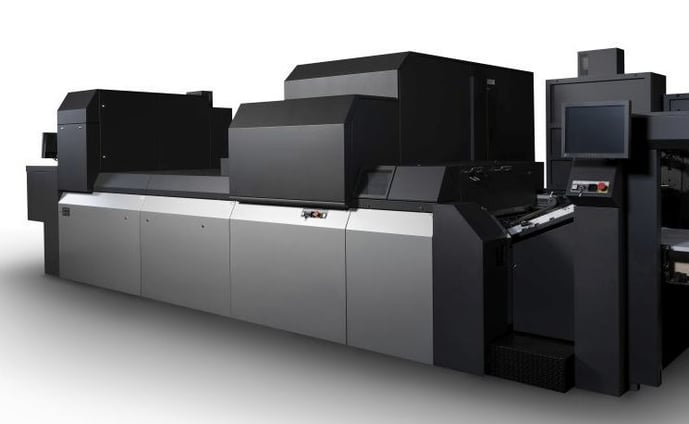
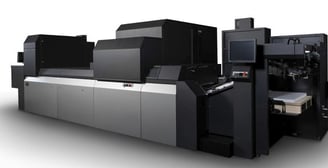
All-In-One, All-In-Line Modular And Upgradable Label Press With Quality Control In 500 Mm Print Width Series Change The Way Label Production Is Done. Leveraging Proven Flexo Experience And Recent Innovative Inkjet Developments, They Provide A Fully Digitalized And Automated Production Line, From Printing To Embellishment And Die-Cutting. Based On A Fully Modular And Upgradeable Architecture,
The All-In-One, All-In-Line Label Press Available In 500 mm Print Width In A New Design That Has Been Optimized For Full Modularity, Improved Operation And Servicing To Expand The Application Versatility Into Larger-Sized Labels, Industrial And Chemical Markets, Wraparound, Shrink Sleeves And Provide Higher Production Volume.
• Reaching Speed Of 80 M/min At Full Native Resolution Of 1000 Dpi, In Four Or Six Colours Plus Optional Digital White, The Bridges The Gap Between Traditional Digital And Flexo Machines
• It Offers Printing, Embellishment And Cutting In A Single Pass, With Seamless Native Integration Between The Uv Inkjet Digital Engine, The Flexo And Converting Modules
• Each Print, Embellishment And Finishing Module Is Digitally Automated For Exceptionally High Uptime, Low Waste, And Outstanding Repeatability Regardless Of The Operator’s Skills
• Quality Control Is Guaranteed By For 100% Inline Inspection At Full Speed.
• Infinite Configurations: From Digital-Only Printing To An All-In-Line Label Production
• Design Your Own Solution Choosing From All Features Available On In-Line Flexo Machine And Access 100% On-Site Upgradability To Make Your Initial Choice Future-Proof
• Application And Substrate Versatility.
Exceptional Productivity And Quality
Maximize Output And Minimize Turnaround Times And Waste
• Highest Inkjet Print Quality (800 X 800 Dpi) And Color Consistency At The Highest Speeds (80 M/Min) Job After Job
• Integrated Maintenance Automation Features
• Fully Automated Flexo Modules
• Embellishment And Converting Solutions
• Available Also In 500 mm Web Width For Additional Productivity.
Inline Quality Control System With Quality Control System Aims For Higher Productivity, Lower Waste And Reduced Operator Skills For Quality Inspection
• True Digital Fully Automatic Non-Stop Print Inspection, Including Foil And Varnish
• Semi-Automatic Calibration For Increased Uptime And Productivity And Faster Setup After Maintenance Interventions
• Detection Of Broad Range Of Defects. Spots, Streaks, Missing Text, Color Variations, Registration Errors, Substrate Integrity, Double Printing, Etc.
• No Setup Time
• Cloud Connectivity And Integration Of Standard Protocols With Mis Systems.
