Grains Milling
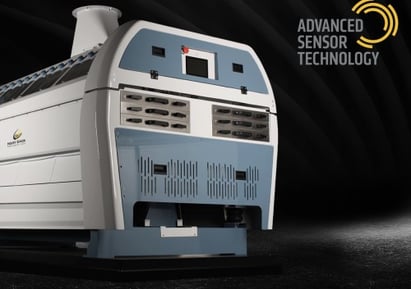
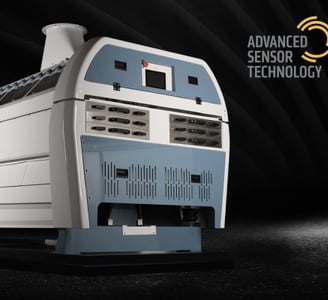
In the competitive landscape of modern Grain Flour Milling, staying abreast of the latest process technologies is crucial for investors. The rapid evolution of processing techniques can pose challenges, yet a well-thought-out process design significantly enhances the mill's competitiveness. By optimizing the process, investors can maximize raw material utilization, minimize waste and losses, and bolster production efficiency. Additionally, effective process flow design allows for better control over the entire flour production sequence, ensuring consistency and quality. Moreover, such design choices lead to lower energy consumption and overall production costs, making it imperative for investors to prioritize strategic planning in the milling operation to achieve sustainable success in this fast-paced industry.
Bran Finisher Machine, which uses a centrifugal action to gently separate the floury endosperm, attached to the bran, thus reducing to the minimum the starch content of offal and ensuring high flour yield.
Structure
· Screw for product introduction with centrifugal disc
· Welded sheet structure
· Statically balanced rotor fitted with four beaters, each with adjustable angle and distance to the cover
· Shaft mounted on a double row of spherical roller bearings and supports
· Cover made of perforated sheet steel specially shaped to avoid internal turbulence
· Adjustable paddles to vary the rate of product flow through the machine
· Two wide doors permit easy access for inspection and screen removal
Features & Advantages
· Low energy consumption and high output
· Minimum and easy maintenance
· Durability and long lifetime
· Practical and easy cleaning process
· Quick and easy screen replacement
· Noiseless working condition
· Trouble free operation
· Less space is needed, when double model is used
· Different air connection possibilities per request
Working Principle
The product is thrown towards the screen by means of a wing - fitted rotor, which is rotated horizontally; consequently, the flour and bran are separated from each other. Due to centrifugal force, the product is thrown towards the screen whose size is selected beforehand. During the screening process, flour passes through the screen and larger sizes of bran are directed to the discharge outlet.
Application Fields
· At food processing industry
· Flour mills, Semolina mills
Bran Finisher
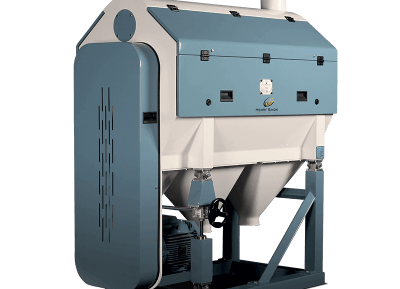
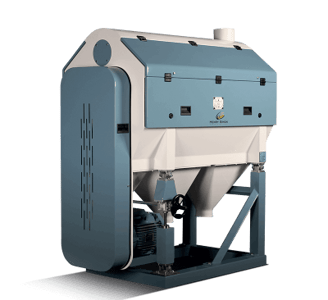
Drum Detacher It is used to break endosperm flakes, which are obtained after reduction rolls, so that it helps for the process of the flour production.
At flour mills; At coarse and fine semolina passages | After roller mills or before plansifter inlet
Application Fields
At flour mills
At coarse and fine semolina passages
After roller mills or before plansifter inlet
Features & Advantages
Delicate detaching without degradation of stock
It can be installed on the floor or suspended from ceiling
Possibility of right hand or left hand inlet
Low power need
Driven either by belt-pulley system or by direct connection to motor
It is designed for higher capacities. Application, design and working principles are similar to those of our regular model. Material incoming is different. The cumulated product enters from the side and feeds axially through the machine.
