Installations Available For High Containment Applications
· The High Speed Impact Mill That Can Be Used To Dry Grind A Wide Variety Of Products And Finesses.
Universal Mill
Hammer mill
Hammer Mill is your ideal solution for precision grinding, sieving, and collection of various materials. Ingeniously designed to grind a vast range of non-hygroscopic, non-heat sensitive, and non-explosive materials, our Hammer Mill ensures consistent small particles size reduction. Owing to its high speed rotating shaft in the grinding chamber, it effectively grind materials. The steel hammer comes with with the provision for collection of the material at the bottom gravity through steel drum or pulsaire jet product collector with dust free operation and providing customized capacity variants. This milling machine is the transformative answer to your heavy duty grinding needs.
Features :
· Laboratory (1 HP) to production (200 HP) available
· Process 250 gram batches up to 15 tons/hour
· Economical milling to D90 < 45 µm
· Easy to operate and maintain
· Available in mild steel, stainless steel and with wear protection
· Pressure shock resistant (PSR) models available
· Various configurations available to produce a wide range of products and results
· Very durable & reliable designs for years of production
· Compact and easy to clean design
· Suitable for Chemical, Pharmaceutical, Food, Mineral and Cosmetic applications
· Cryogenic grinding possible
· External Control Feed: Streamlined feeding process for enhanced efficiency.
· High-Efficiency Bag Filter: Fully automatic pulse jet cleaning ensures dust-free operation.
· Rotary Airlock: Acts as an air seal and aids in discharging material from the bag filter.
· Integrated Fan: Facilitates airflow through the mill and collector, enabling efficient product conveying.
Hammer Mill
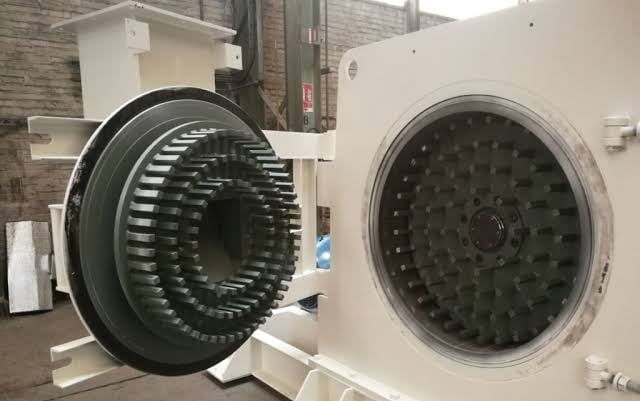
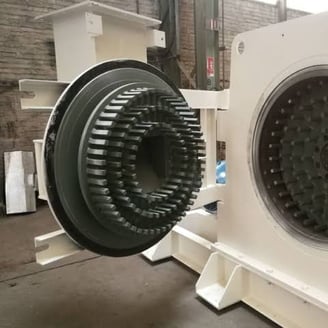
Attrition Mill
Attrition Mill is high speed cutting mill designed for the fine size reduction of plastics, polymers and fibrous materials that do not respond well to other forms of impact milling. It is designed to grind heat sensitive and soft materials without liquid nitrogen or conditioned air.
The raw material enters the grinding zone from a feeding device through the centrally located feed inlet. Size reduction takes place between the adjustable stator plate and high speed rotating grinding plate. The particle size is reduced as it passes through the tapered plates, which has a wider gap at the centre of the plates where the materials is introduced and is closest at the periphery of the plate where material exits. The finely ground product exits the grinding zone and discharges into the product container. Essentially the fineness of the product is dictated by the number of teeth on the plates, rotational speed of the rotor, as well as the gap between the plates.
Features:
Capable of fine grinding to D90 = 100 µm or finer depending on the material & application
Lab & production models available from 1 HP to 40 HP
Capacity ranges from 5 lbs/hour up to 3,000 lbs/hour
Energy efficient & economical to operate
Fabricated stainless steel construction
Variable speed rotor drive
Cantilevered design for ease of cleaning
Maintenance free, sealed for life bearings
Double lip seals & gas purging between drive & process area
Compact design & dust free operation
Gravity or pneumatic conveying discharge available
Chilled or Cryogenic operation available
Variety of feeding options and system configuration
Attrition Mill
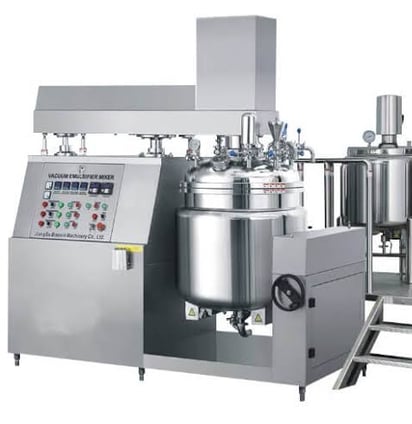
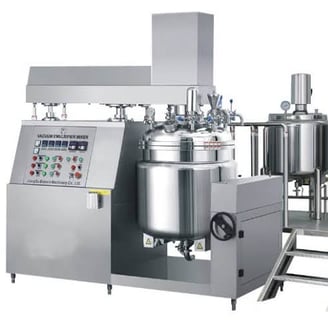
Pin Mills
Pin Mills have been developed for grinding soft and medium-hard products and for surface coating of mineral fillers. With contra-rotating pin discs, the resultant tip speed is over 200 m/s, which enables the grinding of soft to medium and hard minerals to its highest fineness. Independent control of the speed and direction of rotation of the pin disc drives give a high degree of flexibility. An airflow through the mill assists the grinding, enables the control of product temperature and provides a medium for pneumatic transfer of the product.
As standard, the mill body is a robust, welded mild steel construction. Access on the Pin mill is excellent and pin replacement is an easy operation procedure. The pin mill also represents an economical and highly efficient method of coating ultra-fine fillers with stearic acid.
Features :
Fine grinding of soft and medium hard minerals
Extremely reliable and robust design
Suitable for coating applications
Pin discs counter rotation or same rotation depending on material and application requirements
Easy and quick maintenance resulting in low maintenance cost