Extrusion Blow Moulding
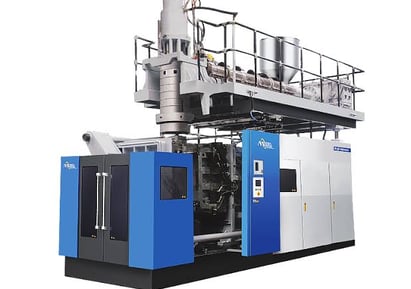
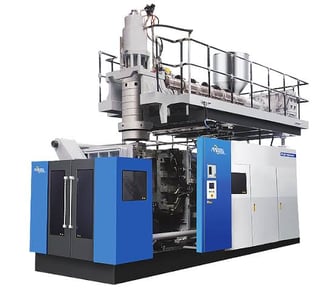
Extrusion blow molding (EBM) is a fascinating process in which plastic is first melted and shaped into a hollow tube known as a parison. This parison is then captured within a cooled metal mold, where air is blown into it, causing the material to expand and take on the desired shape of a bottle, container, or other hollow parts. Once the plastic has cooled sufficiently, the mold is opened, and the finished part is ejected. There are two main variations of EBM: continuous and intermittent. In continuous extrusion blow molding, the parison is extruded nonstop, and individual parts are cut off using a knife. Conversely, intermittent blow molding can involve a process similar to injection molding, where the screw turns to facilitate the production of each part. This versatility allows for efficient manufacturing of various plastic products in different shapes and sizes.
All-Electric Extrusion Blow Molding machine
It has been defined by customers as "the series that the market needed". A range unique in the world, without a doubt, because for each model different versions are available to meet the customer's needs, including machines with increased stroke (LS-long stroke). It is not a result that is reached by chance, but is the result of years of research, investments, application and dedication in electrical technology. Construction carried out entirely in Italy (as for all our other machines), respecting our tradition of having solid machines, compact and reliable over time, with all the refined technological concepts dictated by the Magic experience in over 60 years of activity.
• This is undoubtedly unique in the world and with over years of research and development in electrical technology to reach up to 55 Tons of closing force and increased strokes up to 1600 mm.
• With over a dozen, state-of-the-art technology, intelligent and internet-connected systems, we at Magic can offer Small, Medium or Large machines depending on the request. Thanks to the precision offered by the technology (in the micro meter measurement unit) we can reach weights distributions never seen before, a stable process at each cycle, absence of contamination dictated by the machine and easy to use with the new UI between machine and operator.
• All-Electric market machine trends
• The market over the years and currently, is recognizing the great advantages of the Magic All-Electric machine. This technology is the result of years of experience and research and development. The advantages brought by the All-Electric technology have no end, such as 50%+ less energy consumption than the older technologies. 70% less maintenance costs and less time spent on required machine maintenance. Through Teleservice it can possible connect the machine to the internet for remote software updates.
• Applications
• Personal Care & Medical
• Bottles for clean rooms, environment friendly and for the consumer.
• Cosmetic & Pharmaceutical
• High quality and safety for the final user. Simple to recycle.
• Household & Cleaning
• For high durability bottles, free from contamination and resistant to the surrounding environment.
All-Electric technology
• The 3rd generation of All-Electric Blow Molding machine. Develop up to 60 Tons and 1600 mm clamping stroke.
• High tonnage
• Up to 65 Tons and with 30x less energy consumption and 27% more clamping force. We can develop high tonnage with very small energy requirement.
•
All-Electric Extrusion Blow Moulding machine
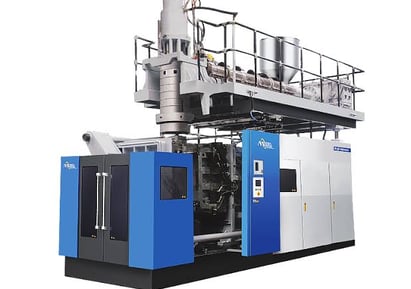
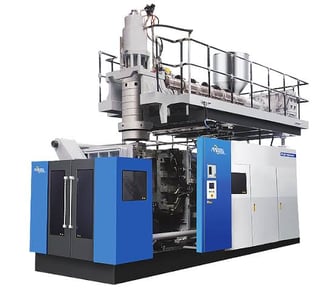
Extrusion Blow Molding For Jerry Can
Maximum performance and minimum energy consumption: The all-electric extrusion blow moulding machines from are the benchmark for bottle and jerry can production. machines will transform your production processes to high-performance production thanks to the shortest cycle and fastest change over times.
The second generation, wins our customers over with even higher productivity alongside lower energy consumption and more attractive investment costs. All-electric extrusion blow moulding machines don’t just set standards in terms of economy; they also do so in terms of ease of use.
The use of master batch is reduced significantly from the 3-layer ReCo3 right through to the multilayer co-extrusion production process. This is because a large proportion of regrind can be returned to the production cycle. You will also be hugely impressed by the machines’ outstanding energy efficiency, proven in tests in line . Many models achieve the highest energy efficiency classification of 10.