Working Principle
The material (stock) to be detached is fed through the inlet directly to the rotor and is caught by the inner surface of the jacket, which is installed with six impact bars helps increasing the detaching output. The pitch of beaters directs the material from the feeding point to the discharge point of the machine.
Structure
A cylindrical steel body is supported by stands from both sides. The design of supports allows the drum detacher to be installed on the floor or to be suspended from the ceiling. The rotor is outfitted with four beaters. It is bedded at both ends by ball bearings, which are installed outside. The rotor can be driven by direct- coupled or belt-pulley system either from inlet or outlet side.
Drum Detacher
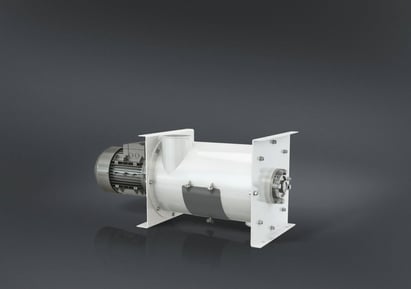
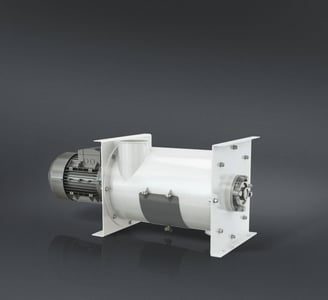
Impact Detacher It is used to realize separating and grind process at the semolina passages in the flour diagrams, this process increases the yield of flour and consumes less energy comparing to other grinders.
Application Fields
At food industry
At the coarse and fine semolina passages in the flour and semolina mills
Just after roller mills or at the peak point of pneumatic tubes to be used as a right-angled elbow
At other similar industrial plants
Working Principle
The product is fed through the center of the machine. Uniform and smooth distribution of product is provided by means of radial wings of the rotating disc. High rotation speed creates a gradually increasing centrifugal force, which throws the product towards the fixed disc’s pins. The impact force depends on the structure of pins. The broken but not ground parts, which come from the passages and stuck on fine and medium size semolina are loosened and separated from each other. Because of free grinding the hard and soft semolina grains are affected differently. Therefore, it causes an automatic grinding between different sized parts. The parts, which are of equal size, are grind by homogeneous breaking quality. So that high flour yield is obtained. The rate of ash almost stays stable or increases slightly which can be neglected. As a result with the high productivity the obtained high flour yield will provide for a shortened flour diagram. The large particles and foreign materials are prevented from getting into the machine by installing a sieve at the inlet of the detacher.
Features & Advantages
Durability and long lifetime comparing to other impact detachers
Installation possibilities, on the floor or to be suspended from the ceiling
Minimum and easy maintenance
Low energy consumption and high efficiency
Hygienic working conditions
Possibility of shortening of flour diagram
Easy installation and less space need
Low investment and operational costs
Impact Detacher
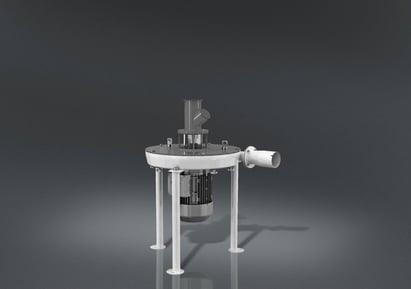
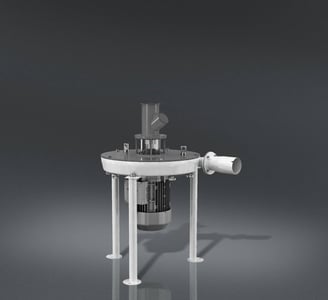
Infestation Destroyer For Flour
It is used in the flour mills to prevent infestation of insects to be grown in the processed product. Application Fields
At food industry
Flour and semolina mills
Biscuit and macaroni factories
Other food industry
Working Principle
The product is conveyed through center into a blade installed rotor which is at horizontal position. During the rotation movement, the product is thrown to wall of the machine and the grown eggs are destroyed.