Complete Default Configuration On Every Press For High Productivity And Consistent Quality
• Jumbo Roll Re Winder & Un Winder
• Web Cleaner
• Corona Unit
• Web-Guide
• Simplex Mark Reader For Second Pass Printing
• Splice Detector
• Chilled Roller
• Maintenance Automation Device
• Digital Front End Server For Fast Data Processing
• Digital Printing Module. 4 Or 6 Colors, With Or Without Digital Whitew
• Priming Flexo Module. For Handling The Most Demanding Substrates
• Uv Flexo Modules. Full Integration Between Uv Flexo And Digital Printing, Providing Effortless Switch From Short To Long Runs With Minimum Ink And Material Waste
• Embellishment Module. Varnishing, Tactile Effects, Holographic Effects, Cold Foil Glue Applied, Uv Lamination, Security Printing, And More
• Die-Cutting Module. Fully Automated, High Speed Semi-Rotary Die-Cutting With A Repeat Range Up To 17"; Rotary Die-Cutting For Full Converting Options Such As Embossing And Sheeting
Specification
Web width 200 to 530 mm
Speed max 80 m/min
Rewinding diameter max 1000 mm
Unwinding diameter max 1000 mm
Printing
Imaging width max 500 mm
Digital print quality 800 x 800 dpi
Digital print quality (optical) 2400 ppp
Ink coverage max 16 g/m2
Colour configuration max 6 + white
Inks UV-Inks
Ink tank capacity 10 liters per color
Inspection and quality control
Calibration and quality inspection Optical Vision
Digital print module maintenance
maintenance automation device Contactless cleaning, dry-capping, purging, flushing
Dimensions & weight
Length 5.60 m
Width 0.00 m
Height 2.10 m
Flexo printing unit
Imaging width 520 mm
Drive Independent servo drives
Number of printing units Unlimited
Print cylinder repeat 140 to 610 mm
Sleeve print cylinder repeat 305 to 610 mm
Gear pitch 3.175 mm
Printing speed max 200 m/min
Dryers UV, IR / hot air
Rotary die-cutting
Drive Independent servo drives
Number of units Up to 3
Repeat 279.5 to 610.0 mm
Mechanical speed max 150 m/min
Ink Jet Printer
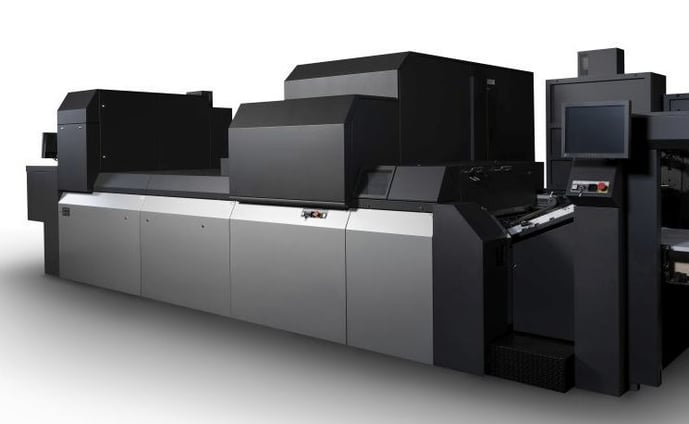
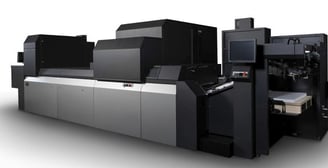
All-In-One, All-In-Line Modular And Upgradable Label Press With Quality Control In 500 Mm Print Width Series Change The Way Label Production Is Done. Leveraging Proven Flexo Experience And Recent Innovative Inkjet Developments, They Provide A Fully Digitalized And Automated Production Line, From Printing To Embellishment And Die-Cutting. Based On A Fully Modular And Upgradeable Architecture,
The All-In-One, All-In-Line Label Press Available In 500 mm Print Width In A New Design That Has Been Optimized For Full Modularity, Improved Operation And Servicing To Expand The Application Versatility Into Larger-Sized Labels, Industrial And Chemical Markets, Wraparound, Shrink Sleeves And Provide Higher Production Volume.
• Reaching Speed Of 80 M/min At Full Native Resolution Of 1000 Dpi, In Four Or Six Colours Plus Optional Digital White, The Bridges The Gap Between Traditional Digital And Flexo Machines
• It Offers Printing, Embellishment And Cutting In A Single Pass, With Seamless Native Integration Between The Uv Inkjet Digital Engine, The Flexo And Converting Modules
• Each Print, Embellishment And Finishing Module Is Digitally Automated For Exceptionally High Uptime, Low Waste, And Outstanding Repeatability Regardless Of The Operator’s Skills
• Quality Control Is Guaranteed By For 100% Inline Inspection At Full Speed.
• Infinite Configurations: From Digital-Only Printing To An All-In-Line Label Production
• Design Your Own Solution Choosing From All Features Available On In-Line Flexo Machine And Access 100% On-Site Upgradability To Make Your Initial Choice Future-Proof
• Application And Substrate Versatility.
Exceptional Productivity And Quality
Maximize Output And Minimize Turnaround Times And Waste
• Highest Inkjet Print Quality (800 X 800 Dpi) And Color Consistency At The Highest Speeds (80 M/Min) Job After Job
• Integrated Maintenance Automation Features
• Fully Automated Flexo Modules
• Embellishment And Converting Solutions
• Available Also In 500 mm Web Width For Additional Productivity.
