Aqua Feed Mill
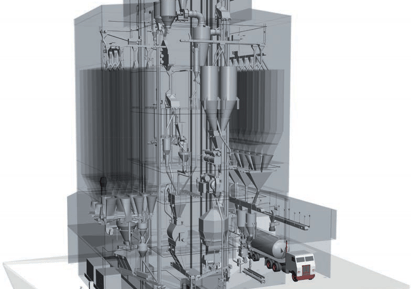
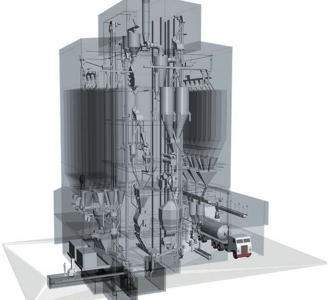
In aqua feed production, achieving the ideal formulation for a complete diet for both food and ornamental fish is paramount. A key aspect of this process is the gentle processing method, particularly through extrusion, which serves to cook and shape the feed while preserving its nutritional value. The extrusion process significantly influences the final characteristics of the product, including texture, digestibility, and overall quality. Furthermore, the pretreatment and post-treatment steps play essential roles in enhancing the feed's performance, impacting its shape, color, and density. By carefully controlling these factors, producers can create high-quality aqua feeds that meet the dietary requirements of various fish species, ensuring optimal growth and health. Our experienced engineers ensure that you meet the most stringent hygiene standards while reducing the risk of cross-contamination. We are dedicated to supporting you in every facet of reliable animal feed production, working closely with you to keep you ahead of the competition. With our tailored solutions, you can enjoy superior quality and enhanced feed safety, ensuring that your livestock receive the best nutrition possible for their health and productivity. Our aim to be a leading global brand in the feed machinery industry, with high customer satisfaction, solution-oriented, sustainable and achievable targets to be the best, adopting a high-quality solid production and service concept, offering advanced technology machines to the market with confidence Feed Tech provides technology products and services that fully meet customer expectations, spend less energy, by making complete facilities, machinery sales, renovation, and capacity increase.
Pre conditioner. The preconditioning concept is based on the separation of the overall process into two stages: component mixing and retention to allow cooking. The BCTC pre conditioner is available in six sizes ranging from 100 to 1,600 liters capacity, with processing throughputs of 100 to 20,000 kg/h.
Single-screw extruder.
The single-screw extruder is a cost-effective tool for cooking and shaping products, and the standard solution for floating Aqua Feed. The machine is characterized by its adjustable process section, various drive options, accessories such as water-cooled or electrically heatable barrels, and its ease of operation and automated control system.
Twin shaft extruder.
The modular twin-screw extrusion system covers the entire capacity range, from laboratory scale to high-capacity production machines. The process configuration of the machine is carefully matched to the specific application.
With this twin shaft technology, new ingredients such as plant based proteins, can be used and can be formulated with mini- mal fish meal inclusions without compromising product quality.
Shaping and Cutting.
Die hole geometry is crucial in the process, as the hot product melt has to be depressurized, shaped, and cut, especially small die holes up to 0.8 mm require an optimized number of holes and a wear-resistant die plate. A movable cutting device enabled precise control with even knife exchange during the process. Since a considerable volume of moisture is evaporated at this point, the addition of hot air and a good aspiration is recommended in order to prevent condensation and agglomeration of the products.
The crucial processes for highest quality.
Extruder
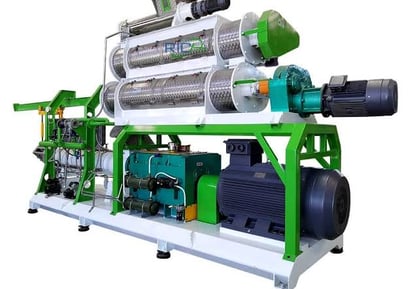
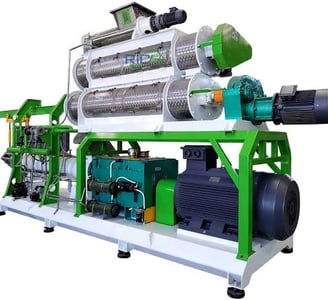
POWDER GRINDING MILLS
With our versatile grinding portfolio, consisting of horizontal and vertical hammer mills as well as roller mills, we can cover all of your size reduction needs. We can bring you solutions for pre- and post-grinding, coarse and fine grinding, as well as for creating crumbles of various sizes.