Advantages
High quality
High efficiency
High extraction
High capacity
Long life
High precision
Maximum hygiene
Maximum security
Maximum simplified using
Low periodical maintenance
Low delay to change the spares parts
Low energy consumption
Noiseless
Perfection and aesthetic
Infestation Destroyer For Flour
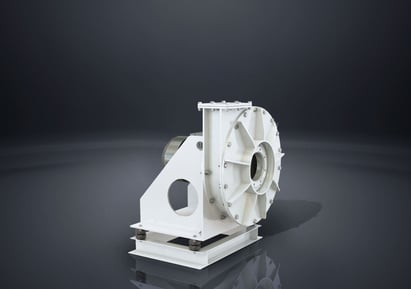
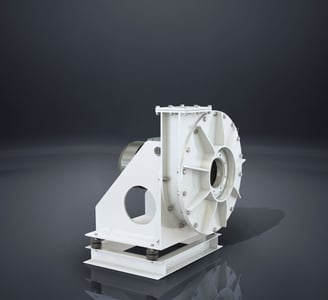
Purifier
It is designed to enrich and classify semolina in flour and semolina mills.
Application Field
At food industry
Flour mills
Semolina mills
Structure
The purifier comprises three main parts;
A fixed main chassis
An oscillating body which accommodates the sifting sieves
An aspiration channel
The exhaust chamber comprises two aerodynamically designed channels with a set of specially designed valves fitted above the sieves for the optimum adjustment of airflow passing through the sieves. The two channels converge at the exhaust intake, which is fitted with an adjustable butterfly valve.
Working Principle
The flow rate of product is adjusted by means of a gate, which provides a perfect distribution of product along all entire width of sieves. The optimum vacuum influence is obtained on the entire surface of sifter by means of aerodynamic air channel and air regulating valves. Bran and similar light materials are kept in suspension due to vacuum influence and transported to discharging channel and collecting box fitted below. The product (semolina) is separated from bran to be classified by means of sieves in accordance with granules.
Features & Advantages
High capacity by using extended sifting surface
Effective cleaning by using brushes
Adjustable sifting speed
Minimum preventative maintenance and trouble - free operation by means of vibro - motor drive
Noiseless working condition
Easy cleaning process and hygienic working conditions
Light metallic sieve frames with adjustable tightening device
Quick and easy replacement of sieves
Purifier
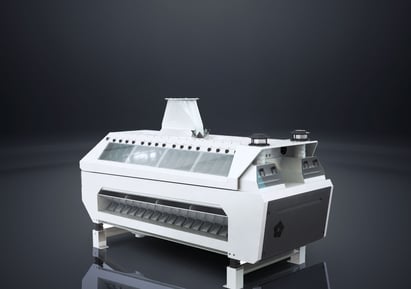
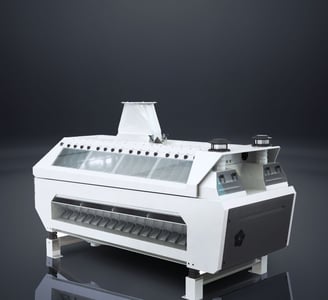
Quadro Plansifter
The square sifter offers many advantages for sifting processes at high capacities. It provides large sifting area in very limited space. The maximum sifting area can be obtained by using different types of boxes. It is used to sift the broken and floury products and classify different kinds of grains.