Inline Quality Control System With Quality Control System Aims For Higher Productivity, Lower Waste And Reduced Operator Skills For Quality Inspection
• True Digital Fully Automatic Non-Stop Print Inspection, Including Foil And Varnish
• Semi-Automatic Calibration For Increased Uptime And Productivity And Faster Setup After Maintenance Interventions
• Detection Of Broad Range Of Defects. Spots, Streaks, Missing Text, Color Variations, Registration Errors, Substrate Integrity, Double Printing, Etc.
• No Setup Time
• Cloud Connectivity And Integration Of Standard Protocols With Mis Systems.
Complete Default Configuration On Every Press For High Productivity And Consistent Quality
• Jumbo Roll Re Winder & Un Winder
• Web Cleaner
• Corona Unit
• Web-Guide
• Simplex Mark Reader For Second Pass Printing
• Splice Detector
• Chilled Roller
• Maintenance Automation Device
• Digital Front End Server For Fast Data Processing
• Digital Printing Module. 4 Or 6 Colors, With Or Without Digital Whitew
• Priming Flexo Module. For Handling The Most Demanding Substrates
• Uv Flexo Modules. Full Integration Between Uv Flexo And Digital Printing, Providing Effortless Switch From Short To Long Runs With Minimum Ink And Material Waste
• Embellishment Module. Varnishing, Tactile Effects, Holographic Effects, Cold Foil Glue Applied, Uv Lamination, Security Printing, And More
• Die-Cutting Module. Fully Automated, High Speed Semi-Rotary Die-Cutting With A Repeat Range Up To 17"; Rotary Die-Cutting For Full Converting Options Such As Embossing And Sheeting
Specification
Web width 200 to 530 mm
Speed max 80 m/min
Rewinding diameter max 1000 mm
Unwinding diameter max 1000 mm
Printing
Imaging width max 500 mm
Digital print quality 800 x 800 dpi
Digital print quality (optical) 2400 ppp
Ink coverage max 16 g/m2
Colour configuration max 6 + white
Inks UV-Inks
Ink tank capacity 10 liters per color
Inspection and quality control
Calibration and quality inspection Optical Vision
Digital print module maintenance
maintenance automation device Contactless cleaning, dry-capping, purging, flushing
Dimensions & weight
Length 5.60 m
Width 0.00 m
Height 2.10 m
Flexo printing unit
Imaging width 520 mm
Drive Independent servo drives
Number of printing units Unlimited
Print cylinder repeat 140 to 610 mm
Sleeve print cylinder repeat 305 to 610 mm
Gear pitch 3.175 mm
Printing speed max 200 m/min
Dryers UV, IR / hot air
Rotary die-cutting
Drive Independent servo drives
Number of units Up to 3
Repeat 279.5 to 610.0 mm
Mechanical speed max 150 m/min
Hybrid Digital Printers
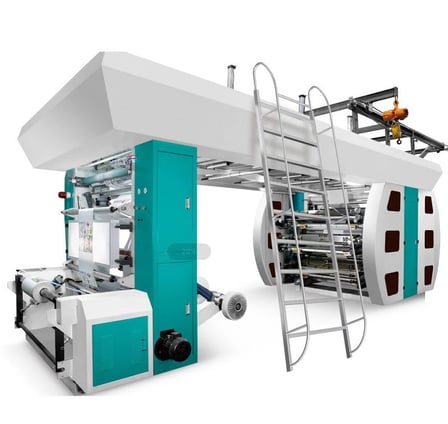
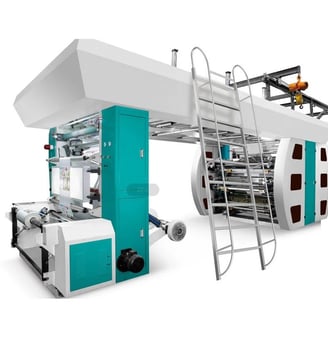
Built For Full Digitalization Of The Production Workflow, The Ultimate Press For Converters Willing To Automate Their Production Line, With Systems And Solutions That Reduce Downtime And Waste. Configurable With Print Cylinders Or Sleeves, The Machine Is Ready To Be Equipped With Technology Delivering Repeatable Consistency Run After Run, Irrespective Of The Application Run Length, And Minimizing Ink Consumption And Inventory.
Outstanding Productivity - Digital Workflow With Integrated Printing And Converting Technologies Enable 1 Minute Job Changes, Very High Quality Consistency At Very Low Operating Costs
• Unlimited Substrate Types
• High Press Uptime, Very Fast Time-To-Market
• Infinite Flower Print Unit For Controlling Print Density Changes At Speed Variations, Monitoring Ink Temperature
• Multi-Process, Product Enhancing Inline Finishing Applications.