Our machines are available as single or double stations. The height of the clamping platens and the scope of the installation depth and the daylight opening represent a key distinguishing characteristic for the jerry can machines. The clamping forces of the bottle variants range from 100 kN to 500 kN.
Technical Details
Mold 610 760 960 1260 660 660
Length (max. mm) 430 430 430 430 700 700
Thickness (mm) 2x 150 2x 150 2x 150 2x 150 2x 250 2x 250
Mold weight (max. kg) 2x 200 2x 225 2x 300 2x 400 2x 600 2x 600
Carriage shuttle stroke (mm) 620 770 970 1270 670 670
Clamp stroke (max. mm) 250 250 250 250 400 400
Blowpin stroke (max. mm) 100 100 100 100 250 250
Clamping force (kN) 200 300 400/500 500 300 300
Calibration force (kN) 35 40 55 63 20 20
Dry cycle time (s) 2,20 2,30 2,80 / 3,10 4,5 3,1 3,1
Extrusion Blow Moulding For Jerry Can
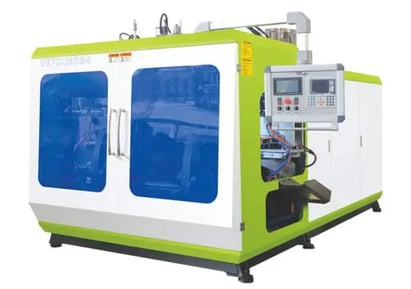
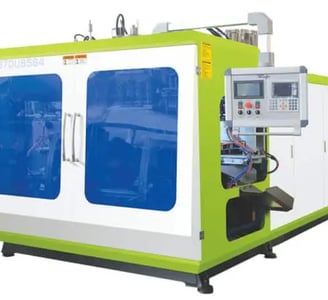
Automatic Extrusion Blow Moulding Machine For 10ML-8L PETG Bottle
This Automatic Blow Moulding Machine mainly to use make PETG Materials 10ML-8L capacity cosmetic bottles and sport water kettles (middle size bottles or container)
PRODUCT DESCRIPTION
Name Units
Max product volume L 8 8
Dry cycle PC/H 800 750*2
Screw diameter MM 75 75
Screw L/D ratio L/D 24 24
Screw drive power KW 22 22
Screw heating capacity KW 7-8 7-8
No. of heating zone ZONE 4 4
Outpul of HDPE KG/H 100 100
oil pump drive power KW 7.5 7.5
Camping force KN 80 80
Max.size of mold MM 400*430 400*430
Template size MM 380*420 380*420
Mold stroke MM 170-520 170-520
Max,die diameter MM 170 170
Bolwing pressure MPa 0.6 0.6
Air volume M³/MIN 0.8 0.8
Cooling water pressure MPa 0.3 0.3
Water consumption L/MIN 60 80
Size of machine L*W*H 4.2*2.0*2.7 4.2*2.0*2.7
Weight of machine Ton 6.8 7.5
PETG material sport water bottles Automatic Extrusion Blow Moulding Machine.
Application:
This Automatic Blow Moulding Machine mainly to use make PETG Materials 10ML-8L capacity cosmetic bottles and sport water kettles
Automatic Single/Double Station Blow Moulding Machine special for plastic PETG bottles Feature as below:
1. Linear guider strip style
2. With single station or double station
3. Adopt 1-4 die mold heads
4. Multi-layers :1-3 Co-Extrusion Layers
5. Multi cavities: 1-4 cavities
6. Production Volume: 10ml-8L
7. Application Products: PETG Cosmetic bottles or Sport water bottles
8. Optional Parison controller/Auto Deflasher/Auto material feeding /Auto Recycling/IML(In Mold Labeling)/Leakage detector/Filling/Packing onlined full automatic production.
9. Energy Saving
Energy savings at least 40% greater than conventional fixed displacement pump systems (The energy-saving effect varies depending on the operation conditions. )
10. High Accuracy with Simple Operation
High-Accuracy servo control according to analog pressure (P) / flow rate (Q) voltage commands
Automatic Extrusion Blow Moulding Machine For 10ML-8L PETG Bottle
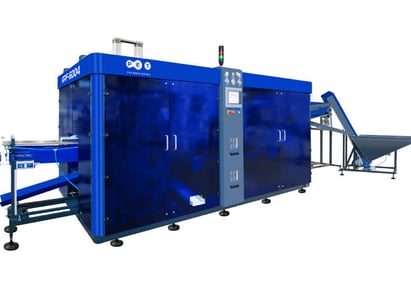
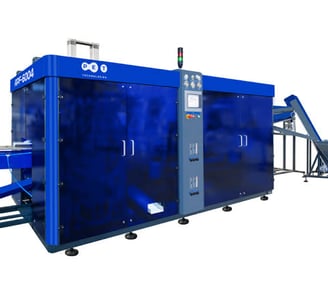