Application Fields
At Food Industry
Wheat, rye, oats, barley and corn processing plants
Coffee and similar products processing plants
And other food products processing plants
Structure
This machine consists of three main parts. Two sieve boxes and a central framework containing the drive unit. These parts are assembled by means of screws and transversal beams. It is possible to separate the machine into three main parts for an easy make handling, shipping and hoisting to the installation floor. 2 pieces symmetrically designed sieve boxes 1 piece drive housing 2 pieces carrier arms 1 set of suspension group including suspension rods The inner framework comprises all the parts dealing with the machine motion, in particular, the electrical motor, shaft and the counterweight mass. The whole shaft - counterweight unit is bedded by double ball bearings. The drive unit is easily accessible by removing the large side panels covering the central framework.
Working Principle
The product comes from above through one or two inlets and is sifted in the sieve nest, this operation being due to rotary motion of the machine and gravity. In this way from 5 (five) to 7 (seven) selections (sorts of product) with different granules can be obtained at the horizontally divided passages and 12 (twelve) selections at the vertically divided passages. A special device fitted at the inlet of channels provides a very precise separation of the product load along the entire width of the upper sieves for a remarkable increasing of the sifting of the single passage. The great numbers of superimposed sieves and their square shape also guarantee an effective sifting action and a precise classification of the products, positively affecting the final grinding yield. Each machine is completed with its own product inlet and outlet boards, the discharge control spouts and the connection sleeves made of fabric permeable to the air. The machine is easy in maintenance for it’s quite an easy matter to install and dismantle and insert the telero frames into the boxes. The special and even structures of sifters do not allow insects and moths to shelter.
Features & Advantages
High sifting capacity can be obtained by using different frame heights and intermediate frames (spacers). In this way, below and above sifting paths can be adjusted.
Effective sifting possibility at high capacities. It is possible to increase 22 % sifting area by using “G” type sifter boxes
Each sifting cabin can accommodate up to 28 sifters.
A special pressure-clamping device provides proper and tight closing of access doors,
Two-way product flow,
The sieves, square shaped and having an unchangeable structure, are made of first quality stable wood and are completely covered with laminated plastic (Formica),
More sifting area is provided by changing the sieve frames position in right angle,
Vertical and horizontal dividing possibility of sifting passages at any required level,
Easy cleaning and maintenance possibility,
Internally coated insulation panels to avoid condensation, if necessary,
A large variety of standard and special sieves enable the arrangement of many sifting in order to meet any flow sheet demand.
Quadro Plansifter
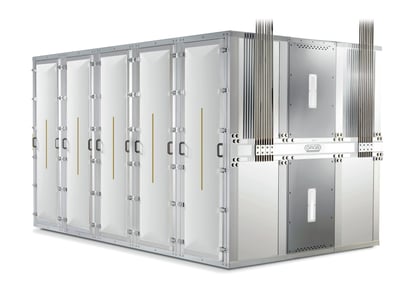
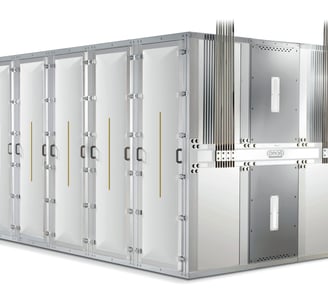
Turbo Control SifterIt is used in the flour mills to separate any foreign material may be mixed into final product during milling process or storage. The foreign materials separated from product before packing, product storage or bulk loading silo.
Application Fields
At food processing industry
Flour and semolina mills
Macaroni factories
Feed mills
At other similar industrial plants
Features & Advantages
Cheap and simple silo design
Durability and long lifetime
Regular and trouble free discharging
Easy accessibility to mechanical parts from outside when the silo is filled
Minimum height
Silent working condition
Low energy consumption
Working Principle
By using numbers of articulated brackets freely suspended a pan-like bottom section is oscillated by means of a vibrator. The product flow is regulated by suitable inserts, which are fixed on discharger for an ideal downward flow of the bulk bran, which is stored in the bin.