Precision And Quality Consistency
• Very Accurate Web-Tension Control From Un Winder To Re Winder
• Automatic Pre-Register Setting
• ARC Automatic Print-To-Cylinder Register Control.
• Digital Automation Ensuring Productivity And Process Repeatability
• Very Short Set-Up Time And Waste
Exceptionally Flexible
• Ideal For Short Runs Compared To A Digital Machine, Long Runs, Profitability, Quality And Product Diversification All In One Press
• Handles All Types Of Substrates Used For The Production Of Labels, Flexible Packaging And Specialties
• Multi-Process, Product Enhancing Inline Finishing Applications
• Lamination Technologies:
• Solventless, Solvent-Based, Water-Based
• Cast & Cure
• Cold Foil And Hot Foil
• Multi-Layer Coupon Labels
• Multiple Printing Processes Available: Flexo, Silk Screen, Gravure.
Fast And Uninterrupted Production
• On-The-Fly Job Changeovers
• Very High Press Uptime, Very Fast Time-To-Market
• Excellence: Special Solutions For Automatic Exchange Of Printing Cylinders And Of Die-Cutting Stations Without Stopping The Press
• Flexo For Full Digital Registration And Printing Pressure Adjustment And Gap For Digitally Automated Die-Cutting Pressure Control. They Provide The Shortest Digital Set-Up Time, Minimal Waste And Consistent Quality During • Very Short Set-Up Time And Waste
• Digital Automation Ensuring Productivity And Process Repeatability
• Very Easy To Run For Less Experienced Operators
• Minimum And Tool-Free Operator Intervention
• Touch Panel On Each Print Unit And Main Touch Screen HMI
• Production Data Accessible From Remote Devices
• Remote Internet Services.
Specifications
Materials Self-adhesive stock (paper, PET, BOPP, PVC); glossy paper; unsupported film (PVC, BOPP, PET, PA); alu-foil; lamitubes; light cardboard.
Web width 370 to 530 mm
Speed max 100 m/min
Unwinding diameter max 1000 mm
Rewinding diameter max 1000 mm
Matrix roll diameter max 700 mm
Gear pitch 3.175 mm
Printing
Number of printing units max Unlimited
Print cylinder repeat 140 to 610 mm
Converting
Number of die-cutting units max 3
Die-cutting cylinder repeat 280 to 610 mm
Dimensions & weight
Length 11.0 m
Width 3.0 m
Height 2.0 m
Flexographic Printing
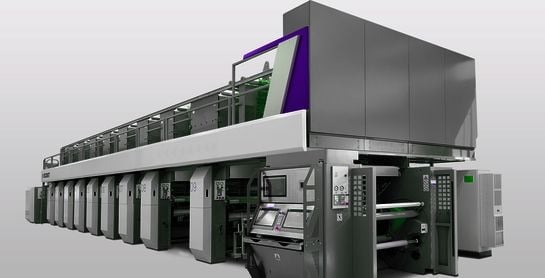
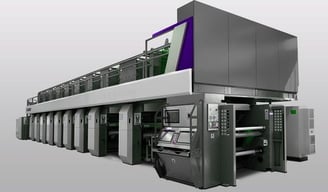
Our Rotogravure Presses With Advanced Technologies For Flexible Packaging Have Been Designed To Take Rotogravure Press With Option Of Either Shafted Or Shaftless Els Cylinder Chucking. Both Design Enable Fast Make Ready Operations And Quick Changeover Excellent Print Quality Along With Cost Effective Production Are What Rotogravure Presses From Stand For. This Includes Running At Maximum Speeds With Quick Make Ready Times. All Of Our Machinery Is Focused On Interconnectivity, Efficiency, Productivity And Profitability So That Your Production Can Run Smoothly. On Demanding Flexible Packaging Print Jobs And Are, Of Course, Compatible With All Of Our Assistance Systems, Such As The Fully-Integrated
ADVANTAGES
Maximum Performance
The high efficient ventilation module with 3D & 2D hole semi-flotation drying system and Separate exhaust blower for floor sweep to remove solvent contaminated air/odor from bottom area of printing units
The doctor blade group with wide adjustments resulting in uniform contact angle, lesser blade pressure, better printing quality, and longer cylinder life
Minimal waste with pre-register setup, the short web path, faster register correction even at speed variations and with minimum volume of ink in
`````Minimal waste with pre-register setup, the short web path, faster register correction ``````even at speed variations and with minimum volume of ink in circulation.