Vertical hammer mill.
With its vertical grinding shaft, our Vertical grinding and pre-grinding hammer mill can deliver up to 25% energy savings. A smaller footprint, change-over and sanitation benefits make it ideal for animal feed, grain/oil milling and biomass industries.
Horizontal hammer mill.
Our horizontal hammer mill is a high efficiency grinder for size reduction in various feed & food processing industries. Generally applied for dry materials with a bulk density of
0.2-0.8kg/dm3, it convinces through high production flexibility and minimal downtime.
Impact Mill
This hammer mill provides industry leading throughput capacities on a wide range of friable and fibrous products with exceptionally uniform particle size distribution from coarse to fine applications.
Cracking mill..
The high performance cracking mill is for optimal processing of oilseeds and various applications in the feed milling industry, providing ease of maintenance, full automation control as well as highest throughput rates.
It is available in a modular design with up to 3 roll pairs, 2 different roll lengths and diameters
Features
From 5 to 35 tons/hours capacities
Two directions of rotations
Rotor has been balanced under maximum working speed
Particle size up to 60 mm. edge length
Bulk density 0.2 to 0.8 kg/dm3
Electro pneumatically controlled pivoted deflection plate
Low noise 90-93 dba under nominal load
Easily changeable screens within one minute by quick span lock
Interlock preventing opening of doors (when motor is running)
Two bearing suspension
Hammers and rods hardened for long life
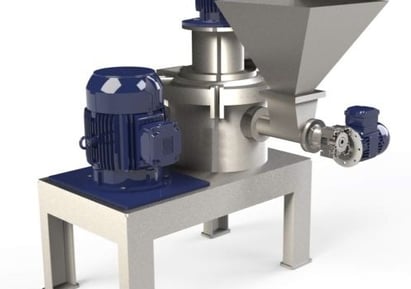
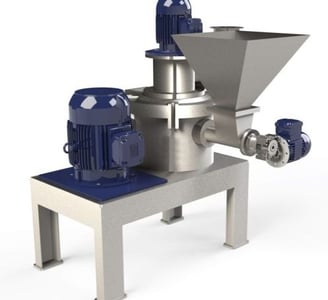
Grinding
PELLET CRUMBLER.
This grinder is applied for crumbling feed pellets and for size reduction applications in multistage grinding systems in various industries. The modular concept allows a combination of up to 3 crushing stages in one crumbler with optional automatic roll gap adjustment system.
Generally for very young poultry, small pellets should be reduced smaller parts as called crumbs 5 or 6 mm. diameter pellets reduced by means of two or four crumbling rolls, also that provide a nutritionally balanced diet. Also the crumbler are used commonly in cattle feed and sheep feed industry today
Features
Roll adjustment assembly with overload protection device
Each roller is driven seperately by means of electric motor
Heavy hardened and fluted longitudinally press rollers
Rolls are mounted in heavy duty self-aligning bearings
Installed in a sturdy steel housing
Pneumatically operated by-pass flap
Low noise level
Capacity up to 30 tons per hour
Seperately driven dosing and supply feeder distributes pellets
PELLET CRUMBLER.
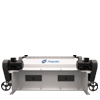
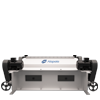
COOLING
Ready for handling and storage.
The cooling of your hot pellets is essential for further handling and proper storage. Our extensive portfolio of counter current coolers offers you an efficient, hygienic and homogeneous cooling process. Different discharge systems ensure gentle handling with minimal fines tailored to your product.
Conical discharge.
The conical screen bottom creates a uniform product layer and therefore an even air distribution across the cooler which results in a very homogeneous cooling. Due to the angle of the cone the pellets move gentle to the outlet leaving almost no product residues behind.
Flatbed discharge.
Compared to the conical discharge, the flatbed coolers take up less space in terms of construction height. The rotating rack distributes the product layer evenly and the discharge systems are designed the way that the pellets stay intact with minimal pellet breakage or fines.
Our portfolio of coolers contains various types and sizes and covers capacities ranging from 7 - 60 t/h.