At food processing industry; Flour mills • Semolina mills
Turbo Control Sifter
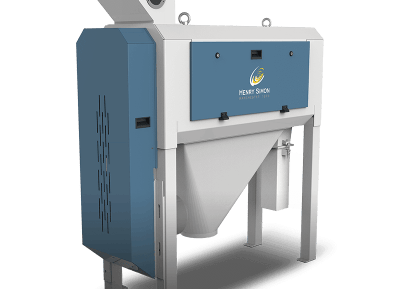
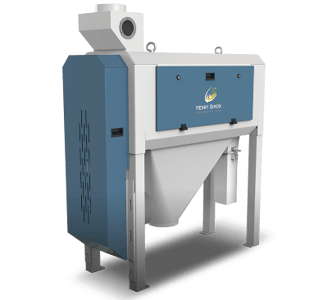
Perfect Milling Technology.
We have various years experience in the milling technology and engineering of roller mills and the complete range of milling machinery. is designed for high, continuous and consistent grinding of cereals such as wheat, maize (corn), rye, spelt, barley and sorghum. A uniform feed rate across the grinding
Feeding Control Systems
Stock Level Control
The product level at the inlet bunker is controlled by using load cells, which sends signals via PLC to adjust the feed roll speed accordingly.
Feeding Gap Adjustment
Manual feeding gap adjustment mechanism ensures a uniform flow on feed rolls.
Grinding Control Systems
Motor Load Protection
Main motor load is constantly measured for protection against any possible damage.
Roll Disengagement System
The system disengages main rolls after the machine shutdown, for preventing any product blockage at the next start-up.
Roll Speed Monitoring
The rotational speed of grinding rolls is monitored against an unexpected stop due to belt problem, etc.
Sanitation
Facelift is built to comply with the high sanitation standards and ensure food safety.
The roller mill’s all front structure is isolated and smoothened against adhering and condensation risk.
Stainless steel product contact surfaces is also available as an option.
Time Saving
Quick Roll Change
Roll change operation can be performed in just 20 minutes, with is a significant reduction in down times. Also, the operation can be carried out easily with only using a standard tool set.
Central Lubrication System
The system allows one-point and automatic lubrication of bearings with a proper distribution at nearly 30 different points; as another time saving, convenient, and reliable solution.
Easy Removal of Parts
The lower chamber of feeding system can be easily set to fully open position with only a single movement. The doors and covers can also be quickly removed for easy access for cleaning.
Variants
800 mm, 1.000 mm or 1.250 mm roll length
250 mm (standard) or 300 mm roll diameter
Double Deck version to save from space
Direct Pick-Up Version
Accessories
Main drive motor, incl. pulleys and belts *
Motor mounting profile beams and fasteners *
Electrical motor trays *
Floor mount metal chassis incl. anchor bolts *
Roll disassembly trolley incl. toolbox *
Pulley and bearings disassembly set *
Discharge hoppers
(*) Only supplied as standard in turnkey projects
Options
Stainless Steel Contact Surfaces
Central Lubrication System rolls ensures a consistent grind.
Pneumatic Roller Mill
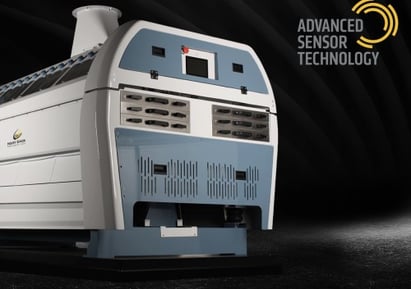
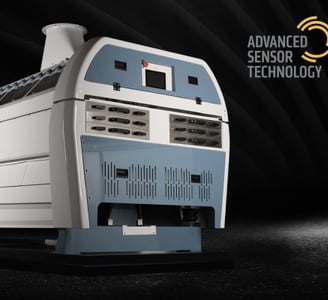