Superior high speed print quality
Fast and operator friendly changeovers
Cutting edge register system
Fully-integrated inspection- and quality control systems
Sustainable use of inks and substrates
Energy efficient drying system
APPLICATIONS
Wide range of food and non-food flexible packaging
Dedicated for film and paper substrates
Wide range of inks e.g. NC, PU, PVB, PVC, also with metalic- and effect-pigments
Gloss, matt and haptic lacquer applications
Quality Printing At High Speed
FOLLOWING OPERATIONAL CONTROLS ARE AVAILABLE ON EACH STATION...
• Easy and perfect web handling
Precise tension control from unwinder to rewinder
Faster register correction even at speed variations
Counter weight infeed with dancer and loadcell ensures stable web tension thus, good print registration. Advance control resulting to high productivity with minimum wastage.
High-performance motion controller having intelligent software for precise tension control
Printing on a wide range of materials
pre-register setting system, completes the register procedure of all print from start, whether it is a new or repeat job
Common DC bus for efficient energy sharing between various drives
Separate exhaust blower for floor sweep to improve the health and safety of the operator
Servo controlled dampers to set recycling of supplied air to reduce energy consumption
Optimum accessibility to all machine sections for cleaning and maintenance
The system mainly composed of push button initiated motorized rotating disc, pneumatically loaded automatic splicing arm, rubber covered pasting roller and cutting blade assembly etc.
Pneumatically expanded self-centering shafts and heavy duty safety chucks to hold the reels.
Unwind Web Handling Control Control using latest generation AC servo technology. The system mainly composed of AC servo motor and drive, pneumatically loaded low friction dancing roller assembly and load cell for tension feed-back and actual tension display.
Electro-electric Edge Guiding System
In-Feed Web Handling Controls
The system provides precise tension control of the web before entering to the first printing station and isolates the printing unit from tension disturbance of the unwinding zone. Dancing roller on pivoting lever mounting loaded by a counterweight (Unique mechanism for tension feedback) having motorized movement by means of slow sync motor. The dancing roller position controls the speed of the in-feed motor./p>
Print Unit
Each print unit mainly consists of pneumatic controls for doctor blade group, impression rubber sleeve and electrical controls for manual length and side-lay register settings, temperature controller for drying chamber, hooter and emergency stop etc.
Sleeve Type Impression Assembly
The sleeve system, consists of an air mandrel with a rubber covered fibre glass sleeve.
Raising - lowering on precision sliding guides with low friction precision linear bearing, which ensure smooth and precise displacement.
Automatic detach of the impression sleeve at machine stop by using special pneumatic cylinder having intermediate stoppage facility.
Transmission
Connection of print cylinder to the motor drive is direct (True direct transmission, without using any reduction ratio components) through a mechanical clamping system ensures fast and easy cylinder locking.
Rotogravure Printing
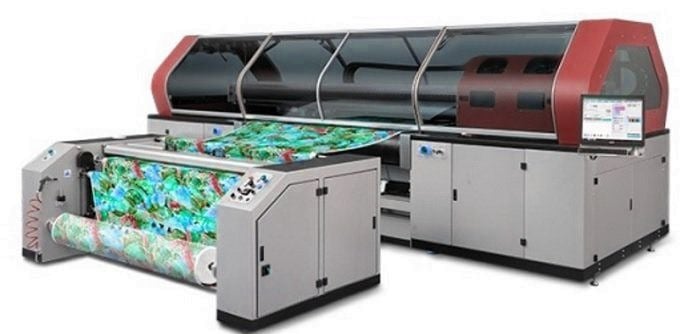
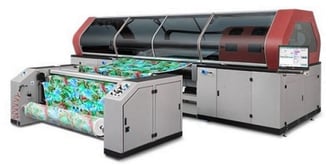
High Speed, High-Quality Digital Textile Printer
Digital Fabric Printing Machine, Which Fantastically Incorporates The Latest Technology And Efficient Engineering To Meet The Ever-Growing Demands Of The Textile Business. As A Digital Textile Printing Consultant, This High-Speed Fabric Printing Machine That Is Compatible To Work With All Types Of Inks Like Reactive, Acid, Disperse, And Pigment. This Industrial Textile Printer Weaves Magic On A Variety Of Fabrics, Ranging From 0.1 Mm To 30 Mm Including Cotton, Polyester, Silk, Viscose, Wool, Nylon, Acetate, Or Any Other Blended Fabric. This High-Speed Digital Textile Printing Machine From Indian Textile Printing Leaders,
It Is The Best Printing Solution For Businesses With An Intent To Invest In Sustainable And Performance-Oriented Digital Textile Printing Solutions. Offers A Clean Future For The Environment. Ink With Binder Offers Greener Solution By Way Of Eliminating Process In Digital Textile Printing. Polymerization At 160-Degree After Printing Provides Excellent Color Fastness And Print Quality With Exceptional Production Capacity
Our Latest Digital Fabric Printer Is A Great Combination Of High Speed And High Quality. It Is The Best Printing Solutions For Businesses That Want To Experiment With Different Patterns Like Checks, Stripes, Geometric Designs On Fabrics And Make Them Appealing Without Compromising The Quality.