Pellet coolers are consist of three sections
Rotary valve | Exhaust hood | Cooling column | Discharge grid system | Collecting hoper
Pellet coolers reduce the temperature very quickly and reduce the moisture level from 18 % to ambient moisture level to 10-12 % avoid moulding for proper storage and handling.
Features
Side walls with one transparent inspection door
Level control sensors
Collecting hoper
Rotary valve with electric motor
Exhaust hood
Pellet spreader
Unloading mechanism consisting of one electro pneumatıcally adjustable, one stationary and one
Electro pneumatically driven sliding grid discharge system
Single deck or double deck design
.
Pellet Cooler
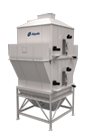
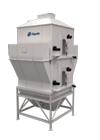
COATING
Upgrading your feed pellets.
Coating & post pelleting applications.
Coating your feed pellets with fats and oils, colorants and flavourings, vitamins or enzymes enables you to offer your products in a higher quality grade at higher values. Our coating and post pelleting application solutions can add this capability to your line. Micro dosing allows to store all ingredients in bulk and it will automatically add the required amount of ingredients needed in the mix.
Uniform coating through high-precision control.
The coating drum enables you to simultaneously coat and thus upgrade your products with up to three different liquids – with a liquids addition rate of max. 8 percent of the product throughput. Design versions of mild steel or high-grade stainless steel for throughputs up to 30 t/h offer you a wide range of choices.
Micro dosing ingredients such as drugs, vitamins and trace minerals with ease and pin point accuracy
Features
Heavy-duty mild steel frame
The rotating drum with scale system is enclosed for dust control
All contact parts with ingredients of the machinery are AISI304 stainless steel
Flexible spouting from the micro hopper to the drum
Clean and dust-free environment
Micro scale accuracy is a +/- of 0.02 lbs. (9.07 grams.)
Micro hopper speed control
Hopper lids are designed to swing or lift open for filling
COATING
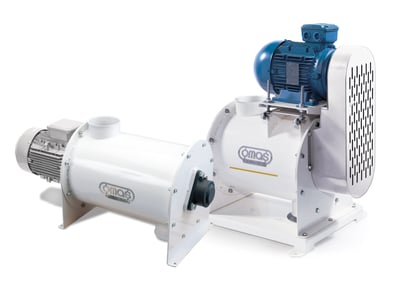
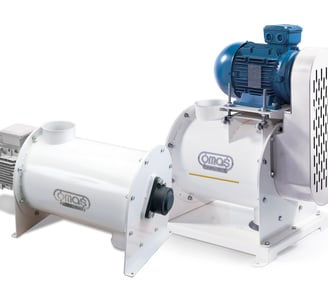
Drying.
The hot and steaming product very rapidly releases the free surface moisture to the hot air stream. Once the surface has been dried, the drying action is limited by the diffusion rate inside the product, and the air stream can be reduced. Due to this physical conditions, the drying process is diverted into different segments with different temperature profiles. This optimized process allows very fast, gentle, and non deforming drying to the necessary final moisture content of 8 to 10% even of soft and sticky products.
The conveyor dryer features uniform, efficient, and durable drying solutions for Aqua Feed. The new dual plenum concept provides a superior airflow that results in uniform moisture content and greater saleable yield. Setting the standard for multi-pass dual plenum conveyor dryers, the new Smart Feed II stands out with engineered airflow control throughout the recirculation loop. This unique design provides uniform airflow temperature and velocity distribution across the entire product bed, resulting in extremely consistent product quality.
Drying
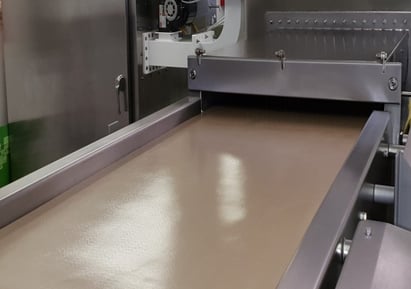
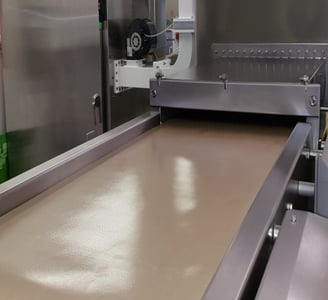