The Machine Delivers Magnificent Prints Using Original Inks Available In The Configuration Of 8 Colors Options And Is Equipped With 32 Industrial Grade Print Heads.
Digital Fabric Printing Machine Addresses Various Market Segments Such As Fashion Apparels (Women’s, Men’s, And Kids Clothing), Home Furnishings (Curtains, Bedsheets, Sofa Covers), Etc. This Digital Fabric Printing Machine Is Used To Print Shirts, Skirts, Scarves, And Sarees. Prints On Cotton, Viscose, Polyester, Polyamide, Silk, And Wool And Is Suited For The Production Of High-Quality Products As Well As Home Decoration Fabrics.
Printing Technology Drop-on-demand , Piezo Electric Inkjet
No. of Print Heads 8 KY 8 KY
Print Heads Type Industrial Grade Jetting Assemblies
Resolution Upto 1200 DPI
Height Adjustment upto 20mm
CleaningMethod Pressure Purge and Wiping
Wetting Control Piezoelectric Actuations
Inks Types Reactive/Disperse/Pigment/Acid
No of colors 8 8
Supply 10 Ltr, Bulk ink Supply System with inline degassing
Digital Textile Printer
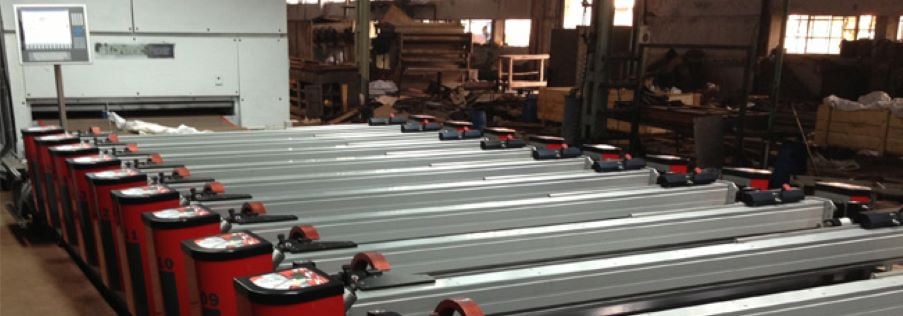
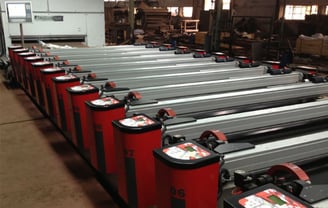
In Rotary Screen Printing, Several Factors Influence The Quality Of Your Printing Results, Such As The Printing Paste And The Screens You Use. The Price You Pay Is Of Course Also Related To These Factors. There Is Good News About That. Introduced A Way To Reduce Process Costs And Improve Product Quality, Without Having To Change The Process Itself. This Will Increase Your Competitiveness In The Printing Business.
We Developed Eco Specifically To Be Both Economically And Technologically Advantageous. The Most Important Adjustment? This Screen Allows More Control On The Print Process And Paste Deposition Than Standard 125mesh Screens. It Brings Other Interesting Features Like A Random Adjustment Of The Holes And Superior Stability Customers Worldwide Are Printing Woven And Knitted Fabrics, Wide And Narrow Width, For Household And Fashion With Great Satisfaction And Profitability.
The New Printing Units Highlight The Typical Features And Advantages That, Top-Quality Printing Machines:
• Closed Bearing Printing Heads
• Multi-Repeat Printing Heads (From 25 In/640 Mm To 40 In/1018 Mm, No Tools Needed)
• Totally Sealed And Lubricated Printing Heads (No Maintenance Required)
• Step Less Adjustment Of Printing Height According To Fabric Thickness
• Step Less Adjustment Of Printing Width (Any Screen Cutting Length Accepted)
• Individual Screen Drive With One Or Two Brushless Servomotors In Closed Loop
• Uniflux Linear Magnetic System
• Easy And Simple Machine Operation, With Touch Screen Interfaces
• High Reliability-Efficiency Electronics.
Closed-Bearing Print Heads
• High Precision And Accuracy
• Self-Aligning Screen Holders
• Evenness In Screen Tension
• Perfect Driving Of The Screen
• No Risk Of Damaging The Screens, No
Mechanical Wearing
• Totally Sealed And Lubricated Print Heads
(No Maintenance Required)
• Easy Screen Installation (With One Operator Only)
• Optimum Control/Access To The Printing, Even With Big Repeats, Thanks To The Large Distance Between The Print Heads
Uniflux Linear Magnetic System
• Perfect Evenness And Uniformity, Even With Widewidth Fabrics
• No Center-Right, Center-Left Effect
• High Flexibility
• Digital Printing Pressure Stepless Adjustment, From Ultra-Low To Very High Pressure
• High Efficiency And Very Low Energy Consumption
• No Pole-To-Pole Overpressure (Typical In Multi-Beammagnet Systems)
Multi-Repeat Print Heads
Totally Pneumatic And Electronically Controlled Between 25 In/640 Mm And 40 In/1018 Mm, And No Tools Are Needed To Change The Repeat. The Operator Sets The Repeat Value On The Main Touch Screen, And All The Print Heads Raise Up So The Screens Can Be Easily Installed On The Machine Without Any Extra Mechanical Parts To Save Time.
Individual Screen Drive
Easy And Friendly Machine Operations, High Efficiency And Low Consumption
All The Electronic Components Are The Most Updated And Highest Performing Available On The Market: The Standard Of
(Plc, Motion Controls, Inverters, Control Panels, And Touch Screens).
The Interfaces Are Simple To Understand And Easy To Use:
• One Touch Screen At The Front Of The Machine
• One Touch Screen On Each Printing Unit (Optionally Available On Both Sides)
• One Main Control Board With A 15ʺ Tft Touch Screen
• One Touch Screen At The Exit Of The Dryer
The Printing And Design Parameters Can Be Easily Adjusted, Saved, And Automatically Reproduced. High Reliability And Very Low Energy Consumption Energy Consumption Is Becoming More And More Important In An Industrial Budget. Which Has Always Been Concerned About Environmental Issues, Has Equipped Its Rotary Printing Machines With Inverters On The Dust And Lint Removal Device, On The Blanket Washing, On The Dryer Fans, And On The Dryer Exhaustion To Guarantee A 25% Savings On Energy Consumption.
Blade Squeegee 180 Cm, Repeat 640
Squeegee Blade Isoform Print Height 1800, Repeat 640. Each Situation Requires A Diverse Setup With Available Adjustments Of The Printing Squeegee System/Color/Cylinder The Squeegee Isoform Can Be Used For Any Type Of Printing On Any Article. The Operations Of Introduction/Extraction Is Facilitated By The Swivel Releasing Completely In The Introduction Section. With No Operator Required, In 10‑12 Minutes, It Is Possible To Wash And Dry All The Screens, Pumps, Color Pipes, And The Blanket On The Machine. The Length And Amount Of Washing And Drying Cycles Can Be Determined By The Operator (And Then Saved And Automatically Reproduced).
After The Washing/Drying Cycles, The Machine Is Ready To Re-Start Printing Without Any Extra Time To Register The Screens. Conceived Mainly For The Colorways, The Wol Washes So Fast And Well That It Is Typically Used For Printing New Designs, Too.
Technical Data
Models 1800mm 2400mm 3200 Mm
Number Of Colors Up To 24
Speed Up To 90 M/Minute
Print Heads Closed Bearing, Self-Aligning, Lubricated
Multi-Repeat Print Heads From 640 To 1018 Mm , Stepless Adjustment,
Electronically Controlled
Screen Drive With One Or Two Brushless Motors
Printing Width Stepless Adjustment
Squeegee System With Uniflux Linear Magnetic System
Operating And Color Side Right Or Left
Gluing System Water Soluble Glue As Well As Thermoplast
Blanket Washing System Two Variable Speed Brushes, Four Rubber Squeegees (The Last One Adjustable)
Interfaces Touch Screens On Each Printing Unit, Touch Screens At The Entry/Exit Of The Machine, One Control Board With A 15ʺ Tft Touch Screen; All With Colors
Electrical Cabinet Conditioned
Rotary Screen Printing Machine
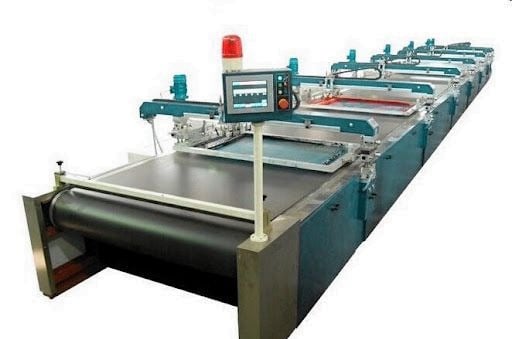
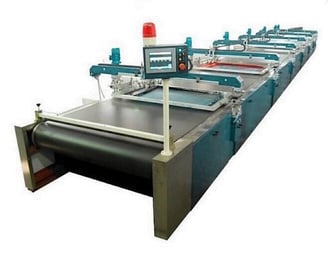
The Fastest Flatbed In The Market
Our Printer Provides High-Performance Printing And Friendly Machine Operation. The Extra Line Control And Driving System Allows For Top-Down Access To All The Main Functions Through One 15-Inch Tft Touch Screen And Two 6-Inch Touch Screens At The Entry And Exit Of The Printer. With The Printing Pressure Applied On The Screen Is Simple And Precise, Assuring High-Quality Results With All The Repeats – But With No Need For Any Additional Equipment. The Desired Features Of Hand Printing Are Available Because Of The Innovative Pressure/Speed Adjustment System. Lifting-Up Speed, Lifting Height, And Delays Can Be Adjusted For Each Stroke, Satisfying The Needs Of Any Printing Application.
Highlights
Wide Range Of Fabrics
Suitable For Any Kind Of Fabric From Woven, Knitted, Elastic, And Synthetic, To Cotton And Silk.
Machine Entry
Fabric Feeding, Using Built-In Devices, Allows For Constant Control Of Fabric Width, Tension, And Type Of Fabric. The Dynaplast System Synchronizes The Blanket Advancement With The Entry Speed To Reduce Fabric Tension, Making It Ideal For Knitted Fabric.
Simple Operation
Easy And Simple Man/Machine Operation Using Touch Screens And Touchpad. The Control Panel, Placed On The Operating Side Of Each Printing Unit, Provides Functions Such As Printing Speed, Printing Mode, Printing Pressure, And More.
Precise Blanket Movement
Printing Blanket Movement Is Driven By Brushless Motors And Is Controlled In A Closed Loop For Precise Control. The Printing Pressure Applied On The Screen Is Easily
And Perfectly Achieved, Even With Big Repeats. Thanks To Our Latest Innovations, Great Printing Evenness Is Achieved With All The Repeats And With No Need For Any Additional Equipment.
The Peculiar Features Of Hand Printing Are Available Because Of The Innovative Pressure/Speed
Adjustment System. Lifting-Up Speed, Lifting Height, And Delays Can Be
Adjusted For Each Stroke, Satisfying The Needs Of Any Printing Application. Additionally, All Of The The Printing Parameters Can Be Easily Saved And Reproduced Thanks To The Top-Down Interfaces.
Machine Entry
The Fabric Feeding Uses Built-In Devices To Keep All
Desired Variables Constant And Controlled, Like:
• Fabric Width
• Fabric Tension
• Kind Of Fabric
System Synchronizes The Discontinuous Blanket Advancement With The Entry Speed By Providing
Constant Speed At The Introduction Of Fabric. This Reduces The Fabric Tension And Is Particularly Suitable For
Knitted Fabric. System Can Be Heated, Which Allows You To Glue The Fabric Onto The Printing Blanket In Caseof Thermoplastic Adhesives. Suitable For Any Kind Of Fabric: Woven, Knitted, Elastic, And Synthetic, From Cotton To Silk
• Bridge Printing Units Equipped With Rubber Squeegees
• Weft Wise Printing Movement
• Pneumatically Adjustable Squeegee Pressure
• Easy And Simple Operation With Touch Screens Andtouch Pad
• High Flexibility
• Blanket Movement Control In A Closed Loop
• Highly Reliable And Efficient Electronics
• High-Quality Printing Blanket Driven By Brushless Motors
Control Panel
The Control Panel, Placed On The Operating Side Of Each Printing Unit, Has The Following Functions:
• Printing Speed: From 1 To 9, Independently Adjustable For Each Direction
• Printing Mode: From 1 To 9, Squeegees Or Flood Stroke
• Printing Pressure: From 1 To 9, Independently Adjustable For Each Direction
• Intermediate Delays Between The Squeegee Passages
• Adjustable Lifting Height To Enable Printing Blanket Advancement
• Adjustable And Self-Learning Squeegee Stroke
• Test Of A Printing Cycle With The Selected Parameters (Cycle Test)
• Unlocking Device For Printing Unit’s Movement Along The Printing Table
15” Main Touch Screen With Colors Touch Screen For Adjustment And Drive Of Printing Heads
Technical Data
Models 1800 , 3200, 3400 mm
Useful Printing Table 6-60 M
Number Of Installable Colors From Four To Max 24
Repeat Fractioning Optional
Squeegee Pass Weft Wise
Squeegee System Bridge, Extraline
Printing Unit Set Up Independent Per Each Printing Unit
Advancement At Adjustable Speed
Screen Lifting Up At Individually Adjustable Height And Speed
Flat Screens Serigraphic With Four Hook-Up Devices
Operating Side Right Or Left (Upon Request)
Color Feeding Manual Or Automatic (Optional)
Printing Table Height 32 In (80 Cm) From The